What is FR1 PCB Material?
FR1 PCB material, also known as phenolic paper, is a low-cost substrate made from paper impregnated with a phenolic resin. It is the most basic and economical PCB material available in the market. FR1 PCBs are typically used for simple, low-frequency applications where cost is a primary concern.
Characteristics of FR1 PCB Material
- Low cost
- Low dielectric constant (around 4.5)
- Low thermal resistance
- Suitable for single-sided PCBs
- Limited electrical and mechanical properties
Applications of FR1 PCB Material
- Simple consumer electronics
- Low-frequency circuits
- Prototype boards
- Educational projects
What is FR2 PCB Material?
FR2 PCB material, also referred to as phenolic cotton paper, is a step up from FR1 in terms of performance and durability. It is made by impregnating cotton paper with phenolic resin, resulting in improved mechanical and electrical properties compared to FR1.
Characteristics of FR2 PCB Material
- Moderate cost
- Higher dielectric constant than FR1 (around 4.8)
- Better thermal resistance than FR1
- Suitable for single-sided and double-sided PCBs
- Improved mechanical strength
Applications of FR2 PCB Material
- Consumer electronics
- Low-frequency applications
- Automotive electronics
- Industrial control systems
What is FR3 PCB Material?
FR3 PCB material, known as epoxy paper, is a composite substrate made from paper impregnated with epoxy resin. It offers better performance and reliability compared to FR1 and FR2 materials. FR3 PCBs are commonly used in applications that require higher mechanical strength and better electrical properties.
Characteristics of FR3 PCB Material
- Higher cost than FR1 and FR2
- Good dielectric constant (around 4.7)
- Improved thermal resistance
- Suitable for single-sided and double-sided PCBs
- Enhanced mechanical strength and durability
Applications of FR3 PCB Material
- Industrial electronics
- Telecommunications equipment
- Medical devices
- Aerospace and defense systems
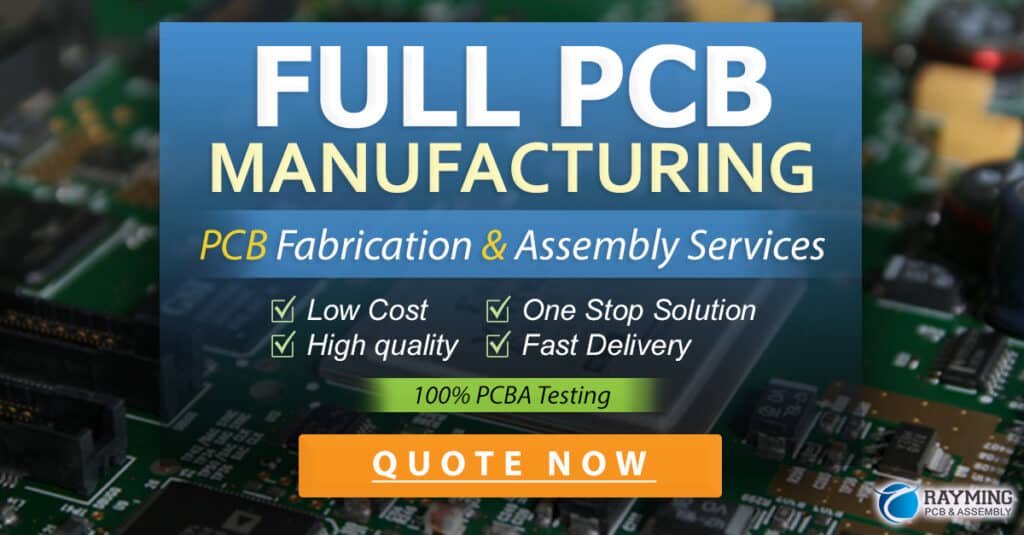
What is FR4 PCB Material?
FR4 PCB material, also known as glass-reinforced epoxy laminate, is the most widely used substrate in the PCB industry. It is made by impregnating woven fiberglass cloth with epoxy resin, resulting in excellent mechanical, thermal, and electrical properties. FR4 PCBs are the go-to choice for a wide range of applications, from consumer electronics to high-performance industrial systems.
