Introduction to Circuit Boards
A circuit board, also known as a printed circuit board (PCB), is the backbone of modern electronic devices. It is a flat board made of insulating material, such as fiberglass or plastic, with conductive pathways etched or printed onto its surface. These pathways, called traces, connect various electronic components, such as resistors, capacitors, and integrated circuits (ICs), to create a functional electronic circuit.
Circuit boards have revolutionized the electronics industry by providing a compact, reliable, and cost-effective way to assemble electronic devices. They are found in virtually every electronic device we use today, from smartphones and computers to home appliances and automobiles.
Types of Circuit Boards
There are several types of circuit boards, each with its own unique characteristics and applications. The most common types include:
-
Single-sided PCBs: These boards have conductive traces on only one side of the insulating substrate. They are the simplest and most cost-effective type of PCB, suitable for low-complexity circuits.
-
Double-sided PCBs: These boards have conductive traces on both sides of the insulating substrate, allowing for more complex circuits and higher component density. The two sides are connected using through-hole technology or vias.
-
Multi-layer PCBs: These boards consist of multiple layers of insulating material and conductive traces, sandwiched together to form a single board. They offer the highest component density and are used in complex electronic devices, such as smartphones and computer motherboards.
-
Flexible PCBs: These boards are made of flexible insulating material, allowing them to bend and conform to various shapes. They are often used in wearable electronics and applications where space is limited.
-
Rigid-Flex PCBs: These boards combine the features of rigid and flexible PCBs, with rigid sections for mounting components and flexible sections for connecting them. They are used in applications that require both stability and flexibility, such as aerospace and military equipment.
Type of PCB | Layers | Complexity | Cost | Applications |
---|---|---|---|---|
Single-sided | 1 | Low | Low | Simple circuits, low-power devices |
Double-sided | 2 | Medium | Medium | More complex circuits, higher component density |
Multi-layer | 3+ | High | High | Complex devices, smartphones, computer motherboards |
Flexible | 1-2 | Low-Medium | Medium | Wearable electronics, space-constrained applications |
Rigid-Flex | 2+ | High | High | Aerospace, military, high-reliability applications |
PCB Design and Manufacturing Process
PCB Design
The PCB design process involves several steps, including:
-
Schematic capture: The first step is to create a schematic diagram of the electronic circuit, which shows the interconnections between components using standardized symbols.
-
Component placement: Once the schematic is complete, the components are placed on the board layout, taking into account factors such as signal integrity, power distribution, and thermal management.
-
Routing: The next step is to route the conductive traces between the components, following the schematic diagram and design rules for the specific PCB manufacturing process.
-
Design rule check (DRC): The completed board layout is checked against a set of design rules to ensure that it meets the manufacturing requirements and will function as intended.
-
Output files generation: Finally, the board layout is exported as a set of output files, such as Gerber files and drill files, which are used by the PCB manufacturer to fabricate the board.
PCB Manufacturing
The PCB manufacturing process involves several steps, including:
-
PCB fabrication: The first step is to fabricate the bare PCB, which involves creating the insulating substrate, applying the conductive traces, and drilling holes for through-hole components.
-
Solder mask application: A layer of solder mask is applied to the board to protect the conductive traces and prevent short circuits during soldering.
-
Silkscreen printing: A layer of silkscreen is printed on the board to add component labels, logos, and other markings.
-
Component assembly: The electronic components are then assembled onto the board, either manually or using automated pick-and-place machines.
-
Soldering: The assembled board is passed through a soldering machine, which applies heat and solder to the component leads and pads, creating electrical connections.
-
Inspection and testing: The completed board is inspected and tested to ensure that it meets the required specifications and functions correctly.
PCB Components and Their Functions
A typical PCB contains several types of electronic components, each with its own specific function. Some of the most common components include:
Resistors
Resistors are passive components that oppose the flow of electric current. They are used to control the current and voltage in a circuit, and to divide voltage among other components. Resistors are available in various types, such as carbon film, metal film, and wirewound, each with its own characteristics and applications.
