What is BGA PCB Assembly?
BGA (Ball Grid Array) PCB (Printed Circuit Board) assembly is a process of attaching electronic components, particularly BGA packages, onto a printed circuit board. BGA packages are surface-mount devices that utilize an array of solder balls on the bottom side of the package to provide electrical connections to the PCB. This packaging technology allows for higher pin counts, better thermal and electrical performance, and smaller package sizes compared to traditional through-hole and surface-mount packages.
BGA PCB assembly requires specialized equipment and expertise due to the complexity of the process and the precision required for proper alignment and soldering of the BGA packages. The assembly process typically involves the following steps:
-
Solder Paste Application: Solder paste, a mixture of tiny solder particles and flux, is precisely applied to the PCB pads using a stencil or screen printing process.
-
Component Placement: BGA packages and other surface-mount components are placed onto the PCB using high-precision pick-and-place machines. The machines use vision systems to ensure accurate alignment of the components with the solder paste deposits.
-
Reflow Soldering: The populated PCB is then subjected to a controlled heating process called reflow soldering. The PCB passes through a reflow oven, where the solder paste melts and forms secure electrical and mechanical connections between the components and the PCB pads.
-
Inspection and Testing: After the reflow process, the assembled PCB undergoes visual inspection and various testing procedures to ensure the quality and functionality of the board. This may include automated optical inspection (AOI), X-ray inspection, in-circuit testing (ICT), and functional testing.
Advantages of BGA PCB Assembly
BGA PCB assembly offers several advantages over traditional through-hole and surface-mount assembly methods:
-
Higher Pin Density: BGA packages allow for a higher number of interconnections in a smaller package size, enabling the design of more complex and compact electronic devices.
-
Improved Thermal Performance: The array of solder balls on the bottom of BGA packages provides a larger surface area for heat dissipation, resulting in better thermal performance compared to other package types.
-
Enhanced Electrical Performance: BGA packages offer shorter lead lengths and lower inductance, which can improve signal integrity and reduce electromagnetic interference (EMI).
-
Space Savings: The compact size of BGA packages allows for higher component density on the PCB, resulting in smaller overall board sizes and more efficient use of space in electronic devices.
-
Increased Reliability: When properly assembled, BGA connections provide a robust and reliable connection between the package and the PCB, minimizing the risk of connection failures.
Challenges in BGA PCB Assembly
Despite its advantages, BGA PCB assembly also presents some challenges that must be addressed to ensure successful and reliable assembly:
-
Precision Alignment: Due to the small size and tight spacing of BGA solder balls, precise alignment between the package and the PCB pads is critical. Misalignment can lead to open or short circuits, compromising the reliability of the assembly.
-
Thermal Management: The high pin density of BGA packages can result in increased heat generation, which must be effectively dissipated to prevent thermal-related failures. Proper PCB design, including the use of thermal vias and heat spreaders, is essential for managing heat in BGA assemblies.
-
Inspection and Rework: The hidden nature of BGA solder joints underneath the package makes visual inspection difficult. Specialized inspection techniques, such as X-ray imaging, are often required to verify the quality of BGA connections. Reworking defective BGA assemblies can also be challenging and may require specialized equipment and skilled technicians.
-
Moisture Sensitivity: Many BGA packages are moisture-sensitive devices (MSDs) and can absorb moisture from the environment. If not properly handled and stored, the absorbed moisture can expand during the reflow process, causing package cracking or delamination. Proper MSD handling procedures, including baking and dry storage, must be followed to mitigate these risks.
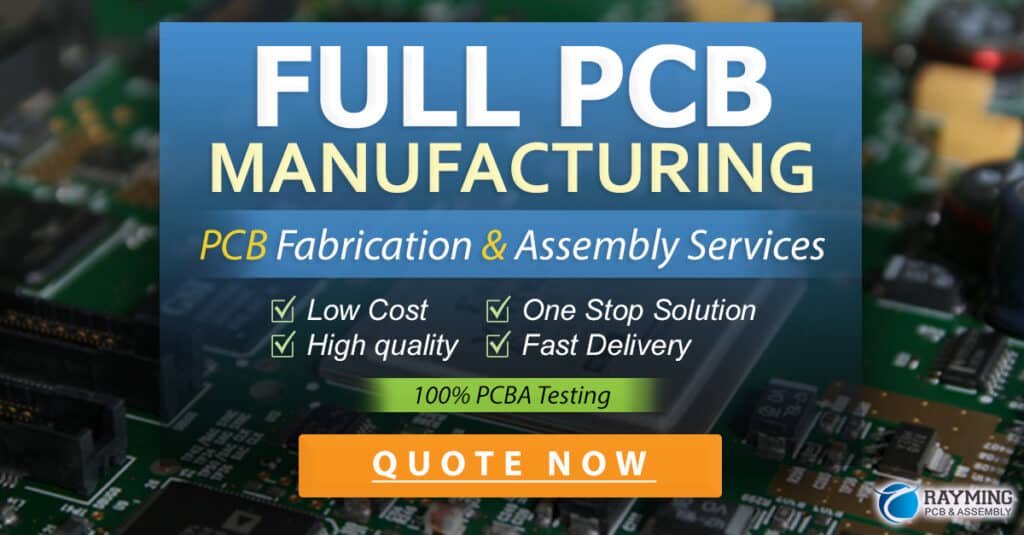
BGA PCB Design Considerations
To ensure successful BGA PCB assembly, several design considerations must be taken into account:
-
Pad Design: The PCB pad layout for BGA packages must match the solder ball array on the package. Proper pad size, shape, and spacing are crucial for reliable solder joint formation. The PCB design should also include solder mask-defined (SMD) or non-solder mask-defined (NSMD) pads, depending on the specific requirements of the BGA package.
