Understanding LED PCBs
LED PCBs are specialized printed circuit boards designed to support and connect light-emitting diodes (LEDs) in a lighting system. These PCBs not only provide a stable platform for the LEDs but also ensure proper electrical connections, heat dissipation, and overall performance of the lighting fixture.
Key Components of an LED PCB
An LED PCB consists of several essential components that work together to ensure optimal functionality and reliability:
- Substrate: The base material of the PCB, typically made of FR-4 or aluminum for better heat dissipation.
- Copper Layers: Conductive copper traces that carry electrical signals and power to the LEDs.
- Solder Mask: A protective layer that covers the copper traces, preventing short circuits and oxidation.
- Silkscreen: A printed layer that provides information such as component designators and logos.
- LEDs: The light-emitting diodes mounted on the PCB, available in various colors, sizes, and power ratings.
LED PCB Design Considerations
Designing an LED PCB requires careful consideration of several factors to ensure optimal performance and longevity:
- Thermal Management: Proper heat dissipation is crucial for LED PCBs to prevent overheating and premature failure of the LEDs.
- Electrical Characteristics: Ensuring appropriate voltage, current, and power ratings for the LEDs and other components.
- Optical Performance: Optimizing the placement and orientation of LEDs to achieve the desired light distribution and intensity.
- Mechanical Stability: Designing the PCB to withstand vibrations, shocks, and other mechanical stresses.
- Manufacturing Feasibility: Considering the limitations and capabilities of the PCB fabrication and assembly processes.
LED PCB Fabrication Process
The fabrication of LED PCBs involves several critical steps to ensure the highest quality and reliability:
- PCB Design: Creating the schematic and layout of the PCB using specialized software, such as Altium Designer or Eagle.
- Material Selection: Choosing the appropriate substrate, copper thickness, and solder mask based on the application requirements.
- PCB Manufacturing: Producing the bare PCB through processes such as etching, drilling, and plating.
- Solder Mask Application: Applying the solder mask layer to protect the copper traces and prevent short circuits.
- Silkscreen Printing: Adding the silkscreen layer to provide necessary information and markings.
- Quality Control: Conducting thorough inspections and tests to ensure the PCB meets the specified quality standards.
PCB Material Selection
Selecting the right material for an LED PCB is essential for optimal performance and reliability. The most common materials used in LED PCBs are:
Material | Advantages | Disadvantages |
---|---|---|
FR-4 | Low cost, good insulation, easy to work with | Limited thermal conductivity, not suitable for high-power LEDs |
Aluminum | Excellent thermal conductivity, lightweight | Higher cost, requires special manufacturing processes |
Metal Core PCB (MCPCB) | Good thermal management, suitable for high-power LEDs | Higher cost, limited flexibility in design |
LED PCB Assembly Process
Once the bare PCB is fabricated, the next step is to assemble the components, including the LEDs, onto the board. The assembly process involves several key steps:
- Solder Paste Application: Applying solder paste to the pads on the PCB where the components will be placed.
- Component Placement: Placing the LEDs and other components onto the PCB using a pick-and-place machine or manual methods.
- Reflow Soldering: Passing the PCB through a reflow oven to melt the solder paste and create a strong electrical and mechanical connection between the components and the PCB.
- Inspection: Conducting visual and automated optical inspections (AOI) to ensure proper component placement and soldering quality.
- Testing: Performing functional tests to verify the performance and reliability of the assembled LED PCB.
LED Placement and Orientation
The placement and orientation of LEDs on the PCB play a crucial role in achieving the desired optical performance. Key considerations include:
- LED Spacing: Ensuring appropriate spacing between LEDs to achieve uniform light distribution and prevent thermal interference.
- LED Orientation: Aligning the LEDs in the correct direction to optimize light output and beam angle.
- Optical Accessories: Incorporating lenses, reflectors, or diffusers to enhance the optical performance of the LED PCB.
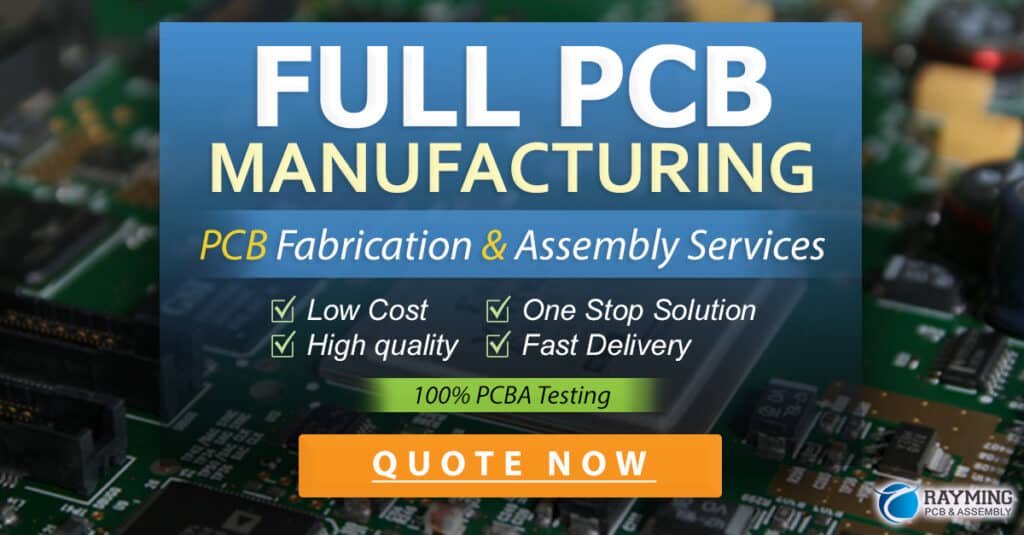
Quality Control and Testing
To ensure the highest quality and reliability of LED PCBs, stringent quality control measures and thorough testing are essential throughout the fabrication and assembly processes.
