Introduction to LED PCB Solutions
Light-emitting diode (LED) technology has revolutionized the lighting industry, offering energy-efficient, long-lasting, and versatile solutions for various applications. LED PCB (Printed Circuit Board) assembly plays a crucial role in the manufacturing of LED lighting products, providing a reliable and cost-effective approach to creating high-quality LED lighting solutions.
In this article, we will explore the various aspects of LED PCB Assembly, including the benefits, manufacturing process, design considerations, and applications. We will also discuss how a one-stop LED lighting PCB solution can streamline the production process and provide customers with a comprehensive and efficient service.
Benefits of LED PCB Assembly
LED PCB assembly offers numerous benefits compared to traditional lighting solutions. Some of the key advantages include:
-
Energy Efficiency: LEDs consume significantly less power than conventional lighting options, resulting in substantial energy savings and reduced environmental impact.
-
Long Lifespan: LED PCBs are designed to last for tens of thousands of hours, minimizing the need for frequent replacements and maintenance.
-
Versatility: LED PCBs can be customized to suit various applications, from small-scale indicators to large-scale illumination projects.
-
Improved Heat Dissipation: PCBs provide an efficient means of dissipating heat generated by LEDs, ensuring optimal performance and longevity.
-
Compact Design: LED PCBs allow for the creation of compact and lightweight lighting solutions, making them ideal for space-constrained applications.
LED PCB Manufacturing Process
The LED PCB manufacturing process involves several key steps to ensure the production of high-quality and reliable LED lighting solutions. These steps include:
1. PCB Design and Layout
The first step in LED PCB manufacturing is the design and layout of the PCB. This involves creating a schematic diagram and a PCB layout using specialized software tools. The design must take into account various factors, such as the number and type of LEDs, power requirements, heat dissipation, and mechanical constraints.
2. PCB Fabrication
Once the design is finalized, the PCB is fabricated using a multi-step process that includes:
- Copper Clad Lamination: A layer of copper is laminated onto the surface of the PCB substrate material.
- Drilling: Holes are drilled into the PCB to accommodate the LED components and other electronic parts.
- Patterning: The copper layer is patterned using a photolithographic process to create the desired circuit traces.
- Plating: Additional copper is plated onto the circuit traces to increase their thickness and improve conductivity.
- Solder Mask Application: A solder mask is applied to the PCB surface to protect the circuit traces and prevent short circuits.
- Silkscreen Printing: Text and symbols are printed onto the PCB surface for identification and assembly purposes.
3. LED Mounting and Soldering
After the PCB is fabricated, the LED components are mounted onto the board using either through-hole or surface-mount technology (SMT). Through-hole LEDs have longer leads that are inserted into holes drilled in the PCB, while SMT LEDs are placed directly onto the surface of the board.
The LEDs are then soldered onto the PCB using a reflow soldering process, which involves applying solder paste to the PCB pads, placing the LEDs onto the pads, and heating the assembly in a reflow oven to melt the solder and create a permanent electrical and mechanical connection.
4. Testing and Quality Control
Once the LED PCB assembly is complete, it undergoes rigorous testing and quality control procedures to ensure that it meets the required specifications and performance standards. This may include visual inspections, electrical tests, and functional tests under various environmental conditions.
