Introduction to Ferrite Core Transformers
Ferrite core transformers are essential components in various electrical and electronic applications, ranging from power supplies to high-frequency communication systems. These transformers utilize ferrite cores, which are made from a ceramic material composed of iron oxide and other metal oxides, to enhance their performance and efficiency. In this comprehensive guide, we will delve into the basics of ferrite core transformers, their properties, advantages, and applications.
What is a Ferrite Core Transformer?
A ferrite core transformer is an electrical device that uses a ferrite core to transfer electrical energy between two or more circuits through electromagnetic induction. The ferrite core is a magnetic ceramic material that provides a high magnetic permeability and low electrical conductivity, making it ideal for use in transformers.
The basic structure of a ferrite core transformer consists of:
1. Ferrite core
2. Primary winding
3. Secondary winding
4. Insulation material
The primary winding is connected to the input power source, while the secondary winding is connected to the load. The ferrite core acts as a magnetic path for the flux generated by the primary winding, which induces a voltage in the secondary winding.
Properties of Ferrite Core Transformers
Ferrite core transformers possess several unique properties that make them advantageous over other types of transformers:
High Magnetic Permeability
Ferrite cores have a high magnetic permeability, which means they can concentrate and guide magnetic fields more effectively than air or other materials. This property allows for the design of compact and efficient transformers.
Low Eddy Current Losses
Ferrite materials have high electrical resistivity, which minimizes eddy current losses. Eddy currents are induced currents that circulate within the core material, causing power loss and heat generation. The low eddy current losses in ferrite cores result in improved efficiency and reduced heat generation.
High Frequency Operation
Ferrite core transformers are suitable for high-frequency applications due to their low core losses at high frequencies. They are commonly used in switching power supplies, RF transformers, and telecommunication systems that operate at frequencies ranging from tens of kilohertz to several megahertz.
Saturation Flux Density
Ferrite cores have a lower saturation flux density compared to other magnetic materials like iron or silicon steel. Saturation occurs when the core cannot accommodate any further increase in magnetic flux, leading to a nonlinear behavior and reduced performance. The lower saturation flux density of ferrite cores limits their use in high-power applications.
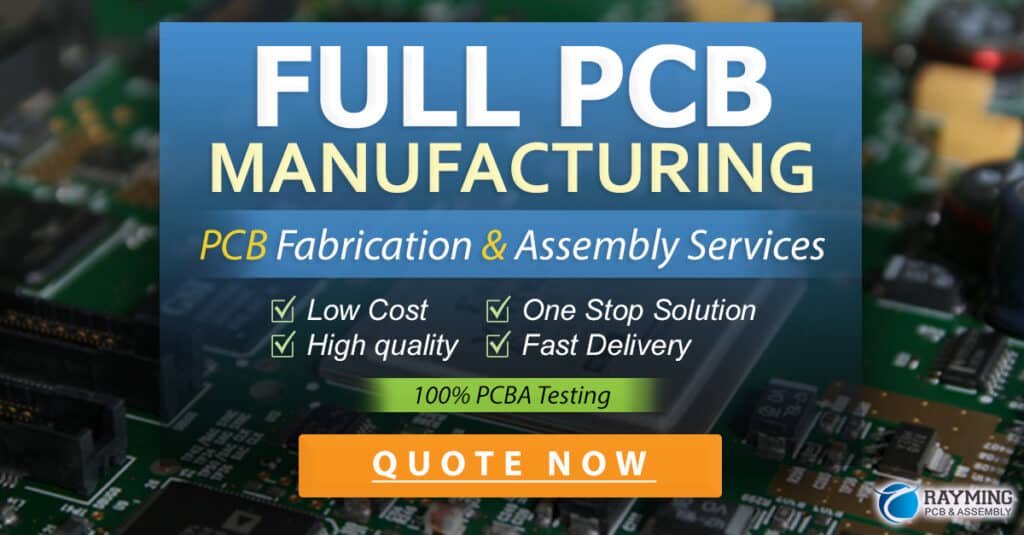
Advantages of Ferrite Core Transformers
Ferrite core transformers offer several advantages over other types of transformers:
-
Compact size: The high magnetic permeability of ferrite cores allows for the design of smaller and lighter transformers compared to those with air or iron cores.
-
High efficiency: The low eddy current losses and high resistivity of ferrite cores contribute to higher efficiency, especially at high frequencies.
