What is a PCB?
A printed circuit board (PCB) is a flat insulating board that holds and connects electronic components using conductive pathways, tracks or signal traces etched from copper sheets laminated onto a non-conductive substrate. It mechanically supports and electrically connects electronic components using conductive tracks, pads and other features etched from one or more sheet layers of copper laminated onto and/or between sheet layers of a non-conductive substrate.
PCBs are inexpensive, can be highly reliable, and can be made with repeatability, so they are used in virtually all but the simplest commercially produced electronic devices. PCBs are used in computers, servers, laptops, tablets, smartphones, televisions, stereos, digital cameras, and more.
The Anatomy of a PCB
To understand how PCBs work, it’s helpful to know the different parts that make them up:
Substrate
The substrate is the foundation of the PCB and what everything else is built on top of. It’s usually made of fiberglass or another insulating material. The substrate provides mechanical support for the components and copper traces.
Copper Layer
Thin layers of copper foil, typically 1 oz or 2 oz copper, are laminated to one or both sides of the substrate. The copper is etched away to leave behind the conductive traces that connect the components.
Solder Mask
The solder mask is the (usually) green coating over the copper layer. It protects the copper from oxidation and prevents solder from bridging between traces. Openings in the solder mask expose the pads where components will be soldered.
Silkscreen
The white silkscreen layer is used to label components, test points, PCB info and logos, etc. It serves as a readable reference on the board.
Drilled Holes
Holes are drilled through the PCB to allow leads from through-hole components to pass through for soldering. They’re also used for mounting, edge connectors, etc. Holes come in two main types:
– Plated Through Holes (PTH) – These holes are copper plated to provide electrical connections between layers
– Non-plated Through Holes (NPTH) – Used for mounting or other mechanical purposes
Vias
Vias are small PTH used specifically to route a trace vertically from one layer to another. There are a few different types of vias:
Via Type | Description |
---|---|
Through Via | Goes through all layers, top to bottom |
Blind Via | Connects an outer layer to an inner layer, but doesn’t go through the whole board |
Buried Via | Connects inner layers without being visible on the outer layers |
Types of PCBs
PCBs come in a variety of different types to suit different applications. The main types are:
Single Layer PCB
Has copper traces on only one side of the substrate. Components are usually only placed on one side. Simple and inexpensive but limited in complexity.
Double Layer PCB
Has copper on both sides of the substrate. Traces on top and bottom layers are connected with vias. Allows for more complex circuits than single layer.
Multi-Layer PCB
Has three or more copper layers with insulators in between. The inner layers are usually dedicated ground and power planes. Used for complex, high density designs like computer motherboards and smartphones. Much more expensive than simpler types.
Flexible PCB
Uses a flexible substrate like polyimide. Can be bent, twisted or folded. Used in applications where the board needs to fit in a tight space or needs to flex during use, like a laptop hinge or wearable device. More difficult to manufacture than rigid boards.
Rigid-Flex PCB
A combination of rigid and flexible sections. Allows flexing between rigid areas for 3D configurations. Used in aerospace, medical devices, etc. Very complex and expensive compared to standard rigid boards.
