What are Proximity Switches?
A proximity switch, also known as a proximity sensor, is a non-contact sensing device that detects the presence or absence of an object within its sensing range. These switches operate by generating an electromagnetic field or using capacitive, ultrasonic, or optical sensing technologies. When an object enters the sensing field, the switch triggers an output signal, indicating the object’s presence.
How Do Proximity Switches Work?
The working principle of proximity switches varies depending on the type of sensing technology employed. Here are the most common types:
- Inductive Proximity Switches:
- Inductive proximity switches generate a high-frequency electromagnetic field around the sensing face.
- When a metallic object enters this field, it creates eddy currents that alter the switch’s oscillation amplitude.
-
The switch detects these changes and triggers an output signal.
-
Capacitive Proximity Switches:
- Capacitive proximity switches create an electrostatic field around the sensing face.
- When an object with a different dielectric constant than air enters this field, it changes the switch’s capacitance.
-
The switch detects these changes and generates an output signal.
-
Ultrasonic Proximity Switches:
- Ultrasonic proximity switches emit high-frequency sound waves and measure the time it takes for the waves to bounce back from an object.
-
By calculating the time of flight, the switch determines the presence and distance of the object.
-
Optical Proximity Switches:
- Optical proximity switches use light (visible, infrared, or laser) to detect objects.
- They consist of an emitter that sends light and a receiver that detects the reflected light from the object.
- The switch triggers an output signal when the received light intensity exceeds a certain threshold.
Types of Proximity Switches
Proximity switches come in various types, each with its own characteristics and application suitability. Let’s explore the main types:
1. Inductive Proximity Switches
Inductive proximity switches are the most common type and are widely used in industrial applications. They are designed to detect metallic objects and are ideal for harsh environments.
Key features of inductive proximity switches:
– Sensing range: typically up to 60 mm
– Target material: ferrous and non-ferrous metals
– Robust construction: resistant to dust, dirt, and vibrations
– High switching frequency: up to 5 kHz
– Output types: PNP, NPN, NO, NC, or NAMUR
2. Capacitive Proximity Switches
Capacitive proximity switches can detect both metallic and non-metallic objects, making them versatile in various applications.
Key features of capacitive proximity switches:
– Sensing range: typically up to 60 mm
– Target material: metals, plastics, liquids, powders, and granular materials
– Adjustable sensitivity: allows detection of materials with different dielectric constants
– Output types: PNP, NPN, NO, or NC
3. Ultrasonic Proximity Switches
Ultrasonic proximity switches offer long sensing ranges and can detect objects regardless of their material, color, or transparency.
Key features of ultrasonic proximity switches:
– Sensing range: typically up to 8 m
– Target material: any solid or liquid object
– Immune to electromagnetic interference and ambient light
– Adjustable switching points and hysteresis
– Output types: analog (0-10 V, 4-20 mA) or digital (PNP, NPN, NO, NC)
4. Optical Proximity Switches
Optical proximity switches provide fast response times and high accuracy in object detection.
Key features of optical proximity switches:
– Sensing range: typically up to 20 m (depending on the type)
– Target material: any object that can reflect light
– Various light sources: LED, laser, or infrared
– Adjustable focus and sensitivity
– Output types: PNP, NPN, NO, NC, or analog
Proximity Switch Applications
Proximity switches find applications in a wide range of industries and processes. Some common applications include:
- Manufacturing and Assembly:
- Detecting the presence of parts on conveyor belts
- Monitoring machine tool positions
- Counting and sorting objects
-
Quality control and inspection
-
Material Handling:
- Detecting the presence of objects on cranes and hoists
- Monitoring the position of automated guided vehicles (AGVs)
- Level control in silos and tanks
-
Collision avoidance in automated storage and retrieval systems (ASRS)
-
Packaging and Labeling:
- Detecting the presence of bottles, cans, or boxes
- Monitoring the position of labels and caps
- Counting and sorting packages
-
Detecting jams or misalignments in packaging machinery
-
Automotive Industry:
- Detecting the presence of metal parts in welding and assembly processes
- Monitoring the position of robotic arms and grippers
- Detecting the presence of vehicles in parking systems
-
Monitoring the level of fluids in tanks and reservoirs
-
Food and Beverage:
- Detecting the presence of bottles, cans, or jars in filling and capping processes
- Monitoring the level of ingredients in tanks and silos
- Detecting the presence of foreign objects in food processing lines
- Counting and sorting products
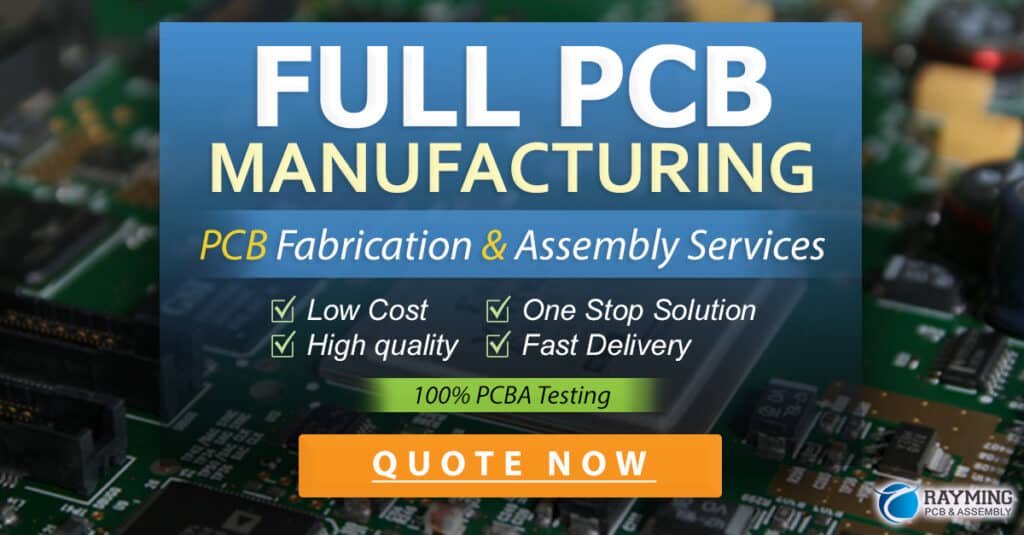
Selecting the Right Proximity Switch
When choosing a proximity switch for your application, consider the following factors:
-
Sensing Range: Determine the required sensing distance based on your application needs. Consider factors such as the size and position of the objects to be detected.
