Introduction to Custom PCBs
Custom printed circuit boards (PCBs) are essential components in modern electronics. They provide a reliable and efficient way to connect electronic components and create complex circuits. Whether you are a hobbyist, a startup, or an established company, understanding the process of designing and manufacturing custom PCBs is crucial for achieving the best results.
In this comprehensive guide, we will walk you through everything you need to know about custom PCBs, from the basics of PCB design to advanced manufacturing techniques. By the end of this article, you will have a solid understanding of how to create high-quality custom PCBs that meet your specific needs.
What is a Custom PCB?
A custom PCB is a printed circuit board that is designed and manufactured according to specific requirements. Unlike off-the-shelf PCBs, which are mass-produced and have pre-determined layouts, custom PCBs are tailored to meet the unique needs of a particular project or application.
Custom PCBs offer several advantages over off-the-shelf boards, including:
- Optimized layout for specific components and circuits
- Improved performance and reliability
- Reduced size and weight
- Increased design flexibility
- Cost-effectiveness for large-scale production
The Custom PCB Design Process
Step 1: Schematic Design
The first step in creating a custom PCB is to design the schematic. A schematic is a visual representation of the electronic circuit, showing how the components are connected. It serves as a blueprint for the PCB layout and helps ensure that the circuit functions as intended.
When designing a schematic, consider the following factors:
- Component selection: Choose components that meet the electrical and mechanical requirements of your project.
- Circuit functionality: Ensure that the circuit performs the desired functions and meets the necessary specifications.
- Signal integrity: Minimize noise, crosstalk, and other signal integrity issues by properly routing and terminating signals.
Step 2: PCB Layout Design
Once the schematic is complete, the next step is to create the PCB layout. The layout determines the physical placement of components and the routing of traces on the board. A well-designed layout is crucial for ensuring proper functionality, manufacturability, and reliability.
When designing a PCB layout, keep the following best practices in mind:
- Component placement: Place components in a logical and organized manner, considering factors such as signal flow, thermal management, and mechanical constraints.
- Trace routing: Route traces efficiently to minimize signal length and avoid unnecessary crossovers. Use appropriate trace widths and spacing to ensure signal integrity and manufacturability.
- Grounding and power distribution: Implement a robust grounding strategy and distribute power evenly across the board to minimize noise and ensure stable operation.
- Design for manufacturing (DFM): Follow DFM guidelines to ensure that the PCB can be easily and reliably manufactured. This includes considerations such as minimum trace widths, clearances, and drill sizes.
Step 3: Design Review and Verification
Before proceeding to manufacturing, it is essential to review and verify the PCB design. This step helps catch any errors or potential issues early in the process, saving time and money in the long run.
Design review and verification typically involve the following tasks:
- Schematic review: Double-check the schematic for accuracy and completeness. Verify that all components are correctly specified and connected.
- Layout review: Examine the PCB layout for any design rule violations, such as insufficient clearances or trace widths. Ensure that the layout meets the requirements for manufacturing and assembly.
- Electrical rule check (ERC): Run an ERC to identify any electrical issues, such as short circuits or unconnected pins.
- Design rule check (DRC): Perform a DRC to verify that the layout complies with the specified design rules, such as minimum trace widths and clearances.