-
Low cost: Ferrite materials are relatively inexpensive compared to other magnetic materials, making ferrite core transformers cost-effective for various applications.
-
Wide frequency range: Ferrite core transformers can operate efficiently over a wide range of frequencies, from a few kilohertz to several megahertz.
-
Low noise: The high resistivity of ferrite cores minimizes the generation of electromagnetic interference (EMI) and noise, making them suitable for use in sensitive electronic circuits.
Applications of Ferrite Core Transformers
Ferrite core transformers find applications in various fields, including:
-
Power supplies: Ferrite core transformers are commonly used in switch-mode power supplies (SMPS) for voltage conversion and isolation. They are essential components in devices such as mobile phone chargers, computer power supplies, and LED drivers.
-
Telecommunications: High-frequency ferrite core transformers are used in RF and microwave circuits for impedance matching, signal coupling, and isolation. They are found in cellular base stations, wireless communication systems, and satellite communication equipment.
-
Automotive electronics: Ferrite core transformers are used in automotive applications for power conversion, signal isolation, and noise suppression. They are found in engine control units, entertainment systems, and advanced driver assistance systems (ADAS).
-
Medical equipment: Ferrite core transformers are used in medical devices for power isolation, signal conditioning, and noise reduction. They are essential components in patient monitoring systems, X-ray machines, and MRI scanners.
-
Industrial automation: Ferrite core transformers are used in industrial control systems for power isolation, signal transmission, and noise suppression. They are found in programmable logic controllers (PLCs), motor drives, and process control equipment.
Ferrite Core Materials
Ferrite cores are made from various types of ferrite materials, each with specific properties and applications. The most common ferrite materials used in transformers are:
-
Manganese-zinc (MnZn) ferrite: MnZn ferrite has a high permeability and is suitable for low to medium frequency applications (up to a few MHz). It is commonly used in power transformers, EMI suppression components, and inductors.
-
Nickel-zinc (NiZn) ferrite: NiZn ferrite has a lower permeability than MnZn ferrite but can operate at higher frequencies (up to several hundred MHz). It is used in high-frequency transformers, RF inductors, and antenna cores.
The choice of ferrite material depends on the specific application, operating frequency, and required performance characteristics.
Ferrite Core Shapes and Sizes
Ferrite cores are available in various shapes and sizes to suit different applications and design requirements. Some common ferrite core shapes include:
-
E cores: E-shaped cores are widely used in power transformers and inductors. They consist of two E-shaped halves that are joined together to form a closed magnetic path.
-
Toroid cores: Toroidal cores are ring-shaped and provide a closed magnetic path, resulting in low electromagnetic interference (EMI) and high efficiency. They are commonly used in high-frequency transformers and inductors.
-
Pot cores: Pot cores consist of a cylindrical ferrite core with a central hole and a matching ferrite lid. They provide good magnetic shielding and are used in transformers and inductors for noise-sensitive applications.
-
RM cores: RM (rectangular modular) cores are rectangular-shaped cores with a central hole. They are used in high-frequency transformers and inductors where a low profile and high power density are required.
The size of the ferrite core is determined by the power handling capability, inductance requirement, and available space in the application.
Designing with Ferrite Core Transformers
When designing circuits with ferrite core transformers, several factors need to be considered:
-
Inductance: The inductance of the transformer is determined by the number of turns, core material, and core geometry. The required inductance is calculated based on the application requirements, such as the operating frequency, voltage, and current.
-
Winding design: The number of turns and the wire gauge of the primary and secondary windings are selected based on the desired voltage ratio, current handling capability, and efficiency. The windings should be arranged to minimize leakage inductance and capacitance.
-
Core selection: The ferrite core material and shape are chosen based on the operating frequency, power handling capability, and required performance characteristics. The core size is determined by the power handling capability and the available space in the application.
-
Losses: The losses in the transformer, including core losses and winding losses, should be minimized to achieve high efficiency. Core losses can be reduced by selecting a suitable ferrite material and operating at an appropriate flux density. Winding losses can be minimized by using the appropriate wire gauge and winding technique.
-
Shielding: In some applications, electromagnetic shielding may be required to reduce EMI and noise. Ferrite cores with high permeability and closed magnetic paths, such as toroid and pot cores, provide better shielding compared to open-shaped cores like E cores.
