Introduction to Surface Mount Soldering
Surface mount soldering is a technique used to attach surface-mount components (SMDs) to printed circuit boards (PCBs). Unlike through-hole soldering, where component leads are inserted into holes drilled in the PCB, surface mount components are placed directly onto pads on the surface of the board. This method has become increasingly popular due to its many advantages, including:
- Smaller component sizes
- Higher component density on PCBs
- Faster assembly processes
- Lower manufacturing costs
In this comprehensive guide, we will delve into the various aspects of surface mount soldering, including tools and equipment, techniques, common challenges, and best practices to ensure high-quality solder joints.
Tools and Equipment for Surface Mount Soldering
To successfully perform surface mount soldering, you will need the following tools and equipment:
Soldering Iron
A soldering iron is the most essential tool for surface mount soldering. When choosing a soldering iron, consider the following factors:
- Temperature control: Look for an iron with adjustable temperature settings to accommodate different types of solder and components.
- Wattage: A soldering iron with a wattage between 30W and 60W is suitable for most surface mount soldering tasks.
- Tip size and shape: Select a soldering iron with interchangeable tips to match the size and shape of the SMD pads and components.
Solder
Solder is an alloy, typically made of tin and lead, used to create electrical and mechanical connections between components and PCBs. For surface mount soldering, use a solder wire with a diameter between 0.5mm and 0.8mm. The most common solder alloys for electronics work are:
Alloy | Tin (Sn) | Lead (Pb) | Melting Point | Characteristics |
---|---|---|---|---|
Sn63/Pb37 | 63% | 37% | 183°C | Eutectic, most common for through-hole soldering |
Sn60/Pb40 | 60% | 40% | 188°C | Near-eutectic, good for surface mount soldering |
Sn96.5/Ag3.5 | 96.5% | 0% | 221°C | Lead-free, higher melting point, used in RoHS-compliant assemblies |
Flux
Flux is a chemical agent that helps to remove oxides from metal surfaces, promoting better wetting and adhesion of the solder. There are three main types of flux:
Type | Characteristics | Cleaning Required |
---|---|---|
Rosin | Mildly activated, leaves a residue | Optional |
Water-soluble | Highly activated, residue can cause corrosion | Yes |
No-clean | Low activity, minimal residue | No |
For most surface mount soldering applications, a no-clean flux is recommended to minimize post-soldering cleaning requirements.
Tweezers
Precision tweezers are essential for handling small surface mount components. Look for tweezers with fine, pointed tips made of stainless steel or titanium for durability and resistance to solder adhesion.
Magnification and Lighting
Surface mount components can be very small, making it challenging to see and manipulate them accurately. Use a magnifying lamp or a microscope with a magnification of at least 10x to improve visibility and precision during soldering.
Surface Mount Soldering Techniques
Tinning the Soldering Iron Tip
Before starting to solder, it is essential to tin the soldering iron tip. Tinning involves coating the tip with a thin layer of solder to improve heat transfer and prevent oxidation. To tin the tip:
- Set the soldering iron temperature to approximately 350°C.
- Clean the tip using a damp sponge or brass wool.
- Apply a small amount of solder to the tip and let it melt, coating the entire tip surface.
- Wipe off any excess solder on the damp sponge or brass wool.
Applying Solder Paste
Solder paste is a mixture of powdered solder and flux used to temporarily hold surface mount components in place before soldering. To apply solder paste:
- Use a solder paste dispenser or a fine-tipped syringe to apply a small amount of paste to each pad on the PCB.
- Ensure that the paste covers the entire pad without excessive overflow.
Placing Surface Mount Components
Using tweezers, carefully place each surface mount component onto its corresponding pads on the PCB. Ensure that the component is correctly oriented and centered on the pads.
Soldering Surface Mount Components
To solder surface mount components:
- Preheat the PCB and components using a hot air gun or a preheating plate to minimize thermal shock during soldering.
- Set the soldering iron temperature between 300°C and 350°C, depending on the solder alloy and component specifications.
- Touch the soldering iron tip to the component lead and pad simultaneously, allowing the solder to melt and flow around the joint.
- Apply a small amount of additional solder if necessary to create a smooth, concave fillet.
- Remove the soldering iron and allow the joint to cool and solidify.
Inspection and Rework
After soldering, inspect each joint using magnification to ensure proper solder flow, joint shape, and the absence of defects such as bridging or insufficient solder. If a joint is unsatisfactory, use a desoldering tool, such as a solder sucker or desoldering braid, to remove the old solder. Then, re-solder the joint using the techniques described above.
