Introduction to CMOS Sensor PCB Layout
CMOS (Complementary Metal-Oxide-Semiconductor) sensors have become increasingly popular in various applications, including digital cameras, smartphones, and industrial imaging systems. Designing a PCB (Printed Circuit Board) layout for a CMOS sensor requires careful consideration of several factors to ensure optimal performance and reliability. In this article, we will dive into the intricacies of CMOS sensor PCB layout and provide you with the knowledge and best practices to create a successful design.
Understanding CMOS Sensors
Before we delve into the PCB layout aspects, let’s briefly understand how CMOS sensors work. A CMOS sensor consists of an array of photosensitive elements, known as pixels, that convert light into electrical signals. Each pixel comprises a photodiode and a set of transistors that amplify and read out the signal. The sensor also includes control circuitry, analog-to-digital converters (ADCs), and other supporting components.
Key Considerations for CMOS Sensor PCB Layout
When designing a PCB layout for a CMOS sensor, several key considerations must be taken into account:
-
Signal Integrity: CMOS sensors deal with low-level analog signals that are susceptible to noise and interference. Ensuring signal integrity is crucial to maintain image quality and minimize distortion.
-
Power Supply: Providing a clean and stable power supply to the CMOS sensor is essential. Any noise or fluctuations in the power supply can introduce artifacts and degrade image quality.
-
Grounding: Proper grounding techniques are critical to minimize noise and ensure a stable reference for the sensor’s analog circuitry.
-
Component Placement: The placement of components on the PCB plays a significant role in signal integrity and overall performance. Careful consideration must be given to the proximity of sensitive components and potential sources of interference.
-
Routing: The routing of traces on the PCB is equally important. Proper trace widths, spacing, and shielding techniques must be employed to minimize crosstalk and electromagnetic interference (EMI).
Signal Integrity in CMOS Sensor PCB Layout
Analog Signal Routing
When routing analog signals from the CMOS sensor to the ADCs and other components, it is essential to minimize the trace length and avoid sharp turns or vias whenever possible. Long traces and discontinuities can introduce parasitic capacitance and inductance, leading to signal degradation and noise.
Consider using differential signaling for critical analog signals to improve noise immunity. Differential signals are less susceptible to common-mode noise and provide better signal integrity over longer distances.
Shielding Techniques
To minimize the impact of external electromagnetic interference (EMI) on sensitive analog signals, employ shielding techniques in your PCB layout. This can include:
- Using ground planes to provide a low-impedance return path for high-frequency currents.
- Placing sensitive traces between ground planes to create a Faraday cage effect.
- Using guard rings or guard traces around sensitive components to isolate them from noise sources.
Decoupling Capacitors
Decoupling capacitors play a crucial role in maintaining signal integrity by providing a local reservoir of charge and minimizing power supply noise. Place decoupling capacitors as close as possible to the power pins of the CMOS sensor and other sensitive components.
Use a combination of bulk decoupling capacitors (e.g., 10µF) and smaller ceramic capacitors (e.g., 0.1µF) to effectively filter out both low-frequency and high-frequency noise.
Power Supply Considerations
Power Supply Routing
When routing power supply traces to the CMOS sensor and associated components, it is important to use wide traces to minimize voltage drop and ensure a stable supply voltage. Avoid routing power traces near sensitive analog signals to prevent crosstalk and noise coupling.
Consider using separate power planes for analog and digital circuitry to minimize noise coupling between the two domains. Use ferrite beads or inductors to isolate the analog power supply from the digital power supply.
Voltage Regulation
Providing a clean and stable voltage supply to the CMOS sensor is critical for optimal performance. Use low-noise voltage regulators, such as low-dropout (LDO) regulators, to regulate the voltage supplied to the sensor.
Place the voltage regulators close to the CMOS sensor to minimize the trace length and reduce the potential for noise pickup. Use appropriate decoupling capacitors at the input and output of the voltage regulators to ensure stable operation.
