The Importance of Quality Control in Business
Quality control is a critical component of any successful business strategy. It helps companies maintain a high level of customer satisfaction, reduce costs associated with defects and returns, and protect their brand reputation. By implementing a robust incoming quality control process, companies can:
- Ensure consistency in product quality
- Identify and address quality issues early in the supply chain
- Minimize the risk of product recalls and liability claims
- Improve efficiency and productivity by reducing rework and waste
- Strengthen relationships with suppliers through clear quality expectations and feedback
The Cost of Poor Quality
Failing to implement an effective quality control process can have significant financial consequences for a company. According to a study by the American Society for Quality (ASQ), the cost of poor quality can range from 15% to 40% of a company’s total revenue. These costs can include:
Cost Category | Examples |
---|---|
Internal Failure Costs | Rework, scrap, downtime, inspections |
External Failure Costs | Warranty claims, returns, lost sales, damage to brand reputation |
Prevention Costs | Quality planning, supplier evaluations, training, equipment maintenance |
Appraisal Costs | Incoming inspections, testing, audits, calibration |
By investing in an incoming quality control process, companies can reduce the overall cost of poor quality and improve their bottom line.
Key Elements of an Incoming Quality Control Process
An effective incoming quality control process should include several key elements:
1. Supplier Qualification and Management
Before accepting materials or components from a supplier, companies should conduct a thorough evaluation of the supplier’s quality management system, production capabilities, and track record. This process may include:
- Reviewing quality certifications (e.g., ISO 9001)
- Conducting on-site audits
- Requesting product samples for testing
- Establishing quality agreements and specifications
Once a supplier is qualified, ongoing management and communication are essential to maintain quality standards and address any issues that may arise.
2. Inspection Planning and Procedures
Companies should develop clear inspection plans and procedures for incoming materials and components. These plans should specify:
- Inspection frequency (e.g., every lot, random sampling)
- Inspection methods (e.g., visual, dimensional, functional testing)
- Acceptance criteria based on product specifications and quality standards
- Roles and responsibilities of quality control personnel
Inspection procedures should be documented, and personnel should be trained to ensure consistent execution.
3. Measuring and Testing Equipment
Accurate measuring and testing equipment is essential for effective incoming quality control. Companies should:
- Identify the necessary equipment for each type of inspection
- Ensure equipment is properly calibrated and maintained
- Provide training for personnel on equipment use and interpretation of results
4. Non-Conformance and Corrective Action
When incoming materials or components fail to meet quality standards, companies should have a clear process for addressing non-conformances. This process may include:
- Quarantining non-conforming items to prevent unintended use
- Notifying suppliers and requesting corrective action
- Conducting root cause analysis to prevent recurrence
- Updating inspection plans and procedures as needed
5. Documentation and Record-Keeping
Thorough documentation and record-keeping are critical for an effective incoming quality control process. Companies should maintain records of:
- Supplier evaluations and qualifications
- Inspection plans and procedures
- Inspection and testing results
- Non-conformances and corrective actions
- Material certifications and test reports
These records provide evidence of the company’s quality control efforts and can be used for continuous improvement, supplier management, and regulatory compliance.
Implementing an Incoming Quality Control Process
Implementing an incoming quality control process requires careful planning and execution. Companies should follow these steps:
- Identify critical materials and components that require incoming inspection
- Develop inspection plans and procedures based on product specifications and quality standards
- Acquire necessary measuring and testing equipment and ensure proper calibration and maintenance
- Train quality control personnel on inspection procedures and equipment use
- Establish a system for documenting and tracking inspection results, non-conformances, and corrective actions
- Communicate quality expectations and requirements to suppliers
- Monitor supplier performance and conduct regular evaluations and audits
- Continuously review and improve the incoming quality control process based on data and feedback
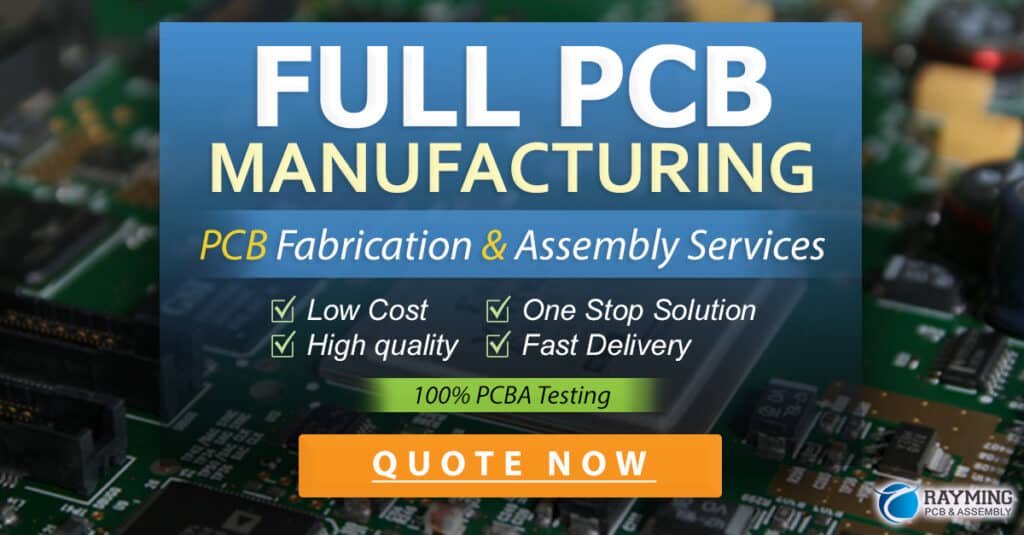
The Role of Technology in Incoming Quality Control
Advances in technology have created new opportunities for companies to streamline and enhance their incoming quality control processes. Some examples include:
1. Automated Inspection Systems
Automated inspection systems use sensors, cameras, and software algorithms to detect defects and measure dimensions more quickly and accurately than manual methods. These systems can be integrated into production lines or used for standalone inspections.
