Introduction to PCB Return Currents
In the world of printed circuit board (PCB) design, understanding and managing return currents is crucial for ensuring the proper functioning and reliability of electronic devices. Return currents, also known as ground currents or reference currents, play a vital role in maintaining signal integrity, reducing electromagnetic interference (EMI), and preventing ground loops. This article delves into the various return current topologies used in PCB design, their advantages, disadvantages, and best practices for implementation.
What are Return Currents?
Return currents are the electrical currents that flow back to the source through a reference plane or conductor, completing the circuit. In a PCB, these currents typically flow through the ground plane, power plane, or a dedicated return path. The path taken by the return current is determined by the impedance of the available routes, following the path of least impedance.
Importance of Return Current Management
Proper management of return currents is essential for several reasons:
-
Signal Integrity: Return currents can affect the quality of signals transmitted through the PCB. Improper return paths can lead to signal distortion, crosstalk, and increased electromagnetic emissions.
-
EMI Reduction: Well-designed return current paths help minimize electromagnetic interference by containing the magnetic fields generated by the currents.
-
Ground Loops: Inadequate return current management can result in ground loops, which occur when there are multiple paths for the return current to flow. Ground loops can introduce noise and degrade signal quality.
-
Reliability: Proper return current management ensures the long-term reliability of the PCB by preventing issues such as voltage drops, thermal stress, and electromigration.
Common Return Current Topologies
There are several return current topologies commonly used in PCB design, each with its own advantages and disadvantages. Let’s explore some of the most prevalent topologies:
1. Ground Plane
A ground plane is a continuous copper layer that serves as a low-impedance return path for currents. It is the most common return current topology in multi-layer PCBs. The ground plane provides a uniform reference voltage and helps minimize the loop area between the signal trace and the return path.
Advantages:
– Low impedance return path
– Reduced EMI
– Improved signal integrity
– Simplified routing
Disadvantages:
– Increased fabrication cost due to additional copper layer
– Potential for ground bounce if not properly designed
Best Practices:
– Use a solid ground plane rather than a mesh or grid pattern
– Ensure proper grounding of components
– Minimize the distance between signal traces and the ground plane
– Use ground vias to connect ground planes on different layers
2. Power Plane
A power plane is similar to a ground plane but is used for distributing power instead of providing a return path. In some cases, a power plane can also serve as a return path for certain signals. Power planes are typically used in conjunction with ground planes to create a low-impedance power distribution network.
Advantages:
– Low impedance power distribution
– Reduced voltage drop
– Improved noise immunity
– Can serve as a return path for some signals
Disadvantages:
– Increased fabrication cost due to additional copper layer
– Potential for power supply noise if not properly decoupled
Best Practices:
– Use dedicated power planes for each voltage level
– Decouple power planes with appropriate capacitors
– Minimize the distance between power planes and ground planes
– Use power vias to connect power planes on different layers
3. Coplanar Waveguide
A coplanar waveguide (CPW) is a transmission line structure where the signal trace is accompanied by ground traces on either side, all on the same layer. The ground traces serve as the return path for the signal. CPW is commonly used for high-frequency signals and in RF circuits.
Advantages:
– Reduced EMI due to tight coupling between signal and ground traces
– Improved signal integrity for high-frequency signals
– Simplified fabrication compared to multi-layer designs
Disadvantages:
– Increased trace width compared to microstrip or stripline
– Potential for mode conversion if not properly designed
Best Practices:
– Maintain a consistent spacing between the signal trace and ground traces
– Use ground vias to connect ground traces to ground planes
– Minimize discontinuities in the ground traces
– Consider the effect of bends and corners on signal integrity
4. Microstrip
Microstrip is a transmission line structure where the signal trace is placed on the top layer of the PCB, with a ground plane on the layer beneath it. The signal trace and the ground plane form a transmission line with a characteristic impedance determined by the trace width, thickness, and dielectric constant of the substrate.
Advantages:
– Simple and cost-effective to fabricate
– Widely used and well-understood
– Suitable for a wide range of frequencies
Disadvantages:
– Higher EMI compared to stripline or CPW
– Susceptible to external noise and interference
Best Practices:
– Choose appropriate trace width and spacing to achieve the desired characteristic impedance
– Use ground vias to provide a low-impedance return path
– Avoid routing microstrip traces near board edges or gaps in the ground plane
– Consider the effect of dielectric thickness and constant on signal propagation
5. Stripline
Stripline is a transmission line structure where the signal trace is sandwiched between two ground planes. The signal trace is typically placed on an inner layer of the PCB, with ground planes above and below it. Stripline provides excellent shielding and isolation from external noise and interference.
Advantages:
– Reduced EMI due to shielding by ground planes
– Improved signal integrity compared to microstrip
– Suitable for high-frequency and high-speed signals
Disadvantages:
– Increased fabrication cost due to additional layers
– Requires careful design to maintain characteristic impedance
– Limited access to signal trace for probing or debugging
Best Practices:
– Choose appropriate trace width and spacing to achieve the desired characteristic impedance
– Maintain a consistent dielectric thickness between the signal trace and ground planes
– Use ground vias to connect ground planes on different layers
– Avoid routing stripline traces near edges or gaps in the ground planes
Return Current Path Design Considerations
When designing return current paths in a PCB, several factors must be considered to ensure optimal performance and reliability:
-
Impedance Control: Match the impedance of the return path to the impedance of the signal trace to prevent reflections and maintain signal integrity.
-
Electromagnetic Coupling: Minimize the loop area between the signal trace and the return path to reduce electromagnetic coupling and EMI.
