Introduction to PCB Layout Design Considerations
Printed Circuit Board (PCB) layout design is a crucial stage in the development of electronic devices. A well-designed PCB ensures optimal performance, reliability, and manufacturability of the final product. When designing a PCB layout, there are several important factors to consider that can significantly impact the board’s functionality and overall success of the project.
In this article, we will discuss six key considerations for designing an effective PCB layout. These include component placement, signal integrity, power distribution, thermal management, manufacturability, and testing and debugging. By carefully addressing each of these aspects during the layout process, designers can create high-quality PCBs that meet the specific requirements of their applications.
1. Component Placement
1.1 Functional Grouping
When placing components on a PCB, it is essential to group them based on their functional relationships. This approach helps minimize the length of traces between related components, reducing signal interference and improving overall performance. For example, keep analog and digital components separate to avoid noise coupling.
1.2 Space Optimization
Efficient use of available board space is crucial in PCB layout design. Designers should strive to achieve a compact layout while maintaining adequate spacing between components for proper signal routing and heat dissipation. Consider using surface-mount devices (SMDs) whenever possible, as they occupy less space compared to through-hole components.
1.3 Orientation and Alignment
Pay attention to the orientation and alignment of components on the PCB. Ensure that polarized components, such as electrolytic capacitors and diodes, are placed in the correct orientation to avoid malfunction or damage. Align components in a neat and organized manner to improve readability and facilitate assembly processes.
2. Signal Integrity
2.1 Trace Routing
Proper trace routing is essential for maintaining signal integrity in a PCB. Keep high-speed traces as short as possible and route them away from noise sources. Use appropriate trace widths based on the current carrying capacity and impedance requirements. Avoid sharp bends or corners in traces, as they can cause reflections and degrade signal quality.
2.2 Impedance Matching
Impedance matching is critical for high-speed signals to minimize reflections and ensure proper signal transmission. The characteristic impedance of traces should match the impedance of the source and load devices. Use controlled impedance techniques, such as stripline or microstrip, for sensitive signals.
2.3 Crosstalk Reduction
Crosstalk occurs when signals from one trace couple with adjacent traces, causing interference. To minimize crosstalk, maintain adequate spacing between traces, especially for high-speed signals. Use ground planes or guard traces to provide shielding between sensitive traces. Consider using differential signaling for critical signals to cancel out common-mode noise.
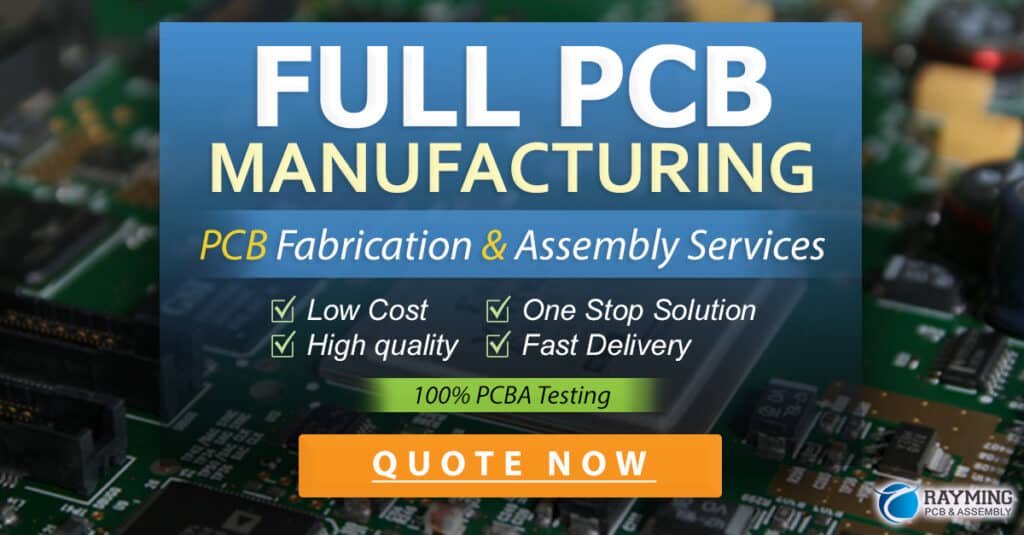
3. Power Distribution
3.1 Power Plane Design
Proper power plane design is crucial for providing a stable and clean power supply to components on the PCB. Use dedicated power and ground planes to distribute power evenly across the board. Keep the power and ground planes as close together as possible to minimize inductance and provide better decoupling.
3.2 Decoupling Capacitors
Place decoupling capacitors close to the power pins of integrated circuits (ICs) to suppress high-frequency noise and provide a stable power supply. Use appropriate capacitor values and types based on the frequency range and current requirements of the ICs. Consider using multiple decoupling capacitors in parallel to cover a wider frequency spectrum.
3.3 Voltage Regulation
Include voltage regulators on the PCB to provide stable and regulated power to sensitive components. Place the regulators close to the power input and use appropriate heat sinking techniques to dissipate excess heat. Use power sequencing if required by the system to ensure proper startup and shutdown of components.
4. Thermal Management
4.1 Heat Dissipation
Proper heat dissipation is essential to prevent components from overheating and ensure reliable operation. Identify components that generate significant heat, such as power transistors or voltage regulators, and provide adequate thermal relief. Use thermal vias to transfer heat from the component to the ground plane or an external heatsink.
