Introduction to Custom PCBs
A custom PCB, or Printed Circuit Board, is a specially designed circuit board that is tailored to meet specific electronic requirements. Unlike generic PCBs, custom PCBs are designed and manufactured according to the unique needs of a particular project or application. This allows for greater flexibility, efficiency, and functionality in electronic devices.
In this comprehensive guide, we will walk you through the process of creating a custom PCB from start to finish. We will cover everything from the basics of PCB design to the various manufacturing techniques and considerations involved in producing a high-quality custom PCB.
Understanding the Basics of PCB Design
What is a PCB?
A Printed Circuit Board (PCB) is a flat board made of insulating material, such as fiberglass or plastic, with conductive pathways etched onto its surface. These pathways, known as traces, connect various electronic components, such as resistors, capacitors, and integrated circuits (ICs), to form a complete electronic circuit.
PCBs are used in virtually all electronic devices, from simple gadgets like calculators and digital clocks to complex systems like computers and smartphones. They provide a stable and organized platform for electronic components, enabling efficient and reliable operation of the device.
Types of PCBs
There are several types of PCBs, each with its own unique characteristics and applications. The most common types include:
-
Single-sided PCBs: These PCBs have conductive traces on only one side of the board. They are the simplest and most cost-effective type of PCB, suitable for basic electronic projects.
-
Double-sided PCBs: These PCBs have conductive traces on both sides of the board, allowing for more complex circuit designs and higher component density. They are commonly used in more advanced electronic devices.
-
Multi-layer PCBs: These PCBs consist of multiple layers of conductive traces separated by insulating layers. They offer the highest level of complexity and density, making them ideal for advanced electronic systems, such as smartphones and computers.
-
Flexible PCBs: These PCBs are made of flexible materials, such as polyimide, allowing them to bend and conform to various shapes. They are often used in wearable electronics and devices with limited space.
-
Rigid-Flex PCBs: These PCBs combine the benefits of both rigid and flexible PCBs, featuring rigid sections for mounting components and flexible sections for connecting them. They are commonly used in aerospace and military applications.
PCB Design Software
To create a custom PCB, you will need to use specialized PCB design software. There are several options available, ranging from free, open-source tools to professional, paid software suites. Some popular PCB design software include:
-
KiCad: A free, open-source PCB design suite that offers schematic capture, PCB layout, and 3D viewing capabilities.
-
Eagle: A widely used PCB design software that offers a free version for non-commercial use and paid versions with advanced features.
-
Altium Designer: A professional-grade PCB design software with a wide range of features and integrations, suitable for complex projects and large teams.
-
Fusion 360: A cloud-based PCB design software that offers seamless integration with mechanical design tools, making it ideal for projects involving both electronic and mechanical components.
When choosing a PCB design software, consider factors such as ease of use, feature set, compatibility with your operating system, and cost. It’s also a good idea to familiarize yourself with the software’s user interface and workflow before starting your project.
Designing Your Custom PCB
Creating a Schematic
The first step in creating a custom PCB is to design the schematic. A schematic is a graphical representation of the electronic circuit, showing the various components and their interconnections. To create a schematic, follow these steps:
-
Choose your components: Select the electronic components required for your circuit, such as resistors, capacitors, ICs, and connectors. Make sure to choose components that are readily available and suitable for your application.
-
Create the schematic: Using your chosen PCB design software, place the components on the schematic and connect them according to your circuit design. Be sure to follow best practices for schematic design, such as using appropriate symbols, labeling components, and organizing the schematic for readability.
-
Assign component values: Specify the values of the components, such as resistance, capacitance, and IC part numbers. This information will be used later when selecting physical components for the PCB.
-
Check for errors: Carefully review your schematic for any errors or inconsistencies. Most PCB design software include built-in error-checking tools that can help identify potential issues.
PCB Layout
Once your schematic is complete, you can move on to the PCB layout stage. This involves arranging the physical components on the PCB and routing the conductive traces between them. Follow these steps to create your PCB layout:
-
Define the board outline: Determine the size and shape of your PCB based on the space available in your device and the number of components required. Most PCB design software allows you to create custom board outlines or choose from predefined templates.
-
Place the components: Arrange the physical components on the PCB, taking into account factors such as component size, heat dissipation, and signal integrity. Ensure that components are spaced appropriately and oriented correctly.
-
Route the traces: Connect the components using conductive traces. Most PCB design software includes autorouting features that can automatically generate trace routes based on your schematic. However, it’s important to review and optimize these routes manually to ensure optimal signal integrity and manufacturability.
-
Add copper pours: Fill any unused areas of the PCB with copper pours, which are large areas of copper connected to a specific net, usually ground. Copper pours help improve signal integrity, reduce electromagnetic interference (EMI), and dissipate heat.
