Introduction to Laser Diodes and Driver Circuits
Laser diodes are specialized semiconductor devices that emit coherent light when an electrical current is applied. They are used in a wide range of applications from fiber optic communications to laser pointers, barcode scanners, and even laser light shows.
To operate properly, laser diodes require a constant current source provided by a Laser Diode Driver circuit. The driver converts a voltage source into a precise constant current to power the diode. It’s critical to drive laser diodes with the correct current – too little and the laser won’t turn on, too much and the laser can be permanently damaged.
In this beginner’s guide, we’ll dive into the basics of laser diodes and driver circuits. You’ll learn how laser diodes work, what specifications are important, and how to design and build your own laser diode driver. By the end, you’ll have the knowledge needed to incorporate laser diodes into your own projects. Let’s get started!
How Laser Diodes Work
Laser diodes are p-n junction diodes that have been heavily doped and contain an active region sandwiched between two reflective surfaces. When forward biased with sufficient current, electrons and holes within the active region recombine and release energy in the form of photons. The reflective surfaces act as a resonant cavity, causing the photons to reflect back and forth and stimulate further emissions. Some photons escape through the partly reflective surface, producing a highly directional laser beam.
The most common types of laser diodes include:
- Fabry-Perot (FP) lasers
- Distributed feedback (DFB) lasers
- Vertical-cavity surface-emitting lasers (VCSELs)
FP and DFB laser diodes emit light from the edge of the chip and produce an elliptical beam, while VCSELs emit a circular beam from the surface. The wavelength of light emitted depends on the semiconductor material and structure, with common laser diodes producing light in the 405nm to 1550nm range.
Key Laser Diode Specifications
When selecting a laser diode, there are several key specifications to consider:
Specification | Description |
---|---|
Wavelength | The color of light emitted, e.g. 450nm blue, 520nm green, 638nm red |
Optical output power | Measured in milliwatts (mW), typical values are 1mW to 200mW |
Forward voltage | Voltage drop when the specified current is applied, usually 2-3V |
Forward current | The drive current needed for rated optical power, typically 20-200mA |
Threshold current | Minimum current needed for lasing to begin, usually a few mA to tens of mA |
Slope efficiency | Ratio of optical output power to current above the threshold |
Beam divergence | The angle the beam spreads, around 10-30 degrees for edge emitters |
Operating temperature | Acceptable use temperature range, e.g. 0 to +40°C |
Laser diodes are also graded according to lifetime and reliability. Be sure to check the power and wavelength stability over temperature and time.
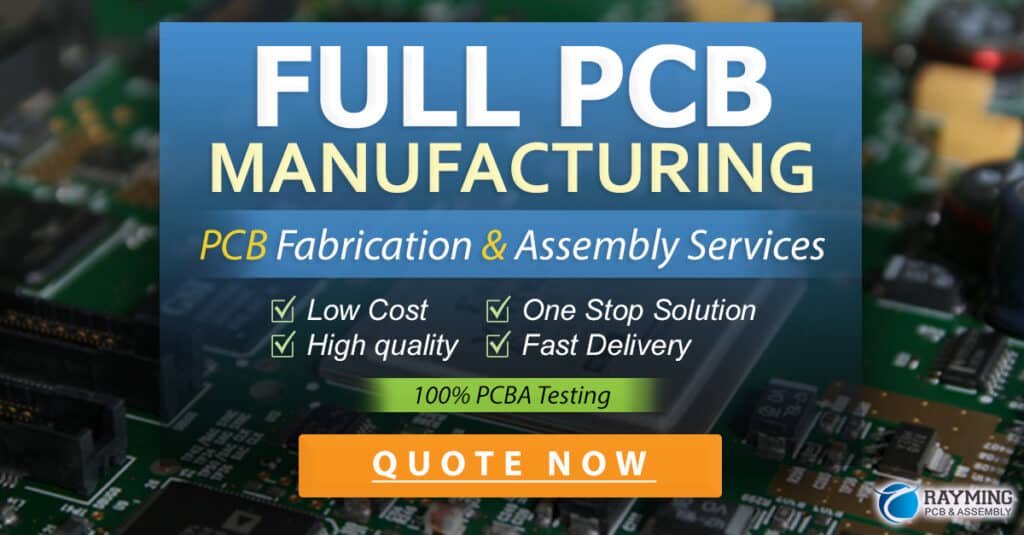
Driving Laser Diodes
To operate a laser diode optimally and avoid damage, it’s essential to drive it with a proper constant current. The current must be above the threshold for lasing to occur, but below the maximum rated level. Common drive currents range from 20mA to 200mA.
Using a constant voltage source is not suitable as laser diodes have a very low dynamic resistance above the threshold, so small changes in voltage cause large changes in current. Transients and spikes can also cause irreversible damage. Therefore, a constant current driver is required.
Laser diode drivers can be built using op-amps, transistors, or dedicated ICs. Let’s examine a few common driver designs.
