Introduction
Printed Circuit Boards (PCBs) are the backbone of modern electronics, and this is especially true in the medical industry. Medical devices require the highest quality and reliability standards to ensure patient safety and effective treatment. Therefore, getting a high-quality medical grade PCB is crucial for any medical device manufacturer. In this article, we will discuss seven essential tips to help you obtain the best possible medical grade PCBs for your projects.
Tip 1: Choose the Right PCB Manufacturer
The Importance of Selecting a Reputable PCB Manufacturer
One of the most critical steps in getting a high-quality medical grade PCB is choosing the right manufacturer. Not all PCB manufacturers are created equal, and it’s essential to select a company with a proven track record of producing reliable, high-quality boards for the medical industry. Look for a manufacturer that:
- Has experience in manufacturing medical grade PCBs
- Is certified to relevant industry standards (e.g., ISO 13485, IPC-6012 Class 3)
- Employs strict quality control processes
- Offers excellent customer support and communication
Researching and Vetting Potential PCB Manufacturers
To find the best PCB manufacturer for your needs, start by researching companies online. Look for reviews, testimonials, and case studies from other medical device manufacturers. You can also attend industry trade shows and conferences to meet with potential manufacturers in person and discuss your requirements.
When vetting potential manufacturers, ask about their:
- Experience with medical grade PCBs
- Quality control processes and certifications
- Lead times and pricing
- Ability to handle your specific project requirements
Tip 2: Design for Manufacturability (DFM)
What is DFM and Why is it Important?
Design for Manufacturability (DFM) is the process of optimizing your PCB design to ensure that it can be efficiently and reliably manufactured. By incorporating DFM principles into your design process, you can:
- Reduce manufacturing costs
- Improve product quality and reliability
- Minimize the risk of production delays or issues
Key DFM Considerations for Medical Grade PCBs
When designing a medical grade PCB, there are several key DFM considerations to keep in mind:
-
Component Selection: Choose components that are suitable for the intended use environment and have a proven track record of reliability in medical applications.
-
Layout and Routing: Ensure that your PCB layout and routing are optimized for manufacturability, with adequate spacing between components, traces, and vias.
-
Thermal Management: Consider the thermal requirements of your components and design your PCB to ensure proper heat dissipation.
-
Signal Integrity: Pay close attention to signal integrity issues, such as electromagnetic interference (EMI) and crosstalk, which can affect the performance and reliability of your device.
-
Testing and Validation: Plan for comprehensive testing and validation processes to ensure that your PCB meets all necessary performance and reliability requirements.
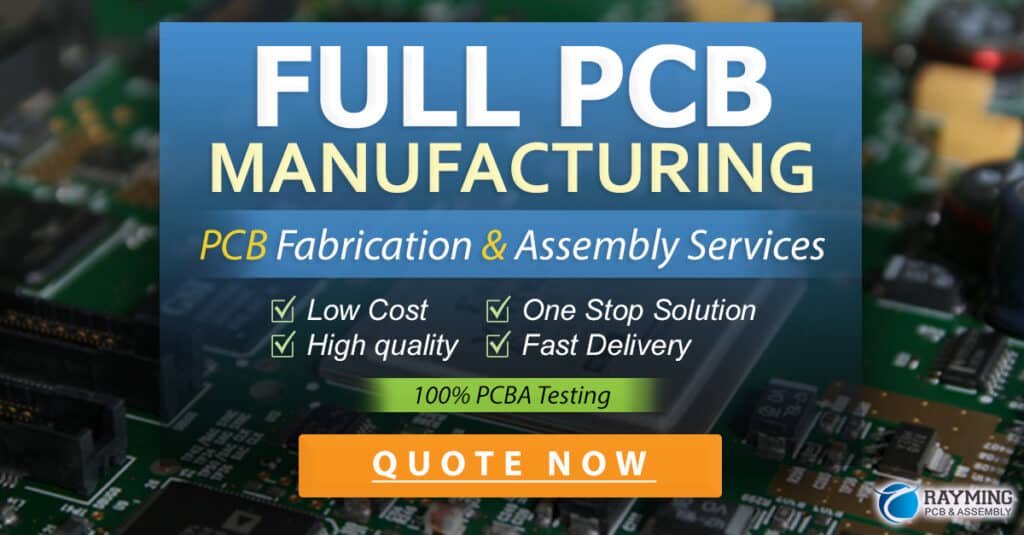
Tip 3: Use High-Quality Materials
The Role of Material Selection in PCB Quality and Reliability
The materials used in your PCB can have a significant impact on its quality, reliability, and longevity. When selecting materials for a medical grade PCB, it’s essential to choose high-quality, medical-grade materials that can withstand the rigors of the intended use environment.
