Linear Amplifier Output Stages
One of the most straightforward methods to drive a piezoelectric load is using a linear amplifier output stage. This involves a high voltage operational amplifier or discrete transistor output stage powered from high voltage DC rails.
The amplifier takes in a low-voltage control signal and linearly amplifies it to the much higher voltage levels required by the piezo, up to 100V or more. The high voltage output signal precisely tracks the input, providing high fidelity and low distortion.
Advantages
- Simple design
- Excellent linearity
- Low output noise
- Flexible control over output waveshape
Disadvantages
- Limited efficiency, especially for high power designs
- Requires large high voltage supply rails
- High power dissipation and heat generation in amplifier stage
- Limited bandwidth compared to switching designs
Key Design Considerations
- Op amp or discrete amplifier stage selection based on voltage, current, power, and speed requirements
- Thermal management for heat dissipation
- High voltage PCB layout and component spacing
- Input signal conditioning and protection
Applications
Linear amplifiers are commonly used for low-power, high-precision piezo positioning systems and vibration control. Application examples include:
- Atomic force microscopy
- Inkjet printing heads
- Optical image stabilization
- High-end audio tweeters
- Nanopositioning stages
Switched-Mode Power Supplies
For higher power piezo systems, a switched-mode power supply (SMPS) output stage is often used. This utilizes power MOSFETs or IGBTs switching at frequencies from 10s to 100s of kHz to generate a high voltage AC waveform from a lower voltage DC input.
A step-up transformer converts the AC voltage to the required high voltage output levels. Feedback control maintains the desired output voltage or current.
Advantages
- High efficiency, commonly exceeding 90%
- Smaller size and weight than linear designs
- Can generate very high voltages
- Flexible control of output voltage and current
Disadvantages
- More complex than linear designs
- Requires careful design of high frequency magnetics
- Switching noise and EMI considerations
- Potential for switching losses and device stress
Key Design Considerations
- Power switch and rectifier diode selection
- Transformer and inductor design for desired frequency and power level
- Snubber circuits for managing switching transients
- Closed-loop control for voltage and current regulation
- Input and output filtering
- PCB layout for minimizing parasitics and EMI
Applications
SMPS piezo drivers excel in applications needing high voltage and high power, such as:
- Industrial ultrasonic cleaning
- Piezoelectric transformers
- Sonar transducers
- Medical ultrasound imaging
- Haptic feedback actuators
Resonant Converters
Resonant converters are a special class of SMPS that utilize the resonance between the piezo’s capacitance and additional inductors to shape the converter switching waveforms. This allows for soft switching, reducing losses in the power devices.
The resonant tank is typically driven at the piezo’s resonant frequency for efficient power transfer. A common topology is the series-resonant half-bridge converter.
Advantages
- Very high efficiency, up to 98%
- Reduced EMI compared to hard-switched SMPS
- Soft switching reduces MOSFET stress and losses
- Load invariant operation
Disadvantages
- Requires accurate matching to piezo resonant characteristics
- More complex control than standard SMPS
- Limited voltage gain compared to transformers
- Potential for high circulating currents
Key Design Considerations
- Resonant tank component selection for desired operating point
- Switching frequency control and locking to piezo resonance
- MOSFET gate driver design for rapid switching
- Dead-time control to maintain soft-switching
- Short-circuit handling and protection
Applications
The high efficiency and low EMI of resonant converters makes them ideal for battery-powered, sensitive, or harsh-environment piezo systems, such as:
