What is Fine Pitch PCB?
Fine pitch PCB refers to printed circuit boards with components that have a pitch (the distance between the center of one pin to the center of the adjacent pin) of less than 0.5mm. These PCBs are designed to accommodate high-density components, such as Ball Grid Array (BGA) packages, Quad Flat Packages (QFP), and other surface mount devices (SMDs) with a large number of pins in a small footprint.
Fine pitch PCBs are essential for modern electronic devices that require high functionality and performance in a compact size, such as smartphones, tablets, and wearable devices. The use of fine pitch components allows for more features and capabilities to be incorporated into these devices while keeping their size small and portable.
Challenges in Fine Pitch PCB Assembly
Smaller Component Sizes
One of the main challenges in fine pitch PCB assembly is the smaller size of the components. As the pitch between pins decreases, the size of the components also decreases, making them more difficult to handle and place accurately on the PCB. This requires specialized equipment and techniques to ensure proper placement and soldering of the components.
Increased Density of Components
Another challenge is the increased density of components on fine pitch PCBs. With more components placed in a smaller area, there is less space between them, which can lead to issues such as short circuits, bridging, and poor soldering. Proper design and layout of the PCB are crucial to minimize these issues and ensure reliable operation of the device.
Thermal Management
The high density of components on fine pitch PCBs also leads to increased heat generation during operation. Proper thermal management is essential to prevent overheating and ensure the longevity of the device. This can be achieved through the use of heat sinks, thermal vias, and other cooling techniques.
Fine Pitch PCB Design Considerations
Component Selection
When designing a fine pitch PCB, careful consideration must be given to the selection of components. The components must be compatible with the fine pitch design and have the appropriate package size and pin configuration. It is also important to consider the thermal characteristics of the components and ensure that they can be adequately cooled during operation.
PCB Layout
The layout of the PCB is critical in fine pitch design. The traces and pads must be designed to accommodate the smaller pitch of the components while maintaining appropriate spacing and clearance to prevent short circuits and other issues. The use of micro-vias and blind/buried vias can help to increase the density of the PCB while maintaining signal integrity.
Signal Integrity
Signal integrity is another important consideration in fine pitch PCB design. As the pitch between pins decreases, the risk of crosstalk and other signal integrity issues increases. Proper design techniques, such as impedance matching, differential pair routing, and ground planes, can help to minimize these issues and ensure reliable operation of the device.
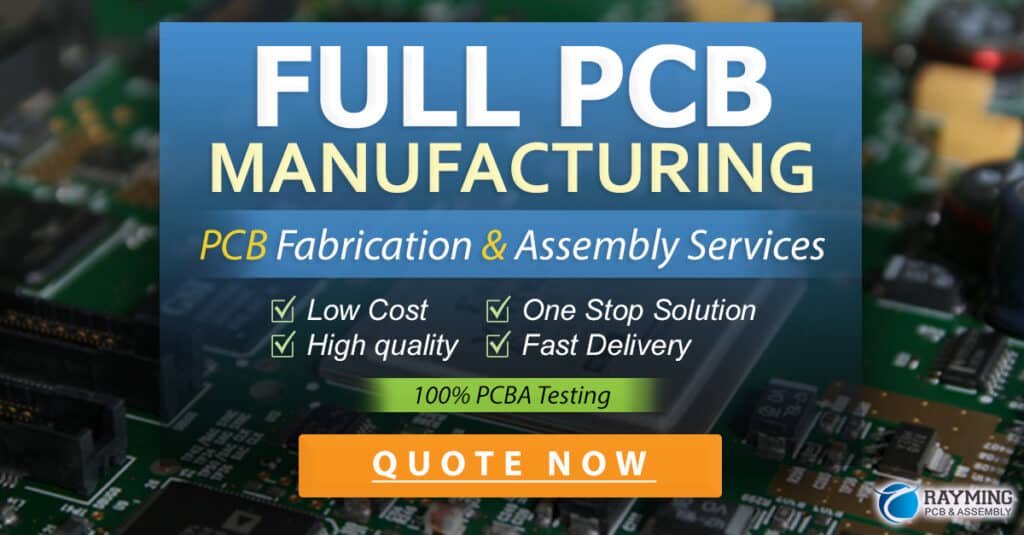
Fine Pitch PCB Assembly Process
Solder Paste Printing
The first step in fine pitch PCB assembly is the application of solder paste to the pads on the PCB. This is typically done using a stencil and a solder paste printer. The stencil is designed with apertures that match the size and shape of the pads on the PCB, allowing the solder paste to be deposited accurately and consistently.
Component Placement
Once the solder paste has been applied, the components are placed on the PCB using a pick-and-place machine. These machines use vision systems and precision placement heads to accurately place the components on the pads. For fine pitch components, specialized nozzles and placement techniques may be required to ensure proper alignment and avoid damage to the components.
Reflow Soldering
After the components have been placed, the PCB is subjected to a reflow soldering process. This involves heating the PCB and components to a specific temperature profile, causing the solder paste to melt and form a strong mechanical and electrical connection between the components and the PCB. The temperature profile must be carefully controlled to ensure proper soldering without damaging the components or the PCB.
Inspection and Testing
Once the soldering process is complete, the PCB undergoes inspection and testing to ensure that all components are properly soldered and functioning correctly. This may involve visual inspection, automated optical inspection (AOI), X-ray inspection, and functional testing. Any defects or issues identified during inspection and testing must be addressed before the PCB can be used in the final product.
