Introduction to PCB Heat Sinks
Printed Circuit Boards (PCBs) are essential components in modern electronic devices. They provide a platform for mounting and interconnecting electronic components, forming a complete functional circuit. However, as electronic devices become more compact and powerful, heat management becomes a critical issue. Excessive heat can lead to component failure, reduced performance, and even permanent damage to the PCB. This is where PCB heat sinks come into play.
PCB heat sinks are designed to dissipate heat away from the electronic components, ensuring that they operate within their specified temperature range. They are typically made of materials with high thermal conductivity, such as aluminum or copper, and are attached to the PCB using thermal adhesive or mechanical fasteners.
Types of PCB Heat Sinks
There are several types of PCB heat sinks available, each with its own advantages and disadvantages. The most common types include:
-
Extruded Heat Sinks: These heat sinks are manufactured by extruding aluminum through a die, creating a profile with fins or pins. They offer good thermal performance and are relatively inexpensive.
-
Stamped Heat Sinks: Stamped heat sinks are made by stamping a flat sheet of metal into a desired shape. They are lightweight and cost-effective but may not provide as much cooling capacity as extruded heat sinks.
-
Bonded Fin Heat Sinks: These heat sinks consist of a base plate with fins bonded to it. They offer excellent thermal performance but are more expensive than extruded or stamped heat sinks.
-
Forged Heat Sinks: Forged heat sinks are created by forging a block of metal into the desired shape. They are highly durable and offer good thermal performance but are more expensive than other types of heat sinks.
Factors Affecting PCB Heat Sink Performance
Several factors can affect the performance of a PCB heat sink, including:
-
Material: The material used for the heat sink plays a significant role in its thermal performance. Aluminum and copper are the most common materials used due to their high thermal conductivity.
-
Surface Area: The surface area of the heat sink determines its ability to dissipate heat. A larger surface area allows for more heat to be transferred away from the components.
-
Fin Design: The design of the fins on the heat sink can impact its cooling capacity. Fins that are too close together may restrict airflow, while fins that are too far apart may not provide enough surface area for heat dissipation.
-
Airflow: Adequate airflow is essential for effective heat dissipation. The heat sink should be positioned in a way that allows for maximum airflow around the fins.
-
Thermal Interface Material: The thermal interface material (TIM) used between the component and the heat sink can affect the thermal performance. A high-quality TIM with good thermal conductivity can improve heat transfer.
Determining if the PCB Heat Sink is Enough
To determine if the PCB heat sink is sufficient for your application, you need to consider several factors, including the power dissipation of the components, the ambient temperature, and the available space for the heat sink.
Calculating Power Dissipation
The first step in determining if the PCB heat sink is enough is to calculate the power dissipation of the components. Power dissipation is the amount of power that is converted into heat by the electronic components. It can be calculated using the following formula:
P = V × I
Where:
– P is the power dissipation in watts (W)
– V is the voltage across the component in volts (V)
– I is the current flowing through the component in amperes (A)
For example, if a component has a voltage of 5V and a current of 1A, the power dissipation would be:
P = 5V × 1A = 5W
Determining the Required Thermal Resistance
Once you have calculated the power dissipation of the components, you need to determine the required thermal resistance of the heat sink. Thermal resistance is a measure of how well a heat sink can dissipate heat. It is expressed in degrees Celsius per watt (°C/W).
The required thermal resistance can be calculated using the following formula:
Rth = (Tj – Ta) / P
Where:
– Rth is the required thermal resistance in °C/W
– Tj is the maximum junction temperature of the component in °C
– Ta is the ambient temperature in °C
– P is the power dissipation of the component in W
For example, if a component has a maximum junction temperature of 125°C, an ambient temperature of 25°C, and a power dissipation of 5W, the required thermal resistance would be:
Rth = (125°C – 25°C) / 5W = 20°C/W
Selecting the Appropriate Heat Sink
Once you have determined the required thermal resistance, you can select an appropriate heat sink. Heat sink manufacturers typically provide thermal resistance data for their products, which can be used to determine if a particular heat sink is suitable for your application.
When selecting a heat sink, you should also consider the available space on the PCB and the mounting options. Some heat sinks may require additional hardware or modifications to the PCB for proper installation.
Testing and Verification
After selecting and installing the appropriate heat sink, it is important to test and verify its performance. This can be done using thermal imaging cameras or temperature sensors.
Thermal Imaging
Thermal imaging cameras can be used to visualize the temperature distribution on the PCB and identify any hot spots or areas of concern. By comparing the thermal images before and after installing the heat sink, you can determine if the heat sink is effectively dissipating heat.
Temperature Sensors
Temperature sensors, such as thermocouples or resistance temperature detectors (RTDs), can be used to measure the temperature of specific components or areas on the PCB. By monitoring the temperature over time, you can ensure that the components are operating within their specified temperature range.
