Introduction to Substrate-Bonded PCBs
Printed Circuit Boards (PCBs) have revolutionized the electronics industry by providing a reliable and efficient method for connecting electronic components. Among the various types of PCBs, Substrate-Bonded PCBs have gained significant attention due to their unique manufacturing process and superior performance characteristics. In this article, we will explore the mSAP (modified Semi-Additive Process) PCB, a specific type of Substrate-Bonded PCB that utilizes an additive copper layer fabrication technique.
What is a Substrate-Bonded PCB?
A Substrate-Bonded PCB is a type of printed circuit board where the copper traces and pads are directly bonded to the substrate material, typically a dielectric layer. This bonding process eliminates the need for an additional adhesive layer between the copper and the substrate, resulting in several advantages over traditional PCB manufacturing methods.
Advantages of Substrate-Bonded PCBs
- Improved Thermal Performance: The direct bonding of copper to the substrate enhances heat dissipation, allowing for better thermal management of electronic components.
- Increased Reliability: The elimination of the adhesive layer reduces the risk of delamination and improves the overall reliability of the PCB.
- Higher Signal Integrity: Substrate-Bonded PCBs offer improved signal integrity due to the reduced dielectric thickness and the absence of an adhesive layer.
- Compact Design: The direct bonding process enables the fabrication of finer copper traces and smaller vias, facilitating the design of more compact and dense PCBs.
mSAP PCB: The Modified Semi-Additive Process
What is mSAP?
mSAP, short for modified Semi-Additive Process, is a specific manufacturing technique used for Substrate-Bonded PCBs. In this process, a thin layer of copper is deposited onto the substrate using an additive process, such as electroless plating. The copper layer is then patterned and etched to create the desired circuit traces and pads.
mSAP vs. Traditional PCB Manufacturing
Traditional PCB manufacturing methods, such as subtractive etching, involve starting with a copper-clad laminate and etching away the unwanted copper to create the circuit pattern. In contrast, mSAP uses an additive process to selectively deposit copper only where it is needed. This approach offers several advantages:
- Reduced Material Waste: The additive nature of mSAP minimizes the amount of copper that needs to be etched away, reducing material waste and environmental impact.
- Finer Feature Sizes: mSAP allows for the fabrication of smaller trace widths and spacing, enabling higher circuit density and more compact designs.
- Improved Yield: The selective deposition of copper reduces the risk of over-etching or under-etching, resulting in higher manufacturing yields.
mSAP Process Steps
The mSAP process typically involves the following steps:
- Substrate Preparation: The substrate material, usually a dielectric layer, is cleaned and prepared for copper deposition.
- Seed Layer Deposition: A thin layer of copper, known as the seed layer, is deposited onto the substrate using electroless plating.
- Photoresist Application: A photoresist material is applied to the surface of the seed layer.
- Exposure and Development: The photoresist is exposed to UV light through a patterned mask and then developed to create the desired circuit pattern.
- Copper Plating: Additional copper is electroplated onto the exposed areas of the seed layer to achieve the desired trace thickness.
- Resist Removal: The remaining photoresist is stripped away, leaving the patterned copper traces on the substrate.
- Etching: The exposed seed layer is etched away, electrically isolating the copper traces.
- Surface Finish: A surface finish, such as ENIG (Electroless Nickel Immersion Gold) or HASL (Hot Air Solder Leveling), is applied to protect the copper traces and provide a solderable surface.
Substrate Materials for mSAP PCBs
The choice of substrate material is crucial in the design and fabrication of mSAP PCBs. The substrate serves as the foundation for the copper traces and provides the necessary electrical insulation and mechanical support. Some commonly used substrate materials for mSAP PCBs include:
FR-4
FR-4 is a glass-reinforced epoxy laminate that is widely used in the PCB industry. It offers good mechanical strength, dimensional stability, and electrical insulation properties. FR-4 is suitable for a wide range of applications and is compatible with the mSAP process.
Polyimide
Polyimide is a high-performance polymer that exhibits excellent thermal stability, chemical resistance, and mechanical properties. It is often used in applications that require high temperature resistance or flexibility. Polyimide substrates can be used in mSAP PCBs for demanding applications such as aerospace, automotive, and medical devices.
Liquid Crystal Polymer (LCP)
LCP is a thermoplastic polymer that offers a unique combination of properties, including low dielectric constant, low loss tangent, and high thermal stability. LCP substrates are particularly suitable for high-frequency applications, such as 5G wireless communication and radar systems. LCP can be used as a substrate material for mSAP PCBs to achieve superior high-frequency performance.
