What is MCPCB?
MCPCB stands for Metal Core Printed Circuit Board. It is a special type of PCB that uses a metal core as the base material instead of the traditional FR-4 material. The metal core is usually made of aluminum, which provides excellent thermal conductivity and helps dissipate heat more efficiently than standard PCBs.
Composition of MCPCB
A typical MCPCB consists of three layers:
-
Dielectric Layer: This layer is made of a thin, electrically insulating material that covers the metal core. It helps to protect the circuitry from short-circuits and provides electrical isolation.
-
Circuit Layer: The circuit layer is where the copper traces and pads are located. This layer is responsible for carrying electrical signals and connecting components.
-
Metal Core: The metal core is the base of the MCPCB and is usually made of aluminum. It acts as a heat sink, drawing heat away from the components and dissipating it into the environment.
Layer | Material | Thickness | Function |
---|---|---|---|
Dielectric Layer | Insulating Material | 0.1 – 0.2 mm | Electrical Isolation |
Circuit Layer | Copper | 0.035 – 0.07 mm | Electrical Connectivity |
Metal Core | Aluminum | 1.0 – 3.0 mm | Heat Dissipation |
Advantages of MCPCB in LED Applications
MCPCBs have become increasingly popular in the LED industry due to their unique properties and advantages over traditional PCBs. Some of the key benefits of using MCPCBs in LED applications include:
1. Improved Heat Dissipation
LEDs generate a significant amount of heat during operation, which can negatively impact their performance and lifespan. MCPCBs excel at dissipating this heat thanks to their metal core, which acts as a built-in heat sink. By efficiently transferring heat away from the LEDs, MCPCBs help to maintain optimal operating temperatures, leading to improved LED performance and longevity.
2. Enhanced Thermal Management
In addition to their heat dissipation capabilities, MCPCBs also offer better thermal management compared to traditional PCBs. The metal core helps to evenly distribute heat across the entire board, preventing hot spots from forming around the LEDs. This uniform heat distribution further contributes to the overall thermal stability of the LED system.
3. Increased Power Density
MCPCBs allow for higher power densities in LED applications. The improved thermal management capabilities of MCPCBs enable LEDs to be driven at higher currents without compromising their performance or reliability. This means that more LEDs can be packed into a smaller space, resulting in brighter and more compact LED fixtures.
4. Better Reliability and Longevity
By maintaining optimal operating temperatures and preventing thermal stress on the LEDs, MCPCBs significantly enhance the reliability and longevity of LED systems. The metal core helps to minimize thermal expansion and contraction, which can cause mechanical stress on the components and solder joints. This reduced stress translates to fewer failures and a longer lifespan for the LED products.
5. Cost-Effectiveness
While MCPCBs may have a higher initial cost compared to traditional PCBs, they offer long-term cost savings in LED applications. The improved thermal management and reliability of MCPCBs lead to reduced maintenance and replacement costs over the lifetime of the LED products. Additionally, the ability to drive LEDs at higher power densities can result in fewer LED components being required, further reducing overall system costs.
Applications of MCPCB in the LED Industry
MCPCBs have found widespread use in various LED applications due to their superior thermal management and reliability. Some of the common applications include:
1. LED Lighting
MCPCBs are extensively used in LED lighting fixtures, such as bulbs, tubes, panels, and downlights. They provide the necessary heat dissipation to keep the LEDs running at optimal temperatures, ensuring consistent light output and prolonging the lifespan of the lighting products.
2. Automotive LED Lighting
In the automotive industry, MCPCBs are used in LED headlights, taillights, and interior lighting. The harsh operating conditions in vehicles, such as high temperatures and vibrations, require robust and reliable LED solutions. MCPCBs offer the thermal management and mechanical stability needed to withstand these challenging environments.
3. LED Displays
Large LED displays, such as those used in outdoor advertising or stadium screens, rely on MCPCBs to manage the heat generated by the high-density LED arrays. The metal core helps to dissipate heat efficiently, preventing thermal damage to the LEDs and ensuring consistent image quality across the display.
4. LED Backlighting
MCPCBs are used in LED backlighting applications for LCD displays, such as those found in televisions, monitors, and mobile devices. The improved thermal management provided by MCPCBs allows for thinner and more compact backlight designs while maintaining optimal LED performance.
