What is a DC Chopper?
A DC chopper is a power electronic device that converts fixed DC input voltage to a variable DC output voltage. It is a type of DC-to-DC converter that can step down or step up the voltage level by adjusting the duty cycle of the switching element. DC choppers are widely used in various applications, such as motor speed control, battery charging, and renewable energy systems.
Key Components of a DC Chopper
A typical DC chopper consists of the following components:
- DC input source
- Switching element (IGBT, MOSFET, or thyristor)
- Freewheeling diode
- Inductor
- Capacitor
- Load
Working Principle of a DC Chopper
The working principle of a DC chopper is based on the concept of pulse width modulation (PWM). The switching element is turned on and off at a high frequency, and the duration of the “on” state determines the output voltage level. The ratio of the “on” time to the total switching period is called the duty cycle (D).
Duty Cycle and Output Voltage Relationship
The relationship between the duty cycle and the output voltage of a DC chopper can be expressed as:
V_out = D × V_in
Where:
– V_out is the output voltage
– D is the duty cycle (0 ≤ D ≤ 1)
– V_in is the input voltage
By varying the duty cycle, the output voltage can be controlled. A higher duty cycle results in a higher output voltage, while a lower duty cycle leads to a lower output voltage.
Types of DC Choppers
There are four main types of DC choppers based on their configuration and operation:
- Step-down chopper (Buck converter)
- Step-up chopper (Boost converter)
- Step-up/down chopper (Buck-Boost converter)
- Two-quadrant chopper
Step-down Chopper (Buck Converter)
A step-down chopper, also known as a buck converter, reduces the input voltage to a lower output voltage. It consists of a switching element, a freewheeling diode, an inductor, and a capacitor. The output voltage is controlled by adjusting the duty cycle of the switching element.
Step-up Chopper (Boost Converter)
A step-up chopper, also known as a boost converter, increases the input voltage to a higher output voltage. It consists of a switching element, an inductor, a diode, and a capacitor. The output voltage is controlled by adjusting the duty cycle of the switching element.
Step-up/down Chopper (Buck-Boost Converter)
A step-up/down chopper, also known as a buck-boost converter, can either increase or decrease the input voltage depending on the duty cycle. It consists of a switching element, an inductor, a diode, and a capacitor. The output voltage polarity is opposite to that of the input voltage.
Two-quadrant Chopper
A two-quadrant chopper can operate in both forward and reverse directions, allowing power flow in both directions between the input and output. It is commonly used in applications that require regenerative braking, such as electric vehicles and traction systems.
Continuous and Discontinuous Conduction Modes
DC choppers can operate in two different conduction modes: continuous conduction mode (CCM) and discontinuous conduction mode (DCM).
-
Continuous Conduction Mode (CCM): In CCM, the inductor current never drops to zero during the switching period. This mode occurs when the load current is relatively high, and the inductor is sufficiently large to maintain a continuous current flow.
-
Discontinuous Conduction Mode (DCM): In DCM, the inductor current drops to zero for a portion of the switching period. This mode occurs when the load current is relatively low, or the inductor is not large enough to maintain a continuous current flow. DCM results in higher ripple current and voltage compared to CCM.
The choice between CCM and DCM depends on the specific application requirements, such as load current, ripple tolerance, and efficiency.
Applications of DC Choppers
DC choppers find applications in various fields, including:
- Motor speed control
- Battery charging systems
- Renewable energy systems (solar and wind)
- Electric vehicles and traction systems
- Uninterruptible power supplies (UPS)
- DC power transmission and distribution
Motor Speed Control
DC choppers are widely used for controlling the speed of DC motors. By varying the duty cycle of the chopper, the average voltage applied to the motor can be adjusted, resulting in speed control. This method offers efficient and smooth speed control over a wide range.
Battery Charging Systems
DC choppers are employed in battery charging systems to regulate the charging current and voltage. They can be used to implement different charging algorithms, such as constant current (CC) and constant voltage (CV) charging. By controlling the duty cycle, the charging current and voltage can be optimized for different battery types and states of charge.
Renewable Energy Systems
In renewable energy systems, such as solar and wind power systems, DC choppers play a crucial role in maximizing power extraction and regulating the output voltage. Maximum power point tracking (MPPT) algorithms are implemented using DC choppers to ensure that the solar panels or wind turbines operate at their optimal power point under varying environmental conditions.
Electric Vehicles and Traction Systems
DC choppers are used in electric vehicles and traction systems for speed control and regenerative braking. In regenerative braking, the motor acts as a generator, and the energy is fed back to the battery through a DC chopper. This helps to improve the overall efficiency and extend the range of the electric vehicle.
Uninterruptible Power Supplies (UPS)
In UPS systems, DC choppers are used to convert the battery voltage to the desired AC voltage level. They help to maintain a stable and uninterrupted power supply to critical loads during power outages or disturbances.
DC Power Transmission and Distribution
DC choppers are employed in DC power transmission and distribution systems to regulate the voltage levels and control power flow. They can be used for voltage step-up or step-down, as well as for power conditioning and quality improvement.
