Introduction to Start-stop Circuits
Start-stop circuits are essential components in various electrical and electronic systems, providing a means to control the operation of devices by initiating and terminating their functions. These circuits play a crucial role in ensuring the proper sequencing and timing of events, as well as providing safety mechanisms to prevent accidents or damage to equipment. In this comprehensive article, we will delve into the world of start-stop circuits, exploring their principles, types, applications, and best practices for design and troubleshooting.
What are Start-stop Circuits?
Start-stop circuits are electrical control circuits that enable the user to initiate (start) and terminate (stop) the operation of a device or system. These circuits typically consist of a combination of switches, relays, contactors, and other components that work together to control the flow of electricity to the load. The main purpose of a start-stop circuit is to provide a safe and convenient way to control the operation of a device, while also protecting the equipment and the operator from potential hazards.
Basic Principles of Start-stop Circuits
The basic principle behind start-stop circuits is the use of momentary switches to control the state of a latching device, such as a relay or contactor. When the start button is pressed, it energizes the coil of the latching device, causing its contacts to close and allowing current to flow to the load. The latching device remains energized even after the start button is released, due to its self-holding feature. To stop the operation, the stop button is pressed, which interrupts the current to the coil, causing the contacts to open and disconnecting the load from the power source.
Types of Start-stop Circuits
There are several types of start-stop circuits, each designed to meet specific requirements and applications. The following are some of the most common types:
1. Two-wire Control Circuit
The two-wire control circuit is the simplest form of start-stop circuit, consisting of a start button, a stop button, and a load. In this configuration, the start and stop buttons are connected in series with the load, and the circuit is powered by a single power source. When the start button is pressed, current flows through the load, and when the stop button is pressed, the current is interrupted, stopping the operation of the load.
2. Three-wire Control Circuit
The three-wire control circuit is a more advanced version of the start-stop circuit, incorporating a latching device, such as a relay or contactor, to maintain the operation of the load even after the start button is released. This circuit consists of a start button, a stop button, a latching device, and a load. The start button is connected in series with the coil of the latching device, while the stop button is connected in series with a normally closed contact of the latching device. When the start button is pressed, the coil is energized, closing the contacts and allowing current to flow to the load. The latching device remains energized through its own normally open contact, which is connected in parallel with the start button. To stop the operation, the stop button is pressed, interrupting the current to the coil and opening the contacts.
3. Jogging Circuit
A jogging circuit is a variation of the start-stop circuit that allows for brief, intermittent operation of the load. This circuit is commonly used in applications where precise control over the duration of the operation is required, such as in positioning systems or machine tools. The jogging circuit consists of a jog button, a stop button, a latching device, and a load. The jog button is connected in series with the coil of the latching device, while the stop button is connected in series with a normally closed contact of the latching device. When the jog button is pressed and held, the coil is energized, closing the contacts and allowing current to flow to the load. As soon as the jog button is released, the coil is de-energized, opening the contacts and stopping the operation.
4. Reversing Circuit
A reversing circuit is a start-stop circuit that allows for the bidirectional control of a load, such as a motor. This circuit is used in applications where the direction of rotation needs to be changed periodically, such as in conveyor systems or machine tools. The reversing circuit consists of two sets of start and stop buttons, two latching devices (forward and reverse contactors), and a load. Each set of start and stop buttons controls one of the contactors, which are electrically interlocked to prevent simultaneous activation. When the forward start button is pressed, the forward contactor is energized, closing its contacts and allowing current to flow to the load in one direction. When the reverse start button is pressed, the reverse contactor is energized, closing its contacts and allowing current to flow to the load in the opposite direction. The stop buttons are used to de-energize the respective contactors and stop the operation.
Applications of Start-stop Circuits
Start-stop circuits find applications in a wide range of industries and systems, including:
1. Industrial Machinery
Start-stop circuits are extensively used in industrial machinery to control the operation of motors, pumps, compressors, and other equipment. These circuits provide a safe and convenient way to start and stop the machinery, while also protecting the equipment and the operator from potential hazards.
2. HVAC Systems
In heating, ventilation, and air conditioning (HVAC) systems, start-stop circuits are used to control the operation of fans, blowers, and compressors. These circuits ensure that the equipment operates according to the desired temperature and humidity settings, while also providing safety features to prevent damage to the system.
3. Lighting Systems
Start-stop circuits are used in lighting systems to control the operation of lamps, fixtures, and other illumination devices. These circuits allow for the convenient switching of lights on and off, as well as the implementation of energy-saving features, such as automatic shutoff or dimming.