5. UV LED Curing Systems
Ultraviolet (UV) LED curing systems, used in various industrial applications such as printing and coating, also benefit from MCPCBs. The high-power UV LEDs used in these systems generate significant heat, which must be effectively dissipated to ensure consistent curing performance and LED longevity.
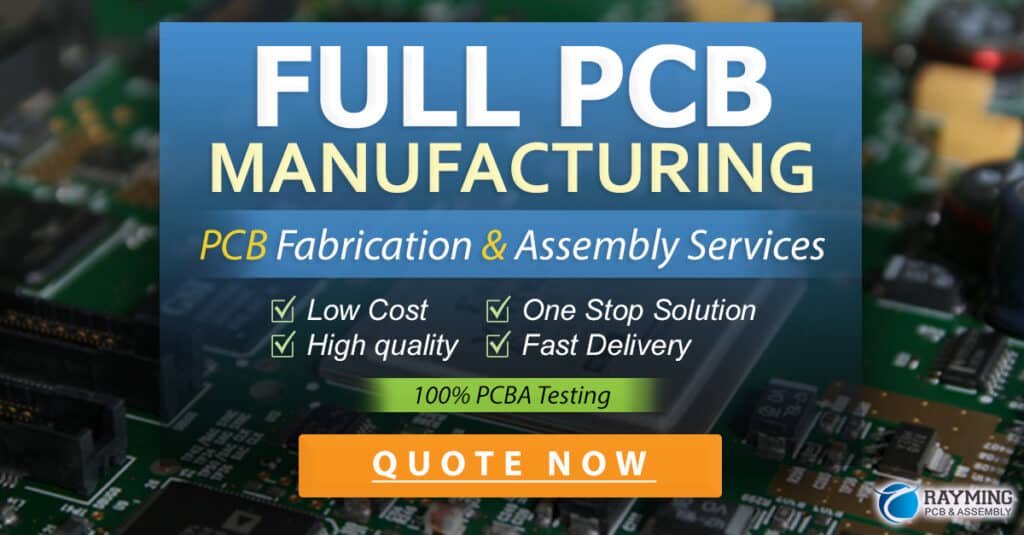
MCPCB Manufacturing Process
The manufacturing process for MCPCBs differs slightly from that of traditional PCBs due to the presence of the metal core. The main steps involved in MCPCB manufacturing are:
-
Substrate Preparation: The aluminum substrate is cleaned and treated to improve adhesion with the dielectric layer.
-
Dielectric Layer Application: A thin layer of dielectric material is applied to the aluminum substrate, typically through a lamination process.
-
Circuit Layer Printing: The copper circuit layer is printed onto the dielectric layer using standard PCB manufacturing techniques, such as screen printing or photolithography.
-
Etching and Plating: The unwanted copper is etched away, leaving the desired circuit pattern. Additional plating processes, such as solder mask application and surface finishing, may be applied as required.
-
Singulation: The individual MCPCBs are cut from the larger panel using routing or punching techniques.
Thermal Management Considerations in MCPCB Design
When designing MCPCBs for LED applications, several thermal management factors must be taken into account to ensure optimal performance and reliability:
-
Metal Core Thickness: The thickness of the metal core should be selected based on the power dissipation requirements of the LED system. Thicker metal cores provide better heat dissipation but may increase the overall board thickness.
-
Dielectric Layer Material: The choice of dielectric material impacts the thermal performance of the MCPCB. Materials with higher thermal conductivity, such as aluminum oxide or boron nitride, can enhance heat transfer from the LEDs to the metal core.
-
Copper Thickness: The thickness of the copper circuit layer affects both electrical and thermal performance. Thicker copper layers offer lower electrical resistance and better heat spreading, but may increase the cost of the MCPCB.
-
Thermal Vias: Incorporating thermal vias, which are conductive pathways through the dielectric layer, can further improve heat transfer from the LEDs to the metal core. The number, size, and placement of thermal vias should be optimized based on the specific thermal requirements of the LED system.
-
Surface Finish: The choice of surface finish, such as HASL (Hot Air Solder Leveling) or ENIG (Electroless Nickel Immersion Gold), can impact the thermal interface between the LEDs and the MCPCB. Finishes with lower thermal resistance can help to improve overall thermal performance.