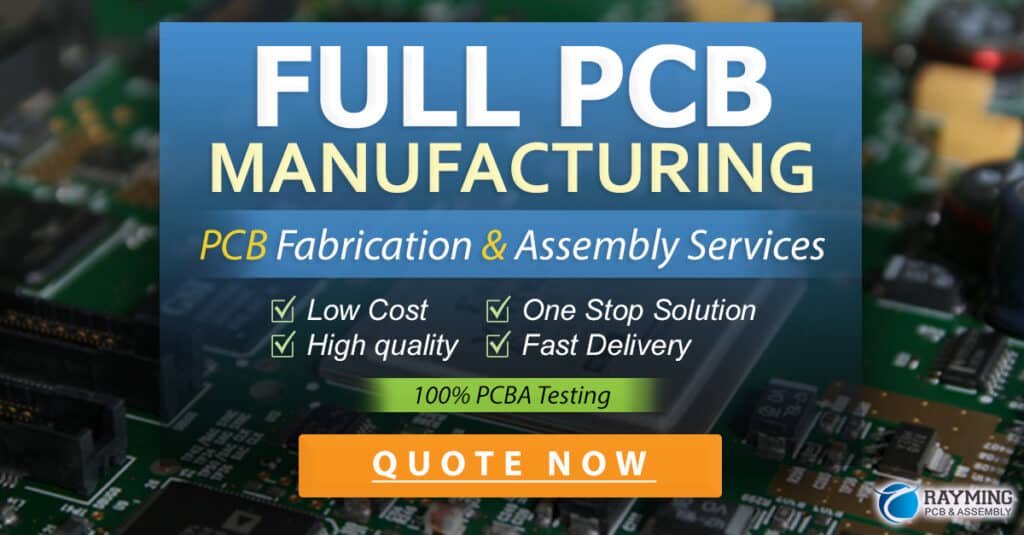
Advantages of DC Choppers
-
High efficiency: DC choppers offer high efficiency, typically above 90%, due to their switched-mode operation and reduced power losses.
-
Smooth control: DC choppers provide smooth and precise control of output voltage or current by adjusting the duty cycle.
-
Wide range of control: DC choppers can control the output voltage or current over a wide range, from zero to the input voltage level.
-
Compact size: DC choppers have a compact size compared to other voltage conversion methods, making them suitable for space-constrained applications.
-
Bidirectional power flow: Some DC chopper configurations, such as two-quadrant choppers, allow bidirectional power flow, enabling regenerative braking and energy recovery.
Disadvantages of DC Choppers
-
High-frequency noise: The switching operation of DC choppers generates high-frequency noise, which may require additional filtering and shielding.
-
Complexity: DC choppers involve complex control circuits and algorithms, which can increase the overall system complexity and cost.
-
Electromagnetic interference (EMI): The high-frequency switching in DC choppers can cause electromagnetic interference, which may affect nearby sensitive electronic devices.
-
Ripple voltage and current: DC choppers inherently produce ripple voltage and current at the output, which may require additional filtering to meet the desired specifications.
FAQs
1. What is the difference between a DC chopper and a linear voltage regulator?
A DC chopper is a switched-mode power converter that efficiently converts a fixed DC voltage to a variable DC voltage by controlling the duty cycle of the switching element. In contrast, a linear voltage regulator is a dissipative regulator that maintains a constant output voltage by continuously adjusting the voltage drop across a pass element. DC choppers offer higher efficiency and wider control range compared to linear voltage regulators.
2. Can a DC chopper be used for AC voltage control?
No, a DC chopper is designed specifically for DC voltage control. For AC voltage control, other power electronic devices such as AC voltage controllers or cycloconverters are used.
3. What is the role of the freewheeling diode in a DC chopper?
The freewheeling diode in a DC chopper provides a path for the inductor current to flow when the switching element is turned off. It helps to prevent voltage spikes across the switching element and ensures continuous current flow through the inductor, reducing the output ripple.
4. How does the switching frequency affect the performance of a DC chopper?
The switching frequency of a DC chopper influences several aspects of its performance. A higher switching frequency results in lower ripple voltage and current, smaller inductor and capacitor sizes, and improved dynamic response. However, higher switching frequencies also lead to increased switching losses and electromagnetic interference (EMI). The choice of switching frequency is a trade-off between these factors and depends on the specific application requirements.
5. What are the main factors to consider when selecting a DC chopper for a specific application?
When selecting a DC chopper for a specific application, several factors should be considered:
- Input and output voltage range
- Load current requirements
- Efficiency and power loss
- Ripple voltage and current specifications
- Dynamic response and transient performance
- Electromagnetic compatibility (EMC) and noise requirements
- Size and weight constraints
- Reliability and operating environment
- Cost and availability
By carefully evaluating these factors, a suitable DC chopper can be selected to meet the specific application needs.
Conclusion
DC choppers are versatile power electronic devices that play a crucial role in various applications requiring DC voltage control. By utilizing pulse width modulation (PWM) and controlling the duty cycle of the switching element, DC choppers can efficiently convert a fixed DC voltage to a variable DC voltage. They find extensive use in motor speed control, battery charging systems, renewable energy systems, electric vehicles, and power distribution.
Understanding the working principle, types, and operating modes of DC choppers is essential for their effective application. While DC choppers offer high efficiency, smooth control, and a wide range of voltage regulation, they also have some limitations, such as high-frequency noise and ripple voltage.
Careful selection and design of DC choppers based on application requirements can help optimize system performance, efficiency, and reliability. As power electronic technologies continue to advance, DC choppers are expected to play an increasingly important role in the development of efficient and sustainable power systems.
No responses yet