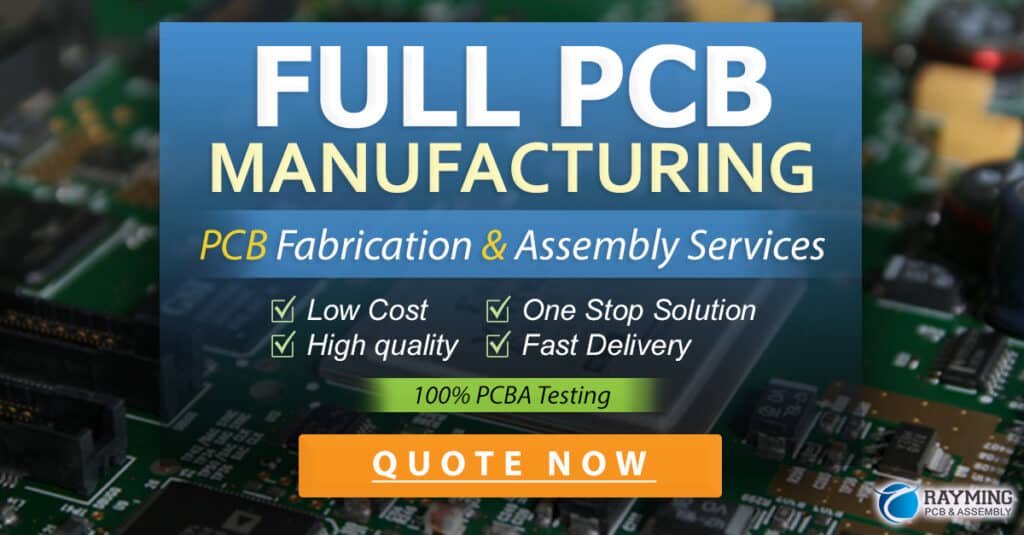
PCB Design Process
Designing a PCB is a multi-step process that requires specialized knowledge and software tools. The basic steps are:
-
Schematic Capture – The circuit is first defined as a schematic diagram showing the components and connections. This is done using electronic design automation (EDA) software.
-
Component Placement – The component footprints are arranged on the board outline for optimal positioning, taking into account mechanical and electrical requirements. Autorouting features in the software can assist with this.
-
Routing – The traces are routed to make the connections between components as defined in the schematic. The EDA tools assist in obeying design rules for trace width, clearance, etc. High density boards usually require manual routing by a PCB layout specialist.
-
Design Rule Checking – The software performs automated checks for any design rule violations like traces too close together, incomplete connections, etc. The design is revised until it passes all DRC.
-
Output Files Generation – Once the design is finalized, the fabrication files are generated, usually Gerber or ODB++ Format. These include the copper layer images, drill files, etc that the board house needs to manufacture the PCB.
PCB Manufacturing Process
Once the design is complete, the fabrication files are sent to a PCB manufacturer for production. The process follows these general steps:
-
Material Preparation – The inner layer copper foils are laminated onto the substrate core material.
-
Drilling – Holes are drilled according to the drill file using CNC machines or laser drills.
-
Plating – Through holes are made conductive using electroless copper deposition followed by electroplating. A thin copper layer is also plated on top of the pads and traces to protect them.
-
Outer Layer Imaging – The outer layer copper patterns are formed by photolithography and etching. A photoresist is applied, the Gerber image is projected onto it, then the unmasked copper is etched away.
-
Soldermask Application – The soldermask ink is applied over the outer copper layers and cured.
-
Silkscreen Printing – The component notation is printed onto the soldermask using silkscreen.
-
Surface Finish – A surface finish like HASL, ENIG, or Immersion Silver is applied to the exposed copper to prevent oxidation and enhance solderability.
-
Fabrication – Slots, cutouts and the board perimeter are routed out according to the mechanical drawings. The individual boards are routed out of the panel. Electrical test may also be done at this stage.
Assembling the PCB
After the bare PCB is manufactured, the components need to be soldered on to complete the assembly. For through-hole components, this can be done manually, but surface mount parts require special equipment and a skilled operator. The process usually goes like this:
-
Solder Paste Printing – A stainless steel stencil is placed over the PCB and solder paste is applied to the pads through the holes in the stencil. The paste is a mixture of tiny solder balls and flux.
-
Pick and Place – The components are picked up from tapes, tubes or trays by a machine and precisely placed onto the PCB pads in the solder paste.
-
Reflow Soldering – The populated PCB is passed through a reflow oven on a conveyor. The solder melts in the high temperature zone and forms solder joints as it cools, making the electrical and mechanical connections.
-
Inspection and Test – The assembled PCB is visually inspected and may undergo electrical testing like in-circuit test (ICT) or functional test depending on the requirements.