Capacitors
Capacitors are passive components that store electric charge and release it when needed. They are used to smooth out voltage fluctuations, filter out noise, and couple AC signals between stages of a circuit. Capacitors are available in various types, such as ceramic, electrolytic, and tantalum, each with its own characteristics and applications.
Inductors
Inductors are passive components that store energy in a magnetic field when current flows through them. They are used to filter out high-frequency noise, smooth out current fluctuations, and create resonant circuits. Inductors are available in various types, such as air core, ferrite core, and toroidal, each with its own characteristics and applications.
Diodes
Diodes are semiconductor devices that allow current to flow in only one direction. They are used to rectify AC voltage into DC voltage, protect circuits from reverse voltage, and create logic gates. Diodes are available in various types, such as rectifier diodes, Zener diodes, and light-emitting diodes (LEDs).
Transistors
Transistors are semiconductor devices that can amplify or switch electronic signals. They are used to create amplifiers, oscillators, and digital logic circuits. Transistors are available in various types, such as bipolar junction transistors (BJTs) and field-effect transistors (FETs), each with its own characteristics and applications.
Integrated Circuits (ICs)
Integrated circuits are miniaturized electronic circuits that contain multiple components, such as transistors, diodes, and resistors, on a single semiconductor chip. They are used to create complex electronic functions, such as microprocessors, memory devices, and analog-to-digital converters (ADCs). ICs are available in various types, such as linear ICs, digital ICs, and mixed-signal ICs.
Component | Function | Types |
---|---|---|
Resistor | Opposes current flow, controls voltage | Carbon film, metal film, wirewound |
Capacitor | Stores and releases electric charge | Ceramic, electrolytic, tantalum |
Inductor | Stores energy in a magnetic field | Air core, ferrite core, toroidal |
Diode | Allows current flow in one direction | Rectifier, Zener, LED |
Transistor | Amplifies or switches electronic signals | Bipolar junction (BJT), field-effect (FET) |
IC | Miniaturized electronic circuit on a single chip | Linear, digital, mixed-signal |
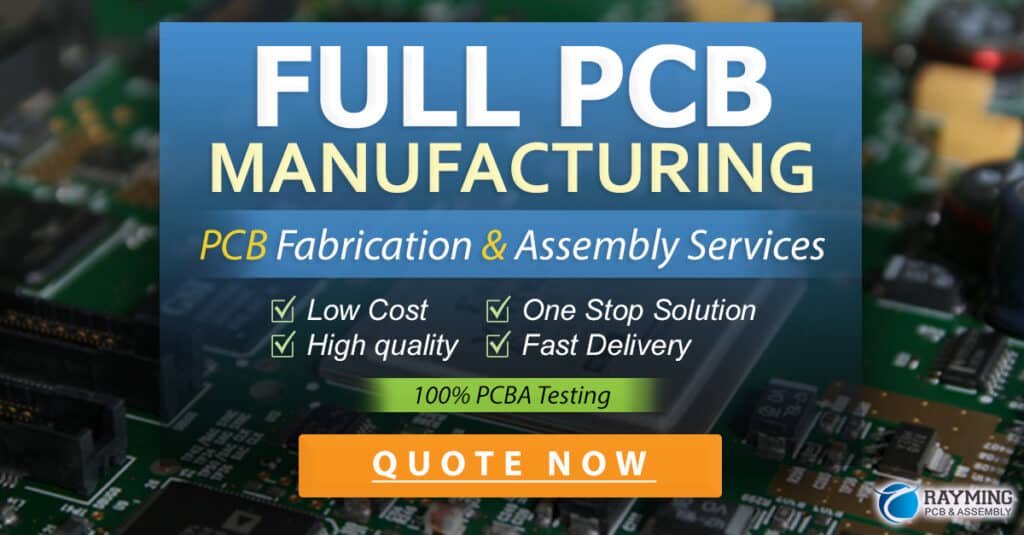
PCB Layout and Design Considerations
When designing a PCB, several factors must be considered to ensure that the board functions correctly and reliably. Some of the most important considerations include:
Signal Integrity
Signal integrity refers to the quality of the electrical signals transmitted through the PCB. Factors that can affect signal integrity include:
- Impedance matching: Ensuring that the impedance of the traces matches the impedance of the components and connectors to minimize reflections and signal distortion.
