Introduction
When it comes to assembling printed circuit boards (PCBs), there are various methods used to secure components and create reliable connections. Two common techniques are countersinking and counterboring. Although they may seem similar, they serve different purposes and have distinct advantages. In this article, we will explore the differences between countersinking and counterboring, their applications in PCB assembly, and how to effectively use them to achieve optimal results.
What is Countersinking?
Countersinking is a process that involves creating a conical recess in a PCB to allow the head of a screw or bolt to sit flush with the surface. This technique is commonly used when a flat surface is required for aesthetic or functional reasons. Countersinking is achieved using a countersink drill bit, which has a conical shape that matches the angle of the screw head.
Advantages of Countersinking
- Flush Surface: Countersinking allows the screw head to sit flush with the PCB surface, creating a smooth and even finish. This is especially important when the PCB needs to fit into a tight space or when a flat surface is required for other components to be mounted on top.
- Reduced Protrusion: By accommodating the screw head within the countersunk recess, the overall protrusion of the fastener is minimized. This can be beneficial in applications where clearance is limited or where a low profile is desired.
- Improved Aesthetics: Countersinking provides a clean and professional appearance to the PCB assembly. The flush screw heads create a seamless look and enhance the overall visual appeal of the finished product.
Disadvantages of Countersinking
- Limited Strength: Countersinking removes material from the PCB, which can weaken the surrounding area. This can be a concern in applications where high mechanical stress is expected or where the PCB thickness is already minimal.
- Precision Required: Creating a countersunk hole requires precise drilling to ensure the correct depth and angle are achieved. Inaccuracies in countersinking can lead to an uneven surface or improper seating of the screw head.
- Specialized Equipment: Countersinking requires the use of specific countersink drill bits, which may not be readily available in all manufacturing facilities. This can add to the tooling costs and require additional inventory management.
What is Counterboring?
Counterboring is a technique that involves drilling a cylindrical recess into the PCB to accommodate the entire head of a screw or bolt. Unlike countersinking, which creates a conical recess, counterboring results in a flat-bottomed hole that allows the screw head to sit completely below the surface of the PCB.
Advantages of Counterboring
- Increased Strength: Counterboring maintains more of the PCB material around the hole compared to countersinking. This provides additional strength and stability, especially in applications where the PCB is subjected to high mechanical stress or vibration.
- Consistent Depth: Counterboring allows for precise control over the depth of the recess. By using a drill bit with a specific depth stop, the counterbore can be created with consistent depth across multiple holes, ensuring uniform seating of the screw heads.
- Versatility: Counterboring can accommodate various screw head shapes and sizes, including pan heads, button heads, and socket caps. This versatility allows for greater flexibility in component selection and assembly design.
Disadvantages of Counterboring
- Increased Footprint: Counterboring requires a larger hole diameter compared to countersinking to accommodate the entire screw head. This can take up more space on the PCB and may limit the available routing area for traces and components.
- Reduced Clearance: Since the screw head sits below the surface of the PCB, counterboring may reduce the clearance between the screw head and any components or obstacles located beneath the PCB. This should be considered during the design phase to ensure adequate clearance is maintained.
- Additional Machining: Creating a counterbored hole typically requires a two-step drilling process – first drilling the clearance hole, then creating the counterbore using a separate drill bit. This additional machining step can increase production time and cost compared to countersinking.
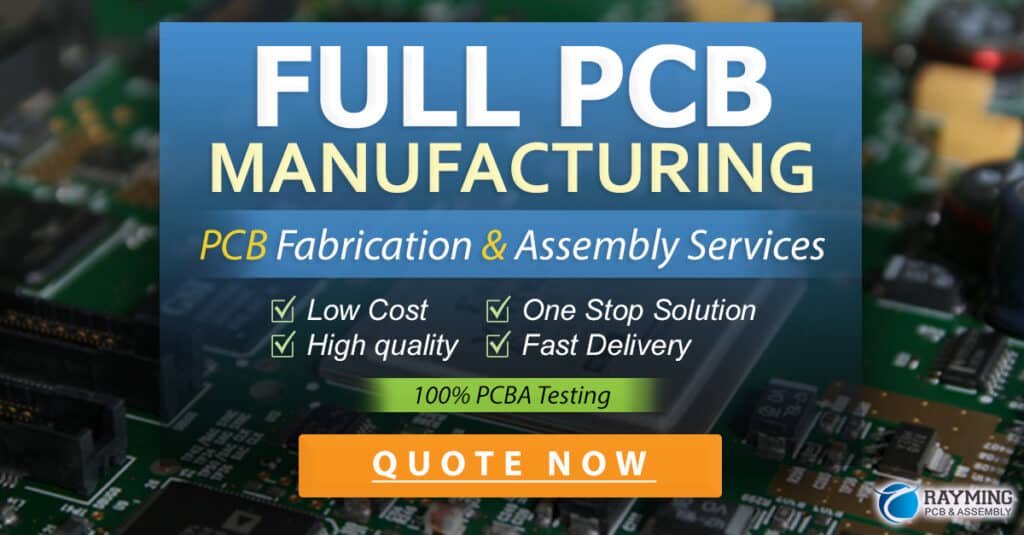
Choosing Between Countersinking and Counterboring
When deciding between countersinking and counterboring for PCB assembly, several factors need to be considered:
-
Strength Requirements: If the PCB will be subjected to high mechanical stress or vibration, counterboring may be preferred due to its ability to maintain more material around the hole, providing added strength and stability.
