What is a Custom Cable Assembly?
A custom cable assembly is a specialized cabling solution designed and manufactured to meet the specific requirements of a particular application or device. Unlike off-the-shelf cables, custom assemblies are tailored to address unique challenges, such as harsh environmental conditions, high-speed data transmission, or space constraints. These assemblies typically consist of cables, connectors, and other components that are carefully selected and configured to ensure optimal performance and reliability.
The Benefits of Custom Cable Assemblies
1. Tailored to Specific Requirements
One of the primary advantages of custom cable assemblies is their ability to be tailored to the exact specifications of a given application. By working closely with experienced cable assembly manufacturers, businesses can ensure that their cabling solutions are designed to meet their unique needs, whether it’s in terms of length, gauge, shielding, or connector type. This level of customization allows for optimal performance and efficiency, as the cables are engineered to handle the specific demands of the application.
2. Improved Reliability and Durability
Custom cable assemblies are built to withstand the rigors of their intended environment. By selecting high-quality materials and incorporating robust design features, such as strain relief and protective jacketing, these assemblies can provide superior reliability and durability compared to generic, off-the-shelf cables. This translates into reduced downtime, lower maintenance costs, and extended product life cycles, ultimately contributing to a better return on investment.
3. Streamlined Installation and Maintenance
Another significant benefit of custom cable assemblies is the streamlined installation and maintenance process they offer. With pre-configured connectors and carefully measured lengths, these assemblies can be easily integrated into a system, minimizing the time and effort required for installation. Additionally, custom labeling and color-coding can simplify troubleshooting and maintenance tasks, allowing technicians to quickly identify and address any issues that may arise.
4. Cost Efficiency
While custom cable assemblies may have a higher upfront cost compared to off-the-shelf cables, they often prove to be more cost-effective in the long run. By investing in a tailored solution that meets the exact requirements of the application, businesses can avoid the need for frequent replacements or modifications, which can be both time-consuming and expensive. Furthermore, the improved performance and reliability of custom assemblies can lead to increased productivity and reduced operational costs.
Applications of Custom Cable Assemblies
Custom cable assemblies find applications across a wide range of industries, each with its own unique set of requirements and challenges. Some of the most common applications include:
1. Industrial Automation
In industrial settings, custom cable assemblies play a crucial role in connecting various components of automated systems, such as sensors, actuators, and controllers. These assemblies must be designed to withstand harsh conditions, including exposure to chemicals, extreme temperatures, and constant vibration. By utilizing custom solutions, industrial facilities can ensure reliable and uninterrupted operation, minimizing costly downtime and maximizing productivity.
2. Medical Devices
The medical industry relies heavily on custom cable assemblies for a variety of applications, from patient monitoring systems to surgical equipment. These assemblies must meet stringent safety and performance standards, as well as being able to withstand frequent sterilization processes. Custom cable solutions in the medical field often feature biocompatible materials, shielding against electromagnetic interference, and specialized connectors to ensure secure and reliable connections.
3. Telecommunications
In the telecommunications industry, custom cable assemblies are essential for transmitting data, voice, and video signals across networks. These assemblies must be capable of handling high-speed transmissions while maintaining signal integrity and minimizing interference. Custom solutions in this field often incorporate shielding, high-quality connectors, and low-loss materials to ensure optimal performance and reliability.
4. Aerospace and Defense
Aerospace and defense applications demand the highest levels of performance and reliability from their cabling systems. Custom cable assemblies in these industries are designed to withstand extreme environmental conditions, such as high altitudes, temperature fluctuations, and exposure to radiation. These assemblies often feature specialized materials, such as lightweight alloys and high-temperature insulation, to meet the unique challenges of aerospace and defense applications.
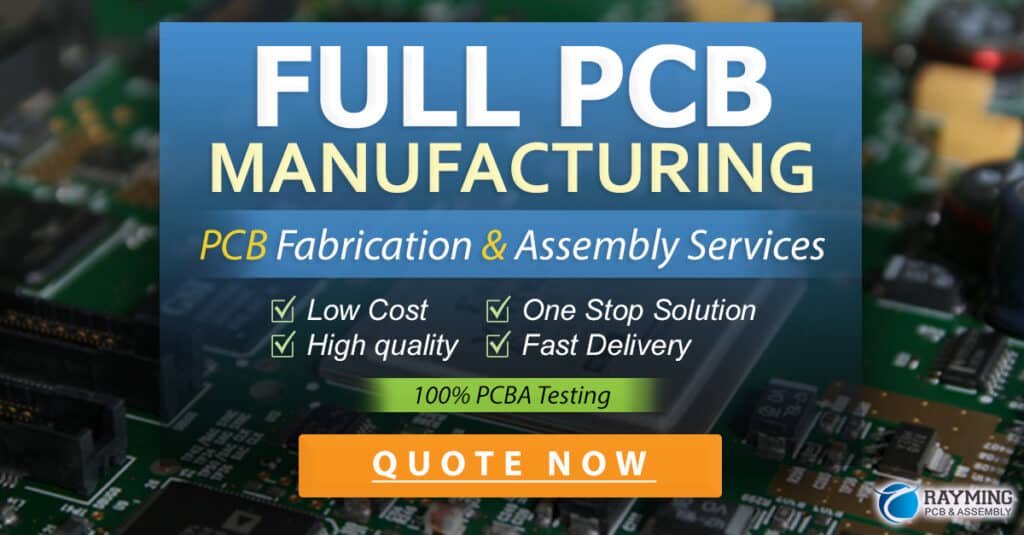
The Custom Cable Assembly Process
Creating a custom cable assembly involves a series of steps that ensure the final product meets the specific requirements of the application. The process typically includes the following stages:
1. Consultation and Design
The first step in creating a custom cable assembly is to consult with the client to understand their specific needs and requirements. This involves gathering information about the intended application, environmental conditions, performance expectations, and any other relevant factors. Based on this input, the cable assembly manufacturer will develop a detailed design that incorporates the appropriate materials, components, and configuration to meet the client’s needs.
