Introduction to Breadboard-to-PCB Transition
Prototyping electronic circuits on a breadboard is a common practice among hobbyists, students, and professionals alike. It allows for quick and easy testing of circuit designs without the need for soldering or permanent connections. However, when it comes to creating a final product, a breadboard prototype is not suitable due to its lack of durability, reliability, and aesthetic appeal. This is where the transition from breadboard to printed circuit board (PCB) becomes essential.
In this comprehensive guide, we will walk you through the process of moving from a breadboard prototype to a full-fledged PCB-based product. We will cover the essential steps, considerations, and best practices to ensure a smooth and successful transition.
Understanding the Differences between Breadboards and PCBs
Before diving into the transition process, it’s crucial to understand the fundamental differences between breadboards and PCBs. This understanding will help you make informed decisions throughout the development process.
Breadboards
Breadboards are solderless prototyping boards that allow for temporary connections between electronic components. They consist of a grid of holes interconnected by metal strips underneath the surface. The main advantages of breadboards include:
- Quick and easy prototyping
- Reusable components
- No soldering required
- Ideal for testing and experimentation
However, breadboards also have some limitations:
- Limited current carrying capacity
- Prone to loose connections and short circuits
- Not suitable for high-frequency or sensitive circuits
- Not durable or reliable for long-term use
PCBs
PCBs, on the other hand, are custom-designed boards with copper traces that permanently connect electronic components. They offer several advantages over breadboards:
- Robust and durable construction
- Reliable connections and reduced noise
- Ability to handle high-frequency and sensitive circuits
- Compact and customizable form factors
- Suitable for mass production
The main drawback of PCBs is that they require more time and effort to design and manufacture compared to breadboards.
Steps to Transition from Breadboard to PCB
Now that we understand the differences between breadboards and PCBs, let’s delve into the step-by-step process of transitioning from a breadboard prototype to a PCB-based product.
Step 1: Finalize and Validate the Circuit Design
Before moving to PCB design, it’s essential to ensure that your breadboard prototype is functioning as intended. Thoroughly test the circuit and make any necessary modifications or improvements. Consider the following aspects:
- Functionality: Verify that the circuit performs the desired functions correctly.
- Component selection: Ensure that the chosen components are suitable for the intended application and operating conditions.
- Power requirements: Determine the power supply requirements and consider any voltage regulation or protection circuitry.
- Signal integrity: Assess the signal quality and integrity, especially for high-frequency or sensitive signals.
Once you are confident in your circuit design, create a detailed schematic diagram that accurately represents the connections and components used in the breadboard prototype.
Step 2: Create a Bill of Materials (BOM)
A Bill of Materials (BOM) is a comprehensive list of all the components required to build your PCB. It includes details such as part numbers, quantities, descriptions, and supplier information. Creating a BOM helps in several ways:
- Ensures all necessary components are accounted for
- Facilitates sourcing and procurement of components
- Helps in cost estimation and budgeting
- Serves as a reference for assembly and manufacturing
Use your schematic diagram and breadboard prototype to create an accurate BOM. Double-check the component specifications and quantities to avoid any discrepancies.
Step 3: Design the PCB Layout
With the schematic and BOM in hand, it’s time to design the PCB layout. This involves translating the schematic into a physical board design that defines the placement of components and routing of copper traces. PCB design software, such as KiCad, Eagle, or Altium Designer, is commonly used for this purpose.
When designing the PCB layout, consider the following factors:
- Component placement: Arrange components in a logical and efficient manner, taking into account signal flow, thermal considerations, and mechanical constraints.
- Trace routing: Route the copper traces to connect the components according to the schematic. Ensure proper trace widths, spacing, and impedance matching for optimal signal integrity.
- Ground plane: Incorporate a solid ground plane to provide a low-impedance return path and reduce noise.
- Power distribution: Design a robust power distribution network with appropriate decoupling capacitors and voltage regulation.
- Manufacturing constraints: Adhere to the manufacturing capabilities and design rules specified by your chosen PCB fabrication vendor.
Iterate and refine your PCB layout until you achieve a design that meets all the functional and manufacturing requirements.
Step 4: Generate Gerber Files and Fabricate the PCB
Once your PCB layout is finalized, generate the necessary Gerber files. Gerber files are industry-standard files that contain the information needed for PCB fabrication. They include data such as copper layers, solder mask, silkscreen, and drill holes.