4.2 Component Spacing
Maintain sufficient spacing between components to allow for proper airflow and heat dissipation. Avoid placing high-power components close to temperature-sensitive devices. Consider the expected operating environment and ambient temperature when determining component spacing.
4.3 Thermal Simulation
Perform thermal simulations during the layout process to identify potential hot spots and optimize the thermal design. Use thermal analysis tools to evaluate the temperature distribution on the PCB and make necessary adjustments to improve heat dissipation.
5. Manufacturability
5.1 Design for Manufacturing (DFM)
Consider the manufacturing process when designing the PCB layout. Adhere to the design rules and guidelines provided by the PCB manufacturer to ensure proper fabrication and assembly. Use standard component footprints and package sizes whenever possible to avoid custom fabrication requirements.
5.2 Component Placement for Assembly
Place components in a way that facilitates the assembly process. Provide sufficient clearance around components for pick-and-place machines and soldering equipment. Use fiducial markers to assist in component alignment during assembly. Consider the orientation of components for efficient manual or automated assembly.
5.3 Testability and Debugging
Design the PCB layout with testability and debugging in mind. Provide test points and probe pads for critical signals to facilitate testing and troubleshooting. Include debug headers or connectors for programming and firmware updates. Consider using boundary scan techniques, such as JTAG, for complex designs to enable efficient testing and debugging.
6. Testing and Debugging
6.1 Prototype Validation
Before finalizing the PCB layout, create prototypes and perform thorough testing and validation. Assemble the prototypes and conduct functional tests to verify the performance and reliability of the design. Use debugging tools, such as oscilloscopes and logic analyzers, to identify and resolve any issues.
6.2 Signal Integrity Analysis
Perform signal integrity analysis on the PCB to ensure proper signal transmission and minimize signal distortion. Use simulation tools to analyze the behavior of critical signals and identify potential issues, such as reflections, crosstalk, or ground bounce. Make necessary adjustments to the layout based on the analysis results.
6.3 Environmental Testing
Subject the PCB to environmental testing to evaluate its performance under various conditions. Conduct temperature cycling, humidity, and vibration tests to ensure the board can withstand the expected operating environment. Address any identified weaknesses or failures by modifying the layout or selecting more suitable components.
Conclusion
Designing a successful PCB layout requires careful consideration of various factors, including component placement, signal integrity, power distribution, thermal management, manufacturability, and testing and debugging. By addressing these key aspects during the layout process, designers can create high-quality PCBs that meet the specific requirements of their applications.
Remember to follow best practices, adhere to design guidelines, and collaborate closely with the PCB manufacturer to ensure a smooth and efficient development process. Continuously iterate and refine the layout based on simulation results, prototype testing, and feedback from stakeholders.
By paying attention to these important considerations and adopting a methodical approach to PCB layout design, you can develop robust and reliable electronic products that perform optimally in their intended environments.
Frequently Asked Questions (FAQ)
-
Q: What is the importance of component placement in PCB layout design?
A: Component placement is crucial in PCB layout design as it impacts signal integrity, power distribution, and thermal management. Proper placement involves grouping functionally related components, optimizing board space, and ensuring correct orientation and alignment. -
Q: How can I ensure signal integrity in my PCB layout?
A: To ensure signal integrity, keep high-speed traces short, use appropriate trace widths, avoid sharp bends, and implement impedance matching techniques. Additionally, maintain adequate spacing between traces, use ground planes or guard traces for shielding, and consider differential signaling for critical signals. -
Q: What are the key considerations for power distribution in a PCB layout?
A: Key considerations for power distribution include designing dedicated power and ground planes, placing decoupling capacitors close to IC power pins, and using voltage regulators for stable power supply. Proper power plane design and decoupling techniques help minimize noise and ensure reliable operation. -
Q: How can I address thermal management in my PCB layout?
A: Thermal management involves identifying heat-generating components, providing adequate thermal relief, and using thermal vias to transfer heat to ground planes or heatsinks. Maintain sufficient spacing between components for proper airflow and consider performing thermal simulations to optimize the thermal design. -
Q: What should I keep in mind for PCB manufacturability?
A: When designing for manufacturability, adhere to the design rules and guidelines provided by the PCB manufacturer. Use standard component footprints and sizes, provide sufficient clearance for assembly, and consider the orientation of components. Include testability features, such as test points and debug connectors, to facilitate testing and debugging.
Consideration | Key Points |
---|---|
Component Placement | – Group functionally related components – Optimize board space – Ensure correct orientation and alignment |
Signal Integrity | – Keep high-speed traces short – Use appropriate trace widths – Avoid sharp bends – Implement impedance matching – Maintain spacing between traces – Use shielding techniques |
Power Distribution | – Design dedicated power and ground planes – Place decoupling capacitors close to IC power pins – Use voltage regulators for stable power supply |
Thermal Management | – Identify heat-generating components – Provide thermal relief – Use thermal vias – Maintain component spacing for airflow – Perform thermal simulations |
Manufacturability | – Adhere to manufacturer’s design rules and guidelines – Use standard component footprints and sizes – Provide clearance for assembly – Consider component orientation – Include testability features |
No responses yet