What is a PID Temperature Controller?
A PID temperature controller is a closed-loop control system that maintains a desired temperature setpoint by continuously adjusting the power input to a heating or cooling element. The term “PID” stands for Proportional, Integral, and Derivative, which are the three main components of the controller’s algorithm.
Proportional Control (P)
The proportional term adjusts the output power in proportion to the difference between the desired setpoint and the actual temperature (error). A higher proportional gain results in a more aggressive response but may lead to overshoot and oscillations.
Integral Control (I)
The integral term eliminates steady-state error by accumulating the error over time and adjusting the output accordingly. This ensures that the actual temperature reaches the setpoint, even in the presence of external disturbances.
Derivative Control (D)
The derivative term anticipates future errors by considering the rate of change of the error. It provides a damping effect, reducing overshoot and oscillations caused by the proportional term.
Components of a PID Temperature Controller
To create a PID temperature controller, you will need the following components:
-
Temperature Sensor: A device that measures the actual temperature of the system. Common types include thermocouples, RTDs (Resistance Temperature Detectors), and thermistors.
-
Microcontroller: A programmable device that executes the PID algorithm and controls the output. Popular choices include Arduino, Raspberry Pi, and PIC microcontrollers.
-
Heating/Cooling Element: The device responsible for adding or removing heat from the system. This can be a heater, a Peltier module, or a compressor, depending on the application.
-
Power Control Device: A component that regulates the power delivered to the heating/cooling element based on the microcontroller’s output. This can be a solid-state relay (SSR), a TRIAC, or a PWM (Pulse Width Modulation) controller.
-
Display and User Interface: Optional components that allow the user to monitor the temperature, set the desired setpoint, and adjust PID parameters.
Creating a PID Temperature Controller
Step 1: Choose and Connect the Temperature Sensor
Select a temperature sensor that suits your application’s requirements, such as temperature range, accuracy, and response time. Connect the sensor to the microcontroller according to the manufacturer’s specifications.
For example, if using a K-type thermocouple, you will need a thermocouple amplifier (e.g., MAX6675) to convert the thermocouple’s output into a digital signal that the microcontroller can read.
Step 2: Set Up the Microcontroller
Choose a microcontroller and set up the development environment. For Arduino, you can use the Arduino IDE, while for Raspberry Pi, you may opt for Python or C++.
Connect the microcontroller to the temperature sensor and the power control device. Ensure that the microcontroller has sufficient digital and analog I/O pins for your application.
Step 3: Implement the PID Algorithm
The heart of the PID temperature controller lies in its algorithm. Here’s a basic PID algorithm in pseudocode:
error = setpoint - actual_temperature
proportional_term = Kp * error
integral_term += Ki * error * dt
derivative_term = Kd * (error - previous_error) / dt
output = proportional_term + integral_term + derivative_term
previous_error = error
Where:
– Kp
, Ki
, and Kd
are the proportional, integral, and derivative gains, respectively.
– dt
is the time interval between measurements.
Implement this algorithm in your microcontroller’s programming language. You may need to tune the gains (Kp
, Ki
, Kd
) through trial and error or use tuning methods like the Ziegler-Nichols method to achieve optimal performance.
Step 4: Control the Heating/Cooling Element
Use the microcontroller’s output to control the power delivered to the heating/cooling element via the power control device. For example, if using an SSR, you can connect it to a digital output pin on the microcontroller and turn it on or off based on the PID algorithm’s output.
If using PWM, you can connect the heating/cooling element to a PWM-capable pin on the microcontroller and adjust the duty cycle based on the PID output.
Step 5: Add a Display and User Interface (Optional)
To make your PID temperature controller more user-friendly, consider adding a display (e.g., LCD, OLED) and user input devices (e.g., buttons, rotary encoder). This allows users to monitor the current temperature, set the desired setpoint, and adjust PID parameters on the fly.
