Introduction
Printed Circuit Boards (PCBs) are essential components in modern electronic devices, ranging from smartphones and computers to industrial equipment and medical devices. When it comes to manufacturing PCBs, one of the most critical aspects is the cost. Understanding the factors that influence PCB pricing can help you make informed decisions and optimize your budget. In this article, we will discuss nine key factors that contribute to the real PCB board price.
PCB Pricing Factors
1. Board Size
The size of the PCB is one of the most significant factors that affect its price. Larger boards require more materials and take up more space on the production panel, resulting in higher costs. PCB sizes are typically measured in square inches or millimeters.
Board Size (mm) | Relative Cost |
---|---|
50 x 50 | 1.0 |
100 x 100 | 1.5 |
150 x 150 | 2.0 |
200 x 200 | 2.5 |
As the board size increases, the relative cost also increases. It’s essential to design your PCB to be as compact as possible while still meeting your functional requirements to minimize costs.
2. Layer Count
The number of layers in a PCB directly impacts its cost. Each additional layer requires more materials, processing time, and labor, resulting in higher prices. Common layer counts include:
- Single-layer
- Double-layer
- Four-layer
- Six-layer
- Eight-layer or more
Layer Count | Relative Cost |
---|---|
1 | 1.0 |
2 | 1.5 |
4 | 2.0 |
6 | 2.5 |
8 | 3.0 |
Minimizing the number of layers in your PCB design can help reduce costs. However, it’s crucial to ensure that your design meets your electrical and mechanical requirements.
3. Material Selection
The choice of materials used in PCB fabrication significantly affects the overall cost. The most common PCB materials are:
- FR-4: A standard, cost-effective material suitable for most applications
- High-Tg FR-4: An improved version of FR-4 with better thermal stability
- Polyimide: A high-performance material with excellent thermal and mechanical properties
- Flexible PCBs: Made from flexible materials like Polyimide or Polyester
Material | Relative Cost |
---|---|
FR-4 | 1.0 |
High-Tg FR-4 | 1.2 |
Polyimide | 1.5 |
Flexible PCBs | 2.0 |
Selecting the appropriate material for your application is crucial. While high-performance materials may increase costs, they can be necessary for demanding applications.
4. Quantity
The quantity of PCBs you order has a significant impact on the unit price. Manufacturers often offer volume discounts, as the fixed costs associated with setting up production can be spread across a larger number of units. Typical quantity breaks include:
- Prototype (1-10 units)
- Small volume (11-100 units)
- Medium volume (101-1,000 units)
- Large volume (1,001-10,000 units)
- Mass production (10,000+ units)
Quantity | Relative Cost per Unit |
---|---|
1-10 | 10.0 |
11-100 | 5.0 |
101-1,000 | 2.0 |
1,001-10,000 | 1.5 |
10,000+ | 1.0 |
Planning your PCB requirements in advance and ordering in larger quantities can help you achieve significant cost savings.
5. Surface Finish
The surface finish of a PCB is applied to protect the exposed copper and enhance solderability. Common surface finishes include:
- HASL (Hot Air Solder Leveling)
- ENIG (Electroless Nickel Immersion Gold)
- OSP (Organic Solderability Preservative)
- Immersion Silver
- Immersion Tin
Surface Finish | Relative Cost |
---|---|
HASL | 1.0 |
OSP | 1.1 |
Immersion Tin | 1.2 |
Immersion Silver | 1.3 |
ENIG | 1.5 |
HASL is the most cost-effective option, while ENIG offers superior durability and flatness at a higher cost. Select the surface finish that best suits your application and budget.
6. Hole Size and Density
The size and density of holes in a PCB affect the manufacturing process and, consequently, the cost. Smaller hole sizes and higher hole densities require more precise drilling and increase processing time.
Hole Size (mm) | Relative Cost |
---|---|
0.8 and above | 1.0 |
0.6 – 0.79 | 1.2 |
0.4 – 0.59 | 1.5 |
Below 0.4 | 2.0 |
Designing your PCB with larger hole sizes and lower hole densities, when possible, can help reduce costs.
7. Copper Weight
The copper weight, or thickness, of a PCB’s conductive layers affects its current-carrying capacity and cost. Thicker copper layers require more material and processing time, resulting in higher prices. Common copper weights include:
- 0.5 oz (17.5 µm)
- 1 oz (35 µm)
- 2 oz (70 µm)
- 3 oz (105 µm)
Copper Weight (oz) | Relative Cost |
---|---|
0.5 | 1.0 |
1 | 1.2 |
2 | 1.5 |
3 | 1.8 |
Select the appropriate copper weight for your application, considering the trade-off between cost and performance.
8. Solder Mask and Silkscreen
Solder mask and silkscreen are optional layers that add functionality and aesthetics to a PCB. Solder mask is a protective layer that covers the copper traces, while silkscreen is used for text and component markings.
