Understanding Time Delay in PCB Traces
Time delay, also known as propagation delay, is the time taken by a signal to travel from one point to another along a PCB trace. It is a critical parameter in high-speed PCB design because it directly affects the timing and synchronization of signals. The time delay of a signal is influenced by several factors, including the physical length of the trace, the dielectric constant of the PCB material, and the characteristic impedance of the trace.
Factors Affecting Time Delay
-
Trace Length: The physical length of the PCB trace is the primary factor that determines the time delay. As the trace length increases, the time delay also increases proportionally.
-
Dielectric Constant: The dielectric constant (Dk) of the PCB material influences the velocity of signal propagation. Materials with higher Dk values result in slower signal propagation and increased time delay.
-
Characteristic Impedance: The characteristic impedance of the trace affects the time delay by influencing the signal’s reflection and transmission properties. Matching the characteristic impedance of the trace to the source and load impedances minimizes reflections and ensures optimal signal propagation.
Calculating Trace Length from Time Delay
To calculate the trace length based on the desired time delay value, we need to consider the signal propagation velocity and the PCB material properties. The following steps outline the process of calculating trace length from time delay:
Step 1: Determine the Signal Propagation Velocity
The signal propagation velocity (v) in a PCB trace is determined by the speed of light (c) and the dielectric constant (Dk) of the PCB material. The formula for signal propagation velocity is:
v = c / √(Dk)
where:
– v is the signal propagation velocity (m/s)
– c is the speed of light (approximately 3 × 10^8 m/s)
– Dk is the dielectric constant of the PCB material
For example, if the PCB material has a Dk value of 4, the signal propagation velocity would be:
v = (3 × 10^8) / √4 = 1.5 × 10^8 m/s
Step 2: Calculate the Trace Length
Once we have the signal propagation velocity, we can calculate the trace length (L) based on the desired time delay (t) using the following formula:
L = v × t
where:
– L is the trace length (m)
– v is the signal propagation velocity (m/s)
– t is the desired time delay (s)
For instance, if we want a time delay of 1 nanosecond (1 × 10^-9 s) and the signal propagation velocity is 1.5 × 10^8 m/s, the trace length would be:
L = (1.5 × 10^8) × (1 × 10^-9) = 0.15 m = 15 cm
Trace Length Calculation Example
Let’s consider a practical example to illustrate the trace length calculation process. Suppose we have a high-speed PCB design with the following requirements:
– PCB Material: FR-4 with a Dk value of 4.5
– Desired Time Delay: 500 picoseconds (500 × 10^-12 s)
Step 1: Calculate the signal propagation velocity:
v = (3 × 10^8) / √4.5 = 1.414 × 10^8 m/s
Step 2: Calculate the trace length:
L = (1.414 × 10^8) × (500 × 10^-12) = 0.0707 m = 7.07 cm
Therefore, to achieve a time delay of 500 picoseconds, the PCB Trace Length should be approximately 7.07 cm.
Considerations for Accurate Trace Length Calculation
While the above calculations provide a basic understanding of trace length determination based on time delay, there are additional factors to consider for accurate results in real-world PCB designs:
1. Dielectric Constant Variation
The dielectric constant of PCB materials can vary depending on factors such as frequency, temperature, and manufacturing tolerances. It is important to use accurate Dk values specific to the operating conditions of the PCB. Consult the material datasheet or perform measurements to obtain precise Dk values.
2. Trace Geometry
The geometry of the PCB trace, including its width and thickness, affects the characteristic impedance and signal propagation velocity. Trace geometry should be carefully designed to maintain the desired characteristic impedance and minimize signal distortion. Use PCB design tools or impedance calculators to determine the appropriate trace dimensions.
3. Frequency-Dependent Effects
At high frequencies, PCB traces exhibit frequency-dependent effects such as skin effect and dielectric loss. These effects can impact the signal propagation velocity and cause variations in time delay. Advanced modeling techniques, such as frequency-domain analysis or full-wave simulations, may be necessary to accurately account for these effects.
4. Via and Connector Delays
In addition to trace delays, vias and connectors introduce additional time delays in the signal path. These delays should be considered and accounted for in the overall time delay budget. Consult via and connector models or perform measurements to characterize their delay contributions accurately.
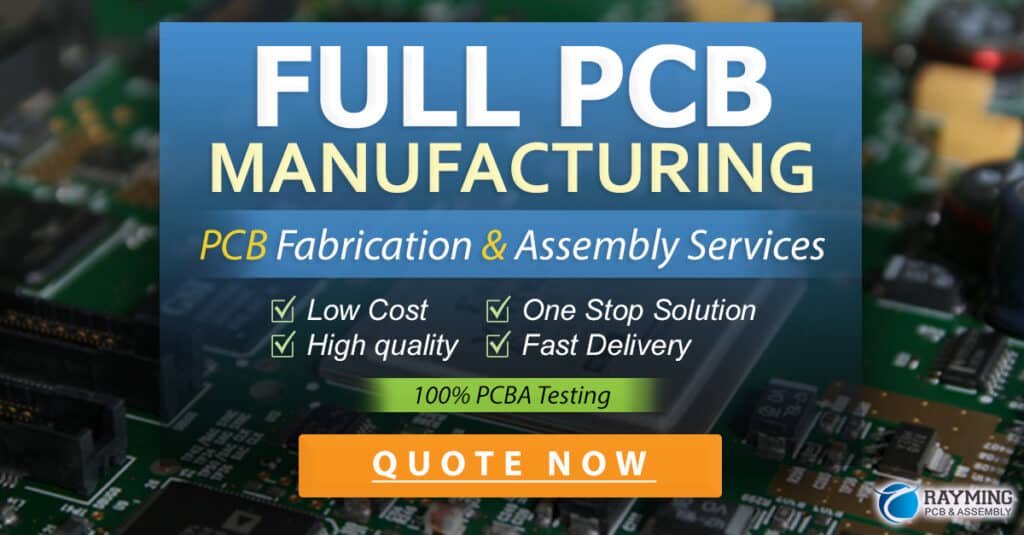
Importance of Accurate Trace Length Control
Accurate control of trace lengths is crucial in high-speed PCB design for several reasons:
-
Signal Integrity: Properly managed trace lengths ensure that signals arrive at their intended destinations with minimal distortion, reflections, and crosstalk. This is essential for maintaining signal integrity and preventing data corruption.
