What are Battery Separators?
Battery separators are thin, porous, and electrically insulating materials placed between the positive and negative electrodes in a battery cell. Their primary function is to prevent direct contact between the electrodes while allowing the flow of ionic charge carriers in the electrolyte. This separation is crucial for preventing short circuits and maintaining the battery’s performance and safety.
Key Functions of Battery Separators
- Preventing direct contact between electrodes
- Allowing ionic charge carrier flow
- Ensuring electrical insulation
- Maintaining battery performance and safety
Types of Battery Separators
There are several types of battery separators, each with its unique characteristics and applications. Let’s explore the most common types:
1. Microporous Separators
Microporous separators are the most widely used type in various battery systems, especially in lead-acid and lithium-ion batteries. These separators have a porous structure with tiny pores that allow the passage of ions while blocking the electrodes’ direct contact.
Advantages of Microporous Separators
- High porosity for efficient ionic flow
- Good mechanical strength
- Excellent chemical stability
- Cost-effective
2. Non-woven Separators
Non-woven separators are made from a web of randomly oriented fibers, typically produced by a wet-laid or dry-laid process. They offer good mechanical properties and are commonly used in nickel-metal hydride (NiMH) and nickel-cadmium (NiCd) batteries.
Advantages of Non-woven Separators
- High mechanical strength
- Good electrolyte absorption and retention
- Excellent thermal stability
- Suitable for high-temperature applications
3. Ceramic Separators
Ceramic separators are made from ceramic materials such as alumina (Al2O3) or zirconia (ZrO2). They are known for their excellent thermal stability and mechanical strength, making them ideal for high-temperature and high-power applications, such as in molten salt batteries.
Advantages of Ceramic Separators
- High thermal stability
- Excellent mechanical strength
- Good chemical resistance
- Suitable for high-temperature applications
4. Polymer Separators
Polymer separators are made from various polymeric materials, such as polyethylene (PE), polypropylene (PP), or a combination of both (PE/PP). They offer a balance of mechanical, thermal, and chemical properties, making them suitable for a wide range of battery applications.
Advantages of Polymer Separators
- Good mechanical strength
- Excellent thermal stability
- High chemical resistance
- Versatile and suitable for various battery chemistries
Materials Used in Battery Separators
The choice of material for a battery separator depends on the specific requirements of the battery system, such as the chemistry, operating conditions, and performance targets. Some of the most common materials used in battery separators include:
1. Polyolefins
Polyolefins, such as polyethylene (PE) and polypropylene (PP), are widely used in battery separators due to their excellent chemical stability, mechanical strength, and low cost. They are particularly common in lithium-ion batteries.
2. Polyvinyl Chloride (PVC)
PVC is used in some battery separators, especially in flooded lead-acid batteries. It offers good chemical resistance and mechanical properties but may have limitations in high-temperature applications.
3. Rubber
Rubber-based separators, such as natural rubber or synthetic rubber, are used in some specialty battery applications. They provide good elasticity and mechanical properties but may have limitations in terms of chemical stability and high-temperature performance.
4. Glass Fiber
Glass fiber separators are known for their excellent thermal stability and mechanical strength. They are commonly used in high-temperature batteries, such as molten salt batteries, and in some specialty applications.