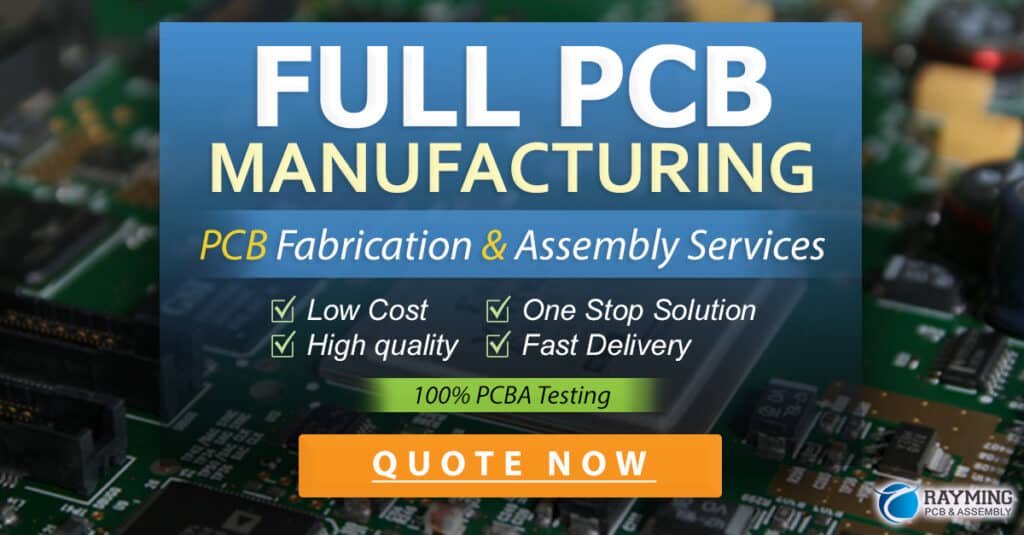
LED PCB Design Considerations
Designing an LED PCB requires careful consideration of several key factors to ensure optimal performance, reliability, and cost-effectiveness. Some of the main design considerations include:
1. LED Selection
Choosing the right type of LED is crucial for achieving the desired lighting characteristics and performance. Factors to consider include:
- Color: LEDs are available in a wide range of colors, including white, red, green, blue, and various shades in between.
- Brightness: The brightness of an LED is measured in lumens and depends on factors such as the LED package size, power rating, and efficiency.
- Viewing Angle: The viewing angle determines the spread of light emitted by the LED and can range from narrow (e.g., 15 degrees) to wide (e.g., 120 degrees).
- Forward Voltage and Current: The forward voltage and current ratings of an LED determine its power consumption and compatibility with the driving circuitry.
2. Thermal Management
Proper thermal management is essential for ensuring the long-term reliability and performance of LED PCBs. As LEDs generate heat during operation, it is important to design the PCB in a way that promotes efficient heat dissipation. This can be achieved through:
- Thermal Vias: Thermal vias are plated holes that provide a conductive path for heat to flow from the LED to the other side of the PCB, where it can be dissipated by a heatsink or other cooling solution.
- Heatsinks: Heatsinks are metal structures that are attached to the PCB to absorb and dissipate heat generated by the LEDs. They can be passive (relying on natural convection) or active (using fans or other forced cooling methods).
- Thermal Interface Materials: Thermal interface materials, such as thermal paste or thermal pads, are used to improve the thermal conductivity between the LED and the PCB or heatsink, reducing thermal resistance and promoting better heat transfer.
3. Power Supply and Driving Circuitry
LED PCBs require a stable and regulated power supply to ensure consistent and reliable operation. The power supply and driving circuitry must be designed to match the voltage and current requirements of the LEDs, while also providing protection against voltage fluctuations, current spikes, and other electrical disturbances.
Common LED driving circuits include:
- Series Resistor: A simple and cost-effective approach that uses a resistor in series with the LED to limit the current flow.
- Linear Regulator: A voltage regulator that maintains a constant voltage across the LED, providing better current regulation than a series resistor.
- Switching Regulator: A more efficient and compact solution that uses a switching circuit to regulate the current flow to the LED, allowing for higher power levels and better thermal management.
4. PCB Layout and Routing
The PCB layout and routing play a crucial role in the performance and reliability of LED PCBs. Some key considerations include:
- Component Placement: LEDs and other components should be placed in a way that minimizes the distance between them and the power supply, reduces the risk of electromagnetic interference (EMI), and facilitates efficient heat dissipation.
- Trace Width and Thickness: The width and thickness of the PCB traces should be designed to handle the expected current flow without excessive voltage drop or resistive heating.
- Ground Plane: A solid ground plane on the PCB can help to reduce EMI, improve signal integrity, and provide a low-impedance return path for the LED current.
- Isolation and Shielding: Proper isolation and shielding techniques should be used to prevent crosstalk between different sections of the PCB and to minimize the impact of external electromagnetic interference.
