Understanding the Basics of Power Bank Circuits
Before diving into the details of creating a Power Bank PCB, it’s essential to understand the basic components and principles behind power bank circuits.
Key Components of a Power Bank Circuit
A typical power bank circuit consists of the following main components:
-
Battery: The heart of the power bank, storing the energy to charge your devices. Lithium-ion (Li-ion) or Lithium Polymer (LiPo) batteries are commonly used due to their high energy density and rechargeable nature.
-
Battery Management System (BMS): A crucial component that ensures safe and efficient charging and discharging of the battery. The BMS protects the battery from overcharging, over-discharging, and short-circuiting.
-
Charging IC: An integrated circuit responsible for controlling the charging process of the battery when the power bank is connected to a power source.
-
Boost Converter: A DC-DC converter that steps up the battery voltage to the required output voltage (usually 5V) for charging external devices.
-
USB Ports: The interface through which you connect your devices to the power bank for charging.
-
Switches and Indicators: Used to control the power bank’s operation and provide visual feedback on the charging status and remaining battery capacity.
How a Power Bank Circuit Works
The power bank circuit operates in two modes: charging mode and discharging mode.
-
Charging Mode: When the power bank is connected to a power source (e.g., a USB wall charger), the charging IC regulates the charging current and voltage to safely charge the battery. The BMS monitors the battery’s voltage and temperature to prevent overcharging and ensure optimal charging conditions.
-
Discharging Mode: When an external device is connected to the power bank’s USB port, the boost converter steps up the battery voltage to the required output voltage (usually 5V). The BMS monitors the battery’s voltage and prevents over-discharging, which could damage the battery.
Designing Your Power Bank PCB
Now that you have a basic understanding of power bank circuits, let’s dive into the process of designing your own power bank PCB.
Selecting the Right Components
Choosing the appropriate components is crucial for building a reliable and efficient power bank. Here are some key considerations:
-
Battery Capacity: Determine the desired capacity of your power bank based on your charging needs. Common capacities range from 2,000mAh to 20,000mAh or more.
-
Battery Type: Li-ion or LiPo batteries are popular choices due to their high energy density and rechargeable nature. Consider factors such as size, cost, and safety when selecting the battery type.
-
Charging IC: Select a charging IC that is compatible with your battery type and provides the desired charging current and voltage. Popular options include the TP4056 and the MCP73831.
-
Boost Converter: Choose a boost converter that can efficiently step up the battery voltage to the required output voltage. The TPS61090 and the MT3608 are commonly used boost converters.
-
BMS: Opt for a BMS that is suitable for your battery type and provides essential protection features such as overcharge protection, over-discharge protection, and short-circuit protection.
Component | Recommended Options |
---|---|
Battery | Li-ion, LiPo (capacity: 2,000mAh-20,000mAh) |
Charging IC | TP4056, MCP73831 |
Boost Converter | TPS61090, MT3608 |
BMS | Protection ICs suitable for battery type |
Schematic Design
Once you have selected the components, it’s time to create the schematic diagram for your power bank PCB. Use a PCB design software such as KiCad, Eagle, or Altium Designer to create the schematic.
-
Battery and BMS: Connect the battery to the BMS, ensuring proper polarity and connections for the positive, negative, and temperature sensing terminals.
-
Charging IC: Connect the charging IC to the BMS and battery, following the manufacturer’s recommended schematic. Include the necessary passive components such as resistors and capacitors.
-
Boost Converter: Wire the boost converter to the battery and the USB output, configuring the feedback network to achieve the desired output voltage.
-
USB Ports: Connect the USB ports to the boost converter output, including any necessary protection components such as Tvs Diodes and current-limiting resistors.
-
Switches and Indicators: Incorporate switches for power control and LEDs or other indicators for battery status and charging feedback.
PCB Layout
With the schematic design complete, proceed to the PCB layout stage. Consider the following guidelines:
-
Component Placement: Arrange the components on the PCB in a logical and space-efficient manner. Place the battery and BMS close together, and position the charging IC and boost converter near their respective connections.
-
Trace Width and Spacing: Ensure that the trace widths are sufficient to handle the expected currents. Maintain proper spacing between traces to avoid interference and meet manufacturing guidelines.
-
Ground Plane: Include a solid ground plane on the PCB to improve signal integrity and reduce noise.
-
Thermal Considerations: Provide adequate copper pours and thermal vias for components that generate heat, such as the boost converter and charging IC.
-
Manufacturability: Adhere to the design rules and guidelines provided by your PCB manufacturer to ensure a smooth and successful manufacturing process.
Manufacturing Your Power Bank PCB
After finalizing your PCB design, it’s time to manufacture the power bank PCB.
Choosing a PCB Manufacturer
Select a reputable PCB manufacturer that offers the required specifications and capabilities for your power bank PCB. Consider factors such as:
-
PCB Material: Choose a suitable PCB material, such as FR-4, that meets your requirements for durability and electrical properties.
-
Layer Count: Determine the number of layers needed for your power bank PCB based on the complexity of your design. A two-layer PCB is often sufficient for simpler designs.
-
Copper Thickness: Specify the desired copper thickness for your PCB traces. A thickness of 1 oz or 2 oz is common for power bank PCBs.
-
Surface Finish: Select an appropriate surface finish, such as HASL (Hot Air Solder Leveling) or ENIG (Electroless Nickel Immersion Gold), based on your soldering requirements and component compatibility.