PCB Design Considerations
Designing a successful PCB requires careful planning and attention to many details. Some of the key considerations include:
Schematic Design
The schematic captures the critical information about component selection and interconnection. Mistakes here can be costly later on. Be sure to:
- Select the right components and packages for the requirements and budget
- Determine proper component values (resistance, capacitance, etc)
- Include proper protection and filtering on I/O, power lines
- Decouple ICs with bypass capacitors
- Use net labels to clearly define connections
Layout
The physical layout of the board has a major impact on manufacturability, reliability, signal integrity and EMC. Important aspects are:
- Creating a stackup with the proper number of layers, materials and thicknesses
- Defining the board outline and component placement
- Routing critical traces first, like signals and supplies
- Providing adequate clearances between traces, components and the board edge
- Having solid ground and power planes for shielding and low impedance paths
- Minimizing vias when possible
- Avoiding 90 degree corners
- Following the manufacturer’s guidelines and IPC standards
Manufacturability
Designing with manufacturing in mind from the beginning can save time and money in the end. Follow these guidelines:
- Use standard materials, thicknesses and surface finishes when possible
- Make the design as simple as it can be and still meet requirements
- Use larger vias, traces and spacing in high voltage areas
- Provide clear space around holes for press fit pins or connectors
- Add fiducials on the outer layers to allow automated assembly equipment to register the location of the board
- Define the solder mask clearance properly to prevent bridging or poor joints
- Panelize properly to allow easy depanelization without damaging the boards
Frequently Asked Questions about PCBs
What are the advantages of using a PCB vs. point-to-point wiring?
PCBs offer several advantages over point-to-point wiring:
- Much more compact and lighter weight
- Can be made identically in large quantities
- Automated assembly for higher quality and throughput
- Easier to test and troubleshoot
- More reliable in high vibration/shock environments
- Lower cost in volume
What’s the difference between through-hole and surface mount components?
Through-hole components have long metal leads that are inserted into holes in the PCB and soldered to pads on the opposite side. Surface mount devices (SMD) have small metal tabs or pads that are soldered directly onto the surface of the PCB. SMDs can be much smaller than through-hole parts, allowing for higher component density. They are also more suitable for automated assembly.
How small of a trace or space can PCB manufacturers make?
The smallest trace width and spacing depends on the PCB fabricator’s capabilities and the specific process being used. In general, most manufacturers can reliably produce trace widths down to about 0.006″ (0.15mm) and spacings down to 0.008″ (0.20mm). More advanced processes can go even smaller. Consult with your specific PCB vendor to determine what they are able to do.
What are some common PCB design mistakes to avoid?
Here are a few common pitfalls to watch out for in PCB design:
- Incorrect footprints or pinouts
- Forgetting to connect a ground or power pin on an IC
- Traces too thin to handle the required current
- Inadequate clearances for the voltage levels used
- Lack of ESD protection on sensitive components
- Improper terminations on high speed signals
- Incorrect hole sizes for through-hole components
- Inadequate heatsinking for power devices
What determines the cost of a PCB?
Many factors influence the cost of producing a PCB, including:
- The number of layers
- The size of the board
- The quantity being ordered
- The component density and sizes
- The materials and surface finishes specified
- The grade of the product (commercial, military, aerospace, etc)
- The location of the PCB manufacturer
In general, higher quantity, fewer layers, and larger sizes will result in a lower cost per board. The cheapest boards will be single or double sided, while complex multilayer boards with microvias and HDI features will be the most expensive. The grade of the end product also makes a difference, as higher reliability requirements call for more stringent manufacturing controls and testing.
Conclusion
We’ve covered a lot of ground in this guide, and you should now have a solid understanding of what PCBs are, how they are made, and what goes into designing them. Of course, there is much more to learn, and we’ve only really scratched the surface of this complex field.
To recap, a PCB is the foundation of most modern electronic devices. It provides mechanical support and electrical interconnectivity for the components that make our gadgets work. PCBs can be simple single-sided boards or complex multi-layer, high density substrates.
The design process starts with a schematic, moves to layout, and then on to fabrication and assembly. Designers must juggle many constraints and considerations throughout this process to create a PCB that meets all the functional, reliability, and cost requirements.
If you are interested in learning more, there are many resources available. Online forums, tutorials, and courses can help you dive deeper into the world of PCBs. And of course, one of the best ways to learn is by doing. Designing and building your own PCBs is a challenging but rewarding pursuit.
So what are you waiting for? Start designing your own PCBs today!
No responses yet