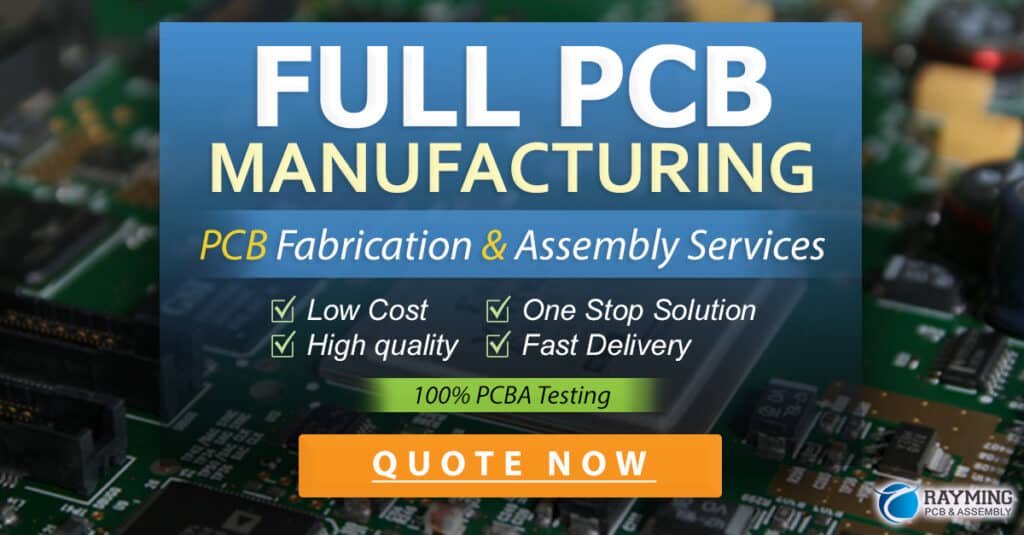
Grounding Techniques
Ground Planes
Implementing a solid ground plane is essential for providing a low-impedance return path for currents and minimizing ground loops. Use a continuous ground plane on one or more layers of the PCB, depending on the complexity of the design.
Connect the ground pins of the CMOS sensor and other components directly to the ground plane using short traces or vias. Avoid creating long ground traces or daisy-chaining ground connections, as this can introduce ground loops and degrade signal integrity.
Split Ground Planes
In some cases, it may be beneficial to use split ground planes to isolate sensitive analog circuitry from noisy digital circuitry. Use a split ground plane technique, where the analog and digital grounds are separated and connected at a single point, typically near the power supply or the ADC.
Use ferrite beads or inductors to connect the analog and digital ground planes, which helps to isolate high-frequency noise while maintaining a common reference point.
Component Placement and Routing
Component Placement
When placing components on the PCB, consider the following guidelines:
- Place the CMOS sensor as close as possible to the lens assembly to minimize the distance between the sensor and the optical path.
- Position the ADCs and other sensitive analog components close to the CMOS sensor to minimize trace lengths and reduce the potential for noise pickup.
- Keep digital components, such as microcontrollers and memory devices, away from sensitive analog circuitry to minimize digital noise coupling.
- Consider the placement of connectors and other interfaces to ensure easy access and minimize signal path lengths.
Routing Considerations
When routing traces on the PCB, adhere to the following best practices:
- Use appropriate trace widths based on the current requirements and signal frequencies. Wider traces are generally used for power supply and high-current signals, while narrower traces are used for low-current and high-speed signals.
- Maintain adequate spacing between traces to minimize crosstalk and interference. Follow the recommended spacing guidelines provided by the PCB manufacturer or design tools.
- Avoid running sensitive analog traces parallel to noisy digital traces or power supply traces. If parallel routing is unavoidable, ensure sufficient spacing or use guard traces to minimize crosstalk.
- Use vias strategically to transition between layers and minimize trace lengths. However, be cautious when using vias for sensitive analog signals, as vias can introduce discontinuities and affect signal integrity.
Electromagnetic Compatibility (EMC)
EMI Reduction Techniques
To minimize electromagnetic interference (EMI) in your CMOS sensor PCB layout, consider the following techniques:
- Use proper grounding and shielding techniques, as discussed earlier, to reduce the emission and susceptibility of EMI.