Option | Relative Cost |
---|---|
No solder mask or silkscreen | 1.0 |
Solder mask only | 1.1 |
Silkscreen only | 1.1 |
Solder mask and silkscreen | 1.2 |
Including solder mask and silkscreen in your PCB design will increase costs, but they offer important benefits such as improved solderability, insulation, and readability.
9. Lead Time
The lead time, or the time required to manufacture and deliver your PCBs, can also affect the price. Faster lead times often come at a premium, as manufacturers may need to prioritize your order and use expedited shipping.
Lead Time | Relative Cost |
---|---|
Standard (2-3 weeks) | 1.0 |
Express (1-2 weeks) | 1.2 |
Super Express (1 week or less) | 1.5 |
Planning ahead and allowing for standard lead times can help you save on costs. However, if your project requires faster delivery, be prepared to pay a premium.
Frequently Asked Questions (FAQ)
1. What is the most significant factor affecting PCB pricing?
The most significant factor affecting PCB pricing is typically the board size. Larger boards require more materials and processing time, resulting in higher costs.
2. Can I reduce PCB costs by using fewer layers?
Yes, reducing the number of layers in your PCB design can help lower costs, as each additional layer requires more materials and processing time. However, it’s essential to ensure that your design still meets your electrical and mechanical requirements.
3. How can I save on PCB costs when ordering small quantities?
When ordering small quantities, you can save on PCB costs by designing your board to be as compact as possible, minimizing the number of layers, and selecting cost-effective materials like FR-4. Additionally, consider using standard surface finishes and allowing for longer lead times.
4. Are there any hidden costs associated with PCB manufacturing?
Some potential hidden costs associated with PCB manufacturing include tooling charges for custom designs, expedited shipping fees for faster lead times, and additional charges for special requirements like controlled impedance or tight tolerances.
5. Can I negotiate pricing with PCB manufacturers?
Yes, it’s often possible to negotiate pricing with PCB manufacturers, especially if you have a long-term relationship or are placing a large order. Be transparent about your budget and requirements, and work with your manufacturer to find a solution that meets your needs while minimizing costs.
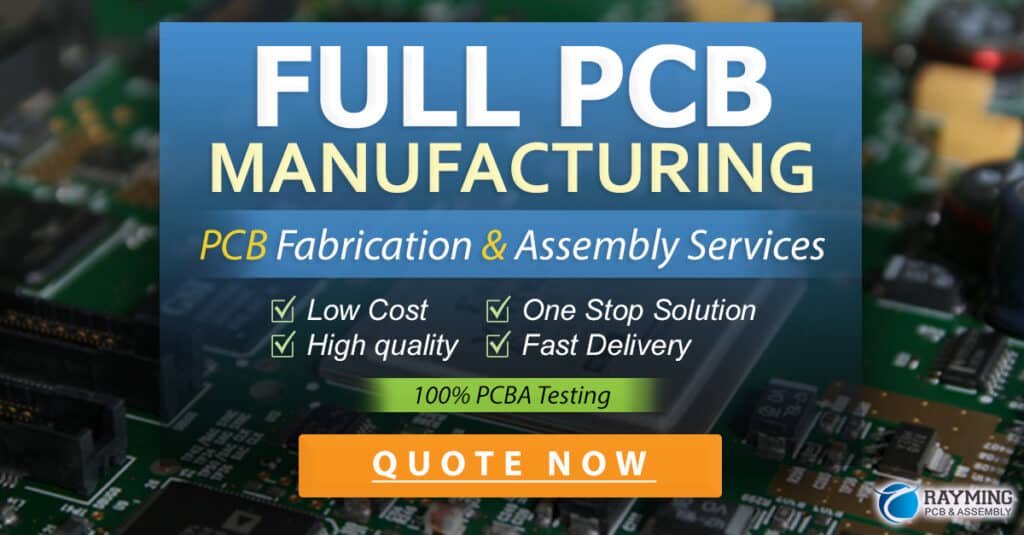
Conclusion
Understanding the factors that influence PCB pricing is crucial for optimizing your budget and making informed decisions. By considering board size, layer count, material selection, quantity, surface finish, hole size and density, copper weight, solder mask and silkscreen, and lead time, you can effectively manage PCB costs without compromising on quality or functionality.
When designing your PCB, prioritize compact layouts, minimize layer counts, and select cost-effective materials and surface finishes whenever possible. Plan your requirements in advance and order in larger quantities to take advantage of volume discounts. Finally, maintain open communication with your PCB manufacturer to discuss your needs, explore cost-saving options, and negotiate pricing when appropriate.
By keeping these nine factors in mind and working closely with your PCB manufacturer, you can achieve the perfect balance between cost and performance for your electronic projects.
No responses yet