Ferrite Core Transformer Construction
The construction of a ferrite core transformer involves the following steps:
-
Core preparation: The ferrite core is cleaned and inspected for any defects or cracks. If the core consists of multiple parts, they are assembled using clamps or adhesives.
-
Winding: The primary and secondary windings are wound on a bobbin or directly on the core, depending on the core shape and size. The windings are insulated from each other and the core using insulating tape or varnish.
-
Termination: The ends of the windings are soldered or welded to terminal pins or leads for external connections.
-
Impregnation: The transformer is impregnated with a suitable varnish or epoxy to provide mechanical strength, moisture resistance, and electrical insulation.
-
Testing: The transformer is tested for electrical parameters such as inductance, resistance, and insulation resistance to ensure compliance with the design specifications.
Ferrite Core Transformer Maintenance and Troubleshooting
Ferrite core transformers are generally reliable and require minimal maintenance. However, some common issues that may arise include:
-
Overheating: Excessive heat generation in the transformer can be caused by overloading, insufficient cooling, or core saturation. Overheating can lead to insulation breakdown and premature failure. Proper heat dissipation through heatsinks or cooling fans can mitigate this issue.
-
Insulation breakdown: The insulation between the windings and the core can degrade over time due to thermal stress, moisture, or mechanical damage. Insulation breakdown can cause short circuits and transformer failure. Regular inspection and maintenance can help identify and prevent insulation issues.
-
Core saturation: If the transformer is operated at a flux density higher than the saturation flux density of the ferrite core, the core will saturate, leading to a nonlinear behavior and reduced performance. Proper core selection and design can prevent core saturation.
-
Winding damage: The transformer windings can be damaged due to mechanical stress, vibration, or improper handling. Damaged windings can cause short circuits or open circuits, leading to transformer failure. Proper mounting and handling of the transformer can prevent winding damage.
Regular visual inspection, cleaning, and testing of the transformer can help identify and prevent potential issues, ensuring reliable operation and long service life.
FAQs
-
What is the difference between a ferrite core transformer and an iron core transformer?
Ferrite core transformers use a ferrite ceramic core, which has high magnetic permeability and high electrical resistivity, resulting in lower losses and higher efficiency at high frequencies. Iron core transformers use laminated iron cores, which have higher saturation flux density but higher losses at high frequencies, making them more suitable for low-frequency and high-power applications. -
Can ferrite core transformers be used for low-frequency applications?
While ferrite core transformers are primarily used for high-frequency applications, they can also be used for low-frequency applications. However, their lower saturation flux density compared to iron cores may limit their power handling capability in low-frequency applications. -
How do I select the appropriate ferrite core material for my application?
The selection of the ferrite core material depends on the operating frequency, required permeability, and desired performance characteristics. MnZn ferrite is suitable for low to medium frequencies (up to a few MHz) and has high permeability, while NiZn ferrite is suitable for higher frequencies (up to several hundred MHz) but has lower permeability. -
What is the purpose of impregnating a ferrite core transformer?
Impregnating a ferrite core transformer with varnish or epoxy provides several benefits, including improved mechanical strength, moisture resistance, and electrical insulation. Impregnation helps protect the windings and the core from environmental factors and enhances the overall reliability and durability of the transformer. -
How can I reduce electromagnetic interference (EMI) in my ferrite core transformer?
To reduce EMI in a ferrite core transformer, you can use a closed magnetic path core such as a toroid or pot core, which provides better magnetic shielding compared to open-shaped cores like E cores. Additionally, proper winding techniques, such as using twisted wires or implementing shielding foils, can help minimize EMI.
Conclusion
Ferrite core transformers are essential components in a wide range of electrical and electronic applications, offering high efficiency, compact size, and excellent high-frequency performance. By understanding the properties, advantages, and design considerations of ferrite core transformers, engineers and designers can effectively utilize these components to develop reliable and efficient systems.
This comprehensive guide has covered the basics of ferrite core transformers, including their structure, properties, advantages, and applications. We have also discussed the various ferrite core materials, shapes, and sizes available, as well as the design considerations and construction process for these transformers.
As technology continues to advance, the demand for high-performance and compact transformers will continue to grow. Ferrite core transformers, with their unique properties and advantages, will play a crucial role in meeting these demands and enabling the development of innovative electrical and electronic systems.
No responses yet