Most PCB design software has built-in functionality to generate Gerber files. Ensure that you select the appropriate settings and include all the required layers.
Next, choose a reputable PCB fabrication vendor and submit your Gerber files for manufacturing. Provide any additional specifications, such as board thickness, copper weight, surface finish, and quantity.
Step 5: Assemble and Test the PCB
Upon receiving the fabricated PCBs, it’s time to assemble the components onto the board. Depending on the complexity of your design and the quantity required, you may choose to assemble the PCBs manually or use professional assembly services.
If assembling manually, follow these guidelines:
- Use a soldering iron with appropriate temperature control and a fine tip.
- Apply solder sparingly and ensure proper joint formation.
- Pay attention to component orientation and polarity.
- Use flux to improve solderability and prevent oxidation.
- Inspect the assembled board for any bridging, cold joints, or misaligned components.
After assembly, thoroughly test the PCB to verify its functionality. Conduct power-on tests, measure voltages and signals, and perform any necessary calibration or programming.
Step 6: Iterate and Refine
Based on the results of your testing and evaluation, you may need to make further refinements to your PCB design. This could involve modifying component values, adjusting trace routing, or adding additional features.
Iterate on your design until you achieve the desired performance and reliability. Keep detailed documentation of any changes made and update your schematic, BOM, and PCB layout accordingly.
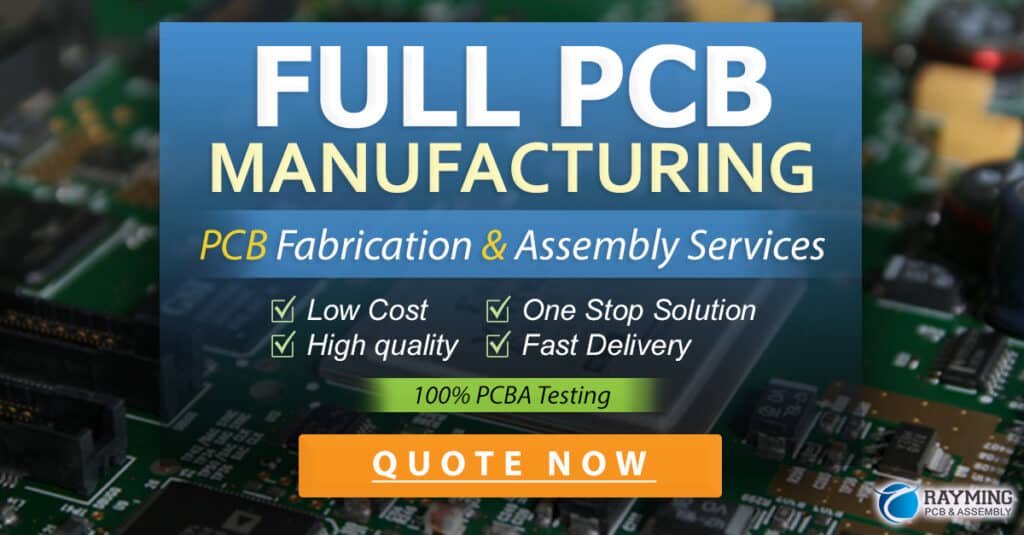
Best Practices for Successful Breadboard-to-PCB Transition
To ensure a smooth and successful transition from breadboard to PCB, consider the following best practices:
-
Start with a well-tested breadboard prototype: Invest time in thoroughly testing and refining your breadboard prototype before moving to PCB design. This will save time and effort in the long run.
-
Use a modular approach: Break down complex designs into smaller, modular sections. This makes it easier to test, debug, and maintain individual parts of the circuit.
-
Choose components wisely: Select components that are readily available, have good documentation, and are suitable for your application. Consider factors such as power ratings, temperature range, and package size.
-
Follow good PCB design practices: Adhere to industry-standard PCB design guidelines, such as proper trace width and spacing, ground plane usage, and component placement. Consult resources like IPC standards for detailed information.
-
Collaborate with experienced professionals: If you lack experience in PCB design or manufacturing, consider collaborating with experienced professionals or seeking guidance from online communities and forums.
