What is the Internet of Things (IoT)?
IoT refers to the network of physical objects embedded with sensors, software, and connectivity which enables them to connect and exchange data. This includes everything from smartphones and wearables to home appliances, vehicles, and industrial equipment. Analysts predict there will be over 75 billion IoT-connected devices by 2025.
IoT Applications in Electronics Manufacturing
IoT has many applications across the electronics manufacturing process:
Predictive Maintenance
Sensors on production equipment can continuously monitor key parameters like vibration, temperature, and output. Advanced analytics predict when machines require maintenance, preventing unplanned downtime. Studies show predictive maintenance increases productivity by 25% and reduces breakdowns by 70%.
Traditional Maintenance | IoT Predictive Maintenance |
---|---|
Reactive, unplanned | Proactive, data-driven |
Time-based inspections | Continuous monitoring |
Frequent failures | 70% less breakdowns |
Process Optimization
IoT provides real-time visibility into production processes. Sensors track parts and assets across the factory floor. Analytics optimize scheduling, inventory, and workflows. Digital work instructions guide operators. This automation improves efficiency, quality, and agility.
Automated Material Handling
Autonomous guided vehicles and robotics—equipped with sensors and wirelessly connected via IoT—streamline material transport and handling. This minimizes manual labor, damage, and human error. IoT-connected conveyor belts, storage systems, and machines enable optimal routing and automated replenishment. Real-time location tracking pinpoints parts at each stage.
Quality Assurance
IoT sensors integrated into products allow for real-time quality testing and monitoring during and after production. Sensors detect defects and nonconformities, isolating issues earlier. Analytics uncover the root causes of quality problems by correlating sensor data with manufacturing conditions. This reduces scrap, rework, and warranty claims.
Quality Metric | Traditional QA | IoT-Enabled QA |
---|---|---|
Scrap Rate | 5% | 2% |
Defects | 10,000 ppm | 2,000 ppm |
Reliability | 95% | 99% |
Energy Management
Wirelessly connected meters and sensors track the energy consumption of machines, systems, and facilities in real-time. Advanced algorithms optimize usage to reduce costs and carbon footprint. Smart HVAC and lighting automatically adjust based on conditions. Manufacturers can participate in demand-response programs with utilities.
Key Technologies Enabling IoT in Manufacturing
Several technologies work together to enable IoT applications in electronics manufacturing:
Industrial IoT Sensors
The foundation of industrial IoT is the sensors that collect data from machines and processes. These include sensors for vibration, temperature, pressure, flow, power, leaks, and more. Ongoing innovations miniaturize sensors, reduce costs, and improve durability for harsh factory environments.
Wireless Connectivity
Pervasive wireless connectivity links IoT sensors to the internet and cloud.
- WiFi is common for connecting equipment within facilities
- Cellular (4G/5G) connects remote sites and provides backup
- LPWAN technologies like LoRa enable long-range, low-power sensors
- Bluetooth is used for close-range, low data rate applications
- RFID wireless tags track parts, assets, inventory
Cloud Platforms
IoT device management platforms running in the cloud provision, configure, monitor, and update IoT sensors and devices remotely. They provide security, data ingestion, storage, processing, analytics, and integration. Leading platforms include Microsoft Azure IoT, Amazon AWS IoT, IBM Watson IoT, and PTC ThingWorx.
Big Data Analytics
The manufacturing IoT generates massive volumes of real-time data. Big data platforms like Hadoop ingest and store this data at scale. Powerful stream and batch processing analyzes the data. Machine learning builds models to detect anomalies, make predictions, and optimize. Analytics turn data into actionable insights.
Edge Computing
Some IoT applications require ultra-low latency processing for real-time responsiveness. Rather than sending all data to the cloud, edge computing does processing closer to the source on edge gateways, routers, and on-premise servers. This enables applications like machine vision QA and automated robot control.
Digital Twin
A key concept in industrial IoT is the digital twin—a virtual model that mirrors a real-world object, product, or process. Fed by real-time IoT data, the digital twin simulates “what-if” scenarios to optimize design and operation. Manufacturers use digital twins to validate products, fine-tune production, and troubleshoot issues.
Augmented Reality (AR)
AR overlays digital information onto a real-world view, often through smart glasses. In IoT-Enabled Manufacturing, AR provides workers with contextual data, instructions, and guidance. AR enables remote expert support, on-the-job training, and service. It improves productivity, quality, and safety.
