Introduction to Brushless Motors
Brushless motors, also known as electronically commutated motors (ECMs), have gained popularity in various industries due to their high efficiency, low maintenance, and precise control capabilities. Unlike traditional brushed motors, brushless motors rely on electronic control systems to manage the power distribution and rotation of the motor. Proper wiring is crucial for the optimal performance and longevity of brushless motors. In this comprehensive guide, we will delve into the specifications and best practices for Brushless Motor Wiring.
Understanding the Basic Components
Before we dive into the wiring process, it’s essential to understand the basic components of a brushless motor:
- Stator: The stationary part of the motor that contains the windings.
- Rotor: The rotating part of the motor that contains the permanent magnets.
- Electronic Speed Controller (ESC): The device that controls the power distribution to the motor windings based on user input and sensor feedback.
Brushless Motor Wiring Configurations
Brushless motors come in various configurations, each with its specific wiring requirements. The most common configurations are:
1. Three-Phase Wiring
Three-phase brushless motors are the most prevalent type, widely used in applications such as drones, electric vehicles, and industrial machinery. These motors have three sets of windings, typically labeled as A, B, and C, or U, V, and W.
The ESC controls the power delivery to each winding in a specific sequence to create a rotating magnetic field, which causes the rotor to spin. The wiring diagram for a three-phase brushless motor is as follows:
Motor Winding | ESC Output |
---|---|
A (or U) | A |
B (or V) | B |
C (or W) | C |
It’s crucial to ensure that the winding connections match the corresponding ESC outputs to achieve proper motor operation.
2. Sensored vs. Sensorless Wiring
Brushless motors can be categorized as sensored or sensorless, depending on the presence of position sensors.
Sensored Brushless Motors
Sensored brushless motors incorporate sensors, typically Hall Effect Sensors, to provide precise rotor position feedback to the ESC. This feedback allows for better low-speed control and smoother startup. In addition to the three-phase wiring, sensored motors require additional connections for the sensor signals.
Sensor Wire | ESC Sensor Input |
---|---|
Hall Sensor A | Ha |
Hall Sensor B | Hb |
Hall Sensor C | Hc |
Sensor Ground | GND |
Sensor Power | +5V |
Make sure to refer to the motor and ESC documentation for the specific pinout and connection details.
Sensorless Brushless Motors
Sensorless brushless motors do not rely on external sensors for rotor position feedback. Instead, they utilize back electromagnetic force (back-EMF) measurement techniques to estimate the rotor position. The ESC monitors the back-EMF signals from the motor windings to determine the appropriate commutation sequence.
Sensorless motors simplify the wiring process, as they only require the three-phase connections between the motor and ESC. However, they may exhibit reduced low-speed performance and less precise control compared to sensored motors.
3. Delta vs. Wye Winding Configuration
Brushless motors can have either a delta or wye (star) winding configuration. The choice between delta and wye configurations depends on the desired torque, speed, and efficiency characteristics of the motor.
Delta Winding Configuration
In a delta configuration, the three motor windings are connected in a triangular pattern, with each winding connected to the other two. This configuration offers high torque at low speeds but may have reduced efficiency at higher speeds.
Wye Winding Configuration
In a wye (star) configuration, one end of each motor winding is connected to a common point, forming a “Y” shape. This configuration provides better efficiency at higher speeds but may have lower torque at low speeds compared to the delta configuration.
The choice between delta and wye configurations depends on the specific application requirements and the motor’s design. Consult the motor manufacturer’s specifications and recommendations to determine the appropriate winding configuration for your project.
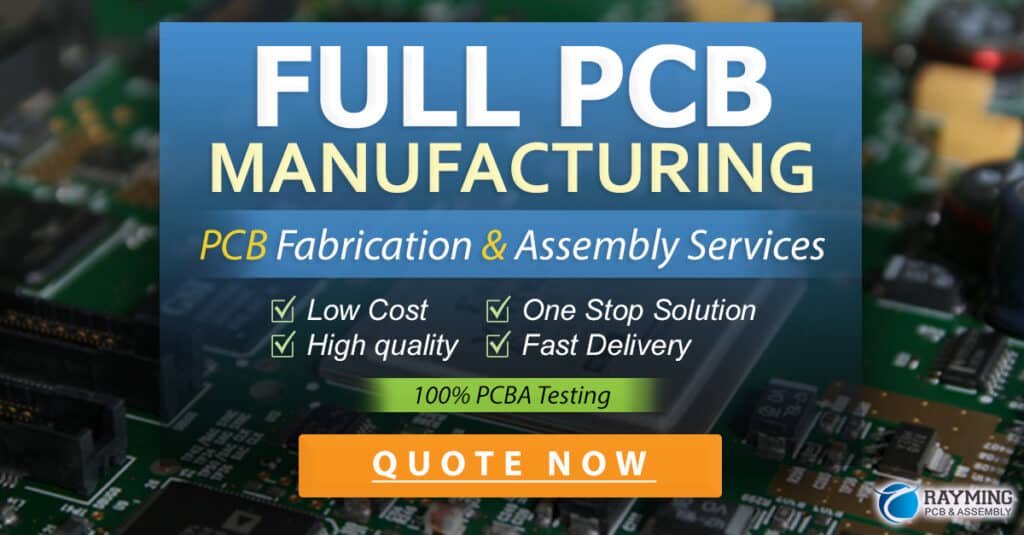
Brushless Motor Wiring Process
Now that we have covered the basic components and configurations, let’s go through the step-by-step process of wiring a brushless motor.
Step 1: Identify the Motor Wires
Identify the three motor wires coming from the brushless motor. They are typically color-coded or labeled as A, B, C, or U, V, W. If the wires are not labeled, consult the motor documentation or use a multimeter to determine the winding pairs.