Future Trends and Developments in MCPCB Technology
As the LED industry continues to evolve, so too does MCPCB technology. Some of the future trends and developments in MCPCB technology include:
-
Advanced Metal Core Materials: Researchers are exploring new metal core materials, such as copper or copper alloys, which offer even higher thermal conductivity than aluminum. These advanced materials could enable further improvements in heat dissipation and thermal management for high-power LED applications.
-
Embedded Components: The integration of passive components, such as resistors and capacitors, directly into the MCPCB structure is gaining interest. This embedded component approach can help to reduce the overall size and complexity of LED systems while improving electrical and thermal performance.
-
Flexible MCPCBs: The development of flexible MCPCBs, which use a thin, flexible metal core, is opening up new possibilities for LED applications in wearable electronics, automotive lighting, and other fields where conformability is required.
-
Improved Dielectric Materials: Ongoing research into advanced dielectric materials, such as nanomaterials or composite materials, aims to enhance the thermal conductivity and electrical insulation properties of MCPCBs. These improvements could lead to even better thermal management and higher power densities in LED applications.
-
Sustainable Manufacturing Processes: As environmental concerns continue to grow, there is an increasing focus on developing sustainable manufacturing processes for MCPCBs. This includes the use of eco-friendly materials, recycling of waste products, and energy-efficient manufacturing techniques.
FAQ
-
Q: What are the main differences between MCPCBs and traditional FR-4 PCBs?
A: MCPCBs use a metal core (usually aluminum) as the base material, which provides superior thermal conductivity compared to FR-4. This allows MCPCBs to dissipate heat more efficiently, making them ideal for high-power LED applications. Traditional FR-4 PCBs, on the other hand, have limited thermal management capabilities and are better suited for lower-power applications. -
Q: Can MCPCBs be used for applications other than LEDs?
A: While MCPCBs are most commonly associated with LED applications, they can also be used in other high-power electronics where thermal management is critical. This includes power converters, motor drives, and high-frequency circuits. However, LEDs remain the primary application for MCPCBs due to their specific thermal requirements. -
Q: Are MCPCBs more expensive than traditional PCBs?
A: Yes, MCPCBs typically have a higher initial cost compared to traditional FR-4 PCBs due to the additional materials and manufacturing processes involved. However, the improved thermal performance and reliability of MCPCBs often lead to long-term cost savings in LED applications through reduced maintenance and replacement costs. -
Q: How does the choice of dielectric material affect the performance of MCPCBs?
A: The dielectric layer in MCPCBs serves as an electrical insulator between the metal core and the copper circuit layer. The choice of dielectric material can impact the thermal conductivity, electrical insulation, and mechanical properties of the MCPCB. Materials with higher thermal conductivity, such as aluminum oxide or boron nitride, can enhance heat transfer and improve overall thermal performance. -
Q: What are the key considerations when designing MCPCBs for LED applications?
A: When designing MCPCBs for LED applications, several key factors must be considered, including metal core thickness, dielectric layer material, copper thickness, thermal via design, and surface finish. These factors all impact the thermal, electrical, and mechanical performance of the MCPCB and must be carefully optimized based on the specific requirements of the LED system. Additionally, the layout and placement of the LEDs on the MCPCB should be designed to ensure even heat distribution and minimize thermal stress on the components.
Conclusion
MCPCBs have revolutionized the LED industry by providing a reliable and efficient solution for thermal management in high-power LED applications. By combining the electrical functionality of a PCB with the thermal conductivity of a metal core, MCPCBs enable LEDs to operate at optimal temperatures, resulting in improved performance, reliability, and longevity.
As the demand for high-power, compact, and cost-effective LED solutions continues to grow, the role of MCPCBs in the LED industry will only become more significant. Ongoing advancements in MCPCB technology, such as new materials, embedded components, and sustainable manufacturing processes, will further drive the development of innovative LED products across various applications.
By understanding the key benefits, applications, and design considerations of MCPCBs, LED manufacturers and designers can leverage this technology to create cutting-edge LED solutions that meet the ever-increasing demands of the market. As MCPCBs continue to evolve, they will undoubtedly play a crucial role in shaping the future of the LED industry and enabling the widespread adoption of energy-efficient, high-performance LED lighting and display technologies.
No responses yet