-
Define the solder mask and silkscreen: Specify the areas of the PCB that will be covered by solder mask (a protective coating that prevents accidental soldering) and silkscreen (text and symbols printed on the PCB for component identification and assembly instructions).
-
Perform design rule checks (DRC): Use your PCB design software’s built-in DRC tools to verify that your layout meets the manufacturing requirements, such as minimum trace width, clearance between components, and drill hole sizes.
Generating Manufacturing Files
Once your PCB layout is complete and has passed the necessary design rule checks, you can generate the manufacturing files required to produce your custom PCB. The most common manufacturing files include:
-
Gerber files: These are the primary files used by PCB manufacturers to produce the physical PCB. They contain information about the copper layers, solder mask, silkscreen, and drill holes.
-
Drill files: These files specify the location, size, and type of drill holes required for through-hole components and vias.
-
Bill of Materials (BOM): This is a list of all the components used in your PCB, including their part numbers, quantities, and suppliers. The BOM is essential for sourcing components and assembling the final product.
-
Assembly drawings: These drawings provide visual instructions for assembling the PCB, including component placement and orientation.
Most PCB design software can generate these files automatically based on your schematic and layout. However, it’s important to review the files carefully to ensure they are complete and accurate before submitting them to a PCB manufacturer.
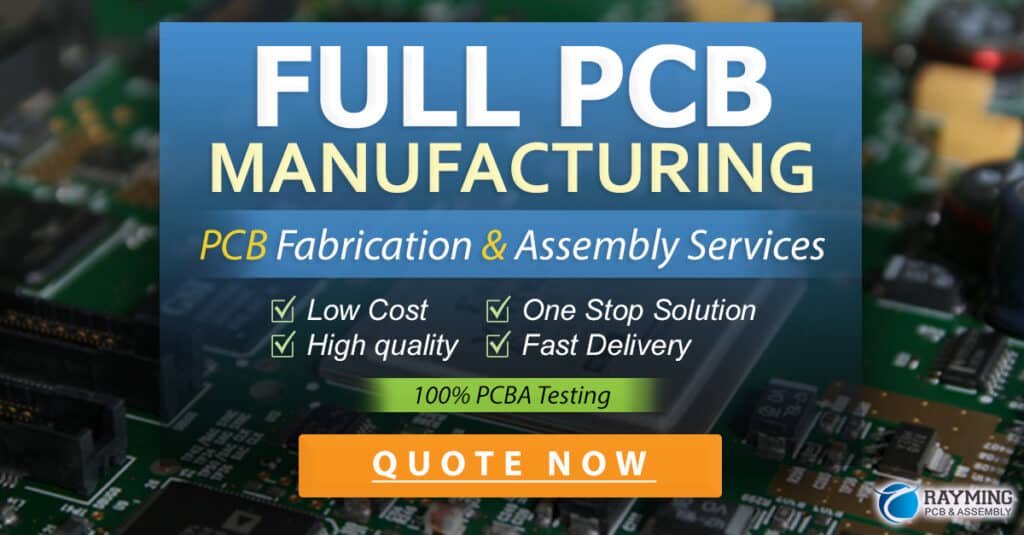
Manufacturing Your Custom PCB
Choosing a PCB Manufacturer
With your manufacturing files in hand, you can now select a PCB manufacturer to produce your custom PCB. There are numerous PCB manufacturers available, each with its own capabilities, pricing, and turnaround times. When choosing a manufacturer, consider the following factors:
-
Manufacturing capabilities: Ensure that the manufacturer can produce PCBs with the specifications you require, such as the number of layers, minimum trace width, and hole sizes.
-
Quality control: Look for manufacturers with strict quality control processes and certifications, such as ISO 9001 or UL listing, to ensure your PCBs meet industry standards.
-
Pricing: Compare prices from multiple manufacturers to find the best value for your project. Keep in mind that lower prices may sometimes come at the cost of quality or longer turnaround times.
-
Turnaround time: Consider the manufacturer’s lead time and whether it meets your project deadlines. Some manufacturers offer expedited services for an additional fee.
-
Customer support: Choose a manufacturer with responsive and helpful customer support, as you may need assistance with design reviews, file preparation, or troubleshooting.
PCB Manufacturing Process
The PCB manufacturing process typically involves the following steps:
-
Pre-production review: The manufacturer reviews your design files to ensure they meet their production requirements and suggests any necessary changes.
-
Copper etching: The conductive traces are etched onto the PCB substrate using a photolithographic process.
-
Lamination: For multi-layer PCBs, the individual layers are laminated together using heat and pressure.
-
Drilling: Holes are drilled through the PCB for through-hole components and vias.
-
Plating: The drilled holes are plated with copper to create electrical connections between layers.
