Introduction to PCB Types
Printed Circuit Boards (PCBs) are the backbone of modern electronics. They provide a platform for mounting and interconnecting electronic components to create a functional circuit. PCBs come in various types, each with its own set of characteristics and applications. In this article, we will focus on two common types of PCBs: single side PCB and multi-layer PCB. We will explore their differences, advantages, and disadvantages, as well as their manufacturing processes and applications.
What is a Single Side PCB?
A single side PCB, also known as a single-sided PCB or a single layer PCB, is a type of PCB that has conductive traces on only one side of the board. The other side of the board is typically left bare or used for component placement. Single side PCBs are the simplest and most basic type of PCB.
Advantages of Single Side PCBs
- Low cost: Single side PCBs are the most cost-effective type of PCB due to their simple design and manufacturing process.
- Quick turnaround: The manufacturing process for single side PCBs is relatively fast, making them ideal for rapid prototyping and low-volume production.
- Easy to design: Single side PCBs have a straightforward design process, making them suitable for beginners and simple projects.
Disadvantages of Single Side PCBs
- Limited routing options: With conductive traces on only one side of the board, single side PCBs have limited routing options, which can lead to larger board sizes and reduced circuit complexity.
- Lower component density: Due to the limited routing options, single side PCBs typically have lower component density compared to other PCB types.
- Reduced electrical performance: Single side PCBs may have reduced electrical performance due to the lack of a dedicated ground plane and the potential for increased electromagnetic interference (EMI).
Manufacturing Process of Single Side PCBs
The manufacturing process for single side PCBs involves the following steps:
- Substrate preparation: A copper-clad laminate board is cut to the desired size and shape.
- Drilling: Holes are drilled in the board for component placement and mounting.
- Copper etching: The unwanted copper is removed from the board using a chemical etching process, leaving only the desired conductive traces.
- Solder mask application: A protective solder mask is applied to the board to prevent short circuits and improve the board’s durability.
- Silkscreen printing: Component labels and other markings are printed on the board using a silkscreen process.
- Surface finish: A surface finish, such as HASL (Hot Air Solder Leveling) or ENIG (Electroless Nickel Immersion Gold), is applied to the exposed copper to prevent oxidation and improve solderability.
Applications of Single Side PCBs
Single side PCBs are commonly used in:
- Simple electronic devices: Such as toys, calculators, and basic remote controls.
- Low-power applications: Where circuit complexity and component density are not critical factors.
- Educational and hobbyist projects: Single side PCBs are often used for learning purposes and in DIY projects due to their simplicity and low cost.
What is a Multi-Layer PCB?
A multi-layer PCB, also known as a multi-sided PCB, is a type of PCB that has conductive traces on two or more layers of the board. These layers are interconnected using vias, which are small holes drilled through the board and plated with conductive material. Multi-layer PCBs offer several advantages over single side PCBs, making them suitable for more complex and demanding applications.
Advantages of Multi-Layer PCBs
- Increased routing options: With multiple layers available for routing, multi-layer PCBs can accommodate more complex circuits and higher component densities.
- Improved electrical performance: Multi-layer PCBs can incorporate dedicated ground and power planes, which reduce EMI and improve signal integrity.
- Reduced board size: By utilizing multiple layers, multi-layer PCBs can achieve the same functionality as single side PCBs in a smaller form factor.
- Enhanced thermal management: Multi-layer PCBs can include thermal management features, such as heat spreaders and thermal vias, to dissipate heat more effectively.
Disadvantages of Multi-Layer PCBs
- Higher cost: The manufacturing process for multi-layer PCBs is more complex and requires additional materials, resulting in higher costs compared to single side PCBs.
- Longer lead times: Due to the increased complexity of the manufacturing process, multi-layer PCBs typically have longer lead times than single side PCBs.
- More complex design process: Designing multi-layer PCBs requires more advanced skills and tools, as designers must consider factors such as layer stackup, via placement, and signal integrity.
Manufacturing Process of Multi-Layer PCBs
The manufacturing process for multi-layer PCBs involves the following steps:
- Substrate preparation: Multiple copper-clad laminate sheets are cut to the desired size and shape.
- Drilling: Holes are drilled in the layers for vias and component placement.
- Copper etching: The unwanted copper is removed from each layer using a chemical etching process, leaving only the desired conductive traces.
- Lamination: The etched layers are aligned and laminated together under high pressure and temperature to form a single board.
- Via plating: The drilled holes are plated with conductive material to interconnect the layers.
- Solder mask application: A protective solder mask is applied to the outer layers of the board.
- Silkscreen printing: Component labels and other markings are printed on the outer layers using a silkscreen process.
- Surface finish: A surface finish is applied to the exposed copper to prevent oxidation and improve solderability.