Ordering and Assembly
-
Gerber Files: Generate the Gerber files from your PCB design software, which include the necessary information for manufacturing, such as the copper layers, solder mask, and silkscreen.
-
Bill of Materials (BOM): Create a comprehensive BOM that lists all the components required for your power bank PCB, including their quantities, part numbers, and specifications.
-
Assembly Instructions: Provide clear assembly instructions to the PCB manufacturer, specifying any special requirements or preferences for component placement and soldering.
-
Order Placement: Submit your Gerber files, BOM, and assembly instructions to the PCB manufacturer, specifying the desired quantity and lead time.
Testing and Verification
Upon receiving your manufactured power bank PCBs, perform thorough testing and verification to ensure proper functionality and safety.
-
Visual Inspection: Carefully inspect each PCB for any manufacturing defects, such as misaligned components, solder bridges, or damaged traces.
-
Continuity Testing: Use a multimeter to verify the continuity of critical connections, such as power lines and ground paths.
-
Functional Testing: Assemble the power bank PCB with the necessary components and perform functional tests, including charging and discharging cycles, to ensure proper operation.
-
Safety Testing: Conduct safety tests to verify that the BMS and protection circuits are functioning as intended, preventing overcharging, over-discharging, and short-circuiting.
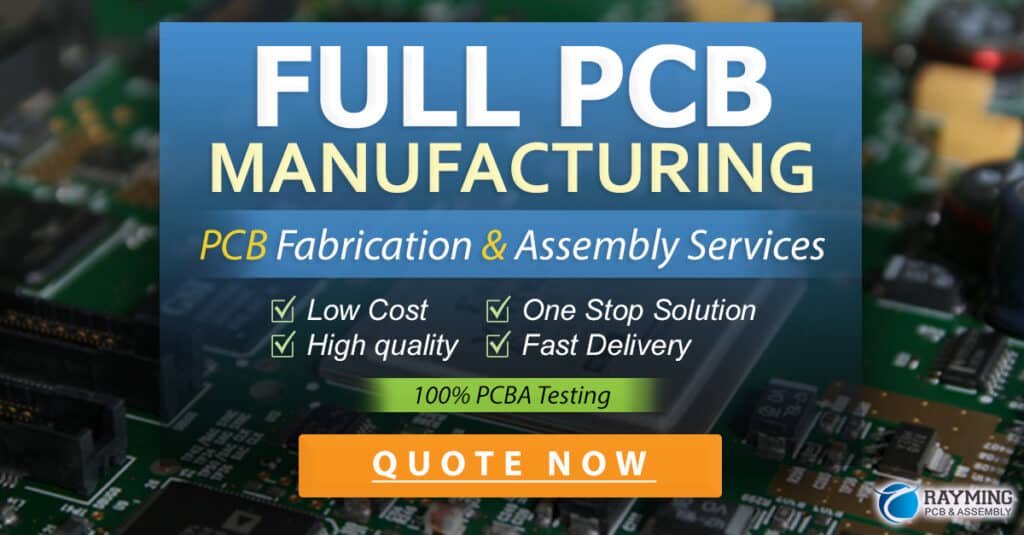
Frequently Asked Questions (FAQ)
- What is the typical capacity range for power banks?
-
Power banks typically range in capacity from 2,000mAh to 20,000mAh or more. The capacity you choose depends on your specific charging needs and the devices you intend to charge.
-
Can I use any type of battery for my power bank PCB?
-
While various Battery Types can be used, lithium-ion (Li-ion) and lithium polymer (LiPo) batteries are the most common choices for power banks due to their high energy density and rechargeable nature. It’s important to select a battery that is compatible with your chosen BMS and meets your capacity and size requirements.
-
What is the purpose of the BMS in a power bank circuit?
-
The Battery Management System (BMS) is a crucial component that ensures the safe and efficient operation of the power bank. It protects the battery from overcharging, over-discharging, and short-circuiting, monitors the battery’s voltage and temperature, and balances the cells in multi-cell battery packs. The BMS helps to prolong the battery’s lifespan and prevent potential safety hazards.
-
How do I select the appropriate boost converter for my power bank PCB?
-
When choosing a boost converter, consider factors such as the input voltage range (determined by your battery voltage), the desired output voltage (usually 5V for USB charging), and the maximum output current required. Popular boost converter ICs include the TPS61090 and the MT3608, which offer high efficiency and compact size.
-
What safety considerations should I keep in mind when designing and manufacturing a power bank PCB?
- Safety is paramount when designing and manufacturing a power bank PCB. Ensure that your design incorporates proper protection features, such as overcharge protection, over-discharge protection, and short-circuit protection, through the use of a reliable BMS. Adhere to best practices for PCB layout, including adequate trace widths, proper spacing, and thermal management. During manufacturing and assembly, follow established guidelines and perform thorough testing and verification to ensure the power bank meets safety standards and functions as intended.
Conclusion
Creating your own power bank circuit on a PCB is a rewarding and educational experience. By understanding the basics of power bank circuits, selecting the right components, designing a robust schematic and PCB layout, and following proper manufacturing and assembly practices, you can build a custom power bank that meets your specific needs.
Remember to prioritize safety throughout the design and manufacturing process, and always perform thorough testing and verification before using your power bank PCB. With the knowledge and skills gained from this guide, you’ll be well-equipped to embark on your own power bank PCB projects and explore further innovations in portable power solutions.
No responses yet