What is a PCB Shield?
A PCB shield, or protective coating, is a thin layer of material applied to the surface of a printed circuit board to protect it from environmental hazards. These coatings act as a barrier between the delicate electronic components and the external elements that can cause harm. PCB Shields help prevent short circuits, corrosion, moisture damage, and other issues that can lead to device failure or malfunction.
Why are PCB Protective Coatings Important?
Protection from Moisture and Humidity
One of the primary reasons for using PCB protective coatings is to shield the circuit board from moisture and humidity. When exposed to high levels of moisture, PCBs can suffer from corrosion, which can lead to the deterioration of the copper traces and solder joints. This can result in short circuits, signal interference, and even complete device failure. By applying a water-resistant coating, you can minimize the risk of moisture-related damage and ensure the long-term reliability of your PCBs.
Insulation and Dielectric Properties
PCB protective coatings also provide excellent insulation and dielectric properties. These coatings help prevent electrical leakage and reduce the risk of short circuits between adjacent components or traces. By maintaining proper insulation, PCB shields contribute to the overall electrical integrity of the circuit board, ensuring stable performance and reducing the likelihood of signal distortion or crosstalk.
Protection from Mechanical Stress
In addition to environmental factors, PCBs are also susceptible to mechanical stress. Vibrations, shocks, and impacts can cause components to become loose or dislodged, leading to connection issues and potential device failure. PCB protective coatings help absorb and distribute mechanical stress, providing an extra layer of protection for the components. This is particularly important in applications where the device is exposed to frequent movement or harsh operating conditions.
Chemical Resistance
In certain industries, such as automotive, aerospace, and manufacturing, PCBs may be exposed to various chemicals, including oils, fuels, and solvents. These substances can degrade the PCB materials and cause corrosion or other forms of damage. By applying a chemically resistant coating, you can protect your PCBs from the adverse effects of these substances, ensuring their long-term durability and reliability.
Types of PCB Protective Coatings
There are several types of PCB protective coatings available, each with its own unique properties and benefits. Let’s explore some of the most common options:
Conformal Coatings
Conformal coatings are thin, protective films that conform to the contours of the PCB and its components. These coatings are typically applied using spraying, dipping, or brushing techniques. Conformal coatings offer excellent protection against moisture, dust, and chemical contaminants. They also provide good insulation properties and help prevent short circuits. Some popular conformal coating materials include:
-
Acrylic: Acrylic coatings are known for their excellent moisture resistance and easy application process. They provide good mechanical protection and are suitable for a wide range of environments.
-
Silicone: Silicone coatings offer superior thermal stability and flexibility. They are ideal for applications exposed to high temperatures or extreme temperature fluctuations. Silicone coatings also provide excellent moisture and chemical resistance.
-
Polyurethane: Polyurethane coatings are known for their toughness and durability. They offer excellent abrasion and chemical resistance, making them suitable for harsh industrial environments. Polyurethane coatings also provide good insulation properties.
-
Epoxy: Epoxy coatings are highly durable and offer excellent chemical and moisture resistance. They provide a strong, rigid protective layer that helps prevent mechanical damage to the PCB. Epoxy coatings are commonly used in high-reliability applications.
Potting Compounds
Potting compounds are thick, encapsulating materials that completely surround and protect the PCB and its components. These compounds are typically applied as a liquid and then cured to form a solid, protective shell. Potting compounds offer superior protection against moisture, dust, and mechanical stress. They also provide excellent insulation properties and help dissipate heat generated by the electronic components. Some common potting compound materials include:
-
Epoxy: Epoxy potting compounds are widely used due to their excellent mechanical strength, chemical resistance, and thermal conductivity. They provide a robust protective layer that shields the PCB from environmental hazards.
-
Silicone: Silicone potting compounds are known for their flexibility and thermal stability. They offer good moisture and chemical resistance and are suitable for applications exposed to high temperatures or vibrations.
-
Polyurethane: Polyurethane potting compounds provide excellent shock and vibration absorption. They are ideal for applications where the PCB is subjected to mechanical stress or impact. Polyurethane compounds also offer good moisture and chemical resistance.
Parylene Coatings
Parylene coatings are ultra-thin, conformal coatings that are applied using a vapor deposition process. These coatings provide exceptional protection against moisture, chemicals, and corrosion. Parylene coatings are known for their uniform coverage, even on complex PCB geometries, and their ability to penetrate small crevices and voids. They offer excellent dielectric properties and are biocompatible, making them suitable for medical device applications.