- Piezoelectric injection systems
- Portable medical devices
- Aerospace actuators
- Underwater acoustic transducers
- High-intensity focused ultrasound (HIFU) therapy
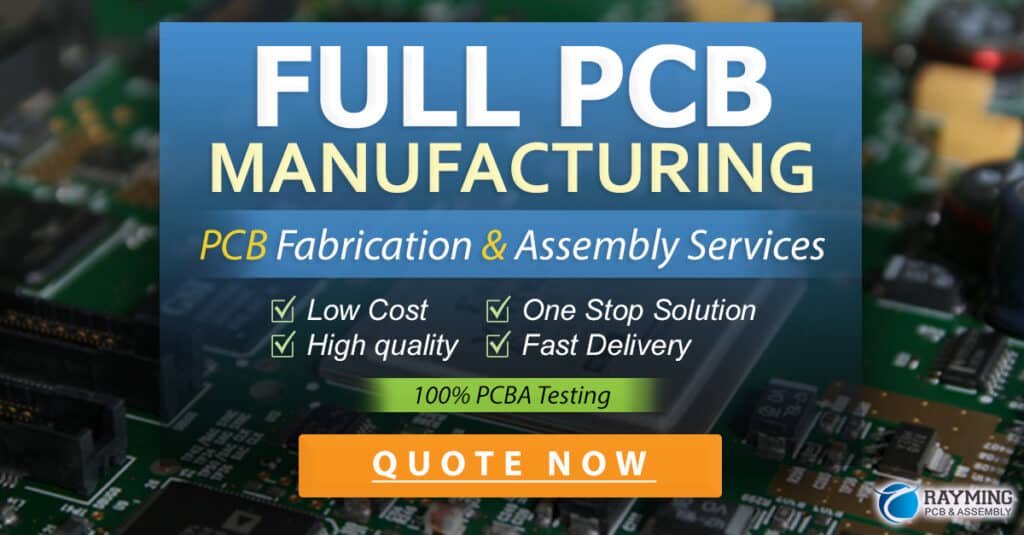
Charge Pump Circuits
Charge pump circuits use a network of switched capacitors to convert a low voltage DC input to a higher DC voltage output. The capacitors are successively charged in parallel from the input, then connected in series to supply the output. Switches are typically implemented with diodes or MOSFETs.
Charge pumps can generate an output voltage that is a multiple of the input voltage, based on the number of switching stages. For example, a Dickson charge pump doubles the voltage with each stage.
Advantages
- Simple, low-cost design
- Minimal EMI concerns
- Can operate from very low input voltages
- Easy to implement multiple outputs
Disadvantages
- Limited maximum output voltage and power
- Requires large capacitor values for high power
- Poor load regulation
- Large output voltage ripple
Key Design Considerations
- Switching device and capacitor selection
- Multistage design for desired output voltage
- Switching control and clocking
- Output filtering and buffering
- Protection from reverse voltages
Applications
Charge pumps are best suited for low-power, low-voltage, battery-operated piezo systems, such as:
- MEMS microphones and microspeakers
- Piezoelectric energy harvesting
- Portable piezo sensors
- Low-power haptic feedback
- EEPROM programming voltages
Comparison Table
Technology | Voltage Range | Power Range | Efficiency | Complexity | EMI |
---|---|---|---|---|---|
Linear Amplifier | Low to High | Low | Low | Low | Low |
SMPS | Medium to Very High | Medium to High | High | Medium | Medium |
Resonant Converter | Medium to High | Medium to High | Very High | High | Low |
Charge Pump | Low to Medium | Very Low to Low | Medium | Low | Very Low |
FAQ
Q1: How do I select the best Piezo Drive Circuit technology for my application?
A1: The key factors to consider are your piezo voltage and power requirements, desired efficiency, circuit complexity, EMI sensitivity, and cost targets. Use the comparison table as a starting point, then dive into the advantages and applications for each technology to find the best fit.
Q2: Can I use a regular op amp to drive a piezo element?
A2: It depends on your voltage and current requirements. Many piezo applications need voltage swings higher than the output range of typical op amps. You’ll likely need a specialized high voltage op amp or a discrete component amplifier stage. Be sure to check the piezo’s specifications.
Q3: What is the main advantage of resonant converters over regular switched-mode designs?
A3: Resonant converters operate the switching devices under soft-switching conditions, either zero-voltage switching (ZVS) or zero-current switching (ZCS). This greatly reduces the switching losses and device stresses compared to the hard-switching used in conventional SMPS designs. Resonant topologies can achieve very high efficiencies.
Q4: How can I reduce the EMI from my piezo drive circuit?
A4: Some effective techniques to reduce EMI include:
– Using soft-switching resonant converter topologies
– Slowing switching transition speeds, consistent with efficiency targets
– Implementing snubbers and clamps on switching waveforms
– Minimizing high-frequency loop areas in the PCB layout
– Liberal use of power supply decoupling and filtering
– Shielding of sensitive circuits
Q5: What is the biggest challenge when designing a piezo drive circuit?
A5: One of the biggest challenges is often achieving the high output voltages required by many piezo devices, which can exceed 100V, while still maintaining good efficiency, control precision, and thermal management. This requires careful selection of topologies and components rated for reliable high voltage operation.
No responses yet