Key Materials to Consider for Medical Grade PCBs
Some of the key materials to consider when manufacturing medical grade PCBs include:
-
Substrates: Choose high-quality, medical-grade substrates such as FR-4, polyimide, or ceramic, depending on your specific application requirements.
-
Copper: Use high-purity, medical-grade copper for your PCB traces and vias to ensure optimal conductivity and reliability.
-
Solder Mask: Select a high-quality, medical-grade solder mask that can withstand the cleaning and sterilization processes required for medical devices.
-
Silkscreen: Opt for a durable, medical-grade silkscreen that can withstand repeated cleaning and handling without fading or wearing off.
Tip 4: Implement Robust Quality Control Processes
The Importance of Quality Control in Medical Grade PCB Manufacturing
Quality control is critical in the production of medical grade PCBs. Even minor defects or inconsistencies can lead to device failure, which can have serious consequences for patient safety and treatment outcomes. Therefore, it’s essential to implement robust quality control processes throughout the entire PCB manufacturing process.
Key Quality Control Processes for Medical Grade PCBs
Some of the key quality control processes to consider for medical grade PCBs include:
-
Incoming Material Inspection: Carefully inspect all incoming materials to ensure they meet the necessary quality and performance standards.
-
In-Process Inspection: Implement regular in-process inspections to identify and correct any issues or defects as early as possible in the manufacturing process.
-
Automated Optical Inspection (AOI): Use AOI systems to quickly and accurately detect surface-level defects such as solder bridges, missing components, and incorrect component placement.
-
X-Ray Inspection: Employ X-ray inspection to detect internal defects such as voids, cracks, and delamination that may not be visible on the surface.
-
Electrical Testing: Conduct comprehensive electrical testing to ensure that your PCBs meet all necessary performance and functionality requirements.
Tip 5: Adhere to Relevant Industry Standards and Regulations
The Importance of Compliance in Medical Grade PCB Manufacturing
Medical devices are subject to strict regulatory requirements to ensure patient safety and effectiveness. Therefore, it’s crucial to ensure that your medical grade PCBs adhere to all relevant industry standards and regulations.
Key Standards and Regulations for Medical Grade PCBs
Some of the key standards and regulations to consider when manufacturing medical grade PCBs include:
-
IPC Standards: Ensure that your PCBs are manufactured in accordance with the relevant IPC standards, such as IPC-6012 (Qualification and Performance Specification for Rigid Printed Boards) and IPC-A-600 (Acceptability of Printed Boards).
-
ISO 13485: Work with a PCB manufacturer that is certified to ISO 13485, which specifies requirements for a quality management system specific to the medical device industry.
-
FDA Regulations: Ensure that your PCBs comply with applicable FDA regulations, such as the Quality System Regulation (21 CFR Part 820) and the Medical Device Reporting regulation (21 CFR Part 803).
-
CE Marking: If you plan to market your medical device in the European Union, ensure that your PCBs meet the requirements for CE marking, which indicates compliance with applicable European health, safety, and environmental protection legislation.
