Understanding High Current PCB Requirements
Before diving into the design and optimization process, it’s essential to understand the specific requirements of high current PCBs. These boards are typically used in power electronics applications, such as:
- Power supplies
- Motor controllers
- Inverters
- Battery management systems
- High-power LED drivers
In these applications, the PCB must be able to handle large currents, often in the range of tens to hundreds of amperes. This presents several challenges, including:
- Ensuring adequate current-carrying capacity of traces and vias
- Managing heat dissipation to prevent thermal damage
- Minimizing voltage drop across the board
- Reducing electromagnetic interference (EMI) and ensuring electromagnetic compatibility (EMC)
Understanding these challenges is crucial for designing a high current PCB that meets the demands of the application and operates reliably over its intended lifespan.
Designing for Current Capacity
One of the most critical aspects of high current PCB design is ensuring that the traces and vias can handle the required current without overheating or suffering from excessive voltage drop. This involves careful consideration of trace widths, copper thickness, and the number and size of vias.
Trace Width Calculation
To determine the appropriate trace width for a given current, designers can use online calculators or refer to industry standards such as IPC-2221. The required trace width depends on several factors, including:
- The current level
- The maximum allowable temperature rise
- The copper thickness
- The ambient temperature
As a general rule, wider traces can handle higher currents, but this must be balanced against the available board space and the need for adequate clearance between traces.
Copper Thickness
In addition to trace width, the thickness of the copper layer also plays a crucial role in current-carrying capacity. Thicker copper can handle higher currents, but it also increases the weight and cost of the board. Common copper thicknesses for high current PCBs range from 2 oz/ft² to 10 oz/ft² or more.
Copper Thickness (oz/ft²) | Typical Current Capacity (A/mm) |
---|---|
1 | 5-10 |
2 | 10-20 |
3 | 15-30 |
4 | 20-40 |
Via Optimization
Vias are used to connect traces on different layers of the PCB, and they must be sized and placed appropriately to handle the required current. In high current designs, it’s common to use multiple vias in parallel to increase current capacity and reduce resistance. The size and number of vias should be calculated based on the current requirements and the thermal considerations of the board.
Thermal Management Techniques
Proper thermal management is essential for high current PCBs to prevent overheating and ensure reliable operation. There are several techniques that designers can use to optimize thermal performance:
Copper Pour and Thermal Vias
Using large copper pour areas on the PCB can help dissipate heat more effectively, especially when combined with thermal vias that transfer heat to other layers or to an external heatsink. Thermal vias should be placed strategically near high-power components and in areas with high current density.
Component Placement
The placement of components on the PCB can also have a significant impact on thermal performance. High-power components should be spaced apart to allow for adequate airflow and heat dissipation. They should also be placed away from thermally sensitive components to avoid hotspots.
Heatsinks and Fans
In some cases, external heatsinks or fans may be necessary to provide additional cooling for high-power components. These should be selected based on the specific thermal requirements of the application and the available space on the PCB.
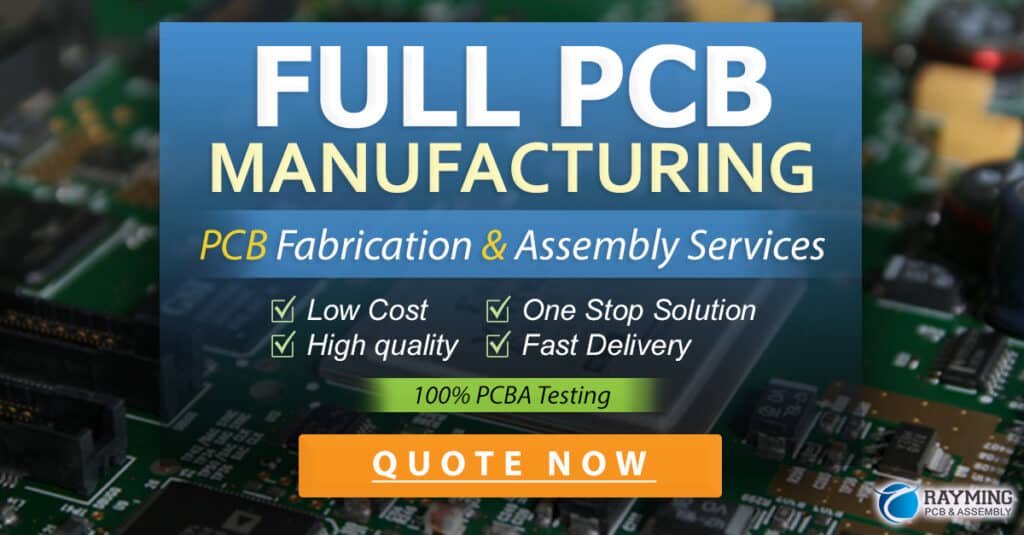
EMI/EMC Considerations
High current PCBs can generate significant electromagnetic interference (EMI) due to the large currents flowing through the board. This can cause problems with other electronic devices and may violate regulatory requirements. To minimize EMI and ensure electromagnetic compatibility (EMC), designers can use several techniques:
Shielding
Shielding sensitive components or the entire PCB with a metal enclosure can help reduce EMI emissions and protect against external interference.