Simple Op-Amp Laser Driver
A basic laser driver can be built using an op-amp and a few resistors. The op-amp is wired as a voltage-controlled current source. Here’s the schematic:
The laser current ILASER is set by voltage VSET and sensing resistor RS according to:
ILASER = VSET / RS
This circuit works well for low power lasers up to about 50mA. Make sure the op-amp has sufficient output current capability. The 1N4148 diode protects the laser from reverse voltage spikes.
High-Power Transistor Driver
For driving high power laser diodes up to a few hundred mA, a transistor-based driver is a good choice. A simple driver can be built with an NPN power transistor and a few resistors:
The laser current is controlled by the base voltage VB according to:
ILASER = (VB – 0.6V) / R2
Resistor R1 limits the base current. Capacitor C1 improves stability. Make sure the transistor can handle the laser current and has sufficient heat sinking.
Dedicated Laser Driver ICs
For the most precise and feature-rich laser drivers, dedicated ICs are available from manufacturers such as Maxim Integrated, Texas Instruments, and iC-Haus. These ICs contain all the control and protection circuitry needed to safely drive laser diodes. Some even include an integrated photodiode and microcontroller for automatic power control (APC).
Here is an example circuit using the popular iC-WK driver IC:
The iC-WK is controlled via an I2C serial interface. It has built-in circuitry to regulate the laser current using an external resistor, monitor laser voltage and photodiode current, and protect the laser from ESD, overtemperature, and reverse voltage.
Using a dedicated driver IC simplifies the design process and provides the best long-term reliability. They are recommended for precision photonics applications.
Laser Diode Driver Design Considerations
When designing a laser diode driver circuit, there are several important considerations to keep in mind:
-
Laser diode protection – Laser diodes are easily damaged by overcurrent, reverse voltage, and electrostatic discharge (ESD). Always include protection diodes across the laser terminals. For added protection, include a current-limiting resistor or fuse and use transient voltage suppressors. Handle laser diodes using ESD-safe procedures.
-
Power supply noise – Laser diodes are sensitive to power supply noise. A noisy or poorly regulated supply can cause mode hopping and optical power fluctuations. Use a well-regulated, low-noise supply for the driver circuit. Place decoupling capacitors close to the laser diode.
-
Thermal management – The optical power and wavelength of laser diodes vary with temperature. Use a temperature-controlled mount and heat sink to maintain a stable operating temperature. For precise control, add a thermoelectric cooler (TEC) and thermistor sensor.
-
Optical feedback – Some laser applications require constant optical power. This can be achieved using automatic power control (APC) by sampling the laser output with a photodiode and adjusting the drive current in a closed feedback loop. Make sure to choose a photodiode with the appropriate spectral response.
-
Laser safety – Laser light can cause eye and skin damage if not used properly. Be sure to follow all relevant laser safety guidelines for your application, including using protective eyewear, warning labels, and beam stops. Avoid looking directly into the laser beam.
Laser Diode Driver Circuit FAQ
Q: What happens if I drive a laser diode with too much current?
A: Applying too much current to a laser diode can cause permanent damage by burning out the junction or facet. Always stay below the maximum rated continuous and peak currents.
Q: Can I use a regular LED driver to power a laser diode?
A: No, LED drivers provide a constant voltage, not constant current. They do not have the precise current control and fast protection circuitry needed for safely driving laser diodes.
Q: How do I select the right resistor values for a laser driver circuit?
A: The resistor values depend on the laser diode specifications and your desired output power. Use Ohm’s law to calculate values based on the desired laser current and supply voltage. Make sure the resistors are rated for the expected power dissipation.
Q: What should I do if my laser diode isn’t turning on?
A: First, double check all connections and supply voltages. Make sure the polarity is correct. Verify you are providing sufficient current to the driver circuit. If the laser still doesn’t turn on, it may be damaged. Check with a multimeter in diode mode – a good laser will have a forward voltage drop of about 2V.
Q: Can I use a laser diode without a collimating lens?
A: Laser diodes can be used without a lens, but the output beam will be highly divergent and elliptical. Using a collimating lens will produce a narrow, circular beam suitable for most applications. Select a lens with the appropriate focal length and numerical aperture for your laser.
Conclusion
You should now have a solid understanding of how laser diodes work and how to drive them safely using constant current driver circuits. Whether you choose a simple op-amp driver for low power lasers or a feature-rich dedicated IC driver for high performance applications, the key is providing a stable current source and protecting the laser from damage.
When building a laser diode driver, remember to use a regulated power supply, include protection circuitry, properly manage heat, and follow laser safety precautions. With proper driver design, laser diodes enable a wide range of applications from laser pointers to atomic clocks.
To continue learning, experiment with building your own laser driver circuits and explore application notes from laser diode manufacturers. With practice, you’ll be integrating laser diodes into your projects in no time!
No responses yet