Introduction to PCB DFM
PCB DFM, or Design for Manufacturability, is a crucial aspect of the printed circuit board (PCB) fabrication process. It involves designing PCBs in a way that optimizes their manufacturability, reliability, and cost-effectiveness. By incorporating DFM principles into the design process, PCB designers can ensure that their boards are easy to manufacture, test, and assemble, while minimizing the risk of defects and delays.
In this article, we will explore the top 9 advantages of PCB fabrication assisted by DFM. We will discuss how DFM can help improve the quality, reliability, and cost-effectiveness of PCBs, and how it can streamline the manufacturing process from start to finish.
Advantage 1: Reduced Manufacturing Costs
One of the primary benefits of incorporating DFM into the PCB fabrication process is the reduction of manufacturing costs. By designing PCBs with manufacturability in mind, designers can minimize the need for expensive materials, complex processes, and specialized equipment. This can help reduce the overall cost of production and make PCBs more affordable for end-users.
Cost-Saving Design Techniques
Some cost-saving design techniques that can be implemented through DFM include:
- Using standard materials and components
- Minimizing the number of layers in the PCB
- Avoiding tight tolerances and small feature sizes
- Using larger vias and trace widths
- Minimizing the use of blind and buried vias
By following these guidelines, designers can create PCBs that are easier and cheaper to manufacture, without compromising on functionality or performance.
Advantage 2: Improved Product Quality
Another key advantage of PCB DFM is the improvement of product quality. By designing PCBs with manufacturability in mind, designers can reduce the risk of defects and errors that can occur during the fabrication process. This can help ensure that the final product meets the required specifications and performs as intended.
Quality-Enhancing Design Techniques
Some quality-enhancing design techniques that can be implemented through DFM include:
- Using appropriate trace widths and spacing to minimize signal interference
- Avoiding sharp corners and angles that can cause stress points
- Using appropriate via sizes and placement to improve signal integrity
- Incorporating test points and other features to facilitate testing and debugging
- Using appropriate solder mask and silkscreen to improve assembly and identification
By following these guidelines, designers can create PCBs that are more reliable, durable, and consistent in quality.
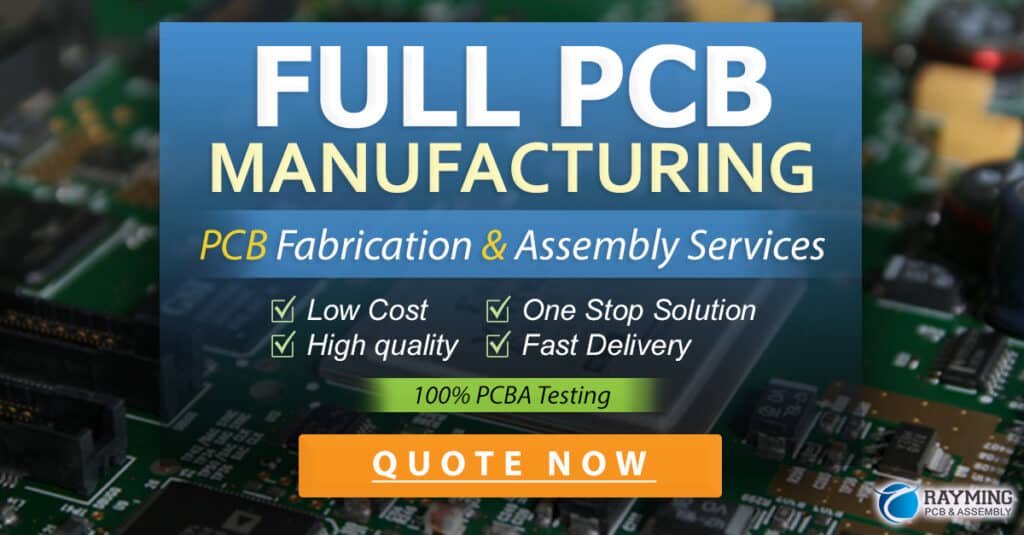
Advantage 3: Faster Time-to-Market
PCB DFM can also help accelerate the time-to-market for new products. By designing PCBs with manufacturability in mind, designers can avoid delays and setbacks that can occur during the fabrication process. This can help ensure that products are delivered to customers on time and within budget.