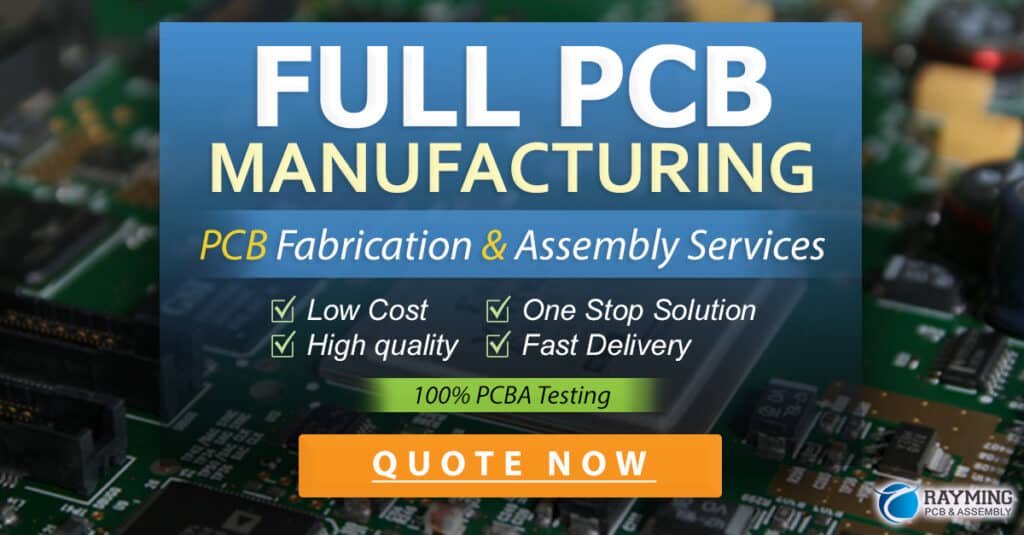
Challenges of Implementing Industrial IoT
While industrial IoT offers compelling benefits, manufacturers must navigate several challenges and risks:
Security
The proliferation of connected devices expands the attack surface for hackers. A breach could compromise sensitive data, disrupt production, or cause unsafe conditions. Manufacturers need to implement end-to-end security covering devices, networks, and cloud. This includes access controls, encryption, monitoring, and updates.
Interoperability and Standards
The IIoT ecosystem spans diverse devices, protocols, and platforms from multiple vendors. Lack of interoperability inhibits data exchange and integrated control. The industry is converging on standards like OPC-UA, MTConnect, and DDS to enable plug-and-play interoperability between systems.
Workforce Readiness
Deploying IIoT requires new skills in data science, networking, cybersecurity, and automation. Manufacturers need to reskill existing workers and recruit tech talent. Engaging workers is critical to driving adoption. Change management, training, and user-friendly tools smooth the transition.
Proving ROI
The business case for IIoT requires demonstrating clear return on investment. But calculating ROI is challenging because many benefits are hard to quantify and accrue over time. Focused IIoT pilots targeting high-priority use cases help build support and pave the way for larger rollouts.
The Future of IoT in Electronics Manufacturing
As IoT technologies advance and converge with other innovations like AI and robotics, even more transformative impacts are expected:
Lights-Out Manufacturing
Pervasive automation and robotics enabled by industrial IoT will make full lights-out manufacturing a reality. Advanced facilities will run autonomously 24/7 with minimal human intervention, significantly boosting productivity.
Mass Customization
IoT will enable cost-effective mass customization of electronics products. Connected, reconfigurable factories will dynamically adapt to shifting requirements and small lot sizes. Direct digital production technologies like 3D printing will allow economical customization.
Servitization
Manufacturers will increasingly sell value-added services, not just products. IoT connectivity allows remote monitoring, predictive maintenance, and performance optimization of products in the field. This enables new business models like product-as-a-service.
Supply Chain 4.0
IoT extends beyond the factory to the entire supply chain. Sensors will track and trace materials and products from end-to-end. This will create a fully transparent, connected supply chain for enhanced planning, coordination, and resiliency.
FAQ
How much does it cost to implement industrial IoT in electronics manufacturing?
Costs depend on the scale and scope of the deployment, but can range from hundreds of thousands to millions of dollars. Elements include sensors, connectivity, software, integration, and training. But the ROI can be substantial from increased efficiency, quality, and uptime.
What are the most important IoT applications in electronics manufacturing?
Key use cases are predictive maintenance, production optimization, inventory tracking, and quality assurance. Predictive maintenance alone can reduce downtime by 50% and increase productivity by 25%.
How can I ensure the security of my industrial IoT deployment?
Security requires a holistic approach across devices, networks, and cloud. Best practices include hardening devices, encryption, access controls, network segmentation, security monitoring, and regular patching/updates. The IEC 62443 standard provides a framework for industrial IoT security.
How long does it take to implement industrial IoT and see results?
Implementation timelines range from a few months for a limited pilot to a year or more for a full production rollout. While some benefits like greater visibility are immediate, others like predictive maintenance may take several months of data collection to fully realize.
What should I look for in an industrial IoT platform?
Key considerations are scalability, reliability, security, and interoperability for your device and data ecosystem. Look for extensive integration options, edge capabilities, advanced analytics, and domain-specific applications. Also consider the provider’s industry experience and support model.
Conclusion
The Internet of Things is ushering in a new era of smart, connected manufacturing. IoT-enabled electronics factories can achieve unprecedented levels of efficiency, agility, and quality. As manufacturers navigate the challenges of complexity, security, and skills, those that successfully harness IoT will be positioned to thrive in the fast-evolving Industry 4.0 world.
No responses yet