Introduction to Li-ion Batteries and Chargers
Lithium-ion (Li-ion) batteries have revolutionized the world of portable electronic devices due to their high energy density, low self-discharge, and long cycle life. These rechargeable batteries are widely used in smartphones, laptops, electric vehicles, and many other applications. To ensure the safe and efficient charging of Li-ion batteries, it is crucial to understand the fundamentals of Li-ion Charger circuits.
In this comprehensive article, we will delve into the intricacies of Li-ion charger circuits, exploring their working principles, key components, and design considerations. Whether you are an electronics enthusiast, a battery pack designer, or simply curious about the technology behind your devices, this article will provide you with a thorough understanding of Li-ion charger circuits.
How Li-ion Batteries Work
Before we dive into the specifics of Li-ion charger circuits, let’s briefly discuss how Li-ion batteries work. A Li-ion battery consists of three main components: a positive electrode (cathode), a negative electrode (anode), and an electrolyte.
During the charging process, lithium ions move from the cathode to the anode through the electrolyte. This movement of ions causes the anode to become more negative and the cathode to become more positive. When the battery is discharging, the lithium ions move back from the anode to the cathode, releasing electrons and generating an electric current.
The chemical composition of the electrodes and electrolyte varies depending on the specific type of Li-ion battery. Some common types include Lithium Cobalt Oxide (LCO), Lithium Manganese Oxide (LMO), Lithium Iron Phosphate (LFP), and Lithium Nickel Manganese Cobalt Oxide (NMC).
Charging Stages of Li-ion Batteries
To ensure the safe and efficient charging of Li-ion batteries, charger circuits typically employ a multi-stage charging algorithm. The most common charging stages are:
-
Trickle Charge (Pre-charge): When the battery voltage is below a certain threshold (usually around 3V), the charger enters the trickle charge stage. During this stage, a small current (typically 10% of the full charge current) is applied to gently raise the battery voltage to a safe level before proceeding to the next stage.
-
Constant Current (CC) Stage: Once the battery voltage reaches the trickle charge threshold, the charger switches to the constant current stage. In this stage, the charger applies a constant current to the battery, usually at a rate of 0.5C to 1C (where C represents the battery capacity). The battery voltage gradually rises during this stage.
-
Constant Voltage (CV) Stage: When the battery voltage reaches the maximum charging voltage (typically 4.2V for most Li-ion batteries), the charger enters the constant voltage stage. During this stage, the charger maintains a constant voltage while the charging current gradually decreases. This stage prevents overcharging and ensures that the battery reaches its full capacity.
-
Charge Termination: The charging process is terminated when the charging current drops below a certain threshold (usually around 0.1C) or when a predetermined time limit is reached. At this point, the battery is considered fully charged, and the charger may enter a standby or maintenance mode.
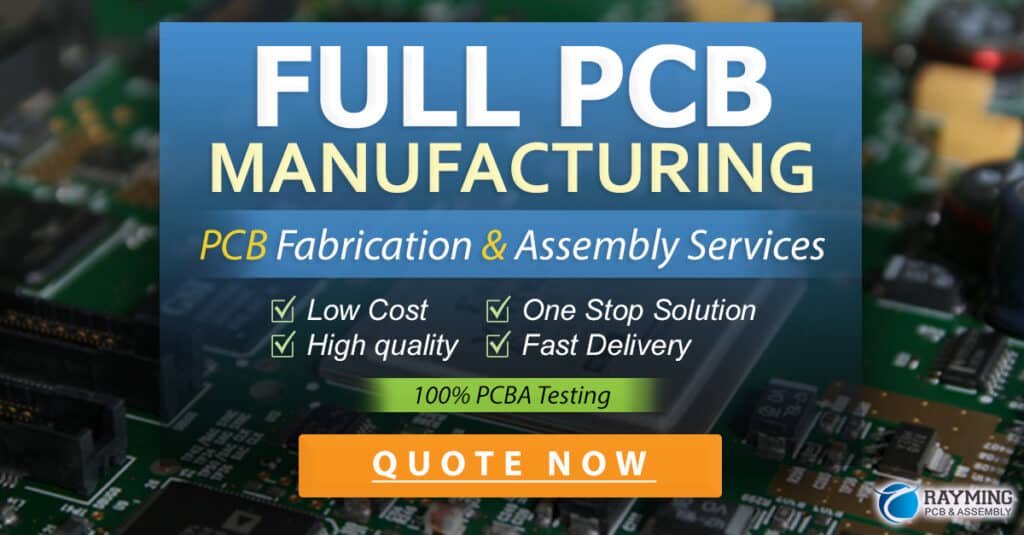
Key Components of Li-ion Charger Circuits
A typical Li-ion charger circuit consists of several key components that work together to ensure safe and efficient charging. Let’s explore each component in detail:
1. Microcontroller or Dedicated Charging IC
The heart of a Li-ion charger circuit is either a microcontroller or a dedicated charging IC. These components are responsible for implementing the charging algorithm, monitoring the battery voltage and current, and controlling the charging process.