- Crosstalk: Minimizing the coupling of signals between adjacent traces to prevent interference and noise.
- Grounding and shielding: Providing adequate grounding and shielding to reduce electromagnetic interference (EMI) and improve signal quality.
Power Distribution
Power distribution refers to the way in which power is supplied to the components on the PCB. Factors that can affect power distribution include:
- Power plane: Using a solid copper plane to distribute power evenly across the board and reduce voltage drops.
- Decoupling capacitors: Placing decoupling capacitors close to the power pins of ICs to reduce noise and provide a stable power supply.
- Voltage regulators: Using voltage regulators to provide stable and accurate voltage levels to sensitive components.
Thermal Management
Thermal management refers to the way in which heat is dissipated from the components on the PCB. Factors that can affect thermal management include:
- Component placement: Placing heat-generating components, such as power transistors and voltage regulators, away from sensitive components and providing adequate spacing for heat dissipation.
- Copper pours: Using large areas of copper on the board to act as heat sinks and distribute heat evenly.
- Thermal vias: Using thermal vias to transfer heat from the components to the opposite side of the board or to an external heat sink.
Manufacturing Considerations
When designing a PCB, it is important to consider the manufacturing process and the limitations of the PCB fabrication and assembly equipment. Factors that can affect manufacturability include:
- Design rules: Adhering to the design rules specified by the PCB manufacturer, such as minimum trace width and spacing, minimum drill hole size, and minimum solder mask opening.
- Component selection: Choosing components that are compatible with the PCB fabrication and assembly process, such as surface-mount devices (SMDs) and through-hole components.
- Panelization: Designing the board to be panelized, or grouped together with other boards, to minimize waste and reduce manufacturing costs.
PCB Testing and Debugging
Once a PCB has been manufactured and assembled, it must be tested and debugged to ensure that it functions correctly and meets the required specifications. Some of the most common testing and debugging techniques include:
Visual Inspection
Visual inspection involves examining the PCB for any visible defects, such as incorrect component placement, solder bridges, or damaged traces. This can be done using a magnifying glass, microscope, or automated optical inspection (AOI) machine.
Continuity Testing
Continuity testing involves checking the electrical continuity between various points on the PCB to ensure that there are no open or short circuits. This can be done using a multimeter or a dedicated continuity tester.
Functional Testing
Functional testing involves applying power to the PCB and testing its functionality using test equipment, such as oscilloscopes, signal generators, and logic analyzers. This can be done manually or using automated test equipment (ATE).
In-Circuit Testing (ICT)
In-circuit testing involves testing the individual components on the PCB using a bed-of-nails test fixture that makes contact with the component leads. This allows the tester to measure the component values and verify that they are within the specified tolerances.
Boundary Scan Testing
Boundary scan testing, also known as JTAG testing, involves using a special test access port (TAP) on the PCB to test the interconnections between the components. This allows the tester to detect open and short circuits, as well as stuck-at faults, without the need for physical access to the component leads.
Debugging Techniques
If a problem is found during testing, various debugging techniques can be used to isolate and fix the issue. These include:
- Visual inspection: Examining the PCB for visible defects, such as solder bridges or damaged components.
- Signal tracing: Using an oscilloscope or logic analyzer to trace the signals through the circuit and identify the source of the problem.
- Component substitution: Replacing suspect components with known good ones to isolate the faulty component.
- Firmware debugging: Using debugging tools, such as JTAG debuggers or in-circuit emulators, to debug the firmware running on the PCB.
