Introduction to Flexible PCBs
Flexible printed circuit boards (PCBs) are thin, lightweight, and bendable circuits used in a wide range of electronic devices. Unlike traditional rigid PCBs, flexible PCBs can conform to various shapes and fit into tight spaces, making them ideal for applications that require flexibility, such as wearable electronics, medical devices, and compact consumer products. In this article, we will guide you through the process of creating your own Diy Flexible PCB.
Advantages of Flexible PCBs
- Lightweight and thin
- Can conform to various shapes
- Increased reliability due to reduced interconnections
- Improved signal integrity
- Reduced assembly costs
- Increased design flexibility
Materials and Tools Required
To create your own flexible PCB, you will need the following materials and tools:
Materials | Tools |
---|---|
Copper-clad polyimide film | Scissors or utility knife |
Photoresist film | Rulers or measuring tape |
Developing solution | Permanent marker |
Etching solution | Sponge or foam brush |
Acetone or isopropyl alcohol | UV exposure unit or sunlight |
Drill bits (for vias and holes) | Etching tank or tray |
Solder paste or wire | Drill or Dremel tool |
Components for your circuit | Soldering iron |
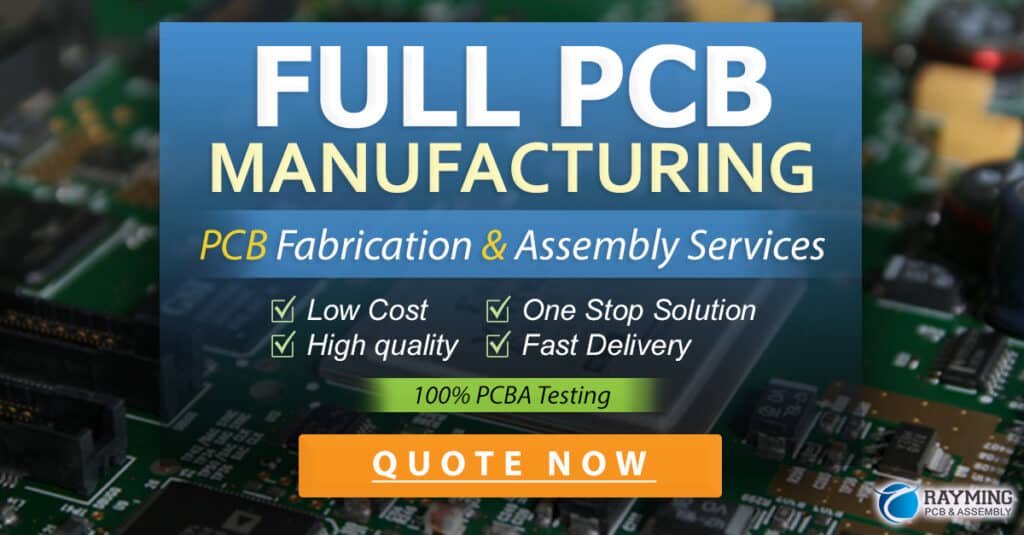
Designing Your Flexible PCB
Step 1: Create Your Circuit Schematic
Before starting the fabrication process, you need to design your circuit schematic using electronic design automation (EDA) software like KiCad, Eagle, or Altium Designer. If you are new to PCB design, you can find numerous tutorials and resources online to help you get started.
Step 2: Convert Your Schematic to a PCB Layout
Once you have completed your circuit schematic, convert it into a PCB layout using your chosen EDA software. Keep in mind the specific requirements for flexible PCBs, such as minimum bend radius, trace width, and spacing.
Step 3: Generate Gerber Files
After finalizing your PCB layout, generate Gerber files, which are the standard file format used for PCB fabrication. These files contain all the necessary information for manufacturing your flexible PCB, including the copper layers, solder mask, silk screen, and drill data.
Fabricating Your Flexible PCB
Step 1: Print Your Circuit Design
Print your circuit design onto a transparency film using a laser printer. Ensure that the print is dark and opaque, as this will serve as the mask for exposing your photoresist-coated copper-clad polyimide film.
Step 2: Prepare the Copper-Clad Polyimide Film
Cut a piece of copper-clad polyimide film slightly larger than your circuit design. Clean the copper surface with acetone or isopropyl alcohol to remove any dirt or grease.
Step 3: Apply Photoresist Film
Apply a layer of photoresist film to the copper surface of the polyimide film. Follow the manufacturer’s instructions for application and ensure that the photoresist is evenly distributed and free of air bubbles.
