Why Use High-TG PCBs?
There are several reasons why High-TG PCBs are preferred in certain applications:
-
Increased Thermal Stability: High-TG PCBs can withstand higher operating temperatures without deforming or losing their mechanical properties. This makes them suitable for applications that generate significant heat, such as power electronics, automotive systems, and aerospace equipment.
-
Improved Reliability: By resisting thermal stress and maintaining their shape, High-TG PCBs offer enhanced reliability and longevity. They are less likely to experience issues like warping, delamination, or conductor breakdown due to heat exposure.
-
Compatibility with Lead-Free Soldering: The transition to lead-free soldering processes has led to higher soldering temperatures. High-TG PCBs can withstand these elevated temperatures during the soldering process, reducing the risk of defects and ensuring a reliable solder joint.
-
Harsh Environment Operation: In industries like automotive, aerospace, and oil and gas, electronic systems may be subjected to extreme temperatures, vibrations, and other harsh conditions. High-TG PCBs provide the necessary robustness to operate reliably in these challenging environments.
Materials Used in High-TG PCBs
High-TG PCBs are fabricated using specific materials that exhibit higher glass transition temperatures. Some commonly used materials include:
-
FR-4 High Tg: FR-4 is a popular PCB substrate material, and its high-TG variant offers a glass transition temperature of around 170°C to 180°C. It is widely used in applications that require increased thermal stability.
-
Polyimide: Polyimide-based PCBs have a glass transition temperature ranging from 250°C to 400°C, making them suitable for extremely high-temperature applications. They offer excellent thermal and chemical resistance but are more expensive than FR-4.
-
Bismaleimide Triazine (BT): BT is another high-performance material used in High-TG PCBs. It has a glass transition temperature of around 210°C to 230°C and offers good electrical properties and dimensional stability.
-
Cyanate Ester: Cyanate ester-based PCBs have a glass transition temperature of approximately 250°C. They provide excellent electrical insulation, low dielectric loss, and high resistance to moisture and chemicals.
Material | Glass Transition Temperature (Tg) |
---|---|
FR-4 High Tg | 170°C – 180°C |
Polyimide | 250°C – 400°C |
Bismaleimide Triazine (BT) | 210°C – 230°C |
Cyanate Ester | 250°C |
Design Considerations for High-TG PCBs
When designing High-TG PCBs, there are several factors to consider:
Thermal Management
Proper thermal management is crucial in High-TG PCB design. The following techniques can help dissipate heat effectively:
- Using wider traces and larger copper pours to improve heat dissipation.
- Incorporating thermal vias to transfer heat from the components to the opposite side of the PCB.
- Utilizing heat sinks and thermal interface materials to enhance heat transfer.
- Providing adequate spacing between components to prevent heat buildup.
Material Selection
Choosing the appropriate High-TG material depends on the specific application requirements. Factors to consider include:
- The maximum operating temperature of the system.
- The desired electrical properties, such as dielectric constant and loss tangent.
- The mechanical requirements, such as flexibility or stiffness.
- The cost constraints of the project.
Layer Stack-up
The layer stack-up of a High-TG PCB should be optimized for thermal performance and signal integrity. Some guidelines include:
- Using thicker copper layers to improve heat dissipation and current carrying capacity.
- Minimizing the number of layers to reduce thermal resistance.
- Placing power and ground planes close to the outer layers to facilitate heat transfer.
- Using dedicated thermal layers or heatspreading layers to distribute heat evenly.
Manufacturing Process
High-TG PCBs may require specialized manufacturing processes to ensure their performance and reliability. Some considerations include:
- Selecting a PCB fabricator with experience in manufacturing High-TG boards.
- Specifying the appropriate solder mask and silkscreen materials that can withstand high temperatures.
- Performing thorough testing and inspection to verify the quality and reliability of the manufactured PCBs.