-
Routing and Via Placement: The high pin density of BGA packages often requires the use of fine-pitch traces and microvias for routing signals from the BGA pads to other layers of the PCB. Careful consideration must be given to trace width, spacing, and via placement to ensure signal integrity and manufacturability.
-
Thermal Management: As mentioned earlier, thermal management is critical in BGA PCB design. The use of thermal vias, heat spreaders, and other thermal management techniques can help dissipate heat away from the BGA package and prevent thermal-related failures.
-
Stackup and Material Selection: The PCB stackup and material selection play a significant role in the performance and reliability of BGA assemblies. The stackup should be designed to provide adequate signal integrity, impedance control, and thermal dissipation. High-performance PCB materials, such as low-loss and high-Tg laminates, may be required for demanding BGA applications.
-
Design for Manufacturing (DFM): Designing the PCB with manufacturing considerations in mind can help ensure successful BGA assembly. This includes providing adequate clearances, avoiding unnecessary complexity, and following recommended design rules for BGA packages and PCB fabrication processes.
BGA PCB Assembly Process Flow
The BGA PCB assembly process typically follows these steps:
-
PCB Fabrication: The PCB is manufactured according to the design specifications, including the BGA pad layout, routing, and stackup.
-
Solder Paste Printing: Solder paste is applied to the PCB pads using a stencil or screen printing process. The stencil apertures are designed to match the size and shape of the BGA pads.
-
BGA Package Placement: The BGA packages are placed onto the solder paste deposits using high-precision pick-and-place machines. Vision systems ensure accurate alignment between the package solder balls and the PCB pads.
-
Reflow Soldering: The populated PCB is subjected to a controlled heating process in a reflow oven. The solder paste melts and forms solder joints between the BGA package and the PCB pads.
-
Inspection: After reflow, the assembled PCB undergoes visual inspection and automated optical inspection (AOI) to check for any defects or misalignments.
-
X-Ray Inspection: X-ray inspection may be performed to verify the quality of the BGA solder joints, as they are hidden underneath the package.
-
Rework (if necessary): If any defects are identified during the inspection process, rework may be required. This involves removing the defective BGA package, cleaning the PCB pads, and reassembling a new package.
-
Testing: The assembled PCB is subjected to various testing procedures, such as in-circuit testing (ICT) and functional testing, to ensure proper functionality and performance.
-
Conformal Coating (optional): Depending on the application and environmental requirements, a conformal coating may be applied to the PCB to provide additional protection against moisture, dust, and other contaminants.
-
Final Inspection and Packaging: The completed BGA PCB assembly undergoes a final visual inspection and is packaged for shipment to the customer.
BGA Rework and Repair
Despite careful design and assembly processes, BGA PCB assemblies may sometimes require rework or repair due to manufacturing defects or field failures. BGA rework and repair can be challenging due to the hidden nature of the solder joints and the risk of damaging the PCB or surrounding components. The following techniques are commonly used for BGA rework and repair:
-
Hot Air Rework: A focused hot air nozzle is used to heat the BGA package and melt the solder joints, allowing for the removal of the defective package. A new package is then aligned and soldered onto the PCB using the same hot air process.
-
Infrared Rework: An infrared heating system is used to heat the BGA package and PCB area, melting the solder joints. The defective package is removed, and a new package is aligned and soldered in its place.
-
Soldering Iron Rework: For smaller BGA packages or individual solder joint repairs, a fine-tipped soldering iron may be used to carefully reflow and repair the solder joints. This method requires a high level of skill and precision to avoid damaging the PCB or surrounding components.
-
Reballing: In some cases, the solder balls on the BGA package may be damaged or require replacement. Reballing involves removing the old solder balls, cleaning the package pads, and attaching new solder balls using a specialized reballing process.
Successful BGA rework and repair require specialized equipment, skilled technicians, and adherence to established procedures to minimize the risk of further damage to the PCB assembly.
Quality Control in BGA PCB Assembly
Ensuring the quality of BGA PCB assemblies is critical for the reliability and performance of the final product. Several quality control measures are implemented throughout the assembly process:
-
Incoming Material Inspection: All incoming materials, including PCBs, BGA packages, and other components, are inspected to ensure they meet the required specifications and are free from defects.
-
Process Control: The assembly process parameters, such as solder paste printing, component placement, and reflow soldering, are carefully monitored and controlled to maintain consistency and minimize process variations.
