Introduction to SolderMask and PCBs
Printed Circuit Boards (PCBs) are the backbone of modern electronics. They provide a platform for electronic components to be mounted and connected, forming a complete circuit. One of the critical elements in the PCB manufacturing process is the application of soldermask. Soldermask, also known as solder resist or solder stop, is a thin layer of polymer applied to the copper traces of a PCB to protect them from oxidation, prevent solder bridges, and provide insulation between adjacent conductive areas.
In this article, we will explore the significance of soldermask in the PCB universe, its properties, application methods, and the advancements made in soldermask technology over the years.
The Importance of SolderMask in PCB Manufacturing
Protection against Oxidation
One of the primary functions of soldermask is to protect the copper traces on a PCB from oxidation. When exposed to air, copper readily reacts with oxygen to form copper oxide, which is an insulator. This oxidation can lead to poor electrical conductivity and may cause circuit failures. By covering the copper traces with soldermask, the exposure to air is minimized, thus preventing oxidation and ensuring the long-term reliability of the PCB.
Prevention of Solder Bridges
Soldermask also plays a crucial role in preventing solder bridges during the soldering process. A solder bridge is an unintended connection between two or more solder joints, which can cause short circuits and lead to device malfunction. The soldermask acts as a barrier, preventing the molten solder from flowing beyond the designated pad areas and creating unwanted connections.
Insulation and Electrical Isolation
In addition to preventing solder bridges, soldermask provides insulation and electrical isolation between adjacent conductive areas on a PCB. This is particularly important in high-density PCB designs where the spacing between components and traces is minimal. The soldermask layer acts as an insulating barrier, preventing current leakage and ensuring proper functioning of the circuit.
Properties of SolderMask
Chemical Resistance
Soldermask must possess excellent chemical resistance to withstand the various chemicals used in the PCB manufacturing process, such as flux, cleaning agents, and etchants. It should also be resistant to the chemicals encountered during the operating life of the PCB, such as moisture, salt spray, and other environmental contaminants.
Thermal Stability
During the soldering process, PCBs are subjected to high temperatures. Soldermask must have good thermal stability to withstand these temperatures without degrading or losing its protective properties. Typically, soldermask materials are designed to withstand temperatures up to 260°C, which is the maximum temperature encountered during lead-free soldering processes.
Adhesion to Copper and Laminate
Soldermask must have excellent adhesion to both the copper traces and the PCB laminate material. Good adhesion ensures that the soldermask remains firmly bonded to the PCB surface, preventing delamination and providing long-term protection. Adhesion is typically achieved through the use of special additives in the soldermask formulation and by proper surface preparation prior to soldermask application.
Dielectric Properties
As an insulating layer, soldermask must have good dielectric properties to prevent current leakage and maintain signal integrity. The dielectric constant and dissipation factor of the soldermask material are critical parameters that influence the electrical performance of the PCB. Soldermask materials with low dielectric constant and low dissipation factor are preferred for high-frequency and high-speed applications.
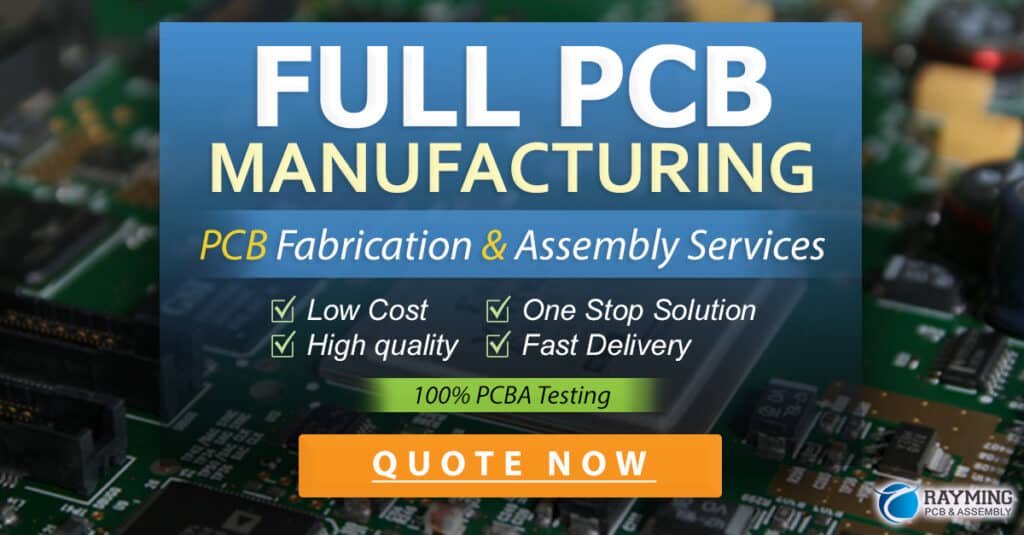
SolderMask Application Methods
Screen Printing
Screen printing is one of the most common methods for applying soldermask to PCBs. In this process, a fine mesh screen is used to transfer the soldermask ink onto the PCB surface. The screen has a stencil of the desired soldermask pattern, and the ink is forced through the openings in the screen using a squeegee. Screen printing is suitable for high-volume production and can achieve a uniform coating thickness.
