What is Solderability Testing?
Solderability testing is a critical process in the manufacturing of printed circuit boards (PCBs) to ensure the quality and reliability of the final product. It involves evaluating the ability of component leads, terminations, and PCB surface finishes to be wetted by molten solder during the assembly process. Proper solderability is essential for creating strong, reliable solder joints that can withstand the stresses of the operating environment.
Importance of Solderability Testing
Solderability testing is crucial for several reasons:
-
Quality Assurance: It helps identify potential issues with component leads, terminations, or PCB surface finishes before the assembly process, reducing the risk of defects and failures in the final product.
-
Cost Savings: By catching solderability issues early, manufacturers can avoid the costs associated with rework, repairs, and product returns.
-
Reliability: Proper solderability ensures the formation of strong, reliable solder joints that can withstand the stresses of the operating environment, increasing the overall reliability of the PCB.
-
Compliance: Solderability testing helps manufacturers meet industry standards and customer requirements for quality and reliability.
Factors Affecting Solderability
Several factors can influence the solderability of components and PCBs:
Surface Finish
The surface finish of component leads, terminations, and PCB pads plays a critical role in solderability. Common surface finishes include:
- Hot Air Solder Leveling (HASL)
- Electroless Nickel Immersion Gold (ENIG)
- Immersion Silver (IAg)
- Immersion Tin (ISn)
- Organic Solderability Preservative (OSP)
Each surface finish has its advantages and disadvantages in terms of solderability, shelf life, and cost.
Storage Conditions
Improper storage conditions can negatively impact solderability. Factors such as humidity, temperature, and exposure to contaminants can cause oxidation, corrosion, or degradation of the surface finish, leading to poor solderability.
Age of Components and PCBs
As components and PCBs age, their solderability may deteriorate due to oxidation, corrosion, or degradation of the surface finish. Older components and PCBs may require additional processing, such as solder dipping or re-tinning, to improve solderability.
Solder Composition
The composition of the solder used in the assembly process can also affect solderability. Different solder alloys have varying wetting properties, melting temperatures, and flux compatibility, which can impact the formation of reliable solder joints.
Solderability Testing Methods
There are several methods for evaluating the solderability of components and PCBs:
Dip and Look Test
The dip and look test is a simple, qualitative method for assessing solderability. It involves dipping the component leads or PCB pads into molten solder for a specified time and then visually inspecting the resulting solder coating for wetting, coverage, and appearance.
Wetting Balance Test
The wetting balance test is a quantitative method that measures the wetting force and time of a component lead or PCB pad when immersed in molten solder. The test provides objective data on the solderability of the surface, allowing for comparison against established standards or requirements.
Globule Test
The globule test, also known as the solder ball test, evaluates the ability of a component lead or PCB pad to form a well-defined solder globule when dipped into molten solder. The size, shape, and appearance of the solder globule provide an indication of the solderability of the surface.
Edge Dip Test
The edge dip test is used to assess the solderability of PCB edge connectors. It involves dipping the edge connector into molten solder at a specified angle and time, then visually inspecting the resulting solder coating for wetting, coverage, and appearance.
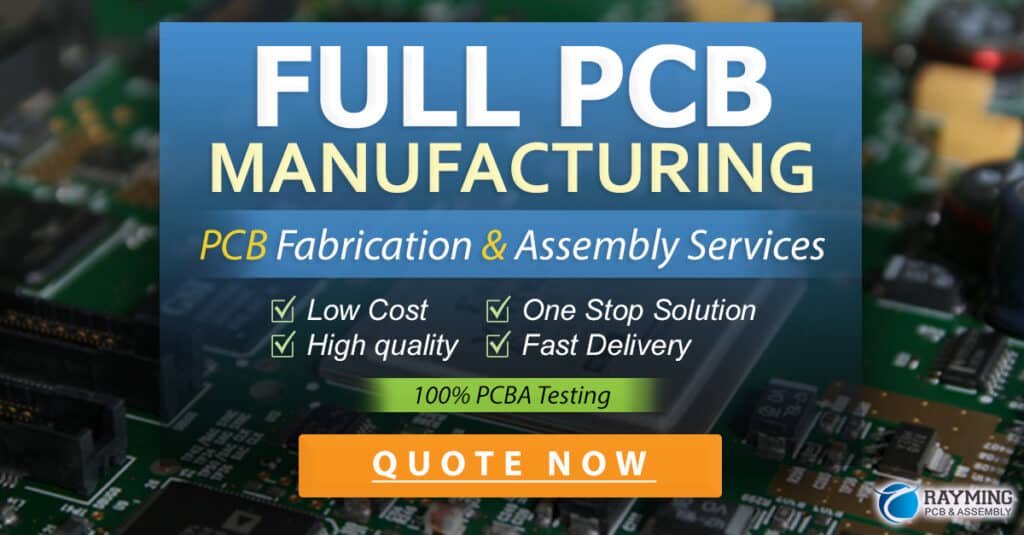
Solderability Test Standards
Several industry standards provide guidelines and requirements for solderability testing:
IPC J-STD-002
IPC J-STD-002, “Solderability Tests for Component Leads, Terminations, Lugs, Terminals, and Wires,” is a widely-used standard that defines test methods, procedures, and acceptance criteria for evaluating the solderability of component leads and terminations.