Advantages of Fine Pitch PCB
Miniaturization
One of the main advantages of fine pitch PCB is the ability to miniaturize electronic devices. By using smaller components with a finer pitch, more functionality can be incorporated into a smaller footprint. This is particularly important for portable devices such as smartphones and wearables, where size and weight are critical factors.
Increased Functionality
Fine pitch PCBs also allow for increased functionality in electronic devices. With more components and interconnects available in a smaller space, designers can incorporate more features and capabilities into their products. This can lead to more advanced and sophisticated devices that offer greater value to consumers.
Cost Reduction
While fine pitch PCB assembly requires specialized equipment and techniques, it can actually lead to cost reductions in the long run. By miniaturizing devices and increasing functionality, manufacturers can reduce the overall size and complexity of their products, leading to lower material and production costs. Additionally, the use of standardized fine pitch components can help to reduce inventory and simplify the supply chain.
Disadvantages of Fine Pitch PCB
Higher Assembly Costs
One of the main disadvantages of fine pitch PCB is the higher assembly costs compared to traditional PCBs. The specialized equipment and techniques required for fine pitch assembly, such as high-precision placement machines and microscopes, can be expensive to acquire and maintain. Additionally, the smaller size of the components and the increased density of the PCB can lead to higher defect rates and longer assembly times, further increasing costs.
Limited Repairability
Another disadvantage of fine pitch PCBs is the limited repairability compared to traditional PCBs. The small size of the components and the high density of the PCB make it difficult to repair or replace individual components without damaging the surrounding components or the PCB itself. In many cases, if a fine pitch PCB fails, it may be more cost-effective to replace the entire board rather than attempt a repair.
Increased Thermal Challenges
The high density of components on fine pitch PCBs can also lead to increased thermal challenges. With more components generating heat in a smaller space, it can be difficult to dissipate the heat effectively, leading to higher operating temperatures and reduced reliability. Designers must carefully consider the thermal management of fine pitch PCBs and incorporate appropriate cooling techniques to ensure reliable operation.
Future of Fine Pitch PCB
As electronic devices continue to become smaller and more advanced, the demand for fine pitch PCBs is expected to grow. Advances in materials, manufacturing processes, and design tools are enabling even finer pitches and higher densities, pushing the boundaries of what is possible in electronic packaging.
One area of particular interest is the development of 3D packaging techniques, such as through-silicon vias (TSVs) and stacked die packaging. These techniques allow for even greater miniaturization and functionality by stacking multiple layers of components and interconnects in a single package.
Another area of development is the use of advanced materials, such as high-density interconnect (HDI) substrates and low-loss dielectrics, to improve signal integrity and reduce losses in fine pitch PCBs. These materials can help to mitigate some of the challenges associated with fine pitch design, such as crosstalk and power dissipation.
FAQ
What is the minimum pitch for a fine pitch PCB?
There is no strict definition of the minimum pitch for a fine pitch PCB, but generally, a pitch of 0.5mm or less is considered fine pitch. Some advanced packaging techniques, such as chip-scale packaging (CSP), can achieve pitches as low as 0.3mm or even 0.2mm.
Can fine pitch PCBs be assembled using traditional soldering techniques?
While it is possible to assemble fine pitch PCBs using traditional soldering techniques, such as hand soldering or wave soldering, these methods are generally not recommended for fine pitch components. The small size and tight spacing of fine pitch components require specialized equipment and techniques, such as solder paste printing and reflow soldering, to ensure reliable and consistent assembly.
Are fine pitch PCBs more expensive than traditional PCBs?
In general, fine pitch PCBs are more expensive to design and assemble than traditional PCBs due to the specialized equipment and techniques required. However, the increased functionality and miniaturization enabled by fine pitch design can lead to cost savings in the long run by reducing the overall size and complexity of the final product.
What are some common applications for fine pitch PCBs?
Fine pitch PCBs are commonly used in a wide range of applications that require high functionality and performance in a small form factor. Some examples include:
- Smartphones and tablets
- Wearable devices, such as smartwatches and fitness trackers
- Medical devices, such as implantable sensors and drug delivery systems
- Aerospace and defense electronics
- High-performance computing and networking equipment
What are some best practices for designing fine pitch PCBs?
Some best practices for designing fine pitch PCBs include:
- Careful selection of components to ensure compatibility with fine pitch design
- Use of micro-vias and blind/buried vias to increase density and improve signal integrity
- Proper layout and routing to minimize crosstalk and other signal integrity issues
- Incorporation of appropriate thermal management techniques to ensure reliable operation
- Close collaboration between design and manufacturing teams to ensure manufacturability and minimize defects.
By following these best practices and staying up-to-date with the latest advances in materials, manufacturing processes, and design tools, designers can successfully create fine pitch PCBs that meet the demanding requirements of today’s electronic devices.
Pitch Range | Typical Applications |
---|---|
0.8mm – 0.5mm | Consumer electronics, such as smartphones and tablets |
0.5mm – 0.4mm | High-performance computing, networking equipment |
0.4mm – 0.3mm | Medical devices, aerospace and defense electronics |
< 0.3mm | Advanced packaging techniques, such as chip-scale packaging (CSP) |
No responses yet