Time-Saving Design Techniques
Some time-saving design techniques that can be implemented through DFM include:
- Using standard components and materials that are readily available
- Avoiding complex or custom designs that require specialized equipment or processes
- Using automated design tools and simulations to identify and resolve potential issues early in the design process
- Collaborating closely with manufacturers to ensure that designs are optimized for their specific capabilities and constraints
By following these guidelines, designers can streamline the PCB fabrication process and reduce the time and effort required to bring new products to market.
Advantage 4: Enhanced Reliability
PCB DFM can also help enhance the reliability of PCBs over their entire lifecycle. By designing PCBs with reliability in mind, designers can ensure that they can withstand the rigors of use and perform consistently over time.
Reliability-Enhancing Design Techniques
Some reliability-enhancing design techniques that can be implemented through DFM include:
- Using appropriate materials and coatings to protect against environmental factors such as moisture, heat, and corrosion
- Incorporating redundancy and fail-safe features to minimize the impact of component failures
- Using stress relief techniques such as underfill and conformal coating to reduce mechanical stress on components
- Performing thorough testing and validation to identify and address potential failure modes
By following these guidelines, designers can create PCBs that are more reliable and have a longer useful life, reducing the need for repairs and replacements.
Advantage 5: Improved Manufacturability
PCB DFM is all about improving the manufacturability of PCBs. By designing PCBs with manufacturability in mind, designers can ensure that they are easy to fabricate, assemble, and test, using standard processes and equipment.
Manufacturability-Enhancing Design Techniques
Some manufacturability-enhancing design techniques that can be implemented through DFM include:
- Using standard panel sizes and layouts to minimize waste and optimize material usage
- Avoiding tight tolerances and small feature sizes that require specialized equipment or processes
- Using appropriate pad sizes and shapes to facilitate soldering and assembly
- Incorporating fiducial marks and other alignment features to ensure accurate placement of components
- Using appropriate labeling and markings to facilitate identification and traceability
By following these guidelines, designers can create PCBs that are easier and more cost-effective to manufacture, reducing the risk of defects and delays.
Advantage 6: Reduced Environmental Impact
PCB DFM can also help reduce the environmental impact of PCB fabrication. By designing PCBs with sustainability in mind, designers can minimize the use of hazardous materials, reduce waste and emissions, and promote recycling and reuse.
Sustainability-Enhancing Design Techniques
Some sustainability-enhancing design techniques that can be implemented through DFM include:
- Using lead-free and halogen-free materials to minimize toxicity and environmental impact
- Minimizing the use of precious metals and rare earth elements to reduce resource depletion
- Designing PCBs for easy disassembly and recycling at end-of-life
- Using renewable energy sources and efficient manufacturing processes to reduce carbon footprint
- Collaborating with suppliers and manufacturers to promote sustainable practices throughout the supply chain
By following these guidelines, designers can create PCBs that are more environmentally friendly and socially responsible, while still meeting the required performance and cost targets.
Advantage 7: Enhanced Collaboration and Communication
PCB DFM can also help enhance collaboration and communication between designers, manufacturers, and other stakeholders involved in the PCB fabrication process. By using a common language and set of guidelines, DFM can help ensure that everyone is on the same page and working towards the same goals.
Collaboration-Enhancing Design Techniques
Some collaboration-enhancing design techniques that can be implemented through DFM include:
- Using standardized file formats and data exchange protocols to facilitate communication and data sharing
- Incorporating feedback and input from manufacturers and assemblers early in the design process to identify and address potential issues
- Using collaborative design tools and platforms to enable real-time collaboration and version control
- Establishing clear roles and responsibilities for each stakeholder involved in the PCB fabrication process
- Conducting regular reviews and assessments to identify opportunities for improvement and optimization
By following these guidelines, designers can foster a culture of collaboration and continuous improvement, leading to better outcomes and more successful projects.
Advantage 8: Improved Supply Chain Management
PCB DFM can also help improve supply chain management for PCB fabrication. By designing PCBs with the supply chain in mind, designers can ensure that the necessary materials, components, and resources are available when and where they are needed.