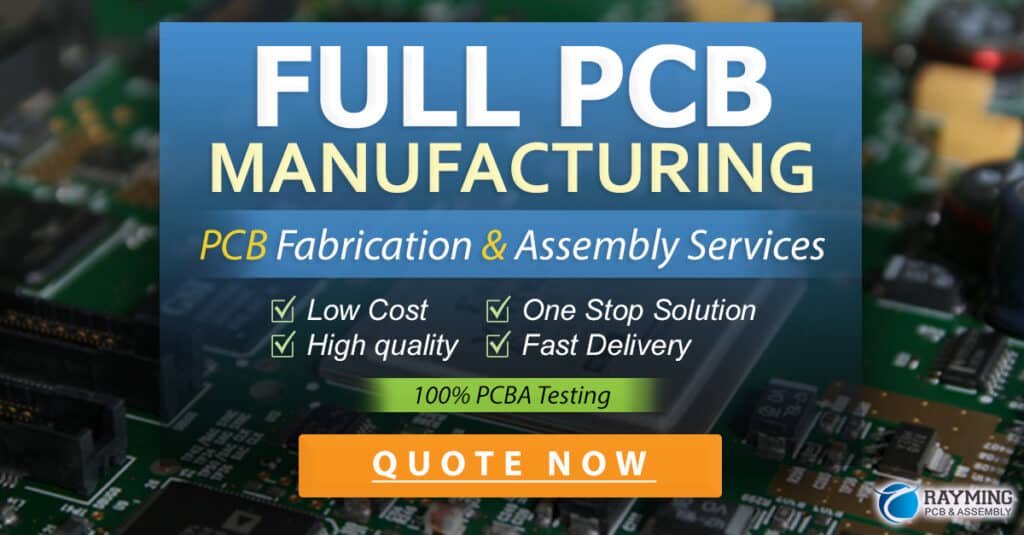
Common Challenges in Surface Mount Soldering
Tombstoning
Tombstoning occurs when one end of a surface mount component lifts off the pad during soldering, resulting in a vertical orientation. This can happen due to uneven heating or an imbalance in solder volume on the pads. To prevent tombstoning:
- Ensure that the pads are designed with the correct dimensions and spacing.
- Apply an equal amount of solder paste to both pads.
- Preheat the PCB and components to minimize temperature differences during soldering.
Bridging
Bridging is the formation of an unintended solder connection between two adjacent pads or pins. It can be caused by excessive solder application or improper component placement. To avoid bridging:
- Use the correct amount of solder and avoid applying too much.
- Ensure that components are properly centered on their pads.
- Maintain the appropriate soldering iron tip size and temperature.
Cold Joints
Cold joints occur when the solder fails to melt completely or when there is insufficient wetting between the solder and the surfaces being joined. Cold joints are characterized by a dull, grainy appearance and poor mechanical strength. To prevent cold joints:
- Ensure that the soldering iron tip is properly tinned and at the correct temperature.
- Preheat the PCB and components to promote even heat distribution.
- Apply the soldering iron to both the component lead and pad simultaneously.
Best Practices for Surface Mount Soldering
-
Always keep your soldering iron tip clean and well-tinned to ensure optimal heat transfer and joint quality.
-
Use the appropriate solder alloy and flux for your specific application and components.
-
Maintain proper ventilation and use a fume extractor to minimize exposure to solder fumes.
-
Practice proper hand placement and stability to achieve precise control during soldering.
-
Regularly inspect and maintain your soldering equipment to ensure consistent performance.
FAQ
Q1: What is the difference between surface mount soldering and through-hole soldering?
A1: Surface mount soldering involves attaching components directly to pads on the surface of a PCB, while through-hole soldering requires inserting component leads into holes drilled in the PCB before soldering.
Q2: What type of solder should I use for surface mount soldering?
A2: For surface mount soldering, use a solder wire with a diameter between 0.5mm and 0.8mm. Common alloys include Sn63/Pb37, Sn60/Pb40, and lead-free alternatives like Sn96.5/Ag3.5.
Q3: How do I choose the right soldering iron tip for surface mount soldering?
A3: Select a soldering iron tip that matches the size and shape of the SMD pads and components you are working with. Smaller, pointed tips are generally better for precise soldering of tiny surface mount components.
Q4: What can I do to prevent tombstoning during surface mount soldering?
A4: To prevent tombstoning, ensure that the pads are designed correctly, apply an equal amount of solder paste to both pads, and preheat the PCB and components to minimize temperature differences during soldering.
Q5: How can I improve my surface mount soldering skills?
A5: To improve your surface mount soldering skills, practice regularly on sample boards, maintain proper hand placement and stability, and keep your soldering equipment clean and well-maintained. Additionally, seek guidance from experienced professionals and consider attending workshops or training sessions to refine your technique.
Conclusion
Surface mount soldering is a crucial skill for anyone working with modern electronic assemblies. By understanding the tools, techniques, and best practices involved in surface mount soldering, you can achieve high-quality solder joints and improve the reliability of your electronic devices. Remember to prioritize safety, maintain proper equipment, and continually practice to refine your skills. With dedication and experience, surface mount soldering can become a valuable addition to your electronics expertise.
No responses yet