1. Optimize PCB Design for Manufacturing
One of the most effective ways to reduce PCB cost is to optimize the design for manufacturing (DFM). DFM involves designing the PCB in a way that minimizes manufacturing complexity and maximizes efficiency. Here are some key considerations for optimizing PCB design:
1.1 Minimize the Number of Layers
Each additional layer in a PCB increases the manufacturing cost. Therefore, it is essential to minimize the number of layers whenever possible. Consider using smaller components and more efficient routing techniques to reduce the need for extra layers.
1.2 Use Standard Sizes and Shapes
Using standard PCB sizes and shapes can help reduce manufacturing costs. Custom sizes and shapes may require additional tooling and setup time, which can increase expenses. Stick to standard dimensions whenever feasible.
1.3 Avoid Tight Tolerances
Tight tolerances can significantly increase manufacturing costs. Unless absolutely necessary, avoid specifying overly tight tolerances for features such as hole sizes, line widths, and spacing. Consult with your manufacturer to determine acceptable tolerances that balance cost and functionality.
1.4 Consider Via Optimization
Vias are small holes drilled through the PCB to connect different layers. Minimizing the number of vias and optimizing their placement can help reduce drilling costs. Additionally, consider using larger via sizes to simplify the drilling process.
2. Choose Cost-Effective Materials
The choice of materials used in PCB manufacturing can have a significant impact on overall cost. Here are some tips for selecting cost-effective materials:
2.1 Substrate Material
FR-4 is the most commonly used substrate material for PCBs due to its good electrical properties and affordability. However, for high-frequency or high-temperature applications, other materials like Rogers or polyimide may be necessary. Consider the specific requirements of your application and choose the most cost-effective substrate that meets those needs.
2.2 Copper Weight
The thickness of the copper traces on a PCB is measured in ounces per square foot (oz/ft²). Thicker copper traces offer better current carrying capacity but also increase the overall cost. Evaluate your current requirements and choose the minimum copper weight that satisfies your needs.
2.3 Surface Finish
The surface finish on a PCB protects the copper traces from oxidation and enhances solderability. Common surface finishes include Hot Air Solder Leveling (HASL), Immersion Silver, Immersion Tin, and Electroless Nickel Immersion Gold (ENIG). HASL is generally the most cost-effective option, while ENIG offers superior durability and flatness at a higher cost. Select the surface finish that balances cost and performance for your application.
Surface Finish | Cost | Durability | Flatness |
---|---|---|---|
HASL | Low | Moderate | Low |
Immersion Silver | Moderate | Good | Moderate |
Immersion Tin | Moderate | Good | Moderate |
ENIG | High | Excellent | High |
3. Leverage Economies of Scale
Manufacturing PCBs in larger quantities can lead to significant cost savings due to economies of scale. Here’s how you can take advantage of this:
3.1 Order in Bulk
Placing larger orders allows manufacturers to optimize their processes and reduce setup costs. This results in a lower per-unit cost for the buyer. Determine your long-term requirements and consider placing bulk orders to achieve cost savings.
3.2 Consider Panelization
Panelization involves grouping multiple PCB designs onto a single panel for manufacturing. This approach minimizes material waste and reduces handling time, leading to cost savings. Work with your manufacturer to explore panelization options that suit your needs.
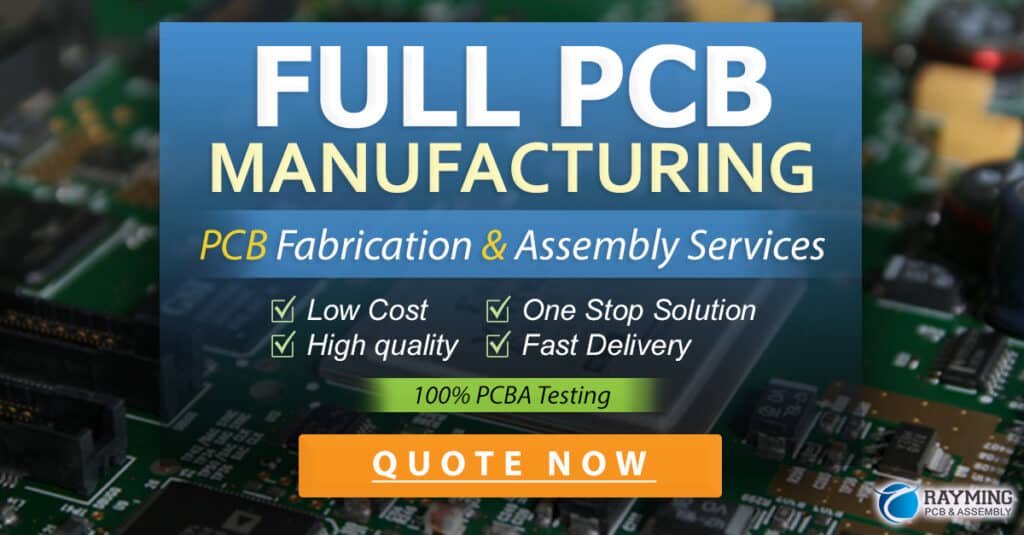
4. Opt for Standard Components
Using standard components instead of custom or specialized parts can significantly reduce PCB cost. Here’s why:
4.1 Lower Component Costs
Standard components are readily available and are often produced in large quantities, resulting in lower unit costs compared to custom or specialized components.