-
Plan for manufacturing and assembly: Keep manufacturing and assembly considerations in mind throughout the design process. Choose components and design features that are compatible with your chosen fabrication and assembly methods.
-
Document everything: Maintain detailed documentation of your schematic, BOM, PCB layout, and any design decisions made along the way. This will be invaluable for future reference, troubleshooting, and iterations.
Common Pitfalls to Avoid
While transitioning from breadboard to PCB, be aware of the following common pitfalls:
-
Overcomplicating the design: Avoid unnecessarily complex designs that increase the chances of errors and make debugging more challenging. Keep your design as simple as possible while still meeting the functional requirements.
-
Neglecting power and ground considerations: Pay close attention to power distribution and grounding in your PCB design. Inadequate power or ground connections can lead to noise, signal integrity issues, and even device failure.
-
Ignoring manufacturing constraints: Failing to consider the manufacturing capabilities and constraints of your chosen PCB fabrication vendor can result in design issues or increased costs. Familiarize yourself with the vendor’s design rules and guidelines.
-
Skipping thorough testing: Don’t rush the testing phase. Allocate sufficient time to thoroughly test your PCB Prototype and ensure it meets all the functional and performance requirements before proceeding to mass production.
-
Not considering future revisions: Design your PCB with future revisions and upgrades in mind. Include provisions for additional features, connectors, or test points that may be required in later iterations.
Frequently Asked Questions (FAQ)
- What tools do I need to transition from breadboard to PCB?
To transition from breadboard to PCB, you’ll need a few essential tools: - PCB design software (e.g., KiCad, Eagle, Altium Designer)
- Schematic capture software (often integrated with PCB design software)
- Soldering iron and accessories (soldering station, solder, flux, etc.)
- Multimeter and oscilloscope for testing and debugging
-
Basic electronic components and consumables (resistors, capacitors, ICs, etc.)
-
Can I design a PCB without prior experience?
While it is possible to design a PCB without prior experience, it is recommended to gain some knowledge and understanding of PCB design principles and best practices. There are many online resources, tutorials, and courses available to help you get started. Collaborating with experienced professionals or seeking guidance from online communities can also be beneficial. -
How long does the breadboard-to-PCB transition process take?
The duration of the breadboard-to-PCB transition process varies depending on the complexity of your design, your experience level, and the resources available to you. A simple design might take a few days to a week, while a more complex design could span several weeks or even months. It’s essential to allocate sufficient time for each step of the process, including design, fabrication, assembly, and testing. -
What are the costs involved in transitioning from breadboard to PCB?
The costs involved in the breadboard-to-PCB transition process include: - PCB design software (some options are free, while others require a license)
- Component procurement (cost of purchasing the required components)
- PCB fabrication (varies based on board size, complexity, and quantity)
- Assembly (cost of soldering components onto the PCB)
- Testing and debugging (cost of test equipment and time invested)
The total cost can range from a few hundred to several thousand dollars, depending on the scale and complexity of your project.
- What if my PCB doesn’t work as expected after fabrication?
If your PCB doesn’t work as expected after fabrication, don’t panic. Start by visually inspecting the board for any obvious issues, such as missing components, short circuits, or poor soldering. Use a multimeter to check for continuity and proper connections. If the issue persists, use an oscilloscope to analyze signals and identify any anomalies. Consult your schematic and PCB layout to troubleshoot the problem systematically. If necessary, seek assistance from experienced professionals or online forums.
Conclusion
Transitioning from a breadboard prototype to a PCB-based product is a crucial step in the electronic product development process. By understanding the differences between breadboards and PCBs, following a systematic approach, and adhering to best practices, you can successfully navigate this transition.
Remember to start with a well-tested breadboard prototype, create a comprehensive schematic and BOM, design a robust PCB layout, and thoroughly test the fabricated board. Iterate and refine your design until you achieve the desired functionality and reliability.
Throughout the process, collaborate with experienced professionals, seek guidance when needed, and maintain detailed documentation. By avoiding common pitfalls and allocating sufficient time and resources, you can transform your breadboard prototype into a fully functional and production-ready PCB-based product.
Embrace the journey from breadboard to PCB, as it is a valuable learning experience that will enhance your skills and knowledge in electronic product development. With perseverance and attention to detail, you can bring your electronic ideas to life and create innovative and reliable products.
No responses yet