4. Automotive Systems
In automotive systems, start-stop circuits are used to control various functions, such as the ignition system, starter motor, and accessories. These circuits ensure that the vehicle starts and stops smoothly and safely, while also protecting the electrical components from damage.
5. Robotics and Automation
Start-stop circuits play a crucial role in robotics and automation systems, where precise control over the operation of actuators, sensors, and other components is required. These circuits enable the smooth and efficient functioning of the system, while also providing safety features to prevent accidents or damage to the equipment.
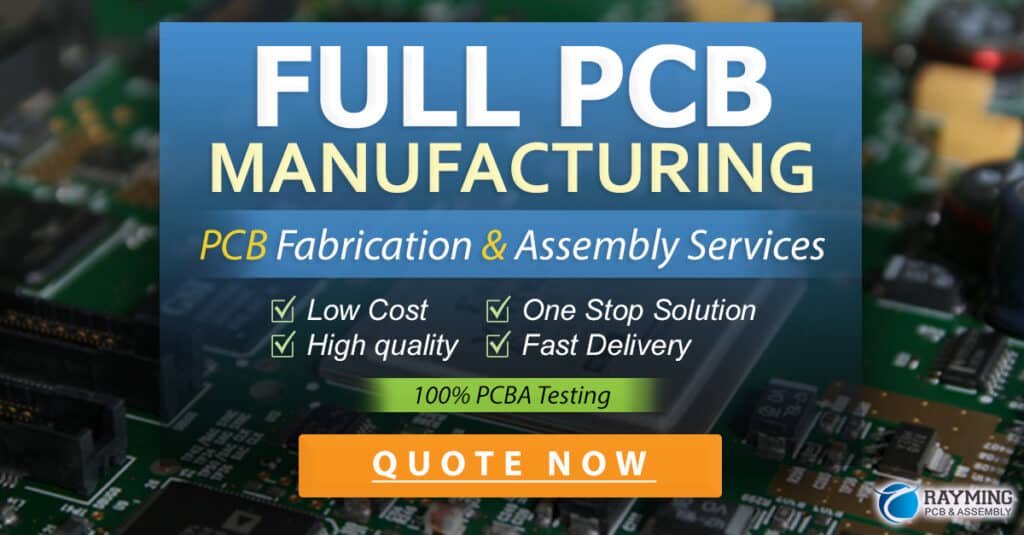
Designing Start-stop Circuits
When designing start-stop circuits, several key factors need to be considered to ensure the proper functioning, safety, and reliability of the system. The following are some of the best practices for designing start-stop circuits:
1. Select the Appropriate Components
The selection of components is a critical aspect of designing start-stop circuits. The components, such as switches, relays, contactors, and overload protection devices, should be chosen based on the specific requirements of the application, such as the voltage and current ratings, environmental conditions, and expected service life. It is essential to use high-quality, reliable components to ensure the proper functioning and longevity of the system.
2. Follow Safety Standards and Regulations
Start-stop circuits must be designed in compliance with the relevant safety standards and regulations, such as the National Electrical Code (NEC), International Electrotechnical Commission (IEC) standards, and Occupational Safety and Health Administration (OSHA) regulations. These standards provide guidelines for the proper sizing of conductors, the selection of overcurrent protection devices, and the implementation of safety features, such as emergency stop buttons and interlocks.
3. Implement Fail-safe Mechanisms
Fail-safe mechanisms are essential in start-stop circuits to ensure that the system remains in a safe state in the event of a failure or malfunction. These mechanisms can include redundant components, such as dual contactors or relays, as well as monitoring devices, such as current sensors or PLC inputs, that can detect and respond to abnormal conditions. By implementing fail-safe mechanisms, the risk of accidents or damage to equipment can be significantly reduced.
4. Use Schematic Diagrams and Wiring Layouts
Schematic diagrams and wiring layouts are essential tools for designing and documenting start-stop circuits. These diagrams provide a clear and concise representation of the circuit, including the interconnections between components, the power supply, and the load. They also serve as a reference for troubleshooting and maintenance, enabling technicians to quickly identify and resolve issues.
5. Test and Validate the Circuit
Before commissioning a start-stop circuit, it is essential to test and validate its functionality and safety features. This process involves conducting a series of tests, such as continuity checks, insulation resistance tests, and functional tests, to ensure that the circuit operates as intended and meets the required safety standards. Any issues or discrepancies should be addressed and rectified before the circuit is put into service.
