Introduction to PCB Imaging
Printed Circuit Board (PCB) imaging is a crucial step in the PCB fabrication process. It involves transferring the circuit pattern from a photomask or artwork onto the copper-clad laminate. The most common methods of PCB imaging are screen printing, photolithography, and dry film imaging.
Dry film imaging, also known as dry film photoresist or dry film solder mask, is a popular method for PCB imaging due to its simplicity, cost-effectiveness, and high resolution capabilities. In this article, we will explore the dry film imaging process in detail, including its advantages, disadvantages, and best practices.
What is Dry Film Photoresist?
Dry film photoresist is a light-sensitive polymer film that is used to create the circuit pattern on a PCB. It consists of three layers:
- Protective polyethylene film
- Light-sensitive photoresist layer
- Polyester base film
The photoresist layer is sensitive to ultraviolet (UV) light and becomes soluble in a developer solution when exposed to it. The protective polyethylene film is removed before exposure, while the polyester base film provides support and is removed after exposure.
Advantages of Dry Film Imaging
Dry film imaging offers several advantages over other PCB imaging methods:
- High resolution: Dry film photoresist can achieve line widths and spaces as small as 50 microns (0.002 inches), making it suitable for high-density PCB Designs.
- Excellent adhesion: The photoresist layer adheres firmly to the copper surface, reducing the risk of undercut or lifting during etching.
- Ease of use: Dry film is easy to handle and apply, requiring minimal equipment and training.
- Cost-effective: Dry film is less expensive than liquid photoresist and has a longer shelf life.
- Environmentally friendly: Dry film generates less waste compared to liquid photoresist and does not require solvents for cleaning.
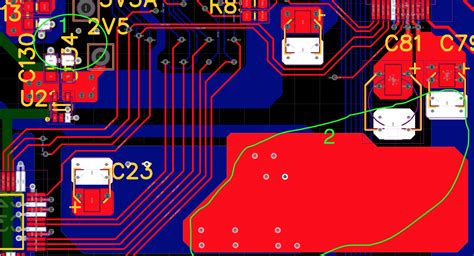
Dry Film Imaging Process
The dry film imaging process consists of several steps:
- Surface preparation
- Lamination
- Exposure
- Development
- Etching
- Stripping
1. Surface Preparation
Before applying the dry film, the copper surface must be clean, dry, and free of contaminants. The PCB is typically cleaned with a mild abrasive or chemical cleaner to remove any oxides or residues. The surface is then dried with compressed air or a lint-free cloth.
2. Lamination
The dry film is applied to the PCB using a laminator, which consists of heated rollers that press the film onto the copper surface. The lamination temperature, pressure, and speed are critical parameters that affect the quality of the lamination.
Parameter | Typical Value |
---|---|
Temperature | 100-120°C (212-248°F) |
Pressure | 2-3 kg/cm² (28-43 psi) |
Speed | 1-2 m/min (3-6 ft/min) |
After lamination, the protective polyethylene film is removed, exposing the photoresist layer.
3. Exposure
The PCB is then exposed to UV light through a photomask or artwork that contains the circuit pattern. The photomask is typically a transparent film with opaque areas that block the UV light from reaching the photoresist.
The exposure time and intensity depend on the thickness and type of photoresist used. Overexposure can cause loss of resolution, while underexposure can result in incomplete development.
Photoresist Thickness | Exposure Energy |
---|---|
38 microns (0.0015 inches) | 30-40 mJ/cm² |
50 microns (0.002 inches) | 40-50 mJ/cm² |
75 microns (0.003 inches) | 50-60 mJ/cm² |
4. Development
After exposure, the PCB is immersed in a developer solution, which dissolves the unexposed areas of the photoresist, revealing the copper surface underneath. The developer is typically an aqueous alkaline solution, such as sodium carbonate or potassium carbonate.
The development time and temperature depend on the type of photoresist and developer used. Overdevelopment can cause loss of resolution, while underdevelopment can result in incomplete removal of the unexposed photoresist.
Parameter | Typical Value |
---|---|
Temperature | 20-30°C (68-86°F) |
Time | 1-2 minutes |
After development, the PCB is rinsed with water to remove any remaining developer and dried with compressed air.
5. Etching
The exposed copper areas are then etched away using a chemical etchant, such as ferric chloride or ammonium persulfate. The photoresist acts as a protective mask, preventing the etchant from attacking the copper underneath.
The etching time and temperature depend on the type of etchant and the thickness of the copper layer. Overetching can cause undercutting of the circuit traces, while underetching can result in incomplete removal of the unwanted copper.
Parameter | Typical Value |
---|---|
Temperature | 30-50°C (86-122°F) |
Time | 1-5 minutes |
After etching, the PCB is rinsed with water to remove any remaining etchant and dried with compressed air.
6. Stripping
Finally, the remaining photoresist is stripped away using a chemical stripper, such as sodium hydroxide or potassium hydroxide. The stripper dissolves the photoresist, leaving the copper circuit pattern intact.
The stripping time and temperature depend on the type of photoresist and stripper used. Overstripping can cause damage to the copper surface, while understripping can result in incomplete removal of the photoresist.
Parameter | Typical Value |
---|---|
Temperature | 50-70°C (122-158°F) |
Time | 1-5 minutes |
After stripping, the PCB is rinsed with water and dried with compressed air. The PCB is now ready for further processing, such as drilling, plating, and solder mask application.