-
Timing and Synchronization: In synchronous systems, accurate trace lengths are necessary to maintain proper timing relationships between signals. Mismatched trace lengths can lead to timing violations, setup and hold time issues, and overall system malfunction.
-
EMI and Radiated Emissions: Uncontrolled trace lengths can act as antennas and contribute to electromagnetic interference (EMI) and radiated emissions. By carefully designing trace lengths and implementing appropriate layout techniques, designers can minimize EMI and comply with regulatory requirements.
-
Manufacturing and Assembly: Well-controlled trace lengths facilitate smoother manufacturing and assembly processes. Consistent trace lengths across different PCB layers and between components simplify the assembly process and reduce the likelihood of manufacturing defects.
Best Practices for Trace Length Management
To effectively manage trace lengths in high-speed PCB designs, consider the following best practices:
-
Define Time Delay Requirements: Clearly define the time delay requirements for critical signals in the system. Collaborate with system architects and component engineers to establish acceptable delay ranges and tolerances.
-
Use PCB Design Tools: Employ PCB design tools that offer trace length management features. These tools can automatically calculate and adjust trace lengths based on specified time delay constraints. They also provide visual aids and reports to analyze and verify trace lengths.
-
Route Signals in Groups: Route related signals, such as buses or differential pairs, in groups with matched trace lengths. This helps maintain signal integrity and minimizes timing skew between signals.
-
Minimize Trace Length Variations: Strive to minimize variations in trace lengths within a signal group. Use serpentine routing techniques or add intentional delays to match trace lengths and ensure consistent time delays.
-
Consider Layer Stack-up: Strategically place signals on appropriate layers in the PCB stack-up to control trace lengths. For example, use inner layers for longer traces and outer layers for shorter traces to optimize signal routing and minimize delay variations.
-
Perform Timing Analysis: Conduct comprehensive timing analysis to verify that the designed trace lengths meet the required time delay constraints. Use simulation tools to analyze signal propagation, timing margins, and potential issues.
-
Document and Communicate: Clearly document trace length requirements, design decisions, and analysis results. Communicate this information to all relevant stakeholders, including PCB layout designers, manufacturers, and testing teams, to ensure consistent implementation and verification.
Frequently Asked Questions (FAQ)
- What is the relationship between trace length and time delay in PCB design?
-
Trace length and time delay are directly proportional in PCB design. As the trace length increases, the time delay also increases. The time delay is determined by the signal propagation velocity, which depends on the PCB material’s dielectric constant.
-
How does the dielectric constant affect the time delay in PCB traces?
-
The dielectric constant (Dk) of the PCB material influences the signal propagation velocity. A higher Dk value results in slower signal propagation and increased time delay. Conversely, a lower Dk value leads to faster signal propagation and reduced time delay.
-
What are the consequences of improper trace length control in high-speed PCB design?
-
Improper trace length control can lead to signal integrity issues, such as signal distortion, reflections, and crosstalk. It can also cause timing and synchronization problems, resulting in system malfunctions. Additionally, uncontrolled trace lengths can contribute to EMI and radiated emissions.
-
How can PCB design tools assist in managing trace lengths?
-
PCB design tools offer trace length management features that automatically calculate and adjust trace lengths based on specified time delay constraints. They provide visual aids and reports to analyze and verify trace lengths, making it easier for designers to control and optimize trace lengths in their designs.
-
What are some best practices for managing trace lengths in high-speed PCB designs?
- Some best practices include defining clear time delay requirements, using PCB design tools with trace length management features, routing signals in groups with matched lengths, minimizing trace length variations, considering layer stack-up, performing timing analysis, and documenting and communicating trace length requirements and design decisions.
Conclusion
Calculating trace lengths from time delay values is a critical aspect of high-speed PCB design. By understanding the factors affecting time delay, such as trace length, dielectric constant, and characteristic impedance, designers can accurately determine the required trace lengths to meet specific time delay requirements. The process involves calculating the signal propagation velocity based on the PCB material’s dielectric constant and then using the desired time delay to calculate the corresponding trace length.
However, accurate trace length calculation goes beyond simple formulas. Designers must consider factors such as dielectric constant variation, trace geometry, frequency-dependent effects, and via and connector delays. Employing best practices, such as using PCB design tools, routing signals in groups, minimizing trace length variations, and performing timing analysis, helps ensure accurate trace length control and optimal signal integrity.
By carefully managing trace lengths in high-speed PCB designs, engineers can mitigate signal integrity issues, ensure proper timing and synchronization, reduce EMI and radiated emissions, and facilitate smoother manufacturing and assembly processes. Effective trace length control is a collaborative effort that involves clear communication and documentation among all stakeholders involved in the PCB design process.
As PCB designs continue to push the boundaries of speed and complexity, the importance of accurate trace length calculation and control will only increase. By staying informed about the latest techniques, tools, and best practices, PCB designers can successfully navigate the challenges of high-speed design and deliver reliable, high-performance electronic systems.
No responses yet