PCB Standards and Regulations
PCBs are subject to various standards and regulations that ensure their safety, reliability, and compatibility with other electronic devices. Some of the most important standards and regulations include:
IPC Standards
IPC (formerly the Institute for Printed Circuits) is a global trade association that develops standards for the electronics industry. Some of the most relevant IPC standards for PCBs include:
- IPC-2221: Generic Standard on Printed Board Design
- IPC-2222: Sectional Design Standard for Rigid Organic Printed Boards
- IPC-6012: Qualification and Performance Specification for Rigid Printed Boards
- IPC-A-600: Acceptability of Printed Boards
UL Standards
UL (Underwriters Laboratories) is a global safety certification company that develops standards for electronic products. Some of the most relevant UL standards for PCBs include:
- UL 94: Standard for Safety of Flammability of Plastic Materials for Parts in Devices and Appliances
- UL 796: Standard for Safety of Printed-Wiring Boards
RoHS Directive
The RoHS (Restriction of Hazardous Substances) Directive is a European Union regulation that restricts the use of certain hazardous substances in electronic and electrical products. These substances include lead, mercury, cadmium, hexavalent chromium, polybrominated biphenyls (PBB), and polybrominated diphenyl ethers (PBDE).
REACH Regulation
The REACH (Registration, Evaluation, Authorization and Restriction of Chemicals) Regulation is a European Union regulation that requires companies to identify and manage the risks associated with the chemicals they manufacture and use. This includes the chemicals used in the manufacture of PCBs, such as solder masks, fluxes, and cleaning agents.
Frequently Asked Questions (FAQ)
What is the difference between a PCB and a breadboard?
A PCB is a custom-designed and manufactured board that contains the electronic components and the conductive traces that connect them. A breadboard, on the other hand, is a reusable prototyping board that allows components to be inserted and connected together using jumper wires. Breadboards are used for temporary prototyping and testing, while PCBs are used for final production.
Can I design my own PCB?
Yes, it is possible to design your own PCB using PCB design software, such as Eagle, KiCad, or Altium Designer. However, designing a PCB requires knowledge of electronics, PCB layout and design principles, and the specific requirements of the PCB manufacturing process. It is recommended to start with simple designs and work your way up to more complex ones as you gain experience.
How much does it cost to manufacture a PCB?
The cost of manufacturing a PCB depends on several factors, such as the size of the board, the number of layers, the quantity ordered, and the turnaround time. For small quantities (less than 10 boards), the cost can range from $10 to $100 per board, depending on the complexity. For larger quantities (more than 100 boards), the cost can be as low as $1 to $10 per board.
What is the typical turnaround time for PCB manufacturing?
The typical turnaround time for PCB manufacturing depends on the complexity of the board and the quantity ordered. For simple, two-layer boards in small quantities, the turnaround time can be as short as 24 to 48 hours. For more complex boards or larger quantities, the turnaround time can be several weeks.
Can I reuse a PCB from an old electronic device?
In general, it is not recommended to reuse a PCB from an old electronic device, as the board may be damaged, outdated, or incompatible with your new design. Additionally, the components on the board may be difficult to remove without damaging the board or the components themselves. It is usually better to design a new PCB from scratch or use a prototyping board for testing and development.
Conclusion
PCBs are the foundation of modern electronic devices, providing a compact, reliable, and cost-effective way to assemble electronic circuits. Understanding the basics of PCB design, manufacturing, and testing is essential for anyone involved in the development or production of electronic products.
This guide has provided an overview of the different types of PCBs, the components that make up a PCB, and the design and manufacturing process. It has also covered important considerations for PCB layout and design, as well as testing and debugging techniques.
By following the principles and best practices outlined in this guide, you can design and manufacture high-quality PCBs that meet the required specifications and standards. Whether you are a hobbyist, a student, or a professional engineer, understanding PCBs is an essential skill in today’s electronic world.
No responses yet