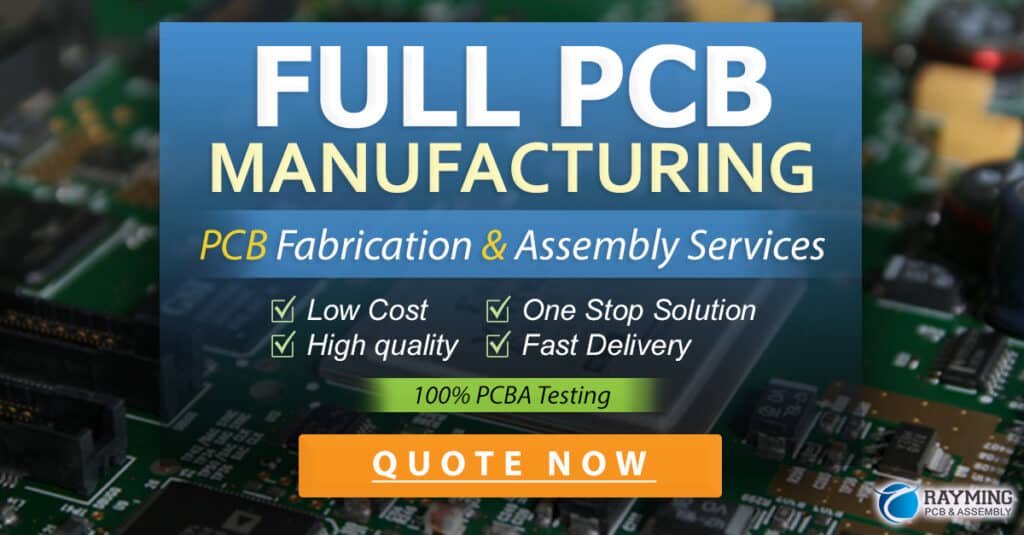
Best Practices for Dry Film Imaging
To achieve the best results with dry film imaging, follow these best practices:
- Use a clean and dry work area to prevent contamination of the PCB or photoresist.
- Handle the dry film with clean gloves to avoid fingerprints or other contaminants.
- Follow the manufacturer’s recommendations for lamination temperature, pressure, and speed.
- Use a high-quality photomask or artwork with sharp edges and high contrast.
- Optimize the exposure time and intensity for the specific photoresist and PCB design.
- Control the development time and temperature to ensure complete removal of the unexposed photoresist without overdevelopment.
- Monitor the etching process closely to prevent undercutting or overetching of the circuit traces.
- Use fresh developer and stripper solutions to ensure consistent results.
- Rinse the PCB thoroughly after each step to remove any residual chemicals.
- Store the dry film in a cool, dry place away from direct sunlight and heat sources.
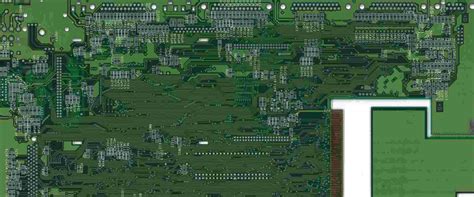
Troubleshooting Common Issues
Despite following best practices, issues can still arise during the dry film imaging process. Here are some common problems and their solutions:
Problem | Cause | Solution |
---|---|---|
Poor adhesion | Contaminated or oxidized copper surface | Clean and dry the surface thoroughly before lamination |
Incomplete development | Underexposure or underdevelopment | Increase exposure time or development time/temperature |
Loss of resolution | Overexposure or overdevelopment | Decrease exposure time or development time/temperature |
Undercut circuit traces | Overetching | Reduce etching time or temperature |
Incomplete stripping | Understripping | Increase stripping time or temperature |
Blistering or lifting of photoresist | Lamination temperature too high or too low | Adjust lamination temperature according to manufacturer’s recommendations |
By troubleshooting these issues and adjusting the process parameters accordingly, you can achieve high-quality PCB imaging with dry film photoresist.
Frequently Asked Questions (FAQ)
-
Q: What is the shelf life of dry film photoresist?
A: The shelf life of dry film photoresist is typically 6-12 months when stored at room temperature (20-25°C or 68-77°F) in a dry, dark place. However, it is best to consult the manufacturer’s specifications for the specific product. -
Q: Can dry film photoresist be used for double-sided PCBs?
A: Yes, dry film photoresist can be used for double-sided PCBs. However, the process is more complex and requires careful alignment of the photomasks on both sides of the PCB. -
Q: What is the difference between positive and negative dry film photoresist?
A: Positive photoresist becomes soluble in the developer solution when exposed to UV light, while negative photoresist becomes insoluble. Positive photoresist is more common for PCB imaging due to its higher resolution and easier stripping. -
Q: Can dry film photoresist be reused?
A: No, dry film photoresist is a single-use material and cannot be reused after exposure and development. -
Q: What is the typical thickness of dry film photoresist?
A: Dry film photoresist is available in thicknesses ranging from 15 to 75 microns (0.0006 to 0.003 inches). The most common thicknesses for PCB imaging are 38 and 50 microns (0.0015 and 0.002 inches).
Conclusion
Dry film imaging is a reliable and cost-effective method for PCB imaging, offering high resolution, excellent adhesion, and ease of use. By following best practices and troubleshooting common issues, you can achieve consistent and high-quality results.
As PCB designs become more complex and miniaturized, dry film imaging will continue to play a crucial role in the PCB fabrication process. With ongoing advancements in photoresist materials and processing equipment, we can expect to see even higher resolutions and faster throughput in the future.
No responses yet