-
Surface Finish: If a flush surface is required for aesthetic purposes or to accommodate other components, countersinking is the better choice. Countersinking allows the screw head to sit flush with the PCB surface, creating a smooth and even finish.
-
Clearance Constraints: Consider the available space and clearance requirements both above and below the PCB. Countersinking results in minimal protrusion above the surface, while counterboring may reduce the clearance below the PCB due to the recessed screw head.
-
Screw Head Type: The shape and size of the screw head will influence the choice between countersinking and counterboring. Countersinking is typically used with flat head screws, while counterboring can accommodate a wider range of screw head types, such as pan heads or button heads.
-
Manufacturing Capabilities: Consider the available manufacturing equipment and tooling. Countersinking requires specific countersink drill bits, while counterboring may necessitate additional drilling steps. Ensure that the chosen method aligns with the manufacturing capabilities and resources available.
Effectively Implementing Countersinking and Counterboring
To effectively implement countersinking and counterboring in PCB assembly, follow these best practices:
-
Design for Manufacturability: During the PCB design phase, consider the specific requirements for countersinking or counterboring. Ensure that the hole sizes, depths, and locations are clearly specified in the design files and communicated to the manufacturing team.
-
Select Appropriate Drill Bits: Use high-quality drill bits specifically designed for countersinking or counterboring. Countersink drill bits should have the correct angle to match the screw head, while counterbore drill bits should have a depth stop to ensure consistent recess depth.
-
Optimize Drilling Parameters: Adjust the drilling speed, feed rate, and depth control to achieve clean and accurate holes. Proper drilling parameters minimize burrs, tear-out, and other defects that can affect the quality of the countersunk or counterbored holes.
-
Implement Quality Control: Establish a robust quality control process to inspect the countersunk or counterbored holes for consistency, depth, and surface finish. Use gauges or depth micrometers to verify that the holes meet the specified dimensions and tolerances.
-
Consider Automated Solutions: For high-volume production or complex PCB designs, consider investing in automated countersinking or counterboring equipment. These machines offer precise depth control, consistent results, and increased efficiency compared to manual drilling methods.
FAQ
-
What is the main difference between countersinking and counterboring?
Countersinking creates a conical recess to allow the screw head to sit flush with the PCB surface, while counterboring creates a cylindrical recess to accommodate the entire screw head below the surface. -
When should I choose countersinking over counterboring?
Countersinking is preferred when a flush surface finish is required for aesthetic or functional purposes, or when minimal protrusion above the PCB surface is desired. -
What are the advantages of counterboring?
Counterboring offers increased strength by maintaining more material around the hole, provides consistent depth control, and accommodates various screw head shapes and sizes. -
Can countersinking and counterboring be used together on the same PCB?
Yes, countersinking and counterboring can be used together on the same PCB, depending on the specific requirements of different components or mounting locations. -
How can I ensure the quality of countersunk or counterbored holes?
Implement a robust quality control process that includes visual inspection, depth measurements, and verification of hole dimensions using gauges or depth micrometers. Adjust drilling parameters and use appropriate drill bits to achieve consistent and accurate results.
Conclusion
Countersinking and counterboring are two distinct methods used in PCB assembly to accommodate screw heads and create secure connections. Countersinking offers a flush surface finish and minimal protrusion, while counterboring provides increased strength and versatility in screw head accommodation. When deciding between the two techniques, consider factors such as strength requirements, surface finish, clearance constraints, screw head type, and manufacturing capabilities.
By understanding the advantages and disadvantages of each method and following best practices for implementation, you can effectively incorporate countersinking and counterboring into your PCB assembly process. This will result in reliable, aesthetically pleasing, and functionally optimized PCB assemblies that meet the specific requirements of your application.
Feature | Countersinking | Counterboring |
---|---|---|
Recess Shape | Conical | Cylindrical |
Screw Head Accommodation | Flush with surface | Below surface |
Strength | Reduced material around hole | Increased material around hole |
Surface Finish | Flush and smooth | Recessed screw head |
Clearance | Minimal protrusion above surface | Reduced clearance below surface |
Screw Head Compatibility | Typically flat head screws | Various head shapes and sizes |
Manufacturing Process | Single-step drilling | Two-step drilling |
Remember, the choice between countersinking and counterboring depends on the specific requirements of your PCB assembly. By carefully considering the factors discussed in this article and implementing the appropriate technique, you can achieve optimal results and create high-quality, reliable PCB assemblies.
No responses yet