Introduction to PCBs and Their Importance in Modern Electronics
Printed Circuit Boards (PCBs) are the backbone of modern electronics, providing a reliable and efficient means of connecting electronic components in a wide range of applications. PCBs are used in everything from simple consumer devices to complex industrial equipment, and their design and manufacturing process have evolved significantly over the years to meet the increasing demands of the electronics industry.
One of the key factors in PCB design is the thickness of the copper traces used to connect components. Standard PCBs typically use copper traces with a thickness of 1-2 oz/ft², which is sufficient for most applications. However, in certain situations, such as high-power electronics or applications requiring enhanced thermal management, Thick Copper PCBs with copper traces of 3 oz/ft² or more are preferred.
In this article, we will explore the differences between standard PCBs and thick copper PCBs, their respective advantages and disadvantages, and the applications where thick copper PCBs are most commonly used.
What is a Thick Copper PCB?
A thick copper PCB is a printed circuit board that uses copper traces with a thickness greater than the standard 1-2 oz/ft². Typically, thick copper PCBs have copper traces ranging from 3 oz/ft² to 20 oz/ft² or more. The increased copper thickness provides several benefits, including:
- Enhanced current-carrying capacity
- Improved thermal management
- Increased mechanical strength
- Reduced resistance and voltage drop
Thick copper PCBs are manufactured using a process similar to that of standard PCBs, with the main difference being the additional copper plating step to achieve the desired thickness. This process involves electroplating additional copper onto the base copper layer until the required thickness is reached.
Advantages of Thick Copper PCBs
1. Higher Current-Carrying Capacity
One of the primary advantages of thick copper PCBs is their increased current-carrying capacity. With thicker copper traces, these PCBs can handle higher currents without experiencing excessive heating or voltage drop. This makes them ideal for high-power applications, such as power electronics, motor drives, and renewable energy systems.
2. Enhanced Thermal Management
Thick copper PCBs also offer improved thermal management compared to standard PCBs. The increased copper thickness allows for better heat dissipation, reducing the risk of thermal-related failures and improving the overall reliability of the electronic device. This is particularly important in applications where high power density or high ambient temperatures are present.
3. Increased Mechanical Strength
The additional copper thickness in thick copper PCBs also provides increased mechanical strength. This makes them more resilient to physical stress and vibration, which is essential in applications such as automotive electronics, aerospace systems, and industrial equipment.
4. Reduced Resistance and Voltage Drop
Thicker copper traces also result in reduced resistance and voltage drop across the PCB. This is because the increased cross-sectional area of the traces allows for more efficient current flow. Reduced voltage drop is particularly important in applications where power efficiency is critical, such as battery-powered devices or energy-harvesting systems.
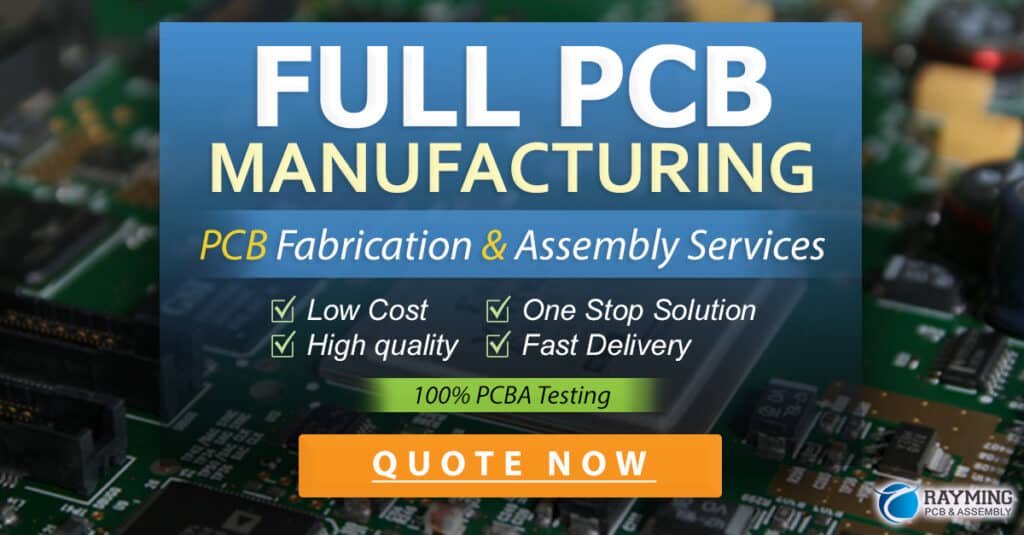
Disadvantages of Thick Copper PCBs
Despite their numerous advantages, thick copper PCBs also have some disadvantages compared to standard PCBs:
1. Higher Manufacturing Cost
The additional copper plating step required to produce thick copper PCBs increases the manufacturing cost compared to standard PCBs. This cost increase is due to the extra materials, processing time, and equipment required.
