What is a Continuity Test?
A continuity test is a simple and effective way to check if an electrical circuit is complete, meaning current can flow through it without any breaks or interruptions. It involves using a multimeter or continuity tester to verify that there is a continuous path for electricity to travel from one point to another in a circuit.
The continuity test is an essential diagnostic tool used by electricians, technicians, and hobbyists to troubleshoot wiring issues, identify faulty components, and ensure proper connections in electrical systems. By performing this test, you can quickly determine whether a circuit is functioning as intended or if there are any open circuits, short circuits, or other problems that need to be addressed.
How Does a Continuity Test Work?
A continuity test works by sending a small electrical current through the circuit being tested. The multimeter or continuity tester applies a voltage across the two points of the circuit and measures the resistance between them. If the circuit is complete and has continuity, the resistance will be very low (usually close to zero ohms), and the tester will indicate this with a audible beep or by lighting up an LED.
On the other hand, if there is a break in the circuit or a high resistance due to a faulty connection or component, the tester will not beep or light up, indicating an open circuit. This means that current cannot flow through the circuit, and further investigation is needed to identify and resolve the issue.
Types of Continuity Testers
There are several types of continuity testers available, each with its own features and benefits. Here are some of the most common types:
1. Multimeters with Continuity Test Function
Most modern digital multimeters (DMMs) come equipped with a continuity test function. To use this feature, you simply set the multimeter to the continuity test mode (usually indicated by a diode symbol) and touch the probes to the two points of the circuit you want to test. If there is continuity, the multimeter will beep and display a low resistance reading.
2. Dedicated Continuity Testers
Dedicated continuity testers are specialized tools designed solely for checking circuit continuity. They are often more compact and easier to use than multimeters, making them a popular choice for quick and frequent testing. These testers usually have a built-in light source and a beeper that activates when continuity is detected.
3. Tone Generators and Probes
Tone generators and probes are used for tracing wires and identifying specific conductors within a bundle or cable. The tone generator sends a unique audio signal through the wire, while the probe is used to detect and follow the signal. This method is particularly useful when working with long or complex wiring systems, such as those found in telecommunications or data networks.
Applications of Continuity Testing
Continuity testing has a wide range of applications across various industries and sectors. Here are some common examples:
Electrical Wiring and Installation
Electricians use continuity tests to verify that wiring is properly connected and free from breaks or short circuits before energizing a system. This helps ensure the safety and reliability of electrical installations in homes, offices, and industrial settings.
Electronics Repair and Maintenance
Technicians rely on continuity tests to troubleshoot and diagnose issues in electronic devices, such as smartphones, computers, and appliances. By testing the continuity of individual components and circuits, they can identify faulty parts and make necessary repairs.
Automotive Electrical Systems
In the automotive industry, continuity tests are used to check the integrity of wiring harnesses, fuses, switches, and other electrical components. This helps mechanics diagnose and resolve issues related to starting, charging, lighting, and other vehicle systems.
Manufacturing Quality Control
Continuity testing is an important part of quality control in manufacturing processes that involve electrical components or assemblies. By performing continuity checks at various stages of production, manufacturers can identify and correct defects before products are shipped to customers.
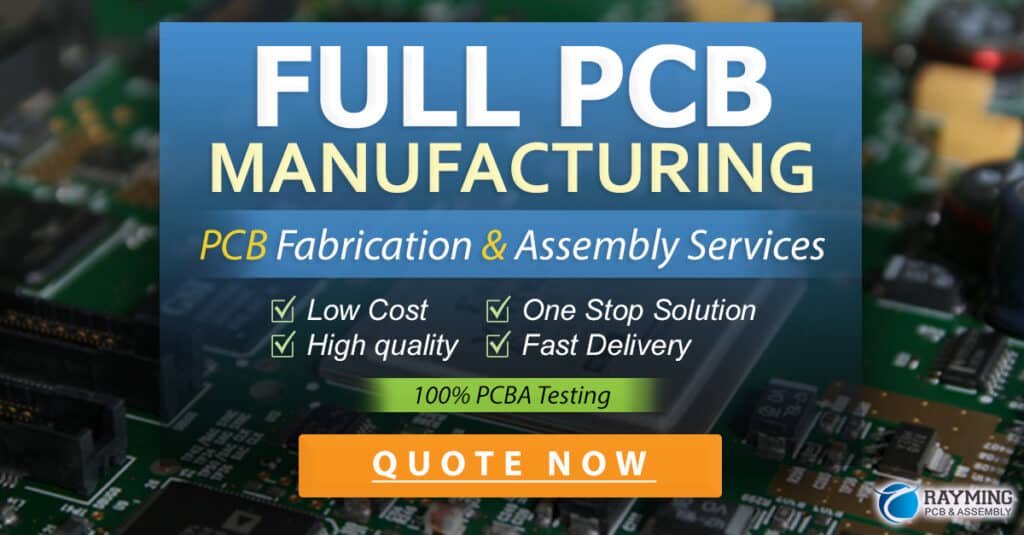
Performing a Continuity Test
To perform a continuity test using a multimeter, follow these steps:
-
Set your multimeter to the continuity test mode, usually indicated by a diode symbol or a beeper icon.