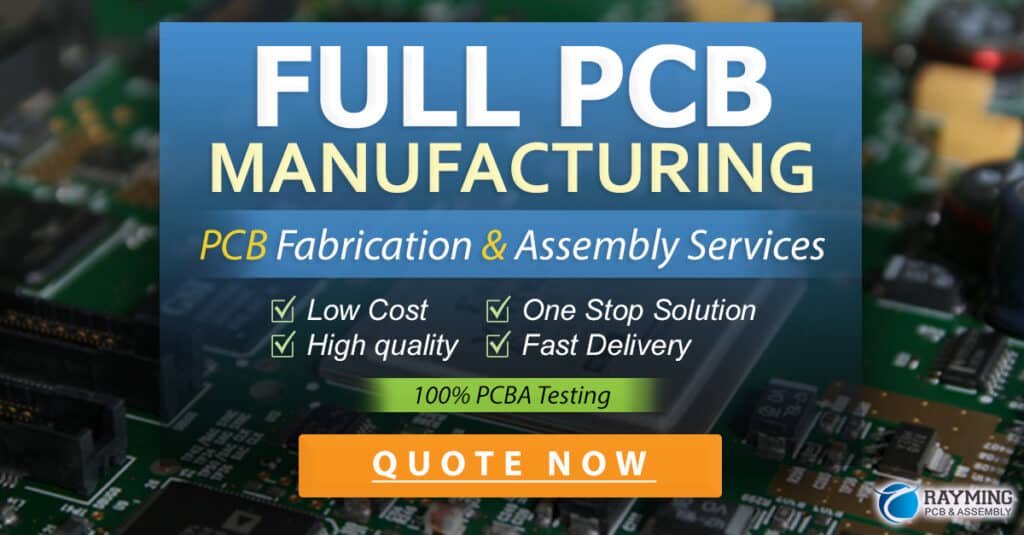
Properties of Battery Separators
The performance and suitability of a battery separator depend on several key properties, including:
1. Porosity
Porosity refers to the volume fraction of voids or pores in the separator material. A high porosity is desirable for efficient ionic transport, but it must be balanced with mechanical strength and dimensional stability.
Typical Porosity Values for Battery Separators
Separator Type | Porosity Range |
---|---|
Microporous | 30-60% |
Non-woven | 50-80% |
Ceramic | 30-50% |
Polymer | 30-60% |
2. Pore Size and Distribution
The pore size and distribution of a battery separator influence its ionic conductivity, mechanical properties, and ability to prevent electrode contact. Smaller pores provide better separation but may limit ionic transport, while larger pores allow faster ionic flow but may compromise the separator’s mechanical integrity.
Typical Pore Size Ranges for Battery Separators
Separator Type | Pore Size Range |
---|---|
Microporous | 0.01-1 μm |
Non-woven | 1-10 μm |
Ceramic | 0.1-1 μm |
Polymer | 0.01-1 μm |
3. Thickness
The thickness of a battery separator affects its mechanical strength, ionic resistance, and overall battery performance. Thinner separators allow for higher energy density and faster ionic transport but may be more susceptible to mechanical damage or short circuits.
Typical Thickness Values for Battery Separators
Separator Type | Thickness Range |
---|---|
Microporous | 10-30 μm |
Non-woven | 100-500 μm |
Ceramic | 100-500 μm |
Polymer | 10-50 μm |
4. Mechanical Strength
Battery separators must have sufficient mechanical strength to withstand the stresses encountered during battery manufacturing, assembly, and operation. This includes tensile strength, puncture resistance, and dimensional stability.
5. Chemical Stability
The separator material must be chemically stable in the presence of the battery electrolyte and withstand the potential degradation caused by oxidation, reduction, or hydrolysis reactions. It should also be compatible with the electrode materials and other battery components.
6. Thermal Stability
Thermal stability is crucial for battery separators, as they must maintain their integrity and performance over a wide range of operating temperatures. The separator should not melt, shrink, or degrade at elevated temperatures, which could lead to short circuits or battery failure.
Manufacturing Processes for Battery Separators
The manufacturing process for battery separators depends on the type of separator and the materials used. Some common manufacturing techniques include:
1. Dry Process
In the dry process, the separator material is extruded, stretched, and annealed to create a microporous structure. This process is commonly used for producing microporous polyolefin separators.
2. Wet Process
The wet process involves the dissolution of the polymer material in a solvent, followed by immersion precipitation or phase inversion to create a porous structure. This process is used for manufacturing certain types of microporous and non-woven separators.
3. Coating Process
In the coating process, a porous substrate is coated with a ceramic or polymer material to create a composite separator. This technique is used for producing ceramic-coated separators or multi-layer separators with enhanced properties.
4. Sintering Process
The sintering process involves the heat treatment of a compressed powder or fiber material to create a porous structure. This process is used for manufacturing certain types of ceramic and glass fiber separators.
Applications of Battery Separators
Battery separators find applications in various battery systems, depending on their specific properties and performance requirements. Some common applications include:
1. Lead-Acid Batteries
In lead-acid batteries, separators are used to prevent contact between the positive and negative electrodes while allowing the flow of sulfuric acid electrolyte. Microporous separators made from PVC or PE are commonly used in flooded lead-acid batteries, while AGM (Absorbent Glass Mat) separators are used in valve-regulated lead-acid (VRLA) batteries.