Microcontrollers offer flexibility and customization options, allowing designers to implement custom charging algorithms and additional features. However, they require more development effort and may not be as cost-effective for simple charger designs.
Dedicated charging ICs, on the other hand, are specifically designed for battery charging applications. They integrate all the necessary control and protection features into a single chip, simplifying the design process. Some popular charging ICs include the TP4056, BQ2407x series, and MCP73831.
2. Voltage Regulator
A voltage regulator is used to provide a stable and regulated voltage supply to the charging circuit. It steps down the input voltage (e.g., from a USB port or a wall adapter) to a level suitable for charging the Li-ion battery.
Linear voltage regulators, such as the LM317 or LM7805, are commonly used in low-power charger designs. They are simple and inexpensive but have limited efficiency and may generate significant heat.
Switching voltage regulators, such as buck converters or switched-mode power supplies (SMPS), offer higher efficiency and are preferred for high-power charger designs. They can handle higher input voltages and currents while generating less heat.
3. Current Sensing Resistor
To monitor and control the charging current, a current sensing resistor is used in series with the battery. The voltage drop across this resistor is proportional to the charging current and is measured by the microcontroller or charging IC.
The value of the current sensing resistor is chosen based on the desired charging current and the maximum voltage drop that can be tolerated. A lower resistance value results in a lower voltage drop but requires a more precise measurement circuit.
4. Protection Circuitry
Li-ion batteries are sensitive to overcharging, overdischarging, and overcurrent conditions. To prevent damage and ensure safe operation, protection circuitry is incorporated into the charger design.
-
Overcharge Protection: The charger IC or microcontroller monitors the battery voltage and terminates the charging process when the voltage reaches the maximum charging voltage (e.g., 4.2V). This prevents the battery from being overcharged, which can lead to reduced capacity, increased internal resistance, and even safety hazards.
-
Overdischarge Protection: The protection circuit prevents the battery from being discharged below a certain voltage threshold (usually around 2.5V). Overdischarging can cause irreversible damage to the battery and significantly reduce its capacity.
-
Overcurrent Protection: The charger circuit includes current limiting mechanisms to prevent excessive charging or discharging currents. This protects the battery and the charger components from damage due to short circuits or other fault conditions.
5. Temperature Sensing
Temperature monitoring is crucial for safe and efficient charging of Li-ion batteries. The charger circuit may include a temperature sensor, such as a thermistor or a dedicated temperature sensing IC, to monitor the battery temperature during charging.
If the battery temperature exceeds a certain threshold (typically around 45°C), the charger reduces the charging current or stops the charging process altogether. This prevents damage to the battery and ensures safe operation.
Designing a Li-ion Charger Circuit
When designing a Li-ion charger circuit, several key considerations should be taken into account:
-
Battery Specifications: The charger circuit must be designed to match the specifications of the Li-ion battery being charged. This includes the battery voltage, capacity, maximum charging current, and charging voltage limits. Refer to the battery datasheet or consult with the battery manufacturer to obtain these specifications.
-
Input Power Source: Consider the input power source for the charger circuit. Will it be powered from a USB port, a wall adapter, or a solar panel? The input voltage range and maximum available current should be taken into account when selecting the voltage regulator and designing the power stage.
-
Charging Current: Determine the desired charging current based on the battery capacity and the required charging time. A higher charging current will charge the battery faster but may generate more heat and require more robust components. A lower charging current will result in slower charging but may be more suitable for smaller batteries or when heat dissipation is a concern.
-
Component Selection: Choose appropriate components for the charger circuit based on the design requirements. This includes the microcontroller or charging IC, voltage regulator, current sensing resistor, protection components (e.g., MOSFETs, fuses), and temperature sensor. Consider factors such as power dissipation, accuracy, and cost when selecting components.
-
PCB Layout: Proper PCB layout is crucial for the performance and reliability of the charger circuit. Consider factors such as component placement, trace widths, and ground planes to minimize noise, reduce electromagnetic interference (EMI), and ensure efficient heat dissipation. Follow best practices for PCB design, such as keeping high-current traces short and wide, providing adequate copper pours for heat sinking, and using proper grounding techniques.