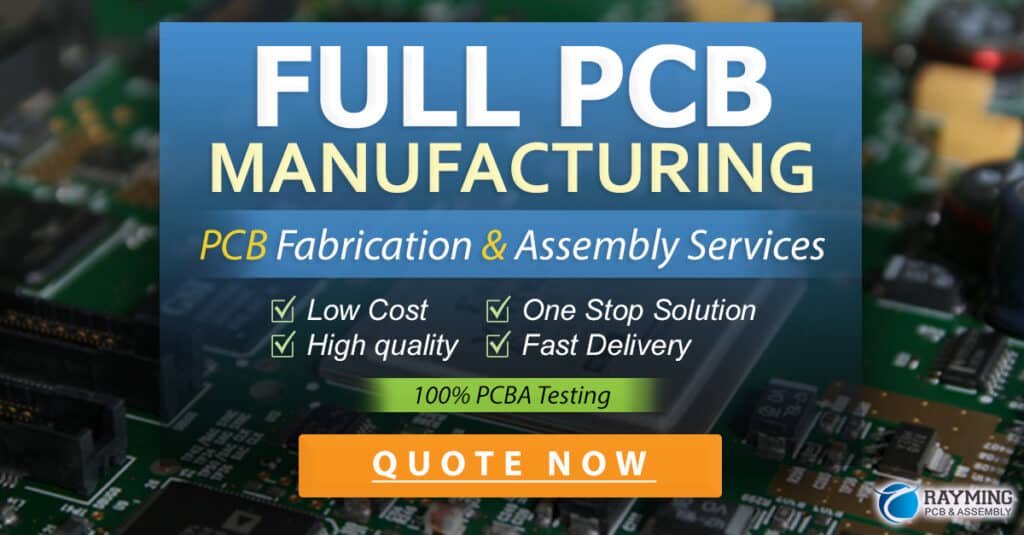
PCB Manufacturing Process
Step 1: Fabrication
Once the PCB design is finalized and verified, it is sent to a PCB fabrication house for manufacturing. The fabrication process involves several steps, including:
- Copper deposition: A thin layer of copper is deposited onto the substrate material, typically FR-4 or other high-quality laminate.
- Photolithography: The PCB layout is transferred onto the copper layer using a photoresist and UV light exposure.
- Etching: The unwanted copper is removed using a chemical etching process, leaving only the desired traces and pads.
- Drilling: Holes are drilled through the board for component leads and vias.
- Plating: The holes are plated with copper to create electrical connections between layers.
- Solder mask application: A protective solder mask is applied to the board, exposing only the areas where components will be soldered.
- Silkscreen printing: Text and symbols are printed onto the board for component identification and assembly instructions.
Step 2: Assembly
After fabrication, the PCB is ready for assembly. The assembly process involves placing and soldering components onto the board. There are two main methods of PCB assembly:
- Through-hole assembly: Components with long leads are inserted through holes in the board and soldered on the opposite side.
- Surface-mount assembly: Components with small, flat leads are placed directly onto pads on the board’s surface and soldered in place.
Automated assembly equipment, such as pick-and-place machines and reflow ovens, is often used to ensure precise and efficient assembly.
Step 3: Testing and Inspection
Once the PCB is assembled, it undergoes rigorous testing and inspection to ensure proper functionality and quality. Common testing methods include:
- In-circuit testing (ICT): Automated test equipment is used to verify the presence and correct placement of components, as well as the integrity of solder joints.
- Functional testing: The PCB is powered up and tested for proper operation, ensuring that it performs the intended functions.
- Visual inspection: The board is visually inspected for any defects, such as poor solder joints, missing components, or damaged traces.
Boards that pass the testing and inspection process are ready for use in the final product.
Advanced PCB Manufacturing Techniques
As technology advances and electronics become more complex, PCB manufacturing techniques continue to evolve. Some advanced techniques that are gaining popularity include:
High-Density Interconnect (HDI) PCBs
HDI PCBs feature smaller trace widths, tighter clearances, and more layers than traditional PCBs. This allows for higher component density and improved signal integrity, making HDI PCBs ideal for applications that require miniaturization and high performance.
Flexible and Rigid-Flex PCBs
Flexible PCBs are made from thin, flexible materials that allow the board to bend and conform to various shapes. Rigid-flex PCBs combine rigid and flexible sections, enabling 3D packaging and reducing the need for connectors. These types of PCBs are commonly used in wearable electronics, medical devices, and aerospace applications.
Embedded Components
Embedded components, such as resistors and capacitors, are placed inside the PCB substrate rather than on the surface. This technique saves space, reduces the number of solder joints, and improves reliability. Embedded components are particularly useful in high-frequency and high-power applications.