Step 2: Connect Motor Wires to ESC
Connect each motor wire to the corresponding ESC output. Match the wire labels (A, B, C, or U, V, W) to the ESC output labels. Ensure a secure and reliable connection using soldering or high-quality connectors.
Step 3: Connect Sensor Wires (if applicable)
If you are using a sensored brushless motor, connect the sensor wires to the appropriate ESC sensor inputs. Refer to the motor and ESC documentation for the specific pinout and connection details. Typically, the sensor wires include Hall sensor signals (Ha, Hb, Hc), sensor ground, and sensor power.
Step 4: Power Connections
Connect the ESC to the power source, such as a battery or power supply. Ensure that the power source meets the voltage and current requirements of the motor and ESC. Follow the ESC manufacturer’s guidelines for power connections, which usually involve connecting the positive (red) and negative (black) power wires.
Step 5: Signal Connection
Connect the ESC signal input to the control source, such as a microcontroller, receiver, or servo tester. The signal input is typically a three-wire connection consisting of ground (GND), power (VCC), and signal (SIG) wires. Consult the ESC documentation for the specific signal input requirements and pinout.
Step 6: Double-Check Connections
Before powering on the system, double-check all the connections to ensure they are secure and correctly mapped. Verify that the motor wires, sensor wires (if applicable), power connections, and signal connections are properly connected and insulated.
Step 7: Calibrate and Test
Follow the ESC manufacturer’s instructions to calibrate the ESC and set up any necessary parameters, such as throttle range and timing. Once calibrated, test the motor by gradually increasing the throttle and verifying that the motor rotates smoothly and in the correct direction. If the motor rotates in the wrong direction, swap any two of the three motor wires to reverse the direction.
Safety Considerations
When working with brushless motors and ESCs, it’s crucial to prioritize safety. Here are some key safety considerations:
- Always disconnect the power source before making any wiring changes or adjustments.
- Ensure that the motor and ESC are properly sized for your application and power source.
- Use high-quality connectors and insulate all connections to prevent short circuits.
- Keep the motor and ESC away from flammable materials and ensure adequate ventilation for heat dissipation.
- Wear protective gear, such as safety glasses and gloves, when handling motors and ESCs.
- Follow the manufacturer’s guidelines and specifications for the motor, ESC, and power source.
Troubleshooting Common Issues
Despite careful wiring and setup, problems may arise. Here are some common issues and their potential solutions:
- Motor not spinning:
- Check the power connections and ensure the ESC is receiving the correct voltage and current.
- Verify that the motor wires are correctly connected to the ESC outputs.
-
Ensure the signal connection between the ESC and control source is properly established.
-
Motor spinning in the wrong direction:
-
Swap any two of the three motor wires to reverse the motor’s direction.
-
Erratic or inconsistent motor behavior:
- Check for loose connections or damaged wires.
- Ensure the ESC is calibrated correctly and receiving a clean signal from the control source.
-
Verify that the motor and ESC are not overheating and have adequate cooling.
-
Excessive noise or vibration:
- Check for mechanical issues, such as a bent shaft or damaged bearings.
- Ensure the motor is securely mounted and properly balanced.
- Verify that the ESC timing settings are appropriate for the motor and application.
If the issue persists, consult the manufacturer’s support resources or seek assistance from experienced users or professionals in the field.
Frequently Asked Questions (FAQ)
- Can I use any ESC with any brushless motor?
-
No, it’s essential to choose an ESC that is compatible with the specific brushless motor you are using. Consider factors such as voltage rating, current capacity, and supported features (e.g., sensored or sensorless) when selecting an ESC.
-
How do I determine the proper wire gauge for my brushless motor?
-
The wire gauge depends on the current draw of the motor and the length of the wires. Refer to the motor manufacturer’s specifications for the recommended wire gauge. As a general rule, use a wire gauge that can handle the maximum current draw of the motor with minimal voltage drop.
-
Can I extend the motor wires if they are too short?
-
Yes, you can extend the motor wires using the same gauge wire or thicker. Ensure that the wire connections are secure, properly insulated, and able to handle the current requirements of the motor. Keep in mind that longer wires may introduce voltage drops and signal integrity issues, so try to keep the extensions as short as possible.
-
What is the difference between inner and outer rotor brushless motors?
-
Inner rotor brushless motors have the permanent magnets mounted on the rotor, which spins inside the stator windings. Outer rotor brushless motors have the permanent magnets mounted on the outer shell, which rotates around the stator. Outer rotor motors are commonly used in applications that require high torque at low speeds, such as electric bicycles and fans.
-
How do I program the ESC for my specific application?
- Most ESCs come with a user manual that provides instructions on how to program and configure the ESC using a programming card or software. The programming process typically involves setting parameters such as throttle range, battery type, cutoff voltage, and timing settings. Consult the ESC manufacturer’s documentation and follow their guidelines for proper programming and configuration.
Conclusion
Brushless motor wiring is a critical aspect of ensuring optimal performance and reliability in various applications. By understanding the basic components, wiring configurations, and following the step-by-step wiring process, you can successfully set up your brushless motor system. Remember to prioritize safety, choose compatible components, and refer to the manufacturer’s specifications and guidelines throughout the wiring process.
As with any electrical project, taking the time to carefully plan, execute, and test your brushless motor wiring will yield the best results. If you encounter any issues or have further questions, don’t hesitate to consult the manufacturer’s support resources or seek guidance from experienced professionals in the field.
With proper wiring and configuration, brushless motors offer a wide range of advantages, including high efficiency, precise control, and long-lasting performance. By mastering the art of brushless motor wiring, you can unlock the full potential of these powerful and versatile motors in your projects and applications.
No responses yet