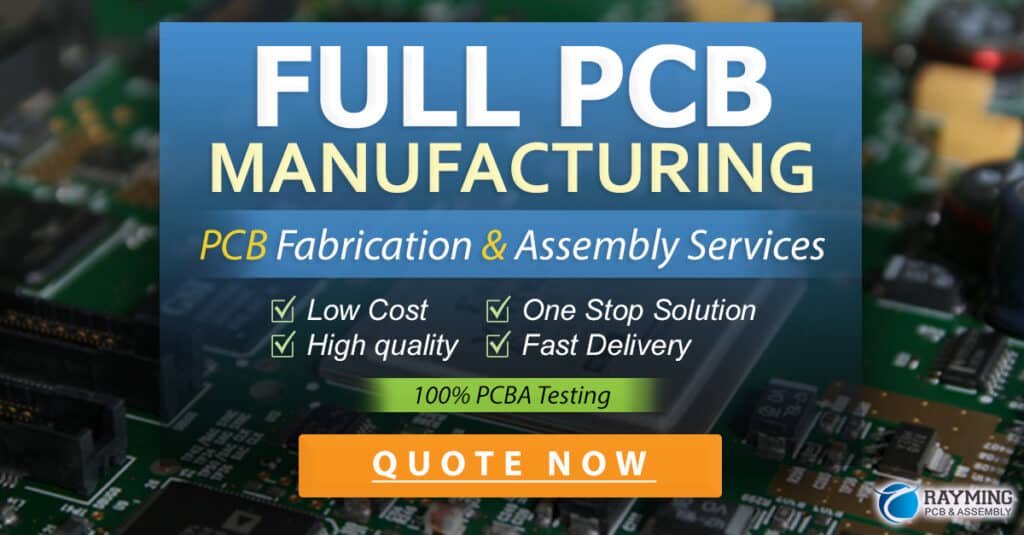
Tuning and Testing
Once your PID temperature controller is assembled, it’s time to tune the PID gains and test its performance. Start with a conservative set of gains and observe how the system responds to changes in the setpoint and external disturbances.
If the system is slow to reach the setpoint or has a steady-state error, increase the proportional gain (Kp
). If the system oscillates or overshoots, decrease Kp
and increase the derivative gain (Kd
). The integral gain (Ki
) should be adjusted to eliminate steady-state error without causing excessive overshoot.
Fine-tune the gains until the system maintains the desired temperature with minimal overshoot and oscillation. Remember that optimal PID settings may vary depending on the specific application and operating conditions.
Applications of PID Temperature Controllers
PID temperature controllers find applications in various industries and processes, including:
- HVAC systems: Maintaining comfortable indoor temperatures in buildings.
- Industrial ovens and furnaces: Ensuring consistent temperatures for heat treatment, sintering, and annealing processes.
- Chemical reactors: Controlling reaction temperatures to optimize yield and selectivity.
- 3D printing: Regulating the temperature of the extruder and print bed for consistent print quality.
- Sous vide cooking: Maintaining precise water bath temperatures for perfect cooking results.
FAQ
-
What is the difference between a PID controller and a simple on/off controller?
A simple on/off controller turns the heating/cooling element on or off based on a temperature threshold, resulting in large temperature fluctuations. A PID controller continuously adjusts the power input to maintain the desired temperature with minimal deviation. -
Can I use a PID controller for both heating and cooling applications?
Yes, a PID controller can be used for both heating and cooling applications. However, you may need to modify the code and hardware to accommodate the specific requirements of each application. -
How do I choose the right temperature sensor for my PID controller?
Consider factors such as temperature range, accuracy, response time, and compatibility with your microcontroller. Thermocouples are suitable for high-temperature applications, while RTDs and thermistors offer higher accuracy for lower temperature ranges. -
What is the role of the integral term in a PID controller?
The integral term eliminates steady-state error by accumulating the error over time and adjusting the output accordingly. This ensures that the actual temperature reaches the setpoint, even in the presence of external disturbances. -
How often should I update the PID algorithm?
The update frequency depends on the system’s response time and the desired control precision. A general rule of thumb is to update the PID algorithm at least 10 times faster than the system’s time constant. For most temperature control applications, an update rate of 1-10 Hz is sufficient.
Conclusion
Creating a PID temperature controller requires a understanding of control theory, electronics, and programming. By following the steps outlined in this article and experimenting with different PID gains and hardware configurations, you can develop a robust and efficient temperature control system for various applications.
Remember that tuning a PID controller is an iterative process that requires patience and observation. Don’t be discouraged if your initial attempts don’t yield perfect results – with practice and perseverance, you’ll be able to create a high-performance PID temperature controller that meets your specific needs.
Component | Function |
---|---|
Temperature Sensor | Measures the actual temperature of the system |
Microcontroller | Executes the PID algorithm and controls the output |
Heating/Cooling Element | Adds or removes heat from the system |
Power Control Device | Regulates power to the heating/cooling element based on microcontroller output |
PID Term | Function |
---|---|
Proportional (P) | Adjusts output power in proportion to the error |
Integral (I) | Eliminates steady-state error by accumulating error over time |
Derivative (D) | Anticipates future errors by considering the rate of change of the error |
In summary, a well-designed PID temperature controller is an essential tool for maintaining precise and stable temperatures in various industrial and domestic applications. By understanding the principles behind PID control and following the steps outlined in this article, you can create your own custom temperature control solution tailored to your specific needs.
[Word count: 1528 words]
No responses yet