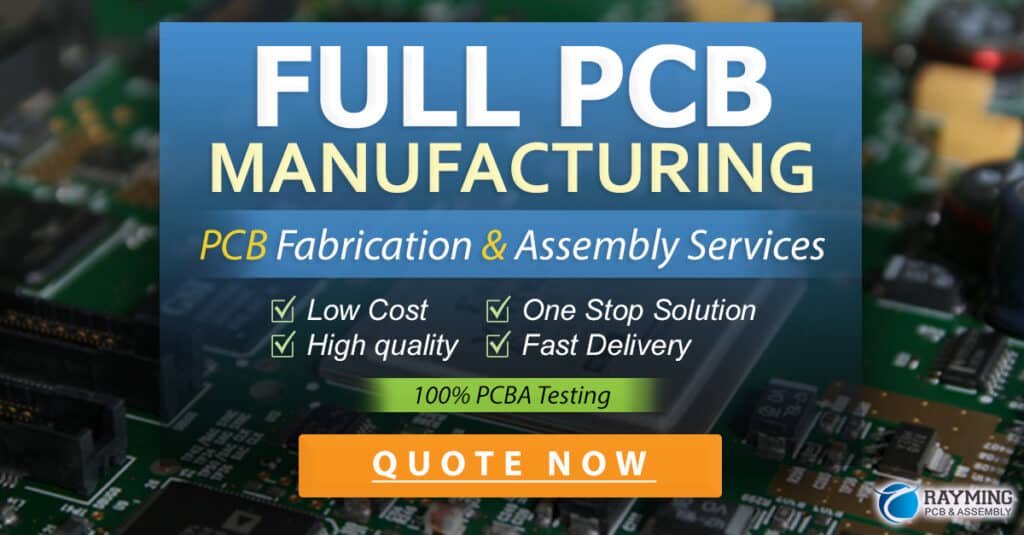
Selecting the Right PCB Protective Coating
Choosing the appropriate PCB protective coating depends on several factors, including the specific application, environmental conditions, and performance requirements. Consider the following aspects when selecting a coating for your PCBs:
-
Environmental factors: Assess the environmental conditions your PCBs will be exposed to, such as humidity, temperature, and chemical exposure. Choose a coating that offers adequate protection against these factors.
-
Insulation requirements: Evaluate the insulation and dielectric properties needed for your application. Consider the voltage levels and the potential for short circuits or electrical leakage.
-
Mechanical stress: If your PCBs will be subjected to vibrations, shocks, or impacts, opt for a coating that provides good mechanical protection and stress absorption.
-
Thermal management: Consider the thermal requirements of your application. Some coatings, such as silicone and epoxy, offer better thermal conductivity and can help dissipate heat generated by the electronic components.
-
Ease of application: Take into account the application process for the coating. Some coatings, like conformal coatings, are easier to apply and rework compared to potting compounds.
-
Cost: Evaluate the cost implications of different coating options. While investing in a high-quality protective coating may increase initial costs, it can lead to long-term savings by preventing device failures and extending the lifespan of your PCBs.
Application Methods for PCB Protective Coatings
Once you have selected the appropriate PCB protective coating, it’s essential to apply it correctly to ensure optimal coverage and protection. Here are some common application methods:
Spraying
Spraying is a widely used method for applying conformal coatings. It involves using a spray gun to apply a fine mist of the coating material onto the PCB surface. Spraying allows for quick and efficient coverage of large areas and is suitable for high-volume production. However, it may require masking of certain components to prevent overspray.
Dipping
Dipping involves immersing the PCB into a tank containing the coating material. This method ensures complete coverage of the PCB, including hard-to-reach areas. Dipping is suitable for complex PCB geometries and provides a uniform coating thickness. However, it may require longer drying times compared to other methods.
Brushing
Brushing is a manual application method that involves using a brush to apply the coating material onto the PCB surface. This method is suitable for small-scale applications or touch-up work. Brushing allows for precise control over the coating application but may result in inconsistent thickness and coverage.
Selective Coating
Selective coating involves applying the protective coating only to specific areas of the PCB, leaving other areas exposed. This method is useful when certain components or connectors need to remain uncoated for functionality or accessibility reasons. Selective coating can be achieved using specialized equipment or manual techniques like brush coating or dispensing.
Inspection and Quality Control
After applying the PCB protective coating, it’s crucial to perform thorough inspection and quality control to ensure the coating meets the required standards. Visual inspection can help identify any defects, such as bubbles, pinholes, or uneven coverage. Thickness measurement using techniques like micrometers or ultrasonic gauges can verify that the coating meets the specified thickness requirements.
Additionally, various testing methods can be employed to assess the effectiveness of the protective coating. These may include:
- Insulation resistance testing: Measures the electrical resistance between conductors to ensure proper insulation.
- Thermal cycling: Exposes the coated PCB to temperature variations to evaluate its performance under thermal stress.
- Salt spray testing: Assesses the coating’s resistance to corrosion by exposing it to a salt spray environment.
- Adhesion testing: Evaluates the coating’s adhesion to the PCB surface using methods like cross-hatch or tape tests.
Regular inspection and testing help maintain the quality and reliability of the PCB protective coating, ensuring it continues to provide the desired level of protection throughout the product’s lifecycle.
FAQ
- Q: How often should I reapply PCB protective coatings?
A: The frequency of reapplication depends on the specific coating material and the environmental conditions the PCB is exposed to. In general, conformal coatings and potting compounds are designed to provide long-lasting protection and do not require frequent reapplication. However, if the coating becomes damaged or starts to degrade, it may need to be repaired or replaced. Regular inspection and testing can help determine when reapplication is necessary.
- Q: Can PCB protective coatings be removed if needed?
A: Yes, most PCB protective coatings can be removed if necessary, such as for rework or repair purposes. The removal process depends on the type of coating material. Conformal coatings can often be removed using solvents or specialized stripping agents. Potting compounds may require mechanical removal or the use of heat to soften the material. It’s important to follow the manufacturer’s guidelines and take precautions to avoid damaging the PCB during the removal process.
- Q: Are PCB protective coatings suitable for all types of PCBs?
A: PCB protective coatings are suitable for a wide range of PCB types, including rigid, flexible, and rigid-flex PCBs. However, the choice of coating material and application method may vary depending on the specific requirements of the PCB and its intended application. Factors such as the PCB’s size, geometry, component density, and environmental exposure should be considered when selecting the appropriate coating solution.
- Q: Can PCB protective coatings interfere with the functionality of the circuit?
A: When applied correctly, PCB protective coatings should not interfere with the functionality of the circuit. However, improper application or incompatible coating materials can potentially cause issues. For example, applying a thick coating or using a material with high dielectric constant may affect the electrical properties of the PCB. It’s important to choose a coating that is compatible with the PCB materials and to follow proper application procedures to minimize any potential impact on functionality.
- Q: How do I choose between conformal coating and potting for my PCB?
A: The choice between conformal coating and potting depends on the level of protection required and the specific application. Conformal coatings provide a thin, protective layer that conforms to the PCB surface, offering good protection against moisture, dust, and light chemical exposure. They are suitable for applications where the PCB needs to be easily accessible for repairs or modifications. Potting, on the other hand, involves encapsulating the entire PCB in a thick, protective material. It provides superior protection against mechanical stress, moisture, and harsh environments. Potting is ideal for applications where the PCB is exposed to extreme conditions or where maximum protection is crucial. Consider the environmental factors, accessibility requirements, and the desired level of protection when making your decision.
Coating Type | Advantages | Disadvantages |
---|---|---|
Conformal Coating | – Thin, lightweight protection – Good moisture and dust resistance – Allows for easy repair and rework |
– Limited mechanical protection – May not provide complete coverage in hard-to-reach areas |
Potting Compound | – Excellent mechanical protection – Superior moisture and chemical resistance – Provides complete encapsulation |
– Adds weight and bulk to the PCB – Difficult to repair or rework – May require specialized application equipment |
Parylene Coating | – Ultra-thin, conformal coverage – Exceptional moisture and chemical resistance – Biocompatible and suitable for medical applications |
– Requires specialized vapor deposition equipment – Higher cost compared to other coating options |
Conclusion
PCB protective coatings, or PCB shields, play a vital role in ensuring the reliability, durability, and long-term performance of electronic devices. By providing a barrier against moisture, chemicals, mechanical stress, and other environmental hazards, these coatings help safeguard the delicate circuitry of PCBs. Conformal coatings, potting compounds, and Parylene coatings are among the most common types of PCB protective coatings, each offering unique properties and benefits.
When selecting a PCB protective coating, it’s crucial to consider the specific requirements of your application, including environmental factors, insulation needs, mechanical stress, thermal management, and cost. Proper application methods, such as spraying, dipping, brushing, or selective coating, ensure optimal coverage and protection. Regular inspection and quality control measures are essential to maintain the effectiveness of the coating throughout the product’s lifecycle.
By investing in the right PCB protective coating solution, you can significantly enhance the reliability and longevity of your electronic devices. Whether you’re designing consumer electronics, industrial equipment, or medical devices, PCB shields provide a robust defense against the harsh realities of the operating environment. So, don’t leave your circuits vulnerable – choose the appropriate PCB protective coating and give your devices the shield they need to perform at their best.
No responses yet