Troubleshooting Start-stop Circuits
Despite the best efforts in design and installation, start-stop circuits may experience issues or malfunctions during their service life. Troubleshooting these circuits requires a systematic approach and a thorough understanding of their operating principles. The following are some of the common issues and troubleshooting techniques for start-stop circuits:
1. Component Failure
One of the most common issues in start-stop circuits is the failure of components, such as switches, relays, or contactors. These failures can be caused by various factors, such as wear and tear, overheating, or electrical surges. To troubleshoot component failures, technicians should visually inspect the components for signs of damage or deterioration, test their continuity and resistance, and replace them if necessary.
2. Wiring Issues
Wiring issues, such as loose connections, damaged insulation, or incorrect terminations, can cause start-stop circuits to malfunction or fail. These issues can be difficult to detect, as they may not be visible to the naked eye. To troubleshoot wiring issues, technicians should perform continuity and resistance tests, visually inspect the wiring for signs of damage or corrosion, and use wiring diagrams to verify the correct interconnections between components.
3. Power Supply Problems
Start-stop circuits rely on a stable and reliable power supply to operate properly. Issues with the power supply, such as voltage fluctuations, brownouts, or power outages, can cause the circuit to malfunction or fail. To troubleshoot power supply problems, technicians should use a multimeter to measure the voltage at various points in the circuit, verify the integrity of the power source, and ensure that the circuit is properly grounded.
4. Logic Errors
In more complex start-stop circuits, such as those incorporating programmable logic controllers (PLCs) or other control devices, logic errors can cause the system to behave unexpectedly or fail to operate altogether. These errors can be caused by incorrect programming, faulty sensors, or communication issues. To troubleshoot logic errors, technicians should review the control logic, test the inputs and outputs of the control devices, and use diagnostic tools, such as PLC software or protocol analyzers, to identify and resolve the issues.
5. Safety Interlocks
Safety interlocks are critical components in start-stop circuits, preventing the system from operating in an unsafe condition. Issues with safety interlocks, such as stuck or misaligned contacts, can compromise the safety of the system and the operator. To troubleshoot safety interlock issues, technicians should test the continuity and resistance of the interlock contacts, verify their proper alignment and operation, and replace them if necessary.
Frequently Asked Questions (FAQ)
1. What is the difference between a two-wire and a three-wire control circuit?
A two-wire control circuit consists of a start button, a stop button, and a load, with the buttons connected in series with the load. A three-wire control circuit incorporates a latching device, such as a relay or contactor, to maintain the operation of the load even after the start button is released.
2. What is the purpose of a jogging circuit?
A jogging circuit allows for brief, intermittent operation of the load, providing precise control over the duration of the operation. This circuit is commonly used in applications such as positioning systems or machine tools.
3. What safety standards and regulations should be followed when designing start-stop circuits?
Start-stop circuits must be designed in compliance with relevant safety standards and regulations, such as the National Electrical Code (NEC), International Electrotechnical Commission (IEC) standards, and Occupational Safety and Health Administration (OSHA) regulations.
4. What are some common issues in start-stop circuits?
Common issues in start-stop circuits include component failure, wiring issues, power supply problems, logic errors, and safety interlock malfunctions.
5. How can I troubleshoot a start-stop circuit?
To troubleshoot a start-stop circuit, technicians should use a systematic approach, including visual inspections, continuity and resistance tests, wiring diagram verification, power supply measurements, and diagnostic tools for control devices. It is essential to identify and resolve the root cause of the issue to ensure the proper and safe operation of the system.
Conclusion
Start-stop circuits are essential components in various electrical and electronic systems, providing a means to control the operation of devices safely and efficiently. By understanding the principles, types, applications, and best practices for designing and troubleshooting start-stop circuits, engineers and technicians can ensure the proper functioning and reliability of these systems. As technology continues to evolve, the importance of start-stop circuits in modern industries will only continue to grow, making it crucial for professionals to stay informed and adapt to the latest advancements in this field.
Component | Function |
---|---|
Start Button | Initiates the operation of the load |
Stop Button | Terminates the operation of the load |
Relay/Contactor | Latching device that maintains the operation of the load |
Overload Relay | Protects the motor from excessive current draw |
Fuse/Circuit Breaker | Provides overcurrent protection for the circuit |
Wiring | Connects the components and carries the electrical current |
Power Supply | Provides the necessary voltage and current for the operation of the circuit |
No responses yet