Step 4: Expose the Photoresist
Place the transparency film with your circuit design onto the photoresist-coated copper-clad polyimide film. Expose the photoresist to UV light using an exposure unit or sunlight for the recommended time. The exposure time will vary depending on the type of photoresist and the intensity of the UV light source.
Step 5: Develop the Photoresist
After exposure, remove the transparency film and develop the photoresist using the appropriate developing solution. Follow the manufacturer’s instructions for development time and agitation. The exposed areas of the photoresist will dissolve, revealing the copper underneath.
Step 6: Etch the Copper
Immerse the developed polyimide film in an etching solution, such as ferric chloride or ammonium persulfate. The etching solution will remove the exposed copper, leaving behind the circuit traces protected by the photoresist. Agitate the solution gently to ensure even etching.
Step 7: Remove the Photoresist
Once etching is complete, remove the polyimide film from the solution and rinse it with water. Use acetone or a photoresist stripper to remove the remaining photoresist, revealing the final circuit traces.
Step 8: Drill Vias and Holes
If your design requires vias or holes, use a drill or Dremel tool with appropriate drill bits to create them. Be careful not to damage the delicate polyimide film while drilling.
Step 9: Apply Solder Mask (Optional)
If desired, apply a layer of solder mask to protect the circuit traces and prevent short circuits. Print the solder mask design onto a transparency film and repeat the exposure, development, and etching process as described above.
Step 10: Apply Silk Screen (Optional)
If you want to add component labels or other markings to your flexible PCB, apply a silk screen layer using the same process as the solder mask.
Assembling Your Flexible PCB
Step 1: Apply Solder Paste or Tin the Pads
Apply solder paste to the component pads using a stencil or syringe. Alternatively, you can tin the pads using a soldering iron and solder wire.
Step 2: Place Components
Place the components on the corresponding pads according to your circuit design. Use tweezers for precise placement of small components.
Step 3: Solder Components
Solder the components to the pads using a soldering iron. Be careful not to overheat the components or the delicate polyimide film. Use a heat sink or tweezers to protect heat-sensitive components.
Step 4: Clean the PCB
After soldering, clean the PCB using isopropyl alcohol and a soft brush to remove any flux residue or debris.
Testing Your Flexible PCB
Before using your flexible PCB in your project, it is essential to test its functionality and reliability.
Step 1: Visual Inspection
Visually inspect your assembled flexible PCB for any obvious defects, such as short circuits, cold solder joints, or misaligned components.
Step 2: Continuity Test
Use a multimeter to test the continuity between the various points on your PCB. Ensure that there are no unintended short circuits or open connections.
Step 3: Functional Test
Power up your flexible PCB and test its functionality according to your circuit design. Verify that all components are working as intended and that the PCB performs its desired function.
Frequently Asked Questions (FAQ)
1. Can I use regular PCB materials for making flexible PCBs?
No, regular PCB materials like FR-4 are rigid and not suitable for making flexible PCBs. You need to use flexible substrates like polyimide film, which can bend without breaking.
2. What is the minimum bend radius for flexible PCBs?
The minimum bend radius depends on the thickness of the polyimide film and the copper traces. As a general rule, the minimum bend radius should be at least six times the total thickness of the PCB to avoid damaging the traces or the substrate.
3. Can I make multi-layer flexible PCBs at home?
Making multi-layer flexible PCBs at home can be challenging, as it requires precise alignment and lamination of multiple layers. It is recommended to start with single-layer flexible PCBs and gain experience before attempting multi-layer designs.
4. How do I connect flexible PCBs to rigid PCBs?
You can connect flexible PCBs to rigid PCBs using various methods, such as:
– Connectors designed for flexible PCBs
– Soldering the flexible PCB directly to the rigid PCB
– Using a stiffener or reinforcement at the connection point
5. Can I reuse the etching solution for multiple PCBs?
Yes, you can reuse the etching solution for multiple PCBs, but its effectiveness will diminish over time. Regularly check the etching speed and replace the solution when it becomes too slow or contaminated.
Conclusion
Creating your own DIY flexible PCB can be a rewarding and educational experience. By following the steps outlined in this article and practicing proper safety precautions, you can design, fabricate, and assemble flexible PCBs for your projects. As you gain experience, you can explore more advanced techniques and tackle more complex designs. Remember to always test your PCBs thoroughly before using them in your final applications.
No responses yet