IPC J-STD-003
IPC J-STD-003, “Solderability Tests for Printed Boards,” provides guidelines and requirements for assessing the solderability of PCB surface finishes and plated through-holes.
MIL-STD-202
MIL-STD-202, “Test Method Standard for Electronic and Electrical Component Parts,” includes solderability test methods for military and aerospace applications.
Interpreting Solderability Test Results
Interpreting solderability test results requires a clear understanding of the acceptance criteria defined in the relevant industry standards or customer requirements. Key factors to consider when evaluating solderability test results include:
- Wetting angle
- Solder coverage
- Solder globule formation
- Dewetting or non-wetting areas
- Presence of contaminants or oxidation
Solderability test results that fall outside the acceptable range may indicate issues with the component leads, terminations, or PCB surface finish that could lead to poor solder joint formation and reduced reliability.
Improving Solderability
When solderability issues are identified, several steps can be taken to improve the solderability of components and PCBs:
Solder Dipping
Solder dipping involves immersing the component leads or PCB pads in molten solder to remove oxides and apply a fresh solder coating. This process can improve solderability by providing a clean, wettable surface for solder joint formation.
Re-tinning
Re-tinning is a process that involves applying a new layer of solder to the component leads or PCB pads to improve solderability. This can be done using a solder pot, solder fountain, or solder iron, depending on the specific application and requirements.
Plasma Cleaning
Plasma cleaning uses a high-energy plasma to remove oxides, contaminants, and organic residues from the surface of component leads or PCB pads. This process can improve solderability by providing a clean, activated surface for solder joint formation.
Protective Coatings
Applying protective coatings, such as organic solderability preservatives (OSPs) or temporary solder masks, can help maintain the solderability of components and PCBs during storage and handling. These coatings protect the surface from oxidation and contamination, preserving its wettability for the assembly process.
FAQ
1. What is the purpose of solderability testing?
Solderability testing is performed to evaluate the ability of component leads, terminations, and PCB surface finishes to be wetted by molten solder during the assembly process. It helps ensure the formation of strong, reliable solder joints and the overall quality of the final product.
2. What are the most common solderability testing methods?
The most common solderability testing methods include the dip and look test, wetting balance test, globule test, and edge dip test. Each method provides a different approach to assessing the solderability of components and PCBs.
3. What factors can affect the solderability of components and PCBs?
Factors that can affect solderability include the surface finish of component leads and PCB pads, storage conditions, age of components and PCBs, and the composition of the solder used in the assembly process.
4. What industry standards provide guidelines for solderability testing?
IPC J-STD-002 and IPC J-STD-003 are widely-used industry standards that provide guidelines and requirements for solderability testing of component leads, terminations, and PCB surface finishes. MIL-STD-202 includes solderability test methods for military and aerospace applications.
5. What steps can be taken to improve the solderability of components and PCBs?
When solderability issues are identified, steps such as solder dipping, re-tinning, plasma cleaning, and applying protective coatings can be taken to improve the solderability of components and PCBs. These processes help remove oxides, contaminants, and apply fresh solder coatings to provide a clean, wettable surface for solder joint formation.
Conclusion
Solderability testing is a vital process in the manufacturing of printed circuit boards, ensuring the quality and reliability of the final product. By understanding the factors that affect solderability, the various testing methods available, and the industry standards that govern solderability testing, manufacturers can effectively evaluate and improve the solderability of their components and PCBs. This, in turn, leads to the formation of strong, reliable solder joints and the production of high-quality electronic devices that meet the demands of today’s market.
No responses yet