Quality Control Measures
- Visual Inspection: Conducting visual checks for any defects, such as scratches, dents, or discoloration on the PCB.
- Automated Optical Inspection (AOI): Using advanced machine vision systems to detect any component placement or soldering issues.
- X-Ray Inspection: Employing X-ray imaging to inspect hidden solder joints and internal connections.
- Electrical Testing: Performing continuity, resistance, and insulation tests to verify the electrical integrity of the PCB.
Performance Testing
- Light Output and Distribution: Measuring the luminous flux, color temperature, and beam angle of the LED PCB to ensure compliance with the specified requirements.
- Thermal Performance: Monitoring the temperature of the PCB and LEDs under various operating conditions to validate the thermal management design.
- Reliability Testing: Conducting accelerated life tests, such as thermal cycling and vibration tests, to assess the long-term reliability of the LED PCB.
Advanced LED PCB Technologies
As the LED lighting industry continues to evolve, new technologies and innovations are emerging to enhance the performance, efficiency, and functionality of LED PCBs.
COB (Chip-on-Board) LEDs
COB LEDs are a compact and efficient solution for high-power lighting applications. In this technology, multiple LED chips are directly mounted onto the PCB, eliminating the need for individual packaging. COB LEDs offer several advantages:
- Higher light output and efficiency
- Better thermal management
- Simplified assembly process
- Reduced size and weight
Flexible LED PCBs
Flexible LED PCBs are designed to conform to curved or irregular surfaces, opening up new possibilities for creative lighting designs. These PCBs are made of flexible materials, such as polyimide or PEEK, and can be bent or folded without damaging the circuit. Flexible LED PCBs are ideal for applications such as:
- Automotive interior lighting
- Wearable electronics
- Signage and displays
- Decorative lighting
Smart LED PCBs
Smart LED PCBs incorporate additional features and functionalities, such as sensors, microcontrollers, and wireless connectivity, to enable intelligent lighting control and automation. These PCBs can be programmed to respond to various stimuli, such as motion, ambient light, or user input, and can be integrated into IoT (Internet of Things) systems for remote monitoring and control.
FAQ
-
What is the difference between an LED PCB and a regular PCB?
LED PCBs are specifically designed to support and connect LEDs, with a focus on thermal management, electrical characteristics, and optical performance. Regular PCBs are more general-purpose and may not have the same level of optimization for LED applications. -
How do I choose the right material for my LED PCB?
The choice of material depends on factors such as the power rating of the LEDs, the thermal requirements, and the overall design constraints. FR-4 is a good choice for low-power applications, while aluminum or MCPCBs are better suited for high-power LEDs that generate more heat. -
What is the importance of thermal management in LED PCBs?
Proper thermal management is crucial for LED PCBs to prevent overheating, which can lead to reduced light output, color shifts, and premature failure of the LEDs. Effective thermal management helps to dissipate heat away from the LEDs, ensuring optimal performance and longevity. -
Can I assemble LED PCBs manually, or do I need specialized equipment?
While it is possible to assemble LED PCBs manually, it is recommended to use specialized equipment, such as pick-and-place machines and reflow ovens, for consistent and reliable results. Manual assembly can be time-consuming and prone to errors, especially for high-volume production. -
How can I ensure the quality and reliability of my LED PCBs?
To ensure the quality and reliability of LED PCBs, implement a comprehensive quality control and testing plan that includes visual inspections, automated optical inspections (AOI), electrical testing, and performance testing. Additionally, work with experienced and reputable PCB fabrication and assembly partners who adhere to strict quality standards and industry best practices.
Conclusion
As an LED PCB Expert, I have shared my knowledge and insights into the fabrication and assembly of high-quality LED PCBs. From understanding the key components and design considerations to exploring advanced technologies and ensuring quality control, this article has covered the essential aspects of LED PCB manufacturing.
By leveraging the expertise of experienced professionals and staying up-to-date with the latest industry trends and innovations, you can create LED PCBs that deliver exceptional performance, reliability, and efficiency for your lighting applications. Whether you are developing a new LED lighting product or optimizing an existing design, the information provided in this article will help you make informed decisions and achieve the best possible results.
No responses yet