- Implement filters, such as low-pass filters or ferrite beads, on power supply lines and sensitive signal lines to suppress high-frequency noise.
- Use balanced or differential signaling for critical signals to cancel out common-mode noise and reduce EMI.
- Minimize the use of high-speed clock signals and ensure proper termination to reduce the generation of EMI.
Regulatory Compliance
Ensure that your CMOS sensor PCB design complies with relevant EMC regulations and standards, such as FCC (Federal Communications Commission) rules in the United States or CE (Conformité Européenne) marking in Europe.
Conduct EMC testing to verify that your design meets the required emission and immunity limits. Take necessary measures to mitigate any identified EMC issues, such as adding additional shielding or filtering components.
Thermal Management
Heat Dissipation
CMOS sensors and associated components generate heat during operation, which can affect performance and reliability if not properly managed. Consider the following thermal management techniques:
- Use a thermally conductive PCB substrate, such as metal-core PCBs or PCBs with thermal vias, to enhance heat dissipation.
- Place thermal pads or heat sinks on heat-generating components, such as voltage regulators or high-speed processors, to facilitate heat transfer away from the components.
- Provide adequate airflow or use fans to promote convective cooling and prevent heat buildup within the enclosure.
Thermal Noise Considerations
Thermal noise can impact the performance of CMOS sensors, particularly in low-light conditions. To minimize the impact of thermal noise:
- Use low-noise components, such as Low-noise Amplifiers and voltage regulators, to reduce the overall noise floor.
- Implement noise reduction techniques, such as correlated double sampling (CDS) or digital noise reduction algorithms, to mitigate the effects of thermal noise.
- Consider the use of cooling techniques, such as thermoelectric cooling (TEC) or liquid cooling, for high-performance applications that require extreme low-noise performance.
Testing and Validation
Prototype Testing
Once your CMOS sensor PCB layout is complete, it is crucial to thoroughly test and validate the design before moving to mass production. Fabricate prototype boards and perform comprehensive testing to ensure proper functionality and performance.
Conduct signal integrity tests, power supply measurements, and noise analysis to verify that the design meets the required specifications. Use oscilloscopes, spectrum analyzers, and other test equipment to capture and analyze signals at critical points in the design.
Hardware and Software Integration
Integrate the CMOS sensor PCB with the rest of the system, including the lens assembly, image processing hardware, and software components. Verify that the sensor communicates correctly with the image processing pipeline and that the captured images meet the desired quality and performance criteria.
Test the system under various operating conditions, such as different lighting scenarios, temperature ranges, and power supply variations, to ensure robustness and reliability.
Continuous Improvement
Based on the results of prototype testing and system integration, identify any areas for improvement in the PCB layout or component selection. Make necessary adjustments and iterate the design to optimize performance, signal integrity, and noise reduction.
Document the lessons learned and best practices developed during the design process to facilitate future CMOS sensor PCB layouts and streamline the development cycle.
FAQs
-
Q: What are the key considerations when choosing components for a CMOS sensor PCB layout?
A: When selecting components for a CMOS sensor PCB layout, consider factors such as noise performance, power consumption, compatibility with the sensor, and thermal characteristics. Choose low-noise components, such as amplifiers and voltage regulators, to minimize noise interference. Ensure that the selected components can handle the required power demands and are compatible with the sensor’s specifications. Additionally, consider the thermal properties of the components and select packages that facilitate heat dissipation. -
Q: How can I minimize crosstalk between analog and digital signals in a CMOS sensor PCB layout?
A: To minimize crosstalk between analog and digital signals, employ proper routing techniques and component placement. Separate analog and digital circuitry into distinct regions on the PCB, and use separate ground planes for each domain. Route sensitive analog traces away from noisy digital traces and power supply lines. Use guard traces or shielding techniques to isolate sensitive signals from potential sources of interference. Additionally, use appropriate decoupling capacitors and filtering techniques to suppress high-frequency noise and prevent crosstalk. -
Q: What are some common mistakes to avoid when designing a CMOS sensor PCB layout?
