Introduction to Microwave PCB Laminates
In the world of high-frequency electronics, particularly in the microwave domain, the choice of printed circuit board (PCB) material is crucial for ensuring optimal performance and reliability. Microwave PCB laminates are specially designed to cater to the unique requirements of high-power applications, offering stability and low dielectric loss tangent properties. This article delves into the intricacies of microwave PCB laminates, their characteristics, and their significance in modern electronic systems.
What are Microwave PCB Laminates?
Microwave PCB laminates are specialized substrate materials used in the fabrication of printed circuit boards for high-frequency applications. These laminates are engineered to exhibit specific properties that are essential for microwave circuits, such as low dielectric loss, controlled permittivity, and excellent thermal stability. They serve as the foundation upon which microwave components and transmission lines are built, enabling efficient signal propagation and minimizing power dissipation.
Importance of Stable and Low Tangent PCB Laminates
In high-power microwave applications, the stability and low dielectric loss tangent of PCB laminates are of utmost importance. Stability refers to the ability of the laminate to maintain its electrical and mechanical properties over a wide range of operating conditions, including temperature variations and exposure to moisture. A stable laminate ensures consistent performance and reliability throughout the lifetime of the electronic device.
Low dielectric loss tangent, denoted as tan δ, is another critical parameter for microwave PCB laminates. The loss tangent quantifies the amount of energy dissipated within the material as heat when subjected to an alternating electric field. In microwave applications, where signal integrity and power efficiency are paramount, a low loss tangent is essential to minimize signal attenuation and power loss. Laminates with low loss tangents enable longer transmission distances, improved signal-to-noise ratio, and reduced heat generation.
Key Characteristics of Microwave PCB Laminates
To meet the stringent requirements of high-power microwave applications, PCB laminates must possess a combination of desirable characteristics. The following sections highlight the key properties that make microwave PCB laminates suitable for these demanding applications.
Dielectric Constant (Dk)
The dielectric constant, also known as relative permittivity (εr), is a measure of a material’s ability to store electrical energy in an electric field. In the context of microwave PCB laminates, a stable and well-controlled dielectric constant is essential for accurate circuit design and predictable performance. Laminates with a consistent dielectric constant across the operating frequency range enable precise impedance matching and minimize signal reflections.
Typical dielectric constant values for microwave PCB laminates range from 2.2 to 10.2, depending on the specific material composition and application requirements. Lower dielectric constant materials, such as PTFE (polytetrafluoroethylene) and its composites, are commonly used for high-frequency applications due to their excellent electrical properties and low loss tangents.
Dissipation Factor (Df) and Loss Tangent (tan δ)
The dissipation factor (Df) and loss tangent (tan δ) are measures of the dielectric loss within a material. In microwave PCB laminates, a low dissipation factor and loss tangent are crucial for minimizing signal attenuation and power loss. These properties directly impact the efficiency and performance of microwave circuits.
The dissipation factor is defined as the ratio of the energy dissipated to the energy stored in a material under an alternating electric field. It is related to the loss tangent through the equation: tan δ = Df. A lower dissipation factor indicates less energy loss and higher signal integrity.
The loss tangent, on the other hand, represents the angle between the real and imaginary parts of the complex permittivity. It quantifies the dielectric loss within the material. A low loss tangent is desirable for microwave PCB laminates to minimize signal attenuation and maintain high power efficiency.
Typical loss tangent values for microwave PCB laminates range from 0.0002 to 0.01, with lower values being preferred for high-performance applications. Materials such as PTFE and its composites, as well as certain ceramic-filled hydrocarbon materials, exhibit exceptionally low loss tangents, making them suitable for demanding microwave circuits.
Thermal Stability and Coefficient of Thermal Expansion (CTE)
Thermal stability is a critical factor in microwave PCB laminates, as high-power applications often generate significant heat. The laminate material must be able to withstand elevated temperatures without degrading its electrical and mechanical properties. Thermal stability ensures reliable performance over the operating temperature range and prevents delamination or other structural failures.
The coefficient of thermal expansion (CTE) is another important consideration in microwave PCB laminates. CTE refers to the rate at which a material expands or contracts with changes in temperature. In multilayer PCBs, mismatches in CTE between different layers can lead to mechanical stress, warping, and potential reliability issues. Therefore, microwave PCB laminates are designed to have a CTE that closely matches that of the copper conductor and other materials used in the circuit board assembly.
Laminates with low CTE values, typically in the range of 10 to 20 ppm/°C, are preferred for microwave applications. This ensures dimensional stability and minimizes the risk of thermal-induced stresses and deformations.
Moisture Absorption
Moisture absorption is a critical factor in microwave PCB laminates, as the presence of moisture can significantly impact the dielectric properties and overall performance of the circuit. Water molecules have a high dielectric constant and can increase the dissipation factor of the laminate, leading to increased signal loss and degraded performance.
Microwave PCB laminates are designed to have low moisture absorption rates to maintain stable dielectric properties and minimize the impact of environmental factors. Laminates with moisture absorption rates below 0.1% are considered suitable for high-reliability microwave applications.