Applications of LED PCB Assembly
LED PCB assembly finds applications in a wide range of industries and sectors, including:
-
General Lighting: LED PCBs are used in various general lighting applications, such as indoor and outdoor lighting, task lighting, and decorative lighting.
-
Automotive Lighting: LED PCBs are increasingly used in automotive lighting applications, such as headlights, taillights, interior lighting, and instrument panel lighting.
-
Backlighting: LED PCBs are commonly used for backlighting applications in displays, signs, and other illuminated panels.
-
Medical Devices: LED PCBs are used in various medical devices, such as endoscopes, surgical lights, and phototherapy equipment.
-
Horticulture Lighting: LED PCBs are used in horticulture lighting applications to promote plant growth and development in indoor and greenhouse environments.
-
Signage and Advertising: LED PCBs are used in illuminated signs, billboards, and other advertising displays to create eye-catching and dynamic visual effects.
-
Industrial and Machine Vision: LED PCBs are used in industrial and machine vision applications, such as inspection systems, barcode scanners, and machine vision cameras.
One-Stop LED Lighting PCB Solution
A one-stop LED lighting PCB solution provides customers with a comprehensive and streamlined approach to LED PCB assembly, covering all aspects of the production process from design to delivery. The benefits of a one-stop solution include:
-
Simplified Procurement: Customers can source all their LED PCB assembly needs from a single supplier, reducing the complexity and time involved in managing multiple vendors.
-
Faster Time-to-Market: A one-stop solution can accelerate the production process by eliminating the need for multiple handoffs between different suppliers and streamlining communication and coordination.
-
Improved Quality Control: With a single supplier responsible for the entire production process, quality control can be more effectively managed and maintained, reducing the risk of defects and inconsistencies.
-
Cost Savings: A one-stop solution can offer cost savings through economies of scale, reduced logistics costs, and optimized production processes.
-
Customization and Flexibility: A one-stop supplier can offer greater customization and flexibility in meeting specific customer requirements, as they have control over the entire production chain.
Conclusion
LED PCB assembly is a critical aspect of the LED lighting industry, enabling the production of high-quality, reliable, and cost-effective LED lighting solutions. By understanding the various aspects of LED PCB assembly, including the benefits, manufacturing process, design considerations, and applications, customers can make informed decisions when selecting an LED PCB assembly provider.
A one-stop LED lighting PCB solution offers numerous advantages, including simplified procurement, faster time-to-market, improved quality control, cost savings, and greater customization and flexibility. By partnering with a reputable and experienced one-stop supplier, customers can streamline their LED lighting projects and achieve optimal results.
Frequently Asked Questions (FAQ)
-
What is LED PCB assembly?
LED PCB assembly is the process of mounting and soldering LED components onto a printed circuit board (PCB) to create a functional LED lighting module. -
What are the benefits of using LED PCBs for lighting applications?
LED PCBs offer several benefits, including energy efficiency, long lifespan, versatility, improved heat dissipation, and compact design, making them an attractive choice for various lighting applications. -
What are the key steps in the LED PCB manufacturing process?
The key steps in the LED PCB manufacturing process include PCB design and layout, PCB fabrication, LED mounting and soldering, and testing and quality control. -
What are some important design considerations for LED PCBs?
Important design considerations for LED PCBs include LED selection, thermal management, power supply and driving circuitry, and PCB layout and routing. -
What are the advantages of using a one-stop LED lighting PCB solution?
The advantages of using a one-stop LED lighting PCB solution include simplified procurement, faster time-to-market, improved quality control, cost savings, and greater customization and flexibility.
Application | Benefits of LED PCBs |
---|---|
General Lighting | Energy efficiency, long lifespan, versatility in design and color options |
Automotive Lighting | Compact size, improved safety and visibility, styling flexibility |
Backlighting | Thin profile, uniform illumination, low power consumption |
Medical Devices | Precise light control, sterility, durability |
Horticulture Lighting | Spectral control for optimal plant growth, energy efficiency |
Signage and Advertising | Dynamic and eye-catching displays, low maintenance, energy savings |
Industrial and Machine Vision | Consistent and controllable illumination, long lifespan, compact size for integration into vision systems |
No responses yet