A: Some common mistakes to avoid when designing a CMOS sensor PCB layout include: - Inadequate grounding and shielding, leading to increased noise and interference.
- Improper component placement, resulting in long signal paths and increased susceptibility to noise.
- Insufficient decoupling capacitors or incorrect placement, causing power supply instability and noise.
- Routing sensitive analog traces near noisy digital traces or power supply lines, leading to crosstalk and signal degradation.
- Neglecting thermal management considerations, resulting in overheating and reduced performance.
-
Failing to comply with relevant EMC regulations and standards, leading to potential EMI issues.
-
Q: How can I ensure proper power supply stability in a CMOS sensor PCB layout?
A: To ensure proper power supply stability, use low-noise voltage regulators, such as LDO regulators, to provide a clean and stable voltage to the CMOS sensor. Place the voltage regulators close to the sensor to minimize trace lengths and reduce the potential for noise pickup. Use appropriate decoupling capacitors at the input and output of the voltage regulators to filter out noise and maintain a stable supply voltage. Implement separate power planes for analog and digital circuitry to minimize noise coupling between the domains. -
Q: What are some best practices for testing and validating a CMOS sensor PCB layout?
A: When testing and validating a CMOS sensor PCB layout, follow these best practices: - Fabricate prototype boards and perform comprehensive testing to verify functionality and performance.
- Conduct signal integrity tests, power supply measurements, and noise analysis using appropriate test equipment, such as oscilloscopes and spectrum analyzers.
- Integrate the CMOS sensor PCB with the rest of the system, including the lens assembly and image processing components, to ensure proper communication and image quality.
- Test the system under various operating conditions, such as different lighting scenarios, temperature ranges, and power supply variations, to assess robustness and reliability.
- Identify areas for improvement based on test results and iterate the design to optimize performance and noise reduction.
- Document the lessons learned and best practices developed during the design process for future reference and improvement.
Conclusion
Designing a CMOS sensor PCB layout requires careful consideration of signal integrity, power supply stability, grounding techniques, component placement, and routing. By following the best practices and guidelines discussed in this article, you can create a robust and reliable PCB layout that maximizes the performance of your CMOS sensor.
Remember to prioritize signal integrity, use appropriate shielding and grounding techniques, and pay attention to power supply and thermal management considerations. Conduct thorough testing and validation to ensure that your design meets the required specifications and performance criteria.
Continuously refine and optimize your CMOS sensor PCB layout based on the lessons learned and best practices developed during the design process. By staying up to date with the latest techniques and technologies, you can create high-quality CMOS sensor PCB layouts that deliver exceptional performance and image quality.
Aspect | Recommendations |
---|---|
Signal Integrity | – Minimize trace lengths and avoid sharp turns or vias for analog signals – Use differential signaling for critical signals – Implement shielding techniques and decoupling capacitors |
Power Supply | – Use wide traces for power routing and separate power planes for analog and digital circuitry – Employ low-noise voltage regulators and appropriate decoupling capacitors |
Grounding | – Implement a solid ground plane and connect components directly to it – Use split ground planes and ferrite beads to isolate analog and digital grounds |
Component Placement | – Place the CMOS sensor close to the lens assembly and sensitive components near the sensor – Separate analog and digital components and consider connector placement |
Routing | – Use appropriate trace widths and spacing based on current and frequency requirements – Avoid running sensitive traces parallel to noisy traces and use vias strategically |
EMC | – Implement proper grounding, shielding, and filtering techniques to reduce EMI – Ensure compliance with relevant EMC regulations and standards |
Thermal Management | – Use thermally conductive PCB substrates and thermal pads/heat sinks for heat dissipation – Consider cooling techniques and low-noise components to minimize thermal noise |
Testing and Validation | – Fabricate prototypes and perform comprehensive testing for functionality and performance – Integrate the PCB with the system and test under various operating conditions |
By following these recommendations and continuously refining your design, you can create a high-performance CMOS sensor PCB layout that delivers excellent image quality and reliability. Happy designing!
No responses yet