-
Safety and Compliance: Ensure that the charger circuit complies with relevant safety standards and regulations. This may include requirements for electrical safety, electromagnetic compatibility (EMC), and environmental protection. Consult the applicable standards and regulations for your target market and application.
-
Testing and Validation: Thoroughly test and validate the charger circuit to ensure its functionality, safety, and reliability. Perform tests such as charging and discharging cycles, temperature monitoring, and fault condition simulations. Use calibrated test equipment and follow established test procedures to ensure accurate and reproducible results.
Example Li-ion Charger Circuit
To illustrate the concepts discussed in this article, let’s take a look at a simplified example of a Li-ion charger circuit using a dedicated charging IC.
In this example, the TP4056 charging IC is used to implement the charging algorithm and control the charging process. The key components of the circuit are:
-
TP4056 Charging IC: The TP4056 is a complete constant-current/constant-voltage linear charger for single-cell Li-ion batteries. It includes built-in protection features such as overcharge protection, overcurrent protection, and thermal regulation.
-
Input Voltage Regulator: A 5V voltage regulator (e.g., LM7805) is used to provide a stable input voltage to the TP4056. It steps down the input voltage from a USB port or a wall adapter to 5V.
-
Current Sensing Resistor: A 1.2Ω resistor (R1) is used to set the charging current. The TP4056 monitors the voltage drop across this resistor to control the charging current.
-
Battery Connection: The Li-ion battery is connected to the BAT pin of the TP4056. The positive terminal of the battery is connected to the BAT pin, while the negative terminal is connected to ground.
-
Status Indicator: An LED (D1) is connected to the CHRG pin of the TP4056 to indicate the charging status. The LED is illuminated during charging and turns off when the battery is fully charged.
This example circuit provides a simple and effective solution for charging a single-cell Li-ion battery. The TP4056 handles the charging algorithm, protection features, and status indication, simplifying the overall design.
FAQs
- What is the difference between CC and CV charging stages?
-
In the constant current (CC) stage, the charger applies a constant current to the battery, causing the battery voltage to gradually rise. In the constant voltage (CV) stage, the charger maintains a constant voltage while the charging current gradually decreases. The CC stage is used to quickly charge the battery, while the CV stage is used to top off the battery and prevent overcharging.
-
Can I charge a Li-ion battery without a dedicated charging IC?
-
While it is possible to charge a Li-ion battery without a dedicated charging IC, it is not recommended. Dedicated charging ICs provide essential protection features and implement the necessary charging algorithm to ensure safe and efficient charging. Attempting to charge a Li-ion battery without proper protection and control circuitry can lead to overcharging, overdischarging, or other damaging conditions.
-
What happens if I overcharge a Li-ion battery?
-
Overcharging a Li-ion battery can have serious consequences. It can cause the battery to swell, generate excessive heat, and even pose a fire or explosion hazard. Overcharging can also lead to reduced battery capacity, increased internal resistance, and shortened battery life. It is crucial to use a proper charger circuit with overcharge protection to prevent these issues.
-
How do I select the appropriate charging current for my Li-ion battery?
-
The appropriate charging current depends on the battery capacity and the desired charging time. As a general rule, a charging current of 0.5C to 1C is considered safe and efficient for most Li-ion batteries. For example, if you have a 2000mAh battery, a charging current of 1000mA to 2000mA (0.5C to 1C) would be suitable. Consult the battery datasheet or manufacturer’s recommendations for specific charging current guidelines.
-
Can I use a Li-ion charger circuit to charge other types of batteries?
- No, Li-ion charger circuits are specifically designed for charging Li-ion batteries. Different battery chemistries have different charging requirements and voltage profiles. Using a Li-ion charger to charge other types of batteries, such as NiMH or lead-acid batteries, can cause damage to both the battery and the charger. Always use a charger circuit specifically designed for the type of battery you are using.
Conclusion
Li-ion charger circuits play a crucial role in ensuring the safe and efficient charging of Li-ion batteries. By understanding the working principles, key components, and design considerations of Li-ion charger circuits, you can develop reliable and high-performance charging solutions for your battery-powered projects.
Remember to consider factors such as battery specifications, input power source, charging current, component selection, PCB layout, safety, and compliance when designing a Li-ion charger circuit. Thorough testing and validation are essential to ensure the functionality and reliability of the charger.
With the knowledge gained from this article, you are well-equipped to tackle your next Li-ion battery charging project. Whether you are designing a charger for a portable device, an electric vehicle, or any other application, the principles and techniques discussed here will guide you in creating a robust and efficient Li-ion charger circuit.
No responses yet