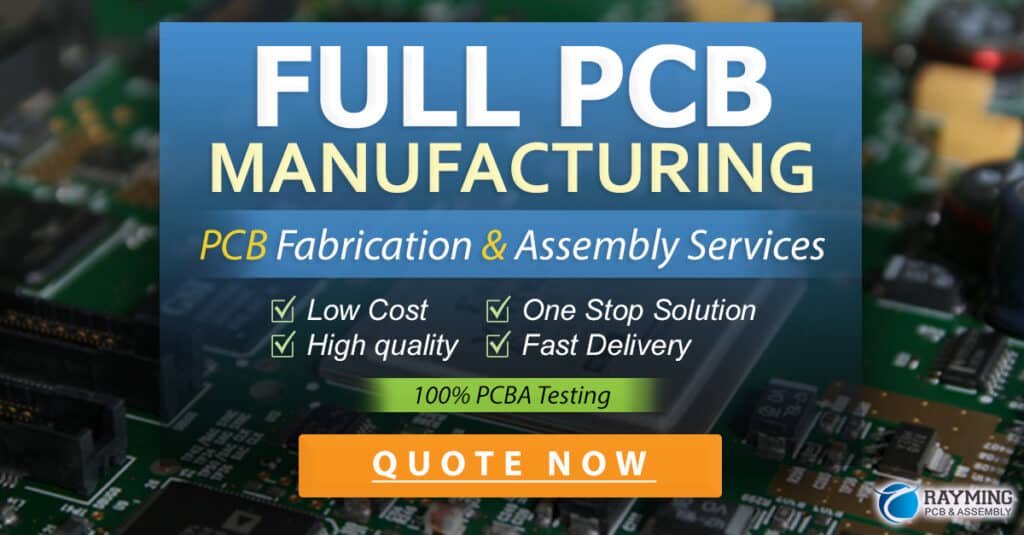
Best Practices for PCB Heat Sink Design
To ensure optimal performance of PCB heat sinks, consider the following best practices:
-
Select the appropriate material: Choose a heat sink material with high thermal conductivity, such as aluminum or copper, to maximize heat dissipation.
-
Maximize surface area: Design the heat sink with a large surface area to increase its ability to dissipate heat. This can be achieved through the use of fins or other features.
-
Ensure proper mounting: Use thermal adhesive or mechanical fasteners to securely attach the heat sink to the PCB. Ensure that there is good contact between the heat sink and the components.
-
Consider airflow: Position the heat sink in a way that allows for maximum airflow around the fins. If necessary, use fans or other cooling solutions to improve airflow.
-
Use thermal interface material: Apply a high-quality thermal interface material between the component and the heat sink to improve heat transfer.
-
Test and verify: Always test and verify the performance of the heat sink after installation to ensure that it is effectively dissipating heat.
FAQ
-
Q: What is a PCB heat sink?
A: A PCB heat sink is a device designed to dissipate heat away from electronic components on a printed circuit board (PCB). It is typically made of a material with high thermal conductivity, such as aluminum or copper, and is attached to the PCB using thermal adhesive or mechanical fasteners. -
Q: Why are PCB heat sinks important?
A: PCB heat sinks are important because they help to prevent electronic components from overheating, which can lead to reduced performance, component failure, and even permanent damage to the PCB. By dissipating heat away from the components, heat sinks ensure that they operate within their specified temperature range. -
Q: How do I know if my PCB needs a heat sink?
A: If your PCB includes components with high power dissipation, such as power transistors, voltage regulators, or processors, it may require a heat sink to prevent overheating. You can determine if a heat sink is necessary by calculating the power dissipation of the components and comparing it to their maximum junction temperature. -
Q: How do I select the right heat sink for my PCB?
A: To select the right heat sink for your PCB, you need to consider factors such as the power dissipation of the components, the ambient temperature, the available space on the PCB, and the required thermal resistance. Heat sink manufacturers typically provide thermal resistance data for their products, which can be used to determine if a particular heat sink is suitable for your application. -
Q: How can I test the performance of a PCB heat sink?
A: You can test the performance of a PCB heat sink using thermal imaging cameras or temperature sensors. Thermal imaging cameras can be used to visualize the temperature distribution on the PCB and identify any hot spots or areas of concern. Temperature sensors, such as thermocouples or resistance temperature detectors (RTDs), can be used to measure the temperature of specific components or areas on the PCB.
Conclusion
PCB heat sinks play a crucial role in ensuring the reliable operation of electronic devices by dissipating heat away from the components. To determine if the PCB heat sink is enough, you need to consider factors such as the power dissipation of the components, the ambient temperature, and the available space for the heat sink.
By following best practices for PCB heat sink design, such as selecting the appropriate material, maximizing surface area, ensuring proper mounting, considering airflow, and using thermal interface material, you can optimize the performance of your PCB heat sink and prevent component failure due to overheating.
Remember to always test and verify the performance of the heat sink after installation to ensure that it is effectively dissipating heat. By taking a proactive approach to thermal management, you can improve the reliability and longevity of your electronic devices.
No responses yet