Introduction to Blind Microvias
Blind microvias are an essential technology for increasing the integration density and functionality of today’s complex printed circuit boards (PCBs). A blind microvia is a small laser-drilled hole that connects an outer layer to an inner layer of a PCB, without going all the way through the board like a traditional through-hole via. This allows for more compact routing and higher component density.
Typical blind microvia diameters range from 0.003 to 0.006 inches (75-150 microns), with a depth of 0.002 to 0.005 inches (50-125 microns). They enable finer pitch components and interconnects compared to through-hole vias.
Key Benefits of Blind Microvias
- Increased PCB design flexibility and integration density
- Smaller footprint and lower profile components
- Shorter signal paths for improved electrical performance
- Easier routing of dense BGA and chip-scale packages
- Enables HDI (high-density interconnect) PCB designs
PCB Manufacturing Process for Blind Microvias
Laser Drilling
The first step in creating blind microvias is precision laser drilling of the via holes. CO2 lasers and UV lasers are the two main types used:
Laser Type | Wavelength | Hole Size | Drilling Speed |
---|---|---|---|
CO2 | 9.3-10.6 μm | >50 μm | Moderate |
UV | 355 nm | 25-150 μm | High |
CO2 lasers have a longer wavelength, enabling drilling of larger holes but at slower speeds. UV lasers offer finer resolution and faster drilling for microvias. The choice depends on the specific via size and throughput requirements.
Via Plating
After laser drilling, the microvia holes need to be metallized to establish electrical conductivity. This is done through an electroless copper plating process:
-
Desmear – A chemical desmear solution removes drilling debris and prepares hole for plating.
-
Activation – A catalyst like palladium is deposited to make the dielectric surface conductive.
-
Electroless Copper – The holes are plated with a thin electroless copper seed layer.
-
Electroplating – Additional copper is electroplated onto the seed layer to the desired thickness, typically 0.5-1.0 mils.
Stacking and Filling
For high layer-count HDI designs, multiple build-up layers with stacked microvias are used. The microvias are filled with copper and planarized before adding the next layer. Stacked and staggered microvias allow dense vertical interconnects between layers.
Microvia Stacking | Description |
---|---|
Stacked | Vias are stacked directly on top of each other |
Staggered | Vias are offset slightly from the ones below |
Stacked and Staggered | Combines stacking and staggering for maximum density |
HDI PCB Design Considerations
Via Placement and Aspect Ratio
Careful attention must be paid to microvia placement during PCB layout. Key considerations include:
-
Pad size – Via pads should be sized to allow sufficient room for annular rings and tolerance. Typical pad diameters are 1.0-1.5x the drill size.
-
Pitch – The via-to-via spacing is limited by the pad size and drilling tolerance. Common pitches are 0.5-1.0mm for microvias.
-
Aspect ratio – This is the ratio of via depth to diameter. For reliable plating, aspect ratios are typically limited to 0.75:1 for blind microvias. Exceeding this can lead to voids or incomplete plating.
Signal Integrity and Electrical Performance
Blind microvias offer several signal integrity advantages compared to through-hole vias:
- Shorter stub length, minimizing the capacitive loading and impedance discontinuity
- Reduced loop inductance and crosstalk by having shorter parallel via segments
- Ability to place vias closer to pads for cleaner breakout and escape routing
However, microvias do introduce some additional resistance and inductance compared to a solid plane layer. This must be accounted for in high-speed designs through accurate PCB modeling and simulation.
Layout and Routing Guidelines
Some general layout guidelines for blind Microvia PCBs include:
- Minimize the number of vias in high-speed nets to reduce discontinuities.
- Avoid vias in pads when possible to improve assembly yield. Use via-in-pad only when necessary.
- Provide sufficient clearance between via pads and traces, typically at least 4 mils.
- Follow the manufacturer’s design rules and guidelines for via size, pitch, and aspect ratio.
- Use autorouting carefully, as the algorithms may not always optimize via placement. Manual cleanup is often needed.
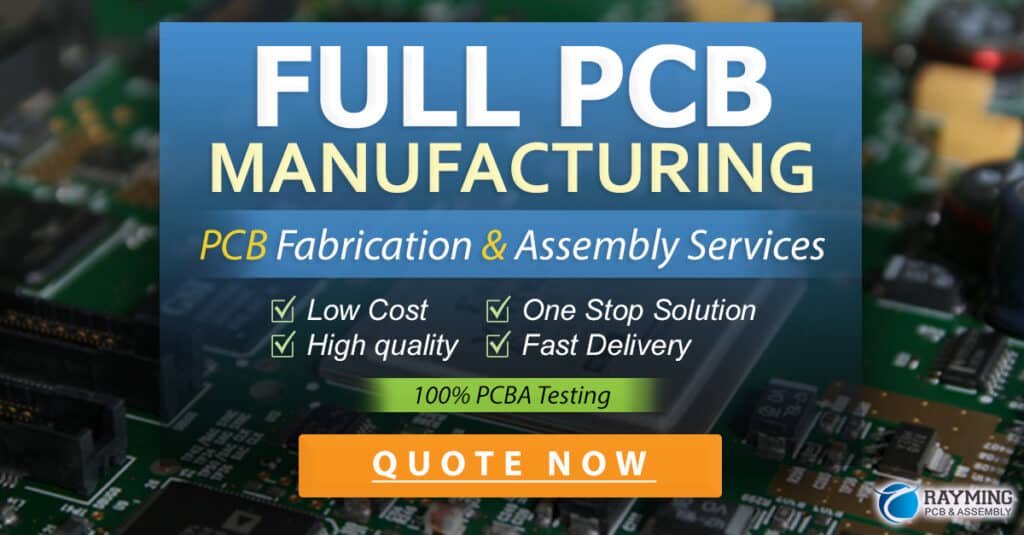
Advanced Applications of Blind Microvias
3D Packaging and Interposers
Blind microvias are an key enabling technology for advanced 3D packaging and chip integration. Some examples include:
-
Package-on-Package (PoP) – Blind vias allow dense vertical interconnects between stacked die or packages. This is commonly used for memory on logic die stacking.