Supply Chain-Enhancing Design Techniques
Some supply chain-enhancing design techniques that can be implemented through DFM include:
- Using standard components and materials that are widely available and have multiple sources
- Avoiding custom or proprietary components that may have limited availability or long lead times
- Incorporating supply chain considerations into the design process, such as lead times, minimum order quantities, and inventory levels
- Collaborating with suppliers and manufacturers to optimize inventory management and logistics
- Using data analytics and forecasting tools to predict demand and optimize supply chain performance
By following these guidelines, designers can create PCBs that are more resilient to supply chain disruptions and can be manufactured and delivered more efficiently and cost-effectively.
Advantage 9: Increased Customer Satisfaction
Finally, PCB DFM can help increase customer satisfaction by ensuring that PCBs meet or exceed customer expectations for quality, reliability, and performance. By designing PCBs with the end-user in mind, designers can create products that are more user-friendly, durable, and functional.
Customer-Centric Design Techniques
Some customer-centric design techniques that can be implemented through DFM include:
- Conducting user research and testing to identify customer needs and preferences
- Incorporating user feedback and suggestions into the design process
- Designing PCBs for ease of use, maintenance, and repair
- Providing clear and concise documentation and support materials to help customers use and troubleshoot PCBs
- Offering warranty and support services to ensure customer satisfaction and loyalty
By following these guidelines, designers can create PCBs that not only meet the technical requirements but also exceed customer expectations, leading to higher levels of customer satisfaction and retention.
Frequently Asked Questions (FAQ)
-
What is PCB DFM?
PCB DFM (Design for Manufacturability) is a set of guidelines and best practices for designing printed circuit boards that are optimized for manufacturability, reliability, and cost-effectiveness. -
Why is PCB DFM important?
PCB DFM is important because it helps ensure that PCBs can be manufactured efficiently and cost-effectively, while also meeting the required performance and quality standards. By incorporating DFM principles into the design process, designers can avoid costly delays, defects, and rework. -
What are some common PCB DFM guidelines?
Some common PCB DFM guidelines include using standard materials and components, minimizing the number of layers, avoiding tight tolerances and small feature sizes, using appropriate trace widths and spacing, and incorporating test points and other features to facilitate testing and debugging. -
How can PCB DFM help reduce manufacturing costs?
PCB DFM can help reduce manufacturing costs by minimizing the need for expensive materials, complex processes, and specialized equipment. By designing PCBs with manufacturability in mind, designers can create boards that are easier and cheaper to fabricate, assemble, and test. -
What are some benefits of collaborating with manufacturers during the PCB design process?
Collaborating with manufacturers during the PCB design process can help identify and address potential manufacturability issues early on, reducing the risk of delays and defects. It can also help optimize the design for the specific capabilities and constraints of the manufacturing process, leading to better outcomes and more successful projects.
Conclusion
In conclusion, PCB DFM is a powerful tool for optimizing the PCB fabrication process and ensuring the success of PCB projects. By incorporating DFM principles into the design process, designers can create PCBs that are more manufacturable, reliable, and cost-effective, while also reducing environmental impact, improving collaboration and communication, and increasing customer satisfaction.
While implementing PCB DFM may require some additional effort and resources upfront, the benefits far outweigh the costs in the long run. By embracing DFM as a core part of the PCB design process, companies can position themselves for success in an increasingly competitive and demanding market.
Advantage | Key Benefit |
---|---|
Reduced Manufacturing Costs | Lower production costs through design optimization and standardization |
Improved Product Quality | Higher reliability and consistency through defect reduction and quality control |
Faster Time-to-Market | Accelerated product development through streamlined manufacturing and reduced delays |
Enhanced Reliability | Longer product lifespan and reduced failures through robust design and testing |
Improved Manufacturability | Easier and more efficient production through design for assembly and process optimization |
Reduced Environmental Impact | More sustainable and eco-friendly products through material selection and waste reduction |
Enhanced Collaboration and Communication | Better project outcomes through improved teamwork and stakeholder alignment |
Improved Supply Chain Management | More resilient and efficient supply chain through design for availability and logistics |
Increased Customer Satisfaction | Higher customer loyalty and retention through user-centric design and superior performance |
No responses yet