2. Increased Weight
Thick copper PCBs are heavier than standard PCBs due to the additional copper used. This can be a disadvantage in applications where weight is a critical factor, such as in aerospace or portable electronics.
3. Limited Flexibility in Design
The increased copper thickness can also limit the flexibility in PCB design. Thicker copper traces may require wider spacing and larger vias, which can affect the overall layout and routing of the PCB. This can be particularly challenging in high-density designs or applications with limited space.
Applications of Thick Copper PCBs
Thick copper PCBs are used in a wide range of applications where their unique properties are advantageous. Some of the most common applications include:
1. Power Electronics
Power electronics, such as switch-mode power supplies, inverters, and motor drives, often require thick copper PCBs to handle the high currents and power levels involved. The enhanced current-carrying capacity and improved thermal management of thick copper PCBs make them well-suited for these applications.
2. Automotive Electronics
Automotive electronics, particularly in electric and hybrid vehicles, rely on thick copper PCBs for their high-power requirements and harsh operating environments. Thick copper PCBs provide the necessary mechanical strength and thermal management to ensure reliable operation in these demanding conditions.
3. Renewable Energy Systems
Renewable energy systems, such as solar inverters and wind turbine controllers, often employ thick copper PCBs to handle the high currents generated by these systems. The improved efficiency and reduced voltage drop of thick copper PCBs help maximize the overall performance and reliability of these systems.
4. Industrial Equipment
Industrial equipment, such as motor drives, power distribution systems, and process control devices, often require thick copper PCBs to handle the high power levels and harsh environmental conditions encountered in these applications. The increased mechanical strength and thermal management capabilities of thick copper PCBs make them ideal for these demanding environments.
Comparison Table: Standard PCB vs. Thick Copper PCB
Feature | Standard PCB | Thick Copper PCB |
---|---|---|
Copper Thickness | 1-2 oz/ft² | 3-20 oz/ft² or more |
Current-Carrying Capacity | Standard | High |
Thermal Management | Standard | Enhanced |
Mechanical Strength | Standard | Increased |
Resistance and Voltage Drop | Standard | Reduced |
Manufacturing Cost | Standard | Higher |
Weight | Standard | Increased |
Design Flexibility | Standard | Limited |
Frequently Asked Questions (FAQ)
1. What is the difference between standard PCBs and thick copper PCBs?
The main difference between standard PCBs and thick copper PCBs is the thickness of the copper traces used. Standard PCBs typically use 1-2 oz/ft² copper, while thick copper PCBs use 3 oz/ft² or more.
2. What are the advantages of using thick copper PCBs?
Thick copper PCBs offer several advantages, including higher current-carrying capacity, enhanced thermal management, increased mechanical strength, and reduced resistance and voltage drop.
3. In what applications are thick copper PCBs commonly used?
Thick copper PCBs are commonly used in power electronics, automotive electronics, renewable energy systems, and industrial equipment, where high power levels, harsh environments, and demanding operating conditions are encountered.
4. Are thick copper PCBs more expensive than standard PCBs?
Yes, thick copper PCBs are generally more expensive than standard PCBs due to the additional copper plating step required in their manufacturing process.
5. Can thick copper PCBs be used in all applications?
While thick copper PCBs offer several advantages, they may not be suitable for all applications. The increased weight and limited design flexibility of thick copper PCBs can be disadvantageous in certain situations, such as in aerospace or portable electronics, where weight and space are critical factors.
Conclusion
Thick copper PCBs offer a range of advantages over standard PCBs, including enhanced current-carrying capacity, improved thermal management, increased mechanical strength, and reduced resistance and voltage drop. These properties make them ideal for applications that demand high power levels, harsh operating environments, and reliable performance.
However, the benefits of thick copper PCBs come at the cost of increased manufacturing complexity and expense, as well as potential limitations in design flexibility and weight. As such, the choice between standard PCBs and thick copper PCBs depends on the specific requirements and constraints of each application.
By understanding the differences between these two types of PCBs and their respective advantages and disadvantages, engineers and designers can make informed decisions when selecting the most appropriate PCB technology for their projects. As the demand for high-power and reliable electronics continues to grow, thick copper PCBs are likely to play an increasingly important role in enabling the next generation of innovative and efficient electronic devices.
No responses yet