Characteristics of FR4 PCB Material
- Higher cost compared to FR1, FR2, and FR3
- Excellent dielectric constant (around 4.5)
- High thermal resistance
- Suitable for multi-layer PCBs
- Superior mechanical strength and durability
- Good dimensional stability
- Flame retardant properties
Applications of FR4 PCB Material
- High-speed digital circuits
- RF and microwave applications
- Automotive electronics
- Medical devices
- Industrial control systems
- Aerospace and defense applications
Comparative Analysis of FR1, FR2, FR3, and FR4 Materials
To better understand the differences between FR1, FR2, FR3, and FR4 PCB materials, let’s compare their key properties and characteristics in a tabular format:
Property | FR1 | FR2 | FR3 | FR4 |
---|---|---|---|---|
Base Material | Paper | Cotton Paper | Paper | Fiberglass |
Resin | Phenolic | Phenolic | Epoxy | Epoxy |
Dielectric Constant | ~4.5 | ~4.8 | ~4.7 | ~4.5 |
Thermal Resistance | Low | Moderate | Good | High |
Mechanical Strength | Low | Moderate | Good | Excellent |
Dimensional Stability | Poor | Moderate | Good | Excellent |
Suitable for Multi-layer | No | Limited | Limited | Yes |
Cost | Low | Moderate | High | Higher |
As evident from the table, FR4 material offers the best overall performance, with excellent thermal, mechanical, and electrical properties. However, it comes at a higher cost compared to the other materials. FR1 and FR2 are more economical options for simple, low-frequency applications, while FR3 provides a balance between cost and performance for intermediate-level applications.
Frequently Asked Questions (FAQ)
-
Q: Can FR1 PCB material be used for multi-layer boards?
A: No, FR1 material is not suitable for multi-layer PCBs due to its limited electrical and mechanical properties. It is primarily used for single-sided PCBs in simple, low-frequency applications. -
Q: What is the main difference between FR2 and FR3 PCB materials?
A: The main difference between FR2 and FR3 is the type of resin used. FR2 uses phenolic resin, while FR3 uses epoxy resin. As a result, FR3 offers better mechanical strength, thermal resistance, and electrical properties compared to FR2. -
Q: Why is FR4 the most widely used PCB material?
A: FR4 is the most popular choice for PCBs because it offers a combination of excellent mechanical, thermal, and electrical properties. Its glass-reinforced epoxy construction provides superior dimensional stability, making it suitable for multi-layer boards and high-performance applications. -
Q: Can FR3 PCB material be used for high-frequency applications?
A: While FR3 offers improved performance compared to FR1 and FR2, it may not be the best choice for high-frequency applications. FR4 material is generally preferred for such applications due to its better dielectric constant and thermal resistance. -
Q: Are there any specific safety considerations when working with these PCB materials?
A: When handling and processing PCB materials, it is important to follow proper safety guidelines. Some materials, such as those containing epoxy resin, may release fumes during the manufacturing process. Adequate ventilation and personal protective equipment (PPE) should be used to ensure the safety of workers. Additionally, proper disposal methods should be followed for any waste generated during PCB fabrication.
Conclusion
Understanding the differences between FR1, FR2, FR3, and FR4 PCB materials is crucial for selecting the most suitable substrate for your specific application. Each material has its own set of characteristics, advantages, and limitations. FR1 and FR2 are cost-effective options for simple, low-frequency applications, while FR3 provides a balance between cost and performance for intermediate-level projects. FR4 stands out as the most versatile and widely used material, offering excellent mechanical, thermal, and electrical properties for a wide range of applications, including high-speed digital circuits and multi-layer boards.
When choosing a PCB material, consider factors such as the intended application, operating frequency, environmental conditions, and budget constraints. By carefully evaluating these aspects and understanding the properties of each material, you can make an informed decision and ensure the optimal performance and reliability of your PCB design.
No responses yet