-
Solder mask and silkscreen application: The solder mask and silkscreen are applied to the PCB according to your design specifications.
-
Surface finish: A surface finish, such as HASL (Hot Air Solder Leveling) or ENIG (Electroless Nickel Immersion Gold), is applied to the exposed copper to prevent oxidation and improve solderability.
-
Electrical testing: The PCB is tested for continuity and short circuits to ensure it functions as intended.
-
Cutting and routing: The individual PCBs are cut and routed from the larger production panel.
-
Packaging and shipping: The finished PCBs are packaged and shipped to you or your assembly partner.
PCB Assembly
Once you receive your custom PCBs, the next step is to assemble the components onto the board. This can be done manually for small quantities or through automated assembly processes for larger production runs. The assembly process typically involves the following steps:
-
Solder paste application: Solder paste, a mixture of tiny solder particles and flux, is applied to the PCB’s solder pads using a stencil or syringe.
-
Component placement: The components are placed onto the PCB, either manually or using automated pick-and-place machines. The components are held in place by the solder paste.
-
Reflow soldering: The PCB is heated in a reflow oven, causing the solder paste to melt and form electrical and mechanical connections between the components and the PCB.
-
Inspection: The assembled PCB is visually inspected for any defects, such as misaligned components, solder bridges, or insufficient solder joints.
-
Testing: The assembled PCB undergoes functional testing to ensure it performs as intended. This may involve using test jigs, automated test equipment, or manual testing procedures.
Best Practices for Custom PCB Design and Manufacturing
To ensure the success of your custom PCB project, follow these best practices:
-
Start with a clear specification: Define your PCB’s requirements, such as the number of layers, component types, and performance criteria, before starting the design process.
-
Use a modular design approach: Break your circuit into smaller, functional modules to simplify the design process and improve maintainability.
-
Follow design for manufacturability (DFM) guidelines: Adhere to your chosen manufacturer’s DFM guidelines to ensure your PCB can be produced efficiently and reliably.
-
Use standard component packages: Whenever possible, use standard component packages, such as through-hole or surface mount, to minimize manufacturing costs and lead times.
-
Plan for testing and debugging: Include test points, debug headers, and other features that facilitate testing and debugging of your assembled PCB.
-
Document your design: Maintain clear and comprehensive documentation of your schematic, layout, and assembly instructions to aid in future modifications or troubleshooting.
-
Work closely with your manufacturer: Communicate regularly with your PCB manufacturer and assembly partner to ensure your design meets their requirements and to resolve any issues that may arise.
-
Allow for multiple iterations: Budget time and resources for multiple design iterations, as it’s common to encounter unforeseen challenges or opportunities for improvement during the development process.
Frequently Asked Questions (FAQ)
-
What is the difference between a custom PCB and a generic PCB?
A custom PCB is designed and manufactured to meet specific requirements for a particular project or application, while a generic PCB is a pre-designed, off-the-shelf board that may not fully meet the needs of a specific project. -
How much does it cost to design and manufacture a custom PCB?
The cost of designing and manufacturing a custom PCB varies depending on factors such as the size, complexity, number of layers, and quantity of the PCBs. Simple, single-sided PCBs can cost a few dollars each, while complex, multi-layer PCBs can cost hundreds of dollars per board. -
What are the advantages of using a custom PCB over a generic PCB?
Custom PCBs offer several advantages over generic PCBs, including: - Tailored functionality to meet specific project requirements
- Optimized layout for improved performance and reliability
- Reduced size and weight compared to generic PCBs
-
Improved integration with other components and systems
-
How long does it take to design and manufacture a custom PCB?
The time required to design and manufacture a custom PCB depends on the complexity of the design and the chosen manufacturer’s lead times. Simple designs can be completed in a few days, while more complex projects may take several weeks or months. -
What skills are required to design a custom PCB?
Designing a custom PCB requires knowledge of electronic circuits, PCB layout principles, and proficiency with PCB design software. Familiarity with manufacturing processes and design for manufacturability (DFM) guidelines is also beneficial.
Conclusion
Designing and manufacturing a custom PCB can be a complex process, but with the right knowledge, tools, and partners, it’s a rewarding and essential skill for anyone working in electronics. By following the steps and best practices outlined in this guide, you’ll be well-equipped to create high-quality, custom PCBs that meet your project’s specific needs.
Remember to start with a clear specification, use a modular design approach, and adhere to design for manufacturability guidelines to ensure the success of your custom PCB project. Work closely with your chosen PCB manufacturer and assembly partner, and allow for multiple design iterations to refine and optimize your PCB.
As you gain experience with custom PCB design and manufacturing, you’ll develop a deeper understanding of the process and be able to tackle increasingly complex projects with confidence. With custom PCBs, the possibilities for innovation and creativity in electronics are nearly endless.
No responses yet