-
Connect the black (negative) probe to the common (COM) jack and the red (positive) probe to the voltage (V) jack on your multimeter.
-
Touch the probes to the two points of the circuit you want to test. Make sure the probes make good contact with the conductors.
-
If there is continuity, the multimeter will beep and display a low resistance reading (usually close to zero ohms). If there is no continuity, the multimeter will not beep, and the display will show “OL” (open loop) or a very high resistance value.
-
Repeat the test at different points along the circuit to isolate any problems and determine the exact location of a break or fault.
When performing a continuity test, it’s important to keep the following tips in mind:
- Always disconnect the power source before testing to avoid electrical shocks and damage to the multimeter.
- Make sure the probes are clean and in good condition to ensure accurate readings.
- Be careful not to touch the metal tips of the probes together while the multimeter is in continuity mode, as this can cause a short circuit and damage the tester.
- If you’re testing a component that is sensitive to polarity (such as a diode), be sure to connect the probes in the correct orientation.
Interpreting Continuity Test Results
Interpreting the results of a continuity test is relatively straightforward. Here’s what the different readings and indications mean:
Result | Interpretation |
---|---|
Beep + Low Resistance | Continuity is present; the circuit is complete and functional |
No Beep + OL or High Resistance | No continuity; there is a break or fault in the circuit |
Beep + High Resistance | Partial continuity; there may be a high-resistance connection or faulty component |
If your continuity test reveals a problem, further investigation is needed to identify the root cause and determine the appropriate course of action. This may involve visually inspecting the circuit for damage, testing individual components, or consulting wiring diagrams and schematics.
Safety Precautions
When working with electrical systems and performing continuity tests, it’s crucial to follow proper safety precautions to prevent accidents and injuries. Here are some important safety tips to keep in mind:
- Always disconnect the power source before working on an electrical circuit or device.
- Use insulated tools and personal protective equipment (PPE), such as gloves and safety glasses, when handling live wires or components.
- Never work on electrical systems while standing in water or on damp surfaces.
- Be aware of your surroundings and keep flammable materials away from your work area.
- If you’re unsure about how to proceed or encounter a situation beyond your expertise, consult a qualified electrician or technician for assistance.
Frequently Asked Questions (FAQ)
1. Can I use a continuity tester to check for voltage?
No, a continuity tester is designed to check for continuity, not voltage. To measure voltage, you need to use a voltmeter or a multimeter set to the appropriate voltage range.
2. Can a continuity test damage electronic components?
In most cases, a continuity test will not damage electronic components, as the test uses a very low current. However, some sensitive components, such as certain ICs and transistors, may be affected by even small currents. Always consult the manufacturer’s specifications and guidelines before testing delicate components.
3. What should I do if my continuity test shows high resistance?
If your continuity test shows high resistance, it indicates that there may be a problem with the circuit, such as a loose connection, corroded contacts, or a faulty component. You should visually inspect the circuit for any obvious issues and then use other diagnostic tools, such as a multimeter or oscilloscope, to further isolate the problem.
4. Can I perform a continuity test on a live circuit?
No, you should never perform a continuity test on a live circuit. Always disconnect the power source before testing to avoid electrical shocks and damage to your testing equipment.
5. How often should I perform continuity tests on my electrical systems?
The frequency of continuity testing depends on the specific application and the environment in which the system operates. As a general rule, it’s a good idea to perform continuity tests whenever you make changes to an electrical system, such as adding new components or repairing existing ones. In critical applications, such as aerospace or medical devices, continuity tests may be performed more frequently as part of regular maintenance and quality control procedures.
Conclusion
Continuity testing is a simple yet essential technique for verifying the integrity of electrical circuits and identifying potential problems. By using a multimeter or dedicated continuity tester, you can quickly check for breaks, short circuits, and other issues that can affect the performance and safety of electrical systems.
Whether you’re an electrician, technician, or hobbyist, understanding how to perform and interpret continuity tests is a valuable skill that can help you diagnose and resolve a wide range of electrical issues. By following proper safety precautions and using the right tools and techniques, you can ensure that your electrical projects are reliable, efficient, and safe.
No responses yet