Liquid Photoimageable SolderMask (LPISM)
Liquid Photoimageable SolderMask (LPISM) is a popular method for applying soldermask to high-density PCBs with fine features. In this process, a liquid photoimageable soldermask is applied to the PCB surface using curtain coating or spraying techniques. The soldermask is then selectively exposed to UV light through a photomask, which hardens the exposed areas while leaving the unexposed areas soluble. The unexposed areas are then removed using a developer solution, leaving behind the desired soldermask pattern.
Dry Film SolderMask (DFSM)
Dry Film SolderMask (DFSM) is another method for applying soldermask to PCBs. In this process, a dry film of soldermask material is laminated onto the PCB surface using heat and pressure. The film is then exposed to UV light through a photomask, similar to the LPISM process. The unexposed areas are removed using a developer solution, leaving behind the desired soldermask pattern. DFSM is known for its excellent thickness control and is suitable for high-volume production.
Advancements in SolderMask Technology
Inkjet SolderMask
Inkjet soldermask is a relatively new technology that offers several advantages over traditional soldermask application methods. In this process, soldermask ink is directly jetted onto the PCB surface using high-precision inkjet printheads. This allows for the creation of very fine features and eliminates the need for screens or photomasks. Inkjet soldermask also enables the use of multiple colors and can be easily customized for specific design requirements.
UV Laser Direct Imaging (UV-LDI)
UV Laser Direct Imaging (UV-LDI) is an advanced technique for exposing soldermask. In this process, a UV laser is used to directly write the soldermask pattern onto the PCB surface, eliminating the need for photomasks. UV-LDI offers high resolution, excellent registration accuracy, and fast turnaround times. It is particularly suitable for prototyping and low-volume production runs.
Environmentally Friendly SolderMask
With the growing emphasis on environmental sustainability, there has been a push towards the development of environmentally friendly soldermask materials. These materials are formulated to minimize the use of hazardous substances and volatile organic compounds (VOCs). They also offer improved biodegradability and reduced environmental impact during manufacturing and disposal. Some examples of eco-friendly soldermask materials include water-based formulations and halogen-free compositions.
Frequently Asked Questions (FAQ)
1. What is the typical thickness of soldermask on a PCB?
The typical thickness of soldermask on a PCB ranges from 0.5 to 2 mils (0.0127 to 0.0508 mm). The exact thickness depends on the specific application requirements, such as the desired insulation properties and the manufacturing process used.
2. Can soldermask be applied to both sides of a PCB?
Yes, soldermask can be applied to both sides of a PCB. In fact, most PCBs have soldermask on both the top and bottom surfaces to provide protection and insulation on all exposed copper areas.
3. What colors are available for soldermask?
Soldermask is available in a variety of colors, with green being the most common. Other popular colors include blue, red, yellow, black, and white. The choice of color is often based on aesthetic preferences, but it can also serve functional purposes, such as improving contrast for better visual inspection or providing UV resistance in outdoor applications.
4. How does soldermask affect the assembly process?
Soldermask plays a critical role in the assembly process by providing a surface that is suitable for soldering. The soldermask layer helps to define the solderable areas on the PCB and prevents solder from spreading beyond the designated pads. This ensures proper solder joint formation and prevents short circuits caused by solder bridges.
5. Can soldermask be removed or reworked if needed?
Yes, soldermask can be removed or reworked if necessary, although it is not a straightforward process. Removal of soldermask typically involves mechanical abrasion or chemical stripping, which can be time-consuming and may damage the underlying copper traces if not done carefully. Reworking soldermask usually involves localized removal of the affected area and reapplication of new soldermask material.
Conclusion
Soldermask is an essential component in the PCB manufacturing process, providing protection, insulation, and solder control. Its properties, such as chemical resistance, thermal stability, and adhesion, are crucial for ensuring the reliability and longevity of PCBs. The advancements in soldermask technology, including inkjet soldermask, UV-LDI, and environmentally friendly formulations, have enabled the production of high-density, high-performance PCBs with improved efficiency and sustainability.
As the electronics industry continues to evolve, with the growing demand for miniaturization, high-speed communication, and environmentally conscious manufacturing, the development of advanced soldermask materials and application techniques will play a vital role in shaping the future of PCB technology.
No responses yet