4.2 Improved Availability
Standard components are more likely to be in stock and have shorter lead times, reducing the risk of production delays and associated costs.
4.3 Simplified Assembly
Using standard components streamlines the assembly process, as they are familiar to manufacturers and require less specialized handling. This can lead to faster assembly times and reduced labor costs.
5. Minimize Assembly Complexity
Simplifying the PCB Assembly process can help reduce costs. Consider the following strategies:
5.1 Reduce Component Count
Minimizing the number of components on a PCB reduces assembly time and the risk of errors. Review your design and eliminate any unnecessary components.
5.2 Use Surface Mount Technology (SMT)
SMT components are smaller and can be placed on both sides of the PCB, enabling higher density designs. SMT assembly is generally more cost-effective than through-hole assembly due to faster placement rates and reduced drilling requirements.
5.3 Optimize Component Placement
Placing components in a logical and efficient manner can streamline the assembly process. Group similar components together and minimize the distance between related components to reduce placement time.
6. Work with Reliable Suppliers
Partnering with reliable suppliers can help ensure consistent quality and minimize the risk of costly errors or delays. Here are some tips for selecting suppliers:
6.1 Evaluate Supplier Capabilities
Choose suppliers with a proven track record of producing PCBs that meet your specific requirements. Consider factors such as manufacturing capabilities, quality control processes, and customer support.
6.2 Establish Long-Term Relationships
Building long-term relationships with suppliers can lead to cost savings through volume discounts, improved communication, and a better understanding of your specific needs.
6.3 Communicate Clearly
Clear communication with suppliers is essential for avoiding misunderstandings and ensuring that your requirements are met. Provide detailed specifications, drawings, and any other necessary information to minimize the risk of errors or delays.
7. Consider Total Cost of Ownership (TCO)
When evaluating PCB cost, it’s important to consider the total cost of ownership (TCO) rather than just the initial manufacturing and assembly costs. TCO takes into account factors such as:
7.1 Reliability and Durability
Investing in higher quality materials and manufacturing processes can lead to more reliable and durable PCBs, reducing the need for costly repairs or replacements over the product’s lifetime.
7.2 Maintenance and Support
Consider the long-term costs associated with maintaining and supporting the PCB. Designing for easier maintenance and selecting components with longer lifecycles can help minimize these costs.
7.3 Inventory Management
Efficient inventory management can help reduce carrying costs and minimize the risk of obsolescence. Work with suppliers to establish appropriate lead times and order quantities that balance cost and availability.
Frequently Asked Questions (FAQ)
1. How much can I expect to save by implementing these cost-saving strategies?
The amount of cost savings will vary depending on factors such as the complexity of your PCB design, the volume of your order, and the specific strategies implemented. However, by applying a combination of these tips, it is possible to achieve significant cost reductions, often in the range of 10-30% or more.
2. Will cost-saving strategies compromise the quality or reliability of my PCBs?
Not necessarily. Many cost-saving strategies, such as optimizing PCB design for manufacturing and using standard components, can actually improve the quality and reliability of your PCBs. The key is to find a balance between cost and performance that meets your specific requirements.
3. How do I determine the right balance between cost and performance for my PCBs?
Determining the right balance between cost and performance requires a thorough understanding of your application’s requirements. Consider factors such as the intended use environment, expected product lifespan, and any critical performance parameters. Consult with your design team and suppliers to identify the most cost-effective solutions that meet these requirements.
4. Can I apply these cost-saving strategies to both prototype and production PCBs?
Yes, many of these strategies can be applied to both prototype and production PCBs. However, some strategies, such as leveraging economies of scale through bulk ordering, may be more applicable to production runs. It’s important to consider the specific needs of each stage of the product development process when implementing cost-saving measures.
5. How can I stay informed about new cost-saving technologies and strategies in PCB manufacturing and assembly?
To stay informed about the latest cost-saving technologies and strategies, attend industry conferences, read trade publications, and engage with suppliers and industry experts. Regularly review your PCB design and manufacturing processes to identify areas for improvement and consider adopting new technologies or strategies as they become available.
In conclusion, reducing PCB cost requires a multifaceted approach that considers design optimization, material selection, economies of scale, component choice, assembly complexity, supplier relationships, and total cost of ownership. By implementing these top 7 tips, you can significantly reduce the cost of PCB manufacturing and assembly without compromising on quality or functionality.
No responses yet