Choosing a PCB Manufacturer
Selecting the right PCB manufacturer is crucial for ensuring the success of your project. When evaluating potential manufacturers, consider the following factors:
- Experience and expertise: Look for a manufacturer with a proven track record in producing high-quality PCBs for applications similar to yours.
- Manufacturing capabilities: Ensure that the manufacturer has the necessary equipment and processes to meet your specific requirements, such as HDI, flexible, or rigid-flex PCBs.
- Quality control: Choose a manufacturer that adheres to strict quality control standards, such as IPC-A-600 and ISO 9001.
- Lead times and pricing: Consider the manufacturer’s lead times and pricing structure to ensure that they align with your project timeline and budget.
- Customer support: Select a manufacturer that offers responsive and knowledgeable customer support to help you navigate the PCB design and manufacturing process.
Frequently Asked Questions (FAQ)
1. What is the difference between a custom PCB and an off-the-shelf PCB?
Custom PCBs are designed and manufactured according to specific requirements, while off-the-shelf PCBs are mass-produced with pre-determined layouts. Custom PCBs offer optimized layouts, improved performance, and increased design flexibility, but they may be more expensive for low-volume production.
2. How long does it take to manufacture a custom PCB?
The lead time for custom PCB manufacturing varies depending on the complexity of the design, the chosen manufacturer, and the current market demand. Typical lead times range from a few days to several weeks. Communicating your timeline requirements with the manufacturer early in the process can help ensure that your project stays on schedule.
3. What are the most common materials used for PCB substrates?
FR-4 is the most widely used PCB substrate material due to its excellent electrical, mechanical, and thermal properties. Other common materials include high-frequency laminates (e.g., Rogers), flexible substrates (e.g., polyimide), and metal-core substrates for high-power applications.
4. How can I ensure the manufacturability of my custom PCB design?
To ensure the manufacturability of your custom PCB design, follow these best practices:
- Adhere to the manufacturer’s design guidelines, including minimum trace widths, clearances, and drill sizes.
- Use standard component sizes and footprints whenever possible.
- Avoid sharp angles and abrupt changes in trace direction.
- Provide clear and accurate documentation, including Gerber files, drill files, and assembly drawings.
5. What are the benefits of using HDI PCBs?
HDI PCBs offer several benefits, including:
- Higher component density, enabling smaller and more compact designs.
- Improved signal integrity due to shorter trace lengths and reduced crosstalk.
- Enhanced thermal management through the use of microvias and embedded components.
- Increased reliability due to fewer solder joints and interconnects.
HDI PCBs are particularly well-suited for applications that require high performance, miniaturization, and reliability, such as smartphones, wearable devices, and aerospace systems.
Conclusion
Creating a custom PCB can be a complex and challenging process, but with the right knowledge and approach, you can achieve excellent results. By understanding the PCB design process, manufacturing techniques, and best practices, you can create high-quality custom PCBs that meet your specific needs and exceed your expectations.
Remember to choose a reputable PCB manufacturer that has the experience, capabilities, and customer support to help you bring your project to life. By following the guidelines and advice in this ultimate guide, you will be well on your way to creating custom PCBs that are reliable, efficient, and tailored to your unique requirements.
Step | Description |
---|---|
1 | Schematic Design |
2 | PCB Layout Design |
3 | Design Review and Verification |
4 | Fabrication |
5 | Assembly |
6 | Testing and Inspection |
Table 1: Custom PCB Design and Manufacturing Process
Material | Description |
---|---|
FR-4 | Most common PCB substrate, offering excellent electrical, mechanical, and thermal properties |
High-Frequency Laminates | Specialized substrates for high-frequency applications, such as Rogers materials |
Flexible Substrates | Thin, flexible materials, such as polyimide, for applications requiring bending or conforming to shapes |
Metal-Core Substrates | Substrates with a metal core for improved thermal management in high-power applications |
Table 2: Common PCB Substrate Materials
By leveraging the information in this guide and partnering with a trusted PCB manufacturer, you can unlock the full potential of custom PCBs and take your electronics projects to new heights.
No responses yet