2. Material Selection
Once the design is finalized, the next step is to select the appropriate materials for the custom cable assembly. This includes choosing the right type of cable, such as coaxial, twisted pair, or fiber optic, as well as the appropriate gauge, insulation, and shielding. Connectors, strain reliefs, and other components are also selected based on the specific requirements of the application.
3. Assembly and Termination
With the materials selected, the actual assembly process can begin. This involves cutting the cables to the required lengths, stripping the insulation, and terminating the ends with the chosen connectors. The assembly process may also include additional steps, such as soldering, crimping, or molding, depending on the specific design of the cable assembly.
4. Testing and Quality Control
To ensure the highest levels of performance and reliability, custom cable assemblies must undergo rigorous testing and quality control procedures. This may include continuity testing to verify proper connections, insulation resistance testing to ensure adequate isolation between conductors, and signal integrity testing to confirm that the assembly can handle the required data transmission rates. Any assemblies that fail to meet the specified standards are either reworked or discarded, ensuring that only the highest quality products are delivered to the client.
5. Packaging and Delivery
Once the custom cable assemblies have passed all quality control checks, they are packaged for delivery to the client. Packaging is designed to protect the assemblies during transit and may include additional features, such as static shielding bags or moisture barrier bags, depending on the specific requirements of the application. The assemblies are then shipped to the client, ready for installation and use in their intended application.
Choosing the Right Custom Cable Assembly Manufacturer
When selecting a custom cable assembly manufacturer, there are several key factors to consider to ensure that you receive the highest quality products and services. These factors include:
1. Experience and Expertise
Look for a manufacturer with a proven track record of success in creating custom cable assemblies for a wide range of applications. Experienced manufacturers will have the knowledge and expertise necessary to guide you through the design process, recommend the appropriate materials and components, and ensure that your assemblies meet all performance and reliability requirements.
2. Capabilities and Capacity
Consider the manufacturer’s capabilities and capacity to handle your specific needs. This includes their ability to work with a variety of materials, their expertise in different termination and assembly techniques, and their capacity to produce the required volume of assemblies within your desired timeframe.
3. Quality Control and Certifications
Choose a manufacturer that places a strong emphasis on quality control and has the necessary certifications to ensure that their products meet industry standards. Look for certifications such as ISO 9001, IPC/WHMA-A-620, and UL, which demonstrate a commitment to quality and adherence to recognized industry standards.
4. Customer Service and Support
Finally, consider the level of customer service and support provided by the manufacturer. Look for a partner that is responsive to your needs, offers timely communication, and provides comprehensive support throughout the entire design and manufacturing process. A manufacturer that values strong relationships with their clients is more likely to go above and beyond to ensure your satisfaction and success.
FAQ
1. How long does it take to create a custom cable assembly?
The lead time for creating a custom cable assembly can vary depending on the complexity of the design, the availability of materials, and the volume of the order. On average, lead times can range from a few days to several weeks. It is best to consult with your chosen manufacturer to get a more accurate estimate based on your specific requirements.
2. Can custom cable assemblies be designed for outdoor use?
Yes, custom cable assemblies can be designed to withstand the challenges of outdoor environments. This may involve the use of special materials, such as UV-resistant jackets or waterproof connectors, to protect the cables from the elements. When discussing your requirements with the manufacturer, be sure to specify the intended outdoor application to ensure that the appropriate design features are incorporated.
3. Are custom cable assemblies more expensive than off-the-shelf cables?
While custom cable assemblies may have a higher upfront cost compared to off-the-shelf cables, they often provide a better long-term value. Custom assemblies are designed to meet the exact requirements of the application, which can lead to improved performance, reliability, and durability. This, in turn, can result in reduced maintenance and replacement costs over the life of the product.
4. Can custom cable assemblies be designed for high-speed data transmission?
Yes, custom cable assemblies can be engineered to handle high-speed data transmission requirements. This may involve the use of specialized materials, such as low-loss dielectrics or high-bandwidth conductors, as well as specific design features, like controlled impedance or shielding, to maintain signal integrity. Working closely with an experienced manufacturer can help ensure that your custom assembly is optimized for your specific high-speed data transmission needs.
5. What industries commonly use custom cable assemblies?
Custom cable assemblies find applications across a wide range of industries, including:
- Industrial automation
- Medical devices
- Telecommunications
- Aerospace and defense
- Automotive
- Consumer electronics
- Oil and gas
- Renewable energy
Essentially, any industry that relies on electrical or electronic systems can benefit from the use of custom cable assemblies to improve performance, reliability, and efficiency.
Conclusion
Custom cable assemblies offer a powerful solution for businesses seeking to optimize the performance and reliability of their electrical and electronic systems. By tailoring cabling solutions to the exact requirements of the application, custom assemblies can improve efficiency, reduce downtime, and lower long-term costs. When choosing a custom cable assembly manufacturer, it is essential to consider factors such as experience, capabilities, quality control, and customer service to ensure that you receive the highest quality products and support.
As technology continues to advance and the demands on cabling systems become ever more complex, the importance of custom cable assemblies will only continue to grow. By partnering with an experienced and reliable manufacturer, businesses can ensure that they have the tailored connectivity solutions they need to stay ahead of the curve and succeed in today’s competitive marketplace.
No responses yet