-
Discontinuities: Avoid discontinuities in the return path, such as gaps or slots, which can cause signal degradation and EMI.
-
Layer Transitions: Use ground vias to provide a low-impedance return path when signals transition between layers.
-
Component Placement: Place components close to their respective return paths to minimize loop area and inductance.
-
Frequency Considerations: Choose the appropriate return current topology based on the frequency range of the signals in the PCB.
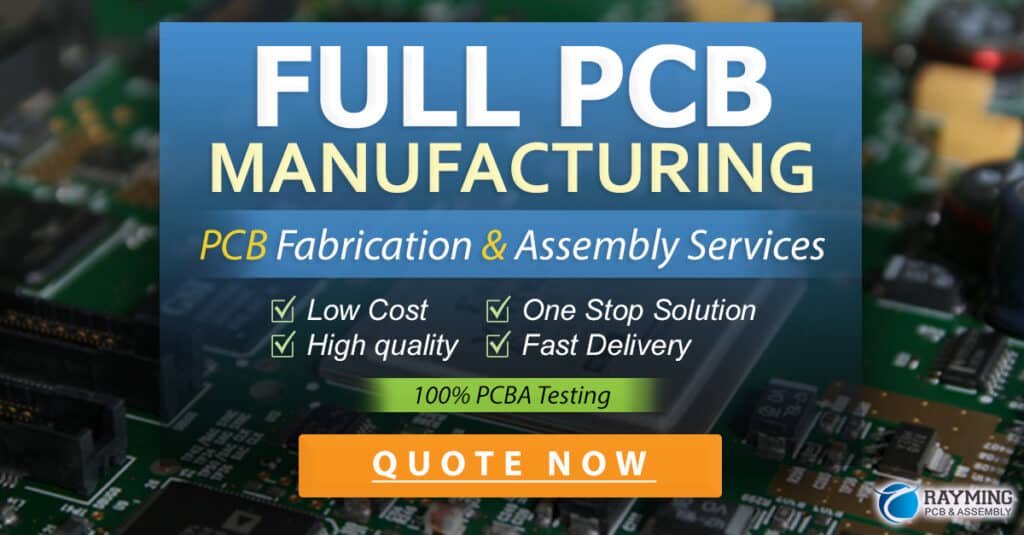
Frequently Asked Questions (FAQ)
- What is the difference between a ground plane and a power plane?
-
A ground plane is a continuous copper layer that serves as a low-impedance return path for currents, while a power plane is used for distributing power to components on the PCB. Power planes can sometimes serve as return paths for certain signals.
-
What is the purpose of a coplanar waveguide (CPW) in PCB design?
-
A coplanar waveguide is a transmission line structure where the signal trace is accompanied by ground traces on either side, all on the same layer. CPW is commonly used for high-frequency signals and in RF circuits due to its reduced EMI and improved signal integrity.
-
How does a microstrip differ from a stripline in terms of return current management?
-
In a microstrip, the signal trace is placed on the top layer of the PCB, with a ground plane on the layer beneath it. Stripline, on the other hand, has the signal trace sandwiched between two ground planes on inner layers of the PCB. Stripline provides better shielding and reduced EMI compared to microstrip.
-
What are the best practices for managing return currents in a multi-layer PCB?
- Use solid ground planes rather than mesh or grid patterns
- Ensure proper grounding of components
- Minimize the distance between signal traces and return paths
- Use ground vias to connect ground planes on different layers
-
Choose appropriate trace widths and spacing to maintain characteristic impedance
-
How can discontinuities in the return path affect signal integrity?
- Discontinuities in the return path, such as gaps or slots, can cause signal degradation and increased EMI. These discontinuities force the return current to find alternative paths, which can lead to signal reflections, crosstalk, and electromagnetic emissions. It is essential to maintain a continuous and low-impedance return path to minimize these effects.
Conclusion
Understanding and managing return currents is a critical aspect of PCB design. By selecting the appropriate return current topology and following best practices for implementation, designers can ensure signal integrity, reduce EMI, and improve the overall reliability of their PCBs. Ground planes, power planes, coplanar waveguides, microstrips, and striplines are common return current topologies, each with its own advantages and disadvantages. Designers must consider factors such as impedance control, electromagnetic coupling, discontinuities, and frequency when designing return current paths. By carefully planning and optimizing return current management, PCB designers can create robust and high-performance electronic devices.
Return Current Topology | Advantages | Disadvantages |
---|---|---|
Ground Plane | – Low impedance return path – Reduced EMI – Improved signal integrity – Simplified routing |
– Increased fabrication cost – Potential for ground bounce |
Power Plane | – Low impedance power distribution – Reduced voltage drop – Improved noise immunity – Can serve as a return path for some signals |
– Increased fabrication cost – Potential for power supply noise |
Coplanar Waveguide | – Reduced EMI – Improved signal integrity for high-frequency signals – Simplified fabrication |
– Increased trace width – Potential for mode conversion |
Microstrip | – Simple and cost-effective to fabricate – Widely used and well-understood – Suitable for a wide range of frequencies |
– Higher EMI – Susceptible to external noise and interference |
Stripline | – Reduced EMI due to shielding – Improved signal integrity – Suitable for high-frequency and high-speed signals |
– Increased fabrication cost – Requires careful design – Limited access to signal trace |
By understanding the characteristics and trade-offs of each return current topology, PCB designers can make informed decisions and optimize their designs for specific applications and requirements. Proper return current management is essential for ensuring the performance, reliability, and electromagnetic compatibility of PCBs in today’s increasingly complex and high-speed electronic systems.
No responses yet