2. Barcode and RFID Tracking
Barcode and RFID (Radio-Frequency Identification) technologies can be used to track materials and components throughout the supply chain. This tracking enables companies to quickly identify and isolate non-conforming items and trace them back to their source.
3. Statistical Process Control (SPC) Software
SPC software analyzes inspection and testing data to identify trends, patterns, and potential quality issues. This analysis can help companies make data-driven decisions about supplier management, process improvements, and quality control strategies.
4. Supplier Portals and Collaboration Tools
Online supplier portals and collaboration tools can facilitate communication and data sharing between companies and their suppliers. These tools can be used to share quality specifications, inspection results, and corrective action requests, enabling faster issue resolution and continuous improvement.
Frequently Asked Questions (FAQ)
1. How often should incoming materials be inspected?
The frequency of incoming inspections depends on various factors, such as the criticality of the material, the supplier’s performance history, and the company’s risk tolerance. Some companies inspect every lot, while others use sampling plans based on statistical methods. The key is to balance the cost and time of inspections with the potential risk and impact of quality issues.
2. What are some common inspection methods for incoming materials?
Common inspection methods for incoming materials include:
- Visual inspection for defects, damage, or contamination
- Dimensional measurements using calipers, micrometers, or coordinate measuring machines (CMMs)
- Functional testing to verify performance or electrical properties
- Chemical analysis to verify composition or purity
- Non-destructive testing (NDT) methods such as X-ray, ultrasound, or magnetic particle inspection
The specific methods used will depend on the type of material and the quality characteristics being evaluated.
3. How can a company determine acceptance criteria for incoming materials?
Acceptance criteria for incoming materials should be based on the product specifications and quality standards required for the end product. These criteria may be derived from:
- Customer requirements and expectations
- Industry standards and regulations
- Design specifications and tolerances
- Historical performance data and process capabilities
Acceptance criteria should be clearly defined, measurable, and communicated to suppliers to ensure a consistent understanding of quality expectations.
4. What should a company do if a supplier consistently fails to meet quality standards?
If a supplier consistently fails to meet quality standards, a company should take a proactive approach to address the issue. This may include:
- Communicating the quality issues and expectations to the supplier
- Requesting a corrective action plan from the supplier to address the root causes of the issues
- Providing technical support or resources to help the supplier improve their processes
- Conducting more frequent audits or inspections to monitor progress
- Considering alternative suppliers if the issues persist and cannot be resolved
The goal is to work collaboratively with suppliers to achieve and maintain the desired level of quality, but a company must also be prepared to take decisive action if a supplier is unable or unwilling to meet quality standards.
5. How can a company ensure the effectiveness of its incoming quality control process?
To ensure the effectiveness of its incoming quality control process, a company should:
- Regularly review and analyze inspection and testing data to identify trends, patterns, and improvement opportunities
- Conduct periodic audits of the quality control process to verify compliance with procedures and identify potential gaps or weaknesses
- Seek feedback from internal customers (e.g., production, assembly) on the quality of incoming materials and the effectiveness of the quality control process
- Benchmark quality control practices against industry best practices and standards
- Continuously monitor and update the process based on changes in products, suppliers, regulations, or customer requirements
By taking a proactive and data-driven approach to quality control, companies can continuously improve the effectiveness of their incoming quality control process and deliver high-quality products and services to their customers.
Conclusion
In today’s competitive business environment, implementing an effective incoming quality control process is essential for companies to ensure product quality, customer satisfaction, and long-term success. By establishing clear quality standards, inspection procedures, and supplier management practices, companies can minimize the risk of quality issues and their associated costs.
Investing in an incoming quality control process is not just a matter of compliance or risk management; it is a strategic decision that can drive continuous improvement, innovation, and growth. By leveraging technology, data analytics, and collaboration with suppliers, companies can create a culture of quality that permeates throughout the organization and sets them apart from their competitors.
Ultimately, the success of an incoming quality control process depends on the commitment and engagement of everyone involved, from top management to front-line inspectors. By fostering a shared sense of responsibility and ownership for quality, companies can unlock the full potential of their people, processes, and products, and build a foundation for long-term success in the marketplace.
No responses yet