Materials such as PTFE and its composites, as well as certain ceramic-filled hydrocarbon materials, exhibit excellent moisture resistance. They are inherently hydrophobic and have minimal water absorption, making them ideal for applications exposed to humid environments.
Common Microwave PCB Laminate Materials
Several materials have been developed specifically for microwave PCB laminates, each with its unique properties and advantages. The following table provides an overview of some commonly used microwave PCB laminate materials:
Material | Dielectric Constant (Dk) | Loss Tangent (tan δ) | Thermal Stability | Moisture Absorption |
---|---|---|---|---|
PTFE (Teflon) | 2.1 | 0.0002 | Excellent | Very Low |
PTFE/Ceramic Composite | 2.2 – 2.6 | 0.0010 – 0.0020 | Excellent | Very Low |
Rogers RO4000 Series | 3.3 – 3.5 | 0.0027 – 0.0037 | Good | Low |
Rogers RT/duroid Series | 2.2 – 10.2 | 0.0009 – 0.0025 | Excellent | Very Low |
Arlon AD Series | 3.3 – 3.5 | 0.0030 – 0.0035 | Good | Low |
Isola FR408HR | 3.65 | 0.0100 | Good | Low |
Each material offers specific advantages based on the application requirements, such as frequency range, power handling capability, and environmental conditions. The choice of laminate material depends on factors such as dielectric constant, loss tangent, thermal stability, and moisture resistance, as well as cost and manufacturing considerations.
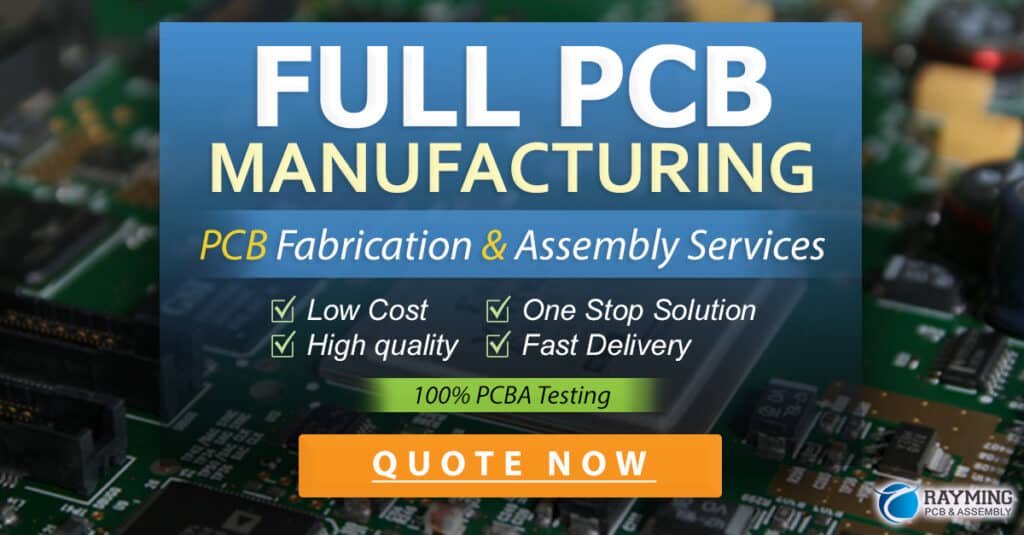
Manufacturing Considerations for Microwave PCB Laminates
The manufacturing process for microwave PCB laminates requires special attention to ensure the desired electrical and mechanical properties are achieved. The following sections highlight some key manufacturing considerations.
Material Selection and Compatibility
Selecting the appropriate microwave PCB laminate material is the first step in the manufacturing process. The chosen material must be compatible with the specific manufacturing techniques and processes used, such as etching, drilling, and plating. Compatibility ensures that the laminate can withstand the various processing steps without compromising its properties or causing manufacturing defects.
Manufacturers should also consider the compatibility of the laminate material with other components used in the circuit board assembly, such as adhesives, solder masks, and surface finishes. Incompatibilities can lead to delamination, poor adhesion, or other reliability issues.
Controlled Impedance and Trace Geometry
Microwave PCB laminates are often used in controlled impedance applications, where the trace geometry and dielectric properties of the laminate must be carefully controlled to achieve the desired impedance values. Manufacturers must consider factors such as trace width, thickness, and spacing, as well as the dielectric constant and thickness of the laminate, to design and fabricate controlled impedance structures.
Accurate modeling and simulation tools are used to optimize the trace geometry and ensure compliance with the specified impedance requirements. Manufacturers may employ techniques such as impedance testing and time-domain reflectometry (TDR) to verify the impedance characteristics of the fabricated PCB.
Multilayer Construction and Lamination
Microwave PCBs often require multilayer construction to accommodate complex circuit designs and achieve the desired functionality. The lamination process, which involves stacking and bonding multiple layers of laminate materials, is critical for ensuring the integrity and reliability of the multilayer structure.
Manufacturers must pay close attention to the lamination parameters, such as temperature, pressure, and duration, to achieve proper bonding between layers and minimize the risk of delamination. The CTE mismatch between different materials must be carefully managed to prevent warping or other mechanical issues.