Comparison of Substrate Materials
Substrate Material | Dielectric Constant | Dissipation Factor | Thermal Stability | Flexibility |
---|---|---|---|---|
FR-4 | 4.2-4.5 | 0.02 | Good | Rigid |
Polyimide | 3.5-3.8 | 0.002-0.008 | Excellent | Flexible |
LCP | 2.9-3.2 | 0.002-0.004 | Excellent | Rigid or Flexible |
The choice of substrate material depends on the specific requirements of the application, such as operating temperature, frequency range, mechanical properties, and cost considerations.
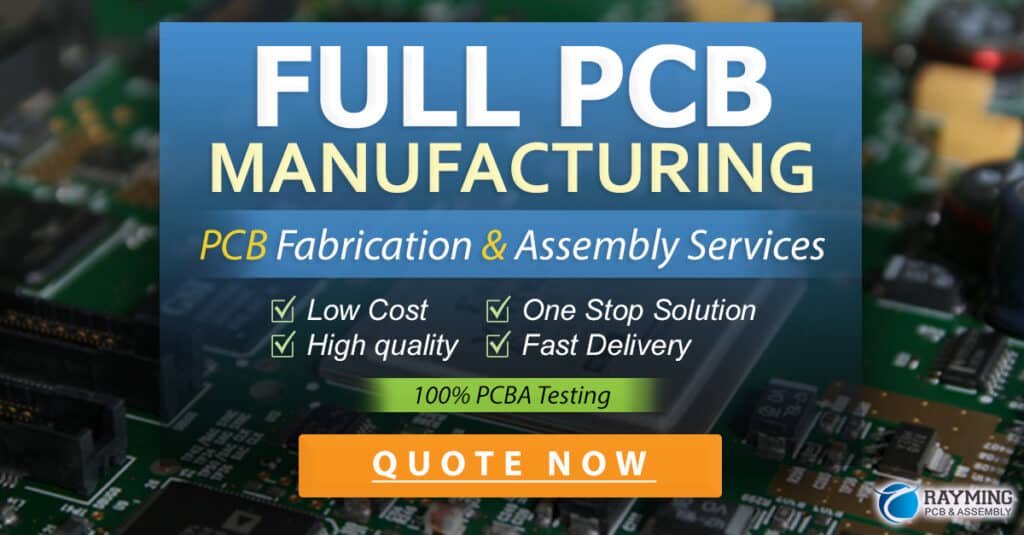
Design Considerations for mSAP PCBs
When designing mSAP PCBs, several factors need to be taken into account to ensure optimal performance and manufacturability. Some key design considerations include:
Trace Width and Spacing
mSAP technology enables the fabrication of finer trace widths and smaller spacing compared to traditional PCB manufacturing methods. Designers should take advantage of this capability to achieve higher circuit density and more compact layouts. However, it is important to adhere to the minimum trace width and spacing guidelines provided by the PCB manufacturer to ensure reliable manufacturing.
Via Design
Vias are used to interconnect different layers of a PCB. In mSAP PCBs, the via design should be optimized to minimize the via size and improve signal integrity. Microvias, which are small-diameter vias that only span a few layers, are commonly used in mSAP designs to achieve higher density and better electrical performance.
Impedance Control
Impedance control is critical in high-speed digital circuits and high-frequency applications. mSAP PCBs offer the advantage of tighter impedance control due to the reduced dielectric thickness and the absence of an adhesive layer. Designers should carefully consider the trace geometry, substrate material, and layer stack-up to achieve the desired impedance characteristics.
Thermal Management
Proper thermal management is essential to ensure the reliability and performance of electronic components. mSAP PCBs provide improved thermal performance due to the direct bonding of copper to the substrate. Designers should incorporate thermal vias and copper planes to facilitate heat dissipation and minimize thermal hotspots.
Signal Integrity Analysis
Signal integrity analysis is crucial in high-speed digital circuits to ensure reliable data transmission and minimize signal distortion. Designers should perform signal integrity simulations to evaluate the impact of trace geometry, via placement, and layer stack-up on the signal quality. Tools such as electromagnetic field solvers and time-domain reflectometry (TDR) analysis can be used to optimize the PCB design for optimal signal integrity.
Applications of mSAP PCBs
mSAP PCBs find applications in various industries and product categories where high performance, reliability, and compact form factors are essential. Some notable applications include:
Wireless Communication Devices
mSAP PCBs are widely used in wireless communication devices, such as smartphones, tablets, and IoT (Internet of Things) devices. The ability to fabricate fine traces and achieve higher circuit density enables the integration of multiple wireless standards, such as 5G, Wi-Fi, Bluetooth, and GPS, into a single compact PCB.
Automotive Electronics
The automotive industry is increasingly adopting advanced electronic systems for safety, infotainment, and autonomous driving functionalities. mSAP PCBs are well-suited for automotive applications due to their improved reliability, thermal performance, and signal integrity. They are used in various automotive subsystems, such as engine control units (ECUs), advanced driver assistance systems (ADAS), and in-vehicle infotainment systems.