2. Lithium-Ion Batteries
Lithium-ion batteries rely on high-performance separators to ensure safety and long-term cycling stability. Microporous polyolefin separators, such as PE, PP, or PE/PP blends, are widely used in lithium-ion batteries for consumer electronics, electric vehicles, and energy storage systems.
3. Nickel-Metal Hydride (NiMH) Batteries
NiMH batteries typically use non-woven separators made from polyolefin fibers or a combination of polyolefin and nylon fibers. These separators provide good electrolyte absorption and mechanical strength, making them suitable for the alkaline electrolyte environment in NiMH batteries.
4. Nickel-Cadmium (NiCd) Batteries
NiCd batteries also use non-woven separators, similar to those used in NiMH batteries. The separators must be resistant to the alkaline electrolyte and provide good mechanical stability to prevent short circuits.
5. Flow Batteries
In flow batteries, such as vanadium redox flow batteries (VRFBs), separators play a crucial role in preventing the mixing of the positive and negative electrolytes while allowing the selective transport of charge carriers. Ion exchange membranes or porous separators with high chemical stability and selectivity are used in these applications.
Future Trends and Developments in Battery Separators
As battery technologies continue to evolve, there is a growing demand for advanced separators with improved performance, safety, and sustainability. Some of the future trends and developments in battery separators include:
1. High-Temperature Separators
With the increasing interest in high-temperature battery systems, such as molten salt batteries or solid-state batteries, there is a need for separators that can withstand extreme temperatures (above 200°C) without degradation. Ceramic separators, glass fiber separators, or specially designed polymer separators are being developed for these applications.
2. Functionalized Separators
Functionalized separators are designed to provide additional benefits beyond their basic functions of separation and ionic transport. Examples include separators with flame-retardant properties, separators with enhanced thermal management capabilities, or separators with built-in safety features such as shutdown mechanisms.
3. Sustainable and Recyclable Separators
As the focus on sustainability and circular economy grows, there is a push for developing separators made from renewable, biodegradable, or recyclable materials. Bio-based polymers, cellulose-derived materials, or recycled materials are being explored as potential alternatives to traditional petroleum-based separators.
4. Smart Separators
Smart separators are an emerging concept that involves integrating sensing, monitoring, or self-healing capabilities into the separator material. These separators could provide real-time information on the battery’s health, detect potential safety issues, or even self-repair in case of damage, enhancing the overall reliability and performance of the battery system.
Frequently Asked Questions (FAQ)
1. What is the difference between a separator and an electrolyte in a battery?
The separator is a solid, porous material that physically separates the positive and negative electrodes in a battery, while the electrolyte is a liquid or gel that fills the pores of the separator and allows the flow of ionic charge carriers between the electrodes.
2. Can a battery operate without a separator?
No, a battery cannot operate safely without a separator. The separator is essential for preventing direct contact between the electrodes, which would cause a short circuit and potentially lead to battery failure, overheating, or even explosion.
3. How does the porosity of a separator affect battery performance?
The porosity of a separator influences the battery’s performance in several ways. Higher porosity allows for better ionic transport, reducing internal resistance and improving battery efficiency. However, very high porosity may compromise the separator’s mechanical strength and increase the risk of short circuits. The optimal porosity depends on the specific battery chemistry and application requirements.
4. What are the most common materials used in battery separators?
The most common materials used in battery separators are polyolefins (polyethylene and polypropylene), PVC, rubber, glass fiber, and ceramics. The choice of material depends on the battery chemistry, operating conditions, and performance requirements.
5. How do separators contribute to battery safety?
Separators play a crucial role in battery safety by preventing direct contact between the positive and negative electrodes, which could lead to short circuits, overheating, or thermal runaway. Additionally, some separators have built-in safety features, such as shutdown mechanisms that block ionic flow at high temperatures, or flame-retardant properties that reduce the risk of fire in case of a failure.
Conclusion
Battery separators are essential components that ensure the safe, efficient, and reliable operation of various battery systems. By understanding the types, materials, properties, and manufacturing processes of battery separators, researchers, engineers, and industry professionals can design and optimize battery systems for specific applications. As battery technologies continue to advance, the development of innovative separator solutions will be crucial for enabling the next generation of high-performance, safe, and sustainable energy storage devices.
No responses yet