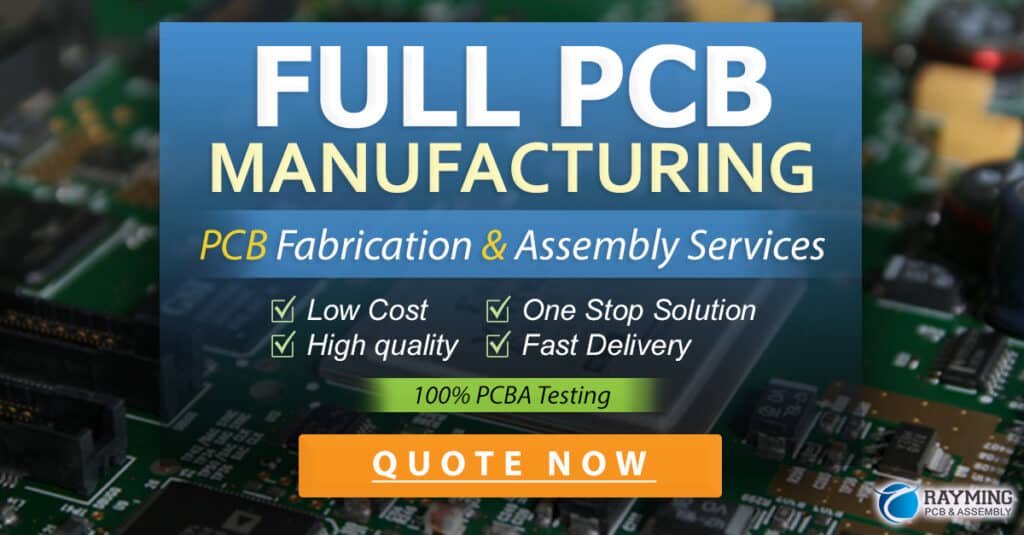
Applications of High-TG PCBs
High-TG PCBs find applications in various industries where high-temperature operation and reliability are critical. Some common applications include:
-
Automotive Electronics: High-TG PCBs are used in automotive systems such as engine control units, transmission control modules, and brake systems, where they are exposed to high temperatures and vibrations.
-
Power Electronics: Power converters, inverters, and motor drives generate significant heat during operation. High-TG PCBs provide the necessary thermal stability to ensure reliable performance.
-
Aerospace and Defense: Avionics systems, radar equipment, and satellite electronics require PCBs that can withstand extreme temperature ranges and harsh environmental conditions. High-TG PCBs meet these demanding requirements.
-
Industrial Automation: Industrial control systems, sensors, and actuators often operate in high-temperature environments. High-TG PCBs provide the robustness needed for reliable operation in these settings.
-
Oil and Gas Industry: Downhole drilling equipment and subsea electronics are subjected to high temperatures and pressures. High-TG PCBs are used to ensure the reliability of these systems in challenging environments.
Frequently Asked Questions (FAQ)
-
What is the difference between standard PCBs and High-TG PCBs?
Standard PCBs are typically made from FR-4 material with a glass transition temperature of around 130°C to 140°C. High-TG PCBs, on the other hand, use materials with higher glass transition temperatures, such as FR-4 High Tg, polyimide, or BT, which can withstand temperatures above 170°C. -
Can High-TG PCBs be used for all applications?
While High-TG PCBs offer superior thermal stability and reliability, they may not be necessary for all applications. If the operating temperature of the system is within the range of standard PCBs, using High-TG PCBs may add unnecessary cost and complexity. It is important to assess the specific requirements of the application before deciding on the type of PCB to use. -
Are High-TG PCBs more expensive than standard PCBs?
Yes, High-TG PCBs are generally more expensive than standard PCBs due to the specialized materials and manufacturing processes involved. The cost difference can vary depending on the specific material chosen and the complexity of the design. However, the added cost is often justified in applications where high-temperature performance and reliability are critical. -
Can High-TG PCBs be manufactured using the same processes as standard PCBs?
While the basic manufacturing processes for High-TG PCBs are similar to those of standard PCBs, there are some additional considerations. The choice of solder mask, silkscreen, and other materials should be compatible with high temperatures. Additionally, the PCB fabricator should have experience in handling and processing High-TG materials to ensure the quality and reliability of the final product. -
How can I determine if my application requires a High-TG PCB?
To determine if your application requires a High-TG PCB, consider the following factors: - The maximum operating temperature of the system.
- The presence of heat-generating components or exposure to high-temperature environments.
- The expected lifespan and reliability requirements of the product.
- The cost constraints and trade-offs between performance and affordability.
If your application involves high temperatures, harsh environments, or demands exceptional reliability, a High-TG PCB may be the suitable choice.
Conclusion
High-TG PCBs are a critical component in applications that require reliable operation in high-temperature environments. By utilizing materials with higher glass transition temperatures, these PCBs offer increased thermal stability, improved reliability, and compatibility with lead-free soldering processes. When designing High-TG PCBs, careful consideration should be given to thermal management, material selection, layer stack-up, and manufacturing processes to ensure optimal performance and longevity.
As technology advances and the demand for reliable electronics in challenging environments grows, the importance of High-TG PCBs will continue to increase. From automotive and aerospace to industrial automation and oil and gas, High-TG PCBs play a vital role in ensuring the robustness and dependability of electronic systems in various industries.
By understanding the characteristics, benefits, and design considerations of High-TG PCBs, engineers and designers can make informed decisions when selecting the appropriate PCB material for their specific applications. With the right design approach and manufacturing processes, High-TG PCBs can provide the necessary performance and reliability to meet the evolving needs of modern electronic systems.
No responses yet