Proper registration and alignment of the layers are also crucial for maintaining the desired electrical performance and avoiding signal integrity issues. Manufacturers employ precise alignment techniques and registration marks to ensure accurate layer stacking and minimize misalignment.
Controlled Environment and Cleanliness
Microwave PCB laminates are sensitive to environmental factors such as moisture, dust, and contamination. Manufacturers must maintain a controlled environment throughout the manufacturing process to minimize the impact of these factors on the laminate properties and circuit performance.
Clean room facilities with controlled humidity and temperature are commonly used for microwave PCB fabrication. Strict cleanliness protocols are implemented to prevent contamination from dust particles, oils, and other foreign materials that can degrade the electrical properties of the laminate.
Proper handling and storage of the laminate materials are also essential to maintain their integrity and prevent moisture absorption or other environmental effects.
Applications of Microwave PCB Laminates
Microwave PCB laminates find applications in various high-frequency and high-power systems. Some common application areas include:
-
Telecommunications: Microwave PCBs are used in base stations, antennas, and wireless communication systems operating at frequencies ranging from a few gigahertz to tens of gigahertz.
-
Radar Systems: Microwave laminates are employed in radar systems for military, aerospace, and automotive applications, where high power handling and low loss are critical.
-
Satellite Communications: Microwave PCBs are used in satellite transponders, ground stations, and earth observation systems, where reliable performance under extreme conditions is essential.
-
Aerospace and Defense: Microwave laminates are utilized in avionics, electronic warfare systems, and missile guidance systems, where high reliability and durability are paramount.
-
Automotive Radar: Microwave PCBs are increasingly used in automotive radar systems for advanced driver assistance systems (ADAS) and autonomous vehicles, enabling functions such as collision avoidance and adaptive cruise control.
-
Medical Imaging: Microwave laminates are employed in medical imaging systems, such as MRI and CT scanners, where high-frequency signals are used for non-invasive diagnostic purposes.
-
Test and Measurement: Microwave PCBs are used in high-frequency test and measurement equipment, such as network analyzers, spectrum analyzers, and signal generators, where accurate and stable performance is crucial.
These applications demand the use of stable, low-loss microwave PCB laminates to ensure reliable performance, high signal integrity, and efficient power handling.
Frequently Asked Questions (FAQ)
-
What is the difference between microwave PCB laminates and standard PCB laminates?
Microwave PCB laminates are specially designed for high-frequency applications and exhibit unique properties compared to standard PCB laminates. They have lower dielectric loss, controlled permittivity, and better thermal stability to meet the demanding requirements of microwave circuits. -
How do I select the appropriate microwave PCB laminate for my application?
The selection of the appropriate microwave PCB laminate depends on several factors, including the operating frequency range, power handling requirements, desired dielectric constant, loss tangent, thermal stability, and moisture resistance. Consider the specific needs of your application and consult with PCB manufacturers or material suppliers to choose the most suitable laminate material. -
What is the significance of the dielectric constant (Dk) in microwave PCB laminates?
The dielectric constant (Dk) of a microwave PCB laminate determines the speed of signal propagation and the impedance of transmission lines. A stable and well-controlled dielectric constant is essential for accurate circuit design, impedance matching, and minimizing signal reflections. The choice of Dk value depends on the specific application requirements and the desired circuit performance. -
How does the loss tangent (tan δ) affect the performance of microwave circuits?
The loss tangent (tan δ) quantifies the dielectric loss within a microwave PCB laminate. A low loss tangent is crucial for minimizing signal attenuation and power loss in microwave circuits. Laminates with low loss tangents enable longer transmission distances, improved signal-to-noise ratio, and reduced heat generation, leading to better overall performance and efficiency. -
What are the challenges in manufacturing microwave PCBs with low-loss laminates?
Manufacturing microwave PCBs with low-loss laminates requires careful consideration of various factors. The manufacturing process must ensure compatibility between the laminate material and other components, maintain controlled impedance and trace geometry, achieve proper multilayer lamination, and maintain a clean and controlled environment. Precise process control, accurate modeling, and rigorous testing are essential to overcome these challenges and produce high-quality microwave PCBs.
Conclusion
Microwave PCB laminates play a critical role in enabling reliable and efficient performance in high-frequency and high-power applications. The stability, low dielectric loss tangent, and other key characteristics of these laminates make them indispensable for microwave circuits used in telecommunications, radar systems, aerospace, defense, automotive, medical imaging, and test and measurement equipment.
The selection of the appropriate microwave PCB laminate material depends on the specific application requirements, considering factors such as dielectric constant, loss tangent, thermal stability, and moisture resistance. Manufacturers must employ advanced manufacturing techniques and maintain strict process control to ensure the desired electrical and mechanical properties are achieved.
As the demand for high-performance microwave systems continues to grow, advancements in microwave PCB laminate materials and manufacturing technologies will play a crucial role in enabling the next generation of wireless communications, radar systems, and other cutting-edge applications. By understanding the intricacies of microwave PCB laminates and their manufacturing considerations, designers and engineers can harness their potential to push the boundaries of microwave electronics and unlock new possibilities in the ever-evolving world of high-frequency technology.
No responses yet