-
Automated Optical Inspection (AOI): AOI systems are used to automatically inspect the assembled PCB for defects such as missing or misaligned components, solder bridging, and insufficient solder joints.
-
X-Ray Inspection: X-ray inspection is used to verify the quality of the BGA solder joints, which are hidden underneath the package. This non-destructive testing method allows for the detection of voids, cracks, and other internal defects.
-
Electrical Testing: In-circuit testing (ICT) and functional testing are performed to verify the electrical functionality and performance of the assembled PCB.
-
Environmental Testing: Depending on the application requirements, environmental testing, such as thermal cycling, vibration, and humidity testing, may be conducted to ensure the reliability of the BGA PCB assembly under various operating conditions.
-
Traceability: Traceability systems are implemented to track the materials, processes, and test results throughout the assembly process. This allows for quick identification and resolution of any quality issues that may arise.
By implementing comprehensive quality control measures, BGA PCB assembly service providers can deliver high-quality and reliable assemblies that meet the demanding requirements of modern electronic devices.
Choosing a BGA PCB Assembly Service Provider
Selecting the right BGA PCB assembly service provider is crucial for the success of your project. Consider the following factors when choosing a provider:
-
Experience and Expertise: Look for a provider with extensive experience in BGA PCB assembly and a proven track record of successfully delivering complex projects.
-
Technical Capabilities: Ensure that the provider has the necessary equipment, processes, and expertise to handle your specific BGA PCB assembly requirements, including the ability to work with fine-pitch BGA packages and high-density PCB designs.
-
Quality Management System: Choose a provider with a robust quality management system, preferably certified to industry standards such as ISO 9001, to ensure consistent and reliable assembly quality.
-
Production Capacity: Consider the provider’s production capacity and lead times to ensure they can meet your volume requirements and delivery schedules.
-
Design Support: A provider that offers design support services, such as DFM analysis and PCB layout optimization, can help ensure the manufacturability and reliability of your BGA PCB design.
-
Certifications and Standards: Depending on your industry and application requirements, look for a provider that holds relevant certifications, such as IPC-A-610 for electronics assembly quality, IPC J-STD-001 for soldering, and UL listing for safety.
-
Cost and Value: While cost is an important consideration, it should not be the sole deciding factor. Evaluate the overall value proposition of the provider, including their quality, reliability, support, and value-added services.
-
Communication and Support: Good communication and responsive support are essential for a successful partnership. Choose a provider that is proactive in communication, responsive to your inquiries, and offers comprehensive technical support throughout the project.
By carefully evaluating these factors and selecting a reputable BGA PCB assembly service provider, you can ensure the successful realization of your electronic product with reliable and high-quality BGA PCB assemblies.
Frequently Asked Questions (FAQ)
-
What is the difference between BGA and other surface-mount packages?
BGA (Ball Grid Array) packages differ from other surface-mount packages, such as QFP (Quad Flat Pack) and SOP (Small Outline Package), in their interconnection method. BGA packages utilize an array of solder balls on the bottom side of the package to provide electrical connections to the PCB, while other surface-mount packages use leads or pins along the edges of the package. -
Can BGA packages be assembled using conventional surface-mount assembly processes?
BGA packages require specialized assembly processes and equipment due to the unique characteristics of the solder ball interconnections. While some of the process steps, such as solder paste printing and reflow soldering, are similar to conventional surface-mount assembly, BGA assembly requires higher precision in alignment, placement, and inspection. -
What are the common challenges faced in BGA PCB assembly?
Some of the common challenges in BGA PCB assembly include precision alignment of the package to the PCB pads, managing thermal dissipation, inspecting and reworking hidden solder joints, and handling moisture-sensitive BGA packages. These challenges require specialized equipment, processes, and expertise to overcome. -
How can I ensure the reliability of my BGA PCB assembly?
To ensure the reliability of your BGA PCB assembly, consider the following: - Design the PCB with BGA-specific considerations, such as pad layout, routing, and thermal management.
- Choose a reputable BGA PCB assembly service provider with experience and expertise in BGA assembly.
- Implement comprehensive quality control measures throughout the assembly process, including inspection, testing, and traceability.
- Follow proper handling and storage procedures for moisture-sensitive BGA packages.
-
Conduct appropriate environmental testing to validate the reliability of the assembly under the expected operating conditions.
-
What should I look for when selecting a BGA PCB assembly service provider?
When selecting a BGA PCB assembly service provider, consider factors such as their experience and expertise in BGA assembly, technical capabilities, quality management system, production capacity, design support services, certifications and standards compliance, cost and value proposition, and communication and support. Evaluating these factors holistically will help you choose a provider that can deliver high-quality and reliable BGA PCB assemblies for your specific requirements.
By understanding the complexities, challenges, and best practices associated with BGA PCB assembly, you can make informed decisions in designing, manufacturing, and sourcing BGA PCB assemblies for your electronic products. Partnering with a reputable and experienced BGA PCB assembly service provider is key to ensuring the success and reliability of your BGA-based electronic devices.
No responses yet