-
Through-Silicon Vias (TSVs) – Blind vias can connect to TSVs in 3D ICs, enabling high-bandwidth die-to-die communication.
-
Silicon Interposers – High-density blind vias in silicon interposer substrates enable 2.5D integration of multiple die with fine pitch interconnects.
Embedded Components
Blind microvias also allow embedding of both active and passive components within the PCB substrate. This can provide several benefits:
– Reduced footprint and higher packaging efficiency
– Shorter interconnects between embedded and surface components
– Improved electrical and thermal performance
– Better mechanical protection of components
Some common examples of embedded components include:
– Thin chips embedded in cavities and connected with blind vias
– Embedded capacitors and resistors using blind vias as terminals
– Optical waveguides embedded and connected to surface devices with microvias
High-Frequency and mmWave Applications
As wireless and high-speed digital systems move to ever higher frequencies, blind microvias become critical for RF PCB Designs.
In mmWave 5G and radar applications from 30 GHz to 100 GHz, wavelengths become very small. This requires extremely dense via spacing to avoid creating unwanted “via fences” that can disrupt current flow. Blind microvias are essential to achieving the required via density and pitch.
Microvias also help minimize parasitic inductance and capacitance in high-frequency interconnects. The reduced stub length is beneficial for maintaining signal integrity and minimizing radiation loss.
Summary
Blind microvias are a versatile technology that enable higher integration density, improved electrical performance, and advanced packaging solutions for today’s demanding PCB Applications. From HDI designs to 3D ICs and mmWave systems, blind microvias are essential to achieving the next level of miniaturization and performance.
However, blind microvias do require careful design considerations and advanced manufacturing capabilities. Designers must pay close attention to via placement, spacing, and aspect ratios to ensure manufacturability and reliability. Close collaboration between design and fabrication teams is essential.
As electronic systems continue to increase in complexity and decrease in size, blind microvias will undoubtedly play an even greater role in future PCB designs. Staying up to date with the latest microvia technologies and design practices will be critical for success in this rapidly evolving field.
Frequently Asked Questions
What is the difference between blind and buried microvias?
Blind vias connect an outer layer to an inner layer, but do not go through the entire PCB. Buried vias connect two inner layers together without being visible on the outer layers. Blind vias are more common and easier to manufacture than buried vias.
What are the limitations of blind microvia technology?
The main limitations of blind microvias are the achievable aspect ratio (hole depth to diameter) and the need for specialized laser drilling and plating equipment. Most PCB shops are limited to aspect ratios of 0.75:1 or less for reliable production. Very small microvias (<50 microns) may also be challenging to fabricate.
How much do blind microvias add to PCB cost?
The cost impact of blind microvias depends on the via density, diameter, and layer count. In general, adding blind microvias will increase the cost by 20-50% compared to a through-hole via design. However, this can be offset by the space and layer reduction enabled by microvias. A cost-benefit analysis should be done based on the specific design requirements.
Are there any reliability concerns with blind microvias?
When properly designed and manufactured, blind microvias have proven to be highly reliable. However, there are a few potential failure modes to be aware of:
- Via cracking due to CTE mismatch or insufficient metal plating
- Outgassing and delamination during reflow if vias are not completely cleaned
- Via-to-pad separation due to weak adhesion or mechanical stress
Following good design practices and qualify vendor processes can mitigate these risks. Thorough reliability testing should be performed for critical applications.
What are the current trends and future directions for blind microvia technology?
Some of the key trends and developments in blind microvia technology include:
- Smaller via diameters (<50 microns) and higher aspect ratios (>1:1) to enable even greater density
- Advances in laser drilling technology for faster and more precise via formation
- Increased use of microvias in 3D packaging and heterogeneous integration applications
- Adoption of blind microvias in high-volume consumer products like smartphones to reduce size and cost
- Development of new materials and processes for reliable microvia filling and stacking
As data rates continue to rise and packaging densities increase, blind microvias will remain a critical technology for PCB designers and manufacturers to master. Continuing research and innovation in this area will help meet the demands of next-generation electronic products.
No responses yet