Medical Devices
Medical devices require high reliability, precision, and miniaturization. mSAP PCBs are used in a wide range of medical applications, including implantable devices, diagnostic equipment, and wearable health monitoring systems. The compact form factor and improved signal integrity of mSAP PCBs enable the development of smaller and more advanced medical devices.
Aerospace and Defense
Aerospace and defense applications demand PCBs that can withstand harsh environments, extreme temperatures, and high levels of vibration and shock. mSAP PCBs, particularly those using polyimide substrates, are well-suited for these demanding applications. They are used in avionics systems, satellite communications, radar systems, and military equipment.
High-Performance Computing
mSAP PCBs are employed in high-performance computing applications, such as servers, data centers, and supercomputers. The improved signal integrity and thermal performance of mSAP PCBs enable faster data processing, higher bandwidth, and more efficient cooling of electronic components.
Future Trends and Advancements
The mSAP PCB technology continues to evolve and adapt to the ever-increasing demands of the electronics industry. Some future trends and advancements in mSAP PCBs include:
Higher Circuit Density
As electronic devices become more compact and feature-rich, there is a constant push for higher circuit density in PCBs. mSAP technology is expected to advance further, enabling even finer trace widths and smaller via sizes. This will allow for the integration of more components and functionalities into smaller PCB form factors.
Advanced Substrate Materials
Research and development efforts are ongoing to identify and develop new substrate materials that offer improved electrical, thermal, and mechanical properties. These advanced substrate materials, such as low-loss dielectrics and high-thermal-conductivity materials, will enhance the performance of mSAP PCBs in demanding applications.
3D Packaging Integration
mSAP PCBs are well-suited for 3D packaging integration, where multiple PCBs are stacked and interconnected using through-silicon vias (TSVs) or other advanced packaging techniques. 3D packaging enables higher packaging density, shorter signal paths, and better thermal management. The combination of mSAP PCBs and 3D packaging will drive the development of more compact and high-performance electronic systems.
Sustainable Manufacturing
As environmental concerns gain prominence, there is a growing emphasis on sustainable manufacturing practices in the PCB industry. mSAP technology, with its reduced material waste and more efficient use of resources, aligns well with sustainable manufacturing goals. Further advancements in eco-friendly substrate materials and processing techniques are expected to make mSAP PCBs even more environmentally friendly.
FAQs
-
What is the main difference between mSAP PCBs and traditional PCBs?
mSAP PCBs use an additive process to deposit copper directly onto the substrate, while traditional PCBs start with a copper-clad laminate and etch away the unwanted copper. This difference in manufacturing process leads to several advantages for mSAP PCBs, such as finer trace widths, improved signal integrity, and reduced material waste. -
Can mSAP PCBs be used for flexible applications?
Yes, mSAP PCBs can be designed for flexible applications by using flexible substrate materials such as polyimide. Flexible mSAP PCBs offer the advantages of improved reliability, compact form factors, and the ability to conform to various shapes and contours. -
Are mSAP PCBs more expensive than traditional PCBs?
The cost of mSAP PCBs can be higher compared to traditional PCBs due to the specialized manufacturing process and equipment involved. However, the cost difference is often justified by the superior performance, reliability, and design flexibility offered by mSAP technology. As mSAP technology becomes more widespread and manufacturing processes are optimized, the cost gap is expected to narrow. -
What are the key design considerations for mSAP PCBs?
When designing mSAP PCBs, key considerations include trace width and spacing, via design, impedance control, thermal management, and signal integrity analysis. Designers should take advantage of the capabilities of mSAP technology while adhering to manufacturing guidelines and best practices to ensure optimal performance and manufacturability. -
What are the future trends in mSAP PCB technology?
Future trends in mSAP PCB technology include higher circuit density, advanced substrate materials, 3D packaging integration, and sustainable manufacturing practices. These advancements will enable the development of more compact, high-performance, and environmentally friendly electronic devices across various industries.
Conclusion
mSAP PCBs, with their substrate-bonded additive copper layer fabrication process, offer numerous advantages over traditional PCB manufacturing methods. The improved thermal performance, increased reliability, higher signal integrity, and compact design capabilities make mSAP PCBs well-suited for a wide range of applications, including wireless communication devices, automotive electronics, medical devices, aerospace and defense systems, and high-performance computing.
As the electronics industry continues to evolve, mSAP technology is expected to play a crucial role in enabling the development of more advanced, reliable, and compact electronic systems. With ongoing research and advancements in substrate materials, manufacturing processes, and design techniques, mSAP PCBs are poised to meet the ever-increasing demands of the digital age.
By understanding the principles, advantages, and design considerations of mSAP PCBs, engineers and designers can leverage this technology to create innovative and high-performance electronic products that push the boundaries of what is possible.
No responses yet