Introduction to Via Fill in Printed Circuit Boards
In the world of printed circuit boards (PCBs), vias play a crucial role in interconnecting different layers of the board. Vias are essentially small holes drilled through the PCB that allow electrical signals to pass from one layer to another. However, simply drilling holes is not enough to ensure reliable connections and optimal performance. This is where via fill comes into play.
Via fill is the process of filling the drilled holes with a conductive or non-conductive material. The choice between conductive and non-conductive via fill depends on various factors such as the PCB’s application, design requirements, and manufacturing constraints. In this article, we will explore the differences between conductive and non-conductive via fill, their advantages and disadvantages, and when to use each type.
What is Conductive Via Fill?
Conductive via fill involves filling the drilled holes with a conductive material, typically a metal such as copper or silver. The conductive fill creates a solid electrical connection between the layers, allowing signals to pass through seamlessly. Conductive via fill is commonly used in high-density PCB designs where signal integrity and reliability are critical.
Advantages of Conductive Via Fill
-
Improved Electrical Conductivity: Conductive via fill provides a low-resistance path for electrical signals, minimizing signal loss and ensuring reliable connections between layers.
-
Enhanced Signal Integrity: By creating a solid conductive path, conductive via fill reduces the risk of signal reflections and distortions, leading to improved signal integrity.
-
Increased Current Carrying Capacity: Conductive via fill allows for higher current carrying capacity compared to non-filled vias, making it suitable for power delivery applications.
-
Better Thermal Management: Conductive via fill helps dissipate heat more efficiently, preventing localized hot spots and improving the overall thermal performance of the PCB.
Disadvantages of Conductive Via Fill
-
Higher Manufacturing Cost: Conductive via fill requires additional processing steps and materials, which can increase the overall manufacturing cost of the PCB.
-
Longer Production Time: The conductive filling process adds extra time to the PCB manufacturing cycle, potentially impacting production schedules.
-
Potential for Voids: If not properly controlled, the conductive filling process can lead to the formation of voids within the via, compromising the electrical and mechanical integrity of the connection.
What is Non-Conductive Via Fill?
Non-conductive via fill, also known as via capping or via plugging, involves filling the drilled holes with a non-conductive material such as epoxy resin. The primary purpose of non-conductive via fill is to provide mechanical support and prevent the entry of contaminants into the via.
Advantages of Non-Conductive Via Fill
-
Cost-Effective: Non-conductive via fill is generally less expensive compared to conductive via fill since it does not require the use of costly conductive materials.
-
Faster Production: The non-conductive filling process is typically faster than conductive filling, allowing for shorter production times.
-
Improved Mechanical Strength: Non-conductive via fill provides additional mechanical support to the PCB, reducing the risk of via breakage and improving the overall structural integrity.
-
Protection Against Contaminants: By sealing the via with a non-conductive material, non-conductive via fill prevents the entry of contaminants such as moisture and dust, which can cause reliability issues.
Disadvantages of Non-Conductive Via Fill
-
No Electrical Conductivity: Non-conductive via fill does not provide any electrical conductivity, making it unsuitable for applications that require electrical connections between layers.
-
Limited Signal Integrity Benefits: Unlike conductive via fill, non-conductive fill does not offer significant improvements in signal integrity or reduce signal reflections.
-
Potential for Thermal Insulation: Non-conductive materials used for via fill may act as thermal insulators, hindering the efficient dissipation of heat from the PCB.
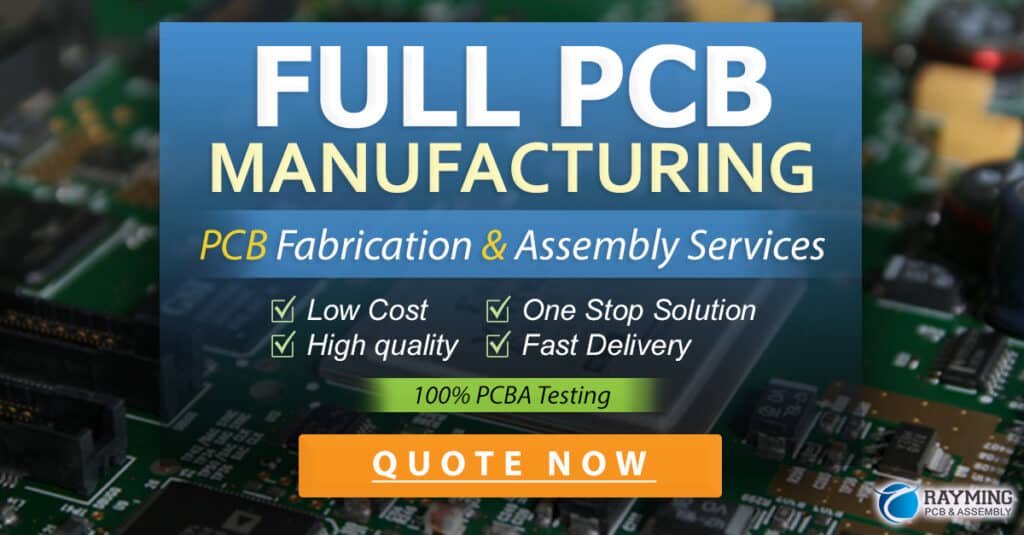
Choosing Between Conductive and Non-Conductive Via Fill
The decision to use conductive or non-conductive via fill depends on various factors specific to the PCB design and its intended application. Here are some key considerations:
-
Electrical Requirements: If the PCB design requires electrical connections between layers and high signal integrity, conductive via fill is the preferred choice. However, if electrical conductivity is not a concern, non-conductive fill can be used.