Grounding and Power Planes
Using dedicated power and ground planes can help reduce EMI by providing low-impedance return paths for high-frequency currents. These planes should be carefully designed to minimize loops and ensure good high-frequency performance.
Filtering and Suppression
Adding filtering components, such as capacitors and ferrite beads, can help suppress high-frequency noise and reduce EMI. These components should be placed close to the noise source to maximize their effectiveness.
PCB Stackup and Layer Arrangement
The arrangement of layers in a high current PCB can also have a significant impact on performance and reliability. A typical stackup for a high current PCB might include:
- Top and bottom signal layers
- Internal power and ground planes
- One or more additional signal layers
- Thick copper layers for high current traces
The specific stackup will depend on the requirements of the application, but in general, it’s important to:
- Place high current traces on thick copper layers to maximize current capacity
- Use internal power and ground planes to provide low-impedance return paths and minimize EMI
- Separate sensitive signals from high current traces to avoid interference
Here’s an example stackup for a 6-layer high current PCB:
Layer | Material | Thickness (mm) | Purpose |
---|---|---|---|
1 | Copper | 0.035 | Top signal layer |
2 | FR-4 | 0.200 | Dielectric |
3 | Copper | 0.070 | Power plane |
4 | FR-4 | 0.400 | Dielectric |
5 | Copper | 0.070 | Ground plane |
6 | FR-4 | 0.200 | Dielectric |
7 | Copper | 0.035 | Bottom signal layer |
Design for Manufacturing (DFM)
When designing high current PCBs, it’s important to consider the manufacturing process to ensure that the board can be produced reliably and cost-effectively. This involves following design for manufacturing (DFM) guidelines, such as:
- Ensuring adequate clearance and spacing between traces and components
- Avoiding sharp angles and using teardrop pads to prevent acid traps
- Using standard via sizes and drill pairs to reduce manufacturing costs
- Providing clear labeling and markings for assembly and testing
Testing and Validation
Before putting a high current PCB into production, it’s essential to thoroughly test and validate the design to ensure that it meets all performance and reliability requirements. This may involve:
- Visual inspection and continuity testing
- In-circuit testing (ICT) to verify component placement and functionality
- Thermal imaging to identify hotspots and ensure adequate cooling
- EMC testing to measure EMI emissions and immunity
Based on the results of these tests, the design may need to be modified and re-tested until all requirements are met.
FAQ
- What is the typical current range for a high current PCB?
High current PCBs typically handle currents in the range of tens to hundreds of amperes, depending on the specific application and design requirements.
- How can I determine the appropriate trace width for a given current?
Trace width can be calculated based on factors such as the current level, maximum allowable temperature rise, copper thickness, and ambient temperature. Designers can use online calculators or refer to industry standards such as IPC-2221 for guidance.
- What is the purpose of using thermal vias in high current PCBs?
Thermal vias are used to transfer heat from high-power components or high current density areas to other layers of the PCB or to an external heatsink. This helps to dissipate heat more effectively and prevent overheating.
- How can I minimize EMI in a high current PCB design?
To minimize EMI, designers can use techniques such as shielding sensitive components, using dedicated power and ground planes, and adding filtering components like capacitors and ferrite beads.
- What is the importance of design for manufacturing (DFM) in high current PCB design?
Following DFM guidelines helps ensure that the PCB can be manufactured reliably and cost-effectively. This involves considerations such as ensuring adequate clearance and spacing, avoiding sharp angles, using standard via sizes, and providing clear labeling and markings.
In conclusion, designing and optimizing high current PCBs requires careful attention to many factors, including current capacity, thermal management, EMI/EMC, PCB stackup, and design for manufacturing. By understanding the specific requirements of the application and following best practices for design and optimization, engineers can create high-performing, reliable PCBs that meet the demands of even the most challenging high current applications.
No responses yet