-
Target Material: Identify the material of the objects you want to detect. Inductive proximity switches are suitable for metallic objects, while capacitive switches can detect both metallic and non-metallic objects. Ultrasonic and optical switches can detect objects regardless of their material.
-
Environment: Consider the environmental conditions in which the proximity switch will operate. Factors such as temperature, humidity, dust, dirt, and vibrations can affect the switch’s performance. Choose a switch with appropriate IP ratings and certifications for your specific environment.
-
Output Type: Select the output type (PNP, NPN, NO, NC, analog) that is compatible with your control system or PLC. Ensure that the switch’s output current and voltage ratings match your application requirements.
-
Mounting and Installation: Consider the mounting options and installation requirements for the proximity switch. Some switches may require flush mounting, while others can be non-flush mounted. Ensure that the switch’s housing and connection type are suitable for your application.
-
Response Time and Switching Frequency: Evaluate the required response time and switching frequency for your application. Faster response times and higher switching frequencies may be necessary for high-speed processes or precise control.
-
Cost and Maintenance: Consider the initial cost of the proximity switch and any associated maintenance or replacement costs. Choose a switch that offers the best balance between performance, reliability, and cost-effectiveness for your application.
Proximity Switch Installation and Wiring
Proper installation and wiring of proximity switches are crucial for their reliable operation. Follow these general guidelines:
-
Mounting: Mount the proximity switch securely using the provided mounting holes or brackets. Ensure that the switching face is aligned with the target object and within the specified sensing range.
-
Wiring: Connect the proximity switch to your control system or PLC according to the manufacturer’s wiring diagram. Ensure that the power supply voltage and polarity are correct. Use shielded cables to minimize electromagnetic interference.
-
Adjustment: If the proximity switch has adjustable sensitivity or switching points, set them according to your application requirements. Follow the manufacturer’s instructions for calibration and adjustment procedures.
-
Maintenance: Regularly inspect the proximity switch for any signs of damage, dirt, or debris. Clean the sensing face periodically to ensure optimal performance. Replace the switch if it shows signs of wear or malfunction.
Proximity Switch Troubleshooting
If you encounter issues with your proximity switch, consider the following troubleshooting steps:
-
Check Power Supply: Verify that the proximity switch is receiving the correct power supply voltage and polarity. Use a multimeter to measure the voltage at the switch’s power terminals.
-
Check Wiring: Ensure that the wiring connections are secure and properly terminated. Check for any loose or damaged wires. Verify that the switch’s output is connected to the correct input on your control system or PLC.
-
Check Sensing Range: Verify that the target object is within the specified sensing range of the proximity switch. Adjust the object’s position or the switch’s sensitivity if necessary.
-
Check Target Material: Ensure that the target object’s material is compatible with the proximity switch type. Inductive switches require metallic targets, while capacitive switches can detect both metallic and non-metallic objects.
-
Check for Interference: Check for any sources of electromagnetic interference, such as power lines, motors, or other electronic devices, that may affect the proximity switch’s performance. Use shielded cables or relocate the switch if necessary.
-
Replace Switch: If the proximity switch continues to malfunction after troubleshooting, it may need to be replaced. Consult the manufacturer’s documentation for replacement procedures and warranty information.
FAQs
- What is the difference between inductive and capacitive proximity switches?
-
Inductive proximity switches detect metallic objects by generating an electromagnetic field, while capacitive proximity switches can detect both metallic and non-metallic objects by creating an electrostatic field.
-
Can proximity switches detect transparent objects?
-
Ultrasonic and optical proximity switches can detect transparent objects, while inductive and capacitive switches may have limitations in detecting transparent materials.
-
How do I choose the right sensing range for my application?
-
Consider the size and position of the objects you want to detect. Ensure that the sensing range is sufficient to reliably detect the objects while avoiding false triggers from nearby objects or surfaces.
-
Can proximity switches be used in explosive environments?
-
Yes, there are proximity switches specifically designed for use in explosive or hazardous environments. These switches have appropriate certifications, such as ATEX or IECEx, and are constructed to prevent sparks or heat generation that could ignite explosive atmospheres.
-
How often should I maintain my proximity switches?
- The maintenance frequency depends on the specific application and environment. As a general guideline, inspect and clean the proximity switches every 3-6 months, or more frequently if they are exposed to harsh conditions or heavy use. Consult the manufacturer’s recommendations for specific maintenance intervals and procedures.
Conclusion
Proximity switches are essential components in industrial automation, providing reliable and accurate object detection without physical contact. By understanding the different types of proximity switches, their working principles, and key selection criteria, you can choose the best switch for your specific application. Proper installation, wiring, and maintenance ensure optimal performance and longevity of your proximity switches. With the knowledge gained from this article, you are well-equipped to implement proximity switches in your automation projects effectively.
No responses yet