Tip 6: Plan for Comprehensive Testing and Validation
The Role of Testing and Validation in Ensuring PCB Quality and Reliability
Comprehensive testing and validation are essential for ensuring the quality, reliability, and performance of your medical grade PCBs. By thoroughly testing your boards at various stages of the manufacturing process and after production, you can identify and address any issues before they lead to device failure or patient harm.
Key Testing and Validation Processes for Medical Grade PCBs
Some of the key testing and validation processes to consider for medical grade PCBs include:
-
Design Validation: Conduct thorough design reviews and simulations to validate your PCB design before moving into production.
-
Prototype Testing: Manufacture and test prototype boards to ensure that your design meets all necessary performance and reliability requirements.
-
Environmental Testing: Subject your PCBs to various environmental stresses, such as temperature, humidity, and vibration, to ensure they can withstand the intended use environment.
-
Accelerated Life Testing: Perform accelerated life testing to assess the long-term reliability of your PCBs under simulated use conditions.
-
Functional Testing: Conduct comprehensive functional testing to verify that your PCBs perform as intended and meet all necessary specifications.
Tip 7: Foster Strong Communication and Collaboration
The Importance of Communication and Collaboration in Medical Grade PCB Manufacturing
Effective communication and collaboration between your team and your PCB manufacturer are critical for ensuring the success of your medical device project. By fostering strong relationships and maintaining open lines of communication, you can:
- Ensure that your requirements are clearly understood and met
- Quickly address any issues or concerns that arise during the manufacturing process
- Benefit from your manufacturer’s expertise and insights to optimize your PCB design and production
Strategies for Effective Communication and Collaboration
Some strategies for effective communication and collaboration with your PCB manufacturer include:
-
Clearly Define Requirements: Provide your manufacturer with clear, detailed specifications for your PCB, including performance requirements, materials, and testing needs.
-
Establish Regular Communication: Set up regular meetings or check-ins with your manufacturer to discuss project progress, address any issues, and share updates.
-
Foster a Partnership Mindset: View your PCB manufacturer as a partner in your success, and work together to optimize your PCB design and manufacturing processes.
-
Leverage Manufacturer Expertise: Don’t hesitate to ask for your manufacturer’s input and expertise on design, materials, or process improvements that could benefit your project.
Frequently Asked Questions (FAQ)
-
What is a medical grade PCB?
A medical grade PCB is a printed circuit board that is designed and manufactured to meet the strict quality, reliability, and regulatory requirements of the medical device industry. -
Why are medical grade PCBs more expensive than standard PCBs?
Medical grade PCBs are more expensive due to the higher quality materials, more stringent manufacturing processes, and additional testing and certification requirements necessary to ensure patient safety and device reliability. -
How do I know if a PCB manufacturer is qualified to produce medical grade PCBs?
Look for a PCB manufacturer that is certified to relevant industry standards such as ISO 13485, has experience manufacturing PCBs for the medical industry, and can provide references or case studies from other medical device clients. -
What are some common challenges in medical grade PCB manufacturing?
Common challenges include meeting strict regulatory requirements, ensuring high reliability and long-term performance, managing complex designs and materials, and maintaining consistent quality control throughout the manufacturing process. -
How long does it typically take to manufacture a medical grade PCB?
Lead times for medical grade PCBs can vary depending on the complexity of the design, the materials used, and the specific manufacturing and testing requirements. It’s essential to work closely with your PCB manufacturer to establish realistic timelines and plan accordingly.
Conclusion
Obtaining high-quality medical grade PCBs is essential for ensuring the safety, reliability, and effectiveness of medical devices. By following these seven tips – choosing the right manufacturer, designing for manufacturability, using high-quality materials, implementing robust quality control processes, adhering to industry standards and regulations, planning for comprehensive testing and validation, and fostering strong communication and collaboration – you can ensure that your medical grade PCBs meet the highest standards of quality and performance. As the medical device industry continues to evolve and advance, partnering with a trusted, experienced PCB manufacturer will be crucial for bringing innovative, life-saving products to market.
No responses yet