-
Current Carrying Capacity: For applications that involve high current flows, such as power delivery, conductive via fill is necessary to ensure adequate current carrying capacity.
-
Manufacturing Cost and Time: Conductive via fill is generally more expensive and time-consuming compared to non-conductive fill. If cost and production time are critical factors, non-conductive fill may be the more suitable option.
-
Mechanical Strength: Non-conductive via fill provides additional mechanical support to the PCB, making it advantageous in applications where mechanical integrity is crucial.
-
Environmental Factors: If the PCB will be exposed to harsh environmental conditions or contaminants, non-conductive via fill can provide added protection by sealing the via holes.
The table below summarizes the key differences between conductive and non-conductive via fill:
Factor | Conductive Via Fill | Non-Conductive Via Fill |
---|---|---|
Electrical Conductivity | High | None |
Signal Integrity | Improved | Limited |
Current Carrying Capacity | High | Low |
Thermal Management | Efficient | Potential Insulation |
Manufacturing Cost | Higher | Lower |
Production Time | Longer | Faster |
Mechanical Strength | Moderate | Improved |
Protection Against Contaminants | Limited | Effective |
Best Practices for Via Fill Implementation
Regardless of the type of via fill chosen, following best practices during the design and manufacturing process is essential to ensure optimal performance and reliability. Here are some guidelines to consider:
-
Design for Manufacturability (DFM): Collaborate with the PCB manufacturer to ensure that the via fill design is compatible with their manufacturing capabilities and processes.
-
Proper Via Sizing: Select appropriate via sizes based on the PCB’s layer stack and the specific requirements of the via fill process. Consult with the manufacturer for recommended via dimensions.
-
Material Selection: Choose the appropriate conductive or non-conductive fill material based on the application requirements, such as electrical conductivity, thermal conductivity, and chemical resistance.
-
Process Control: Implement strict process controls during the via fill manufacturing process to minimize defects such as voids, incomplete filling, or material contamination.
-
Testing and Inspection: Conduct thorough testing and inspection of the filled vias to ensure their integrity and performance. This may include electrical testing, cross-sectional analysis, and reliability testing.
Frequently Asked Questions (FAQ)
-
Q: Can conductive and non-conductive via fill be used together in the same PCB?
A: Yes, it is possible to use both conductive and non-conductive via fill in the same PCB design. The choice depends on the specific requirements of each via and the overall design goals. -
Q: Is via fill necessary for all PCB designs?
A: No, via fill is not always necessary. The decision to use via fill depends on factors such as the PCB’s application, layer count, signal integrity requirements, and manufacturing constraints. -
Q: What are the typical materials used for conductive via fill?
A: Common materials for conductive via fill include copper, silver, and conductive epoxies. The choice of material depends on the specific electrical and thermal requirements of the application. -
Q: How does via fill affect the PCB’s overall thickness?
A: Via fill can slightly increase the overall thickness of the PCB, especially when using conductive fill materials. However, the impact on thickness is generally minimal and can be accounted for during the design phase. -
Q: Are there any specific design considerations for via fill in high-frequency applications?
A: Yes, in high-frequency applications, the choice of via fill material and the design of the via geometry can impact signal integrity. It is important to consider factors such as the dielectric constant, loss tangent, and skin effect when designing via fill for high-frequency PCBs.
Conclusion
Via fill is a critical aspect of PCB design and manufacturing, offering benefits such as improved electrical conductivity, enhanced signal integrity, and increased mechanical strength. The choice between conductive and non-conductive via fill depends on the specific requirements of the PCB application, including electrical performance, cost, and manufacturing constraints.
By understanding the advantages and disadvantages of each type of via fill and following best practices during the design and manufacturing process, PCB designers and manufacturers can ensure optimal performance, reliability, and cost-effectiveness in their PCB projects.
As PCB technology continues to advance, innovations in via fill materials and processes are expected to emerge, providing even more options and capabilities for PCB designers. Staying up-to-date with the latest developments in via fill technology and collaborating closely with PCB manufacturers will be key to achieving successful and high-quality PCB designs.
No responses yet