Applications of Multi-Layer PCBs
Multi-layer PCBs are commonly used in:
- Complex electronic devices: Such as smartphones, computers, and medical equipment.
- High-speed applications: Where signal integrity and low EMI are critical, such as in telecommunications and networking equipment.
- Aerospace and military applications: Where reliability and performance under extreme conditions are essential.
- Compact devices: Where space is limited, and high component density is required, such as in wearable technology and IoT devices.
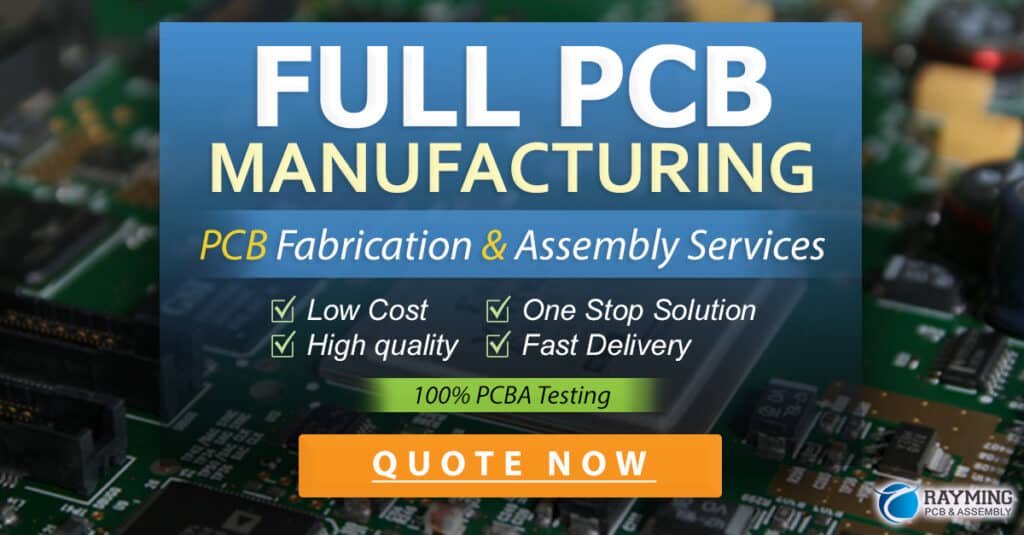
Comparison Table: Single Side PCB vs. Multi-Layer PCB
Feature | Single Side PCB | Multi-Layer PCB |
---|---|---|
Layers | One | Two or more |
Routing options | Limited | Extensive |
Component density | Low | High |
Electrical performance | Reduced | Improved |
Thermal management | Limited | Enhanced |
Cost | Low | High |
Lead time | Short | Long |
Design complexity | Simple | Advanced |
Applications | Simple devices, low-power applications, educational projects | Complex devices, high-speed applications, aerospace and military, compact devices |
Frequently Asked Questions (FAQ)
-
Q: Can a single side PCB have components on both sides?
A: Yes, a single side PCB can have components on both sides, but the conductive traces will only be present on one side of the board. -
Q: How many layers can a multi-layer PCB have?
A: Multi-layer PCBs can have anywhere from two to more than 50 layers, depending on the application and manufacturing capabilities. -
Q: Are multi-layer PCBs more durable than single side PCBs?
A: Multi-layer PCBs are generally more durable than single side PCBs due to their laminated construction and the presence of multiple layers that provide structural support. -
Q: Can a single side PCB be converted into a multi-layer PCB?
A: No, a single side PCB cannot be directly converted into a multi-layer PCB. The manufacturing processes for these two types of PCBs are different, and a new multi-layer PCB would need to be designed and manufactured from scratch. -
Q: Which type of PCB is better for high-frequency applications?
A: Multi-layer PCBs are generally better suited for high-frequency applications due to their improved electrical performance, dedicated ground and power planes, and ability to incorporate controlled impedance features.
Conclusion
Single side PCBs and multi-layer PCBs are two common types of printed circuit boards, each with its own set of advantages, disadvantages, and applications. Single side PCBs are simple, cost-effective, and suitable for basic projects and low-power applications. On the other hand, multi-layer PCBs offer increased routing options, improved electrical performance, and enhanced thermal management, making them ideal for complex devices, high-speed applications, and compact designs.
When choosing between a single side PCB and a multi-layer PCB, it is essential to consider factors such as circuit complexity, performance requirements, board size, and budget. By understanding the differences between these two PCB types and their respective manufacturing processes, designers and engineers can make informed decisions and select the most appropriate type of PCB for their projects.
As technology continues to advance, the demand for more sophisticated and compact electronic devices will likely drive the increased adoption of multi-layer PCBs. However, single side PCBs will continue to play a role in simple, low-cost applications and educational projects. Ultimately, the choice